Electric Bus Powertrain: Wheel-Side Drive Motor - Introduction and Analysis
Electric buses have traditionally relied on centralized drive systems. Two main configurations have dominated the market:
- Direct-Drive Motor System
In these systems, the electric motor directly replaces the internal combustion engine. This approach offers a simple and straightforward system architecture, with mature vehicle structural design technology that has made it the mainstream configuration for battery electric buses.
- Motor + Gearbox Systems
This configuration, which combines an electric motor with an Automatic Manual Transmission (AMT) gearbox, delivers superior performance on steep slopes, meeting the demands of mountainous or scenic areas. Although it borrows extensively from conventional fuel vehicle technology and is relatively mature, including an automatic shifting mechanism can compromise reliability, leading to practical challenges in real-world operations.
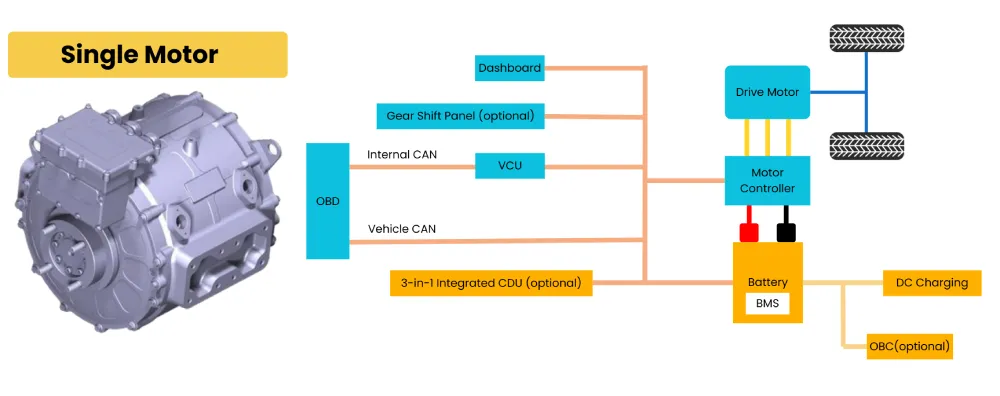

As electric bus powertrain systems evolve toward higher speeds, greater integration, and lightweight designs, distributed electric drive technology—exemplified by wheel-side drive motors—has begun to enter the practical stage. Compared with centralized drive systems, wheel-side drive configurations eliminate the need for transmission shafts, main reduction gears, and differentials. This results in a shorter power transmission chain, higher transmission efficiency, and a more compact structure.
In addition, precise control of wheel-side motor speed and torque enables integrated functions such as vehicle propulsion, braking, differential action, and energy recovery. Owing to its high degree of freedom and functional expandability, the wheel-side drive system has become a focal point in the research and development of pure electric bus powertrain systems.
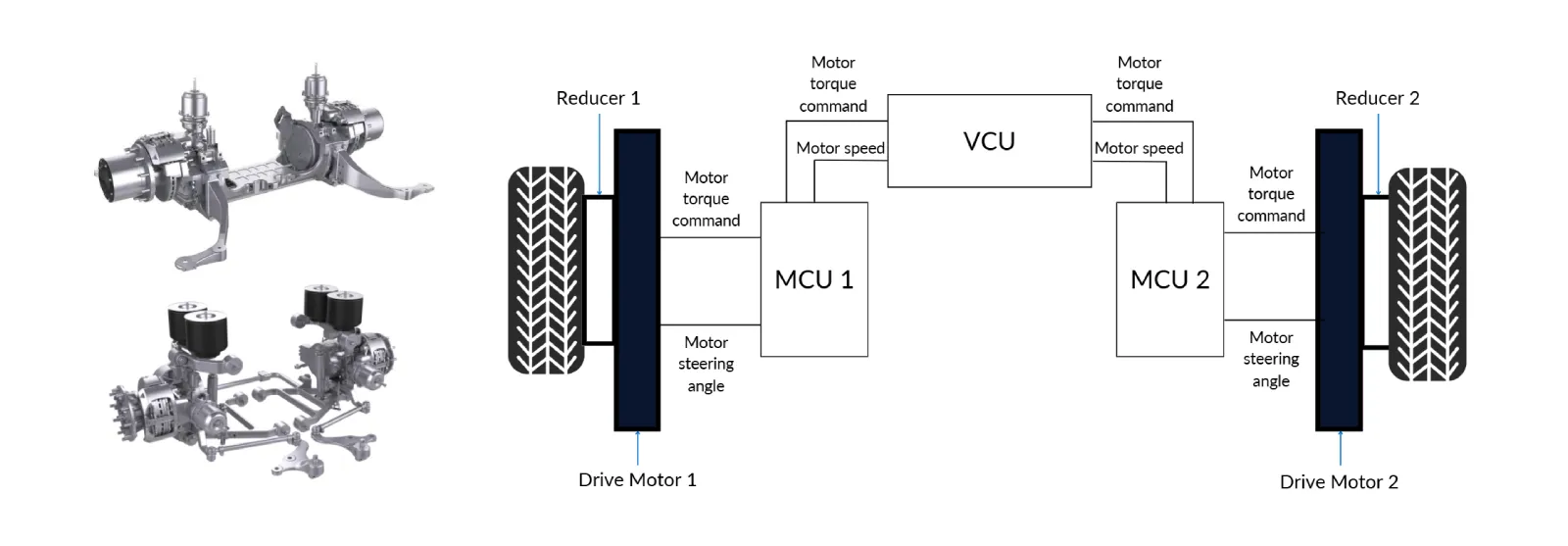
In addition, precise control of wheel-side motor speed and torque enables integrated functions such as vehicle propulsion, braking, differential action, and energy recovery. Owing to its high degree of freedom and functional expandability, the wheel-side drive system has become a focal point in the research and development of pure electric bus powertrain systems.
Electric Bus Powertrain: Wheel-Side Motor Drive Configurations
Wheel-side motor solutions for battery electric buses bridge the gap between centralized and hub motor designs. They typically integrate a motor with a fixed-ratio reducer mounted on the chassis, directly driving the wheels via short axles. Two primary configurations exist:
A. Fixed-Motor Configuration
The fixed-motor configuration usually takes the form of an integrated wheel-side drive axle. In this design, the conventional axle housing and half-shafts are eliminated, and the drive motor is mounted adjacent to the wheel. Despite maintaining a rigid axle structure, this design can employ either steel leaf springs or a combination of air springs and coil-over shock absorbers.
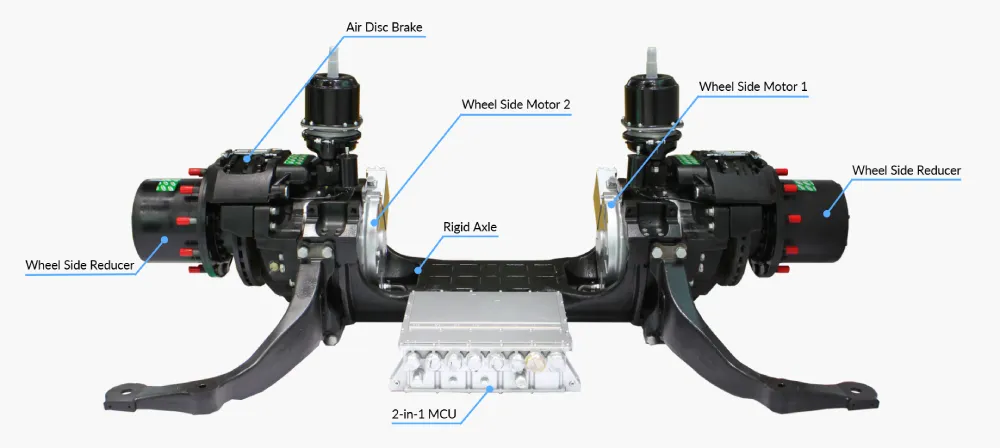
Key advantages:
- Reduced Weight and Space: By removing the axle housing, casing, and half-shafts, the overall structure is significantly lighter and more compact.
- High-Speed Motor Integration: With the use of high-speed motors paired with high reduction ratios (often through a planetary gear structure), the design minimizes motor volume and weight while increasing power density.
- Robust Performance: Our integrated wheel-side drive axle, for example, features two high-speed motors mounted on either side of the axle. With a two-stage reduction system, it delivers enhanced torque and is capable of handling high axle loads—ideal for heavy-duty, low-floor city buses.
B. Swing-Motor Configuration
In the swing-motor configuration, the traditional rigid axle is abandoned in favor of an independent air suspension system. Here, both the drive motors and reducers are mounted directly on the suspension, and the reducer can be designed as either a two-stage or planetary gear system.
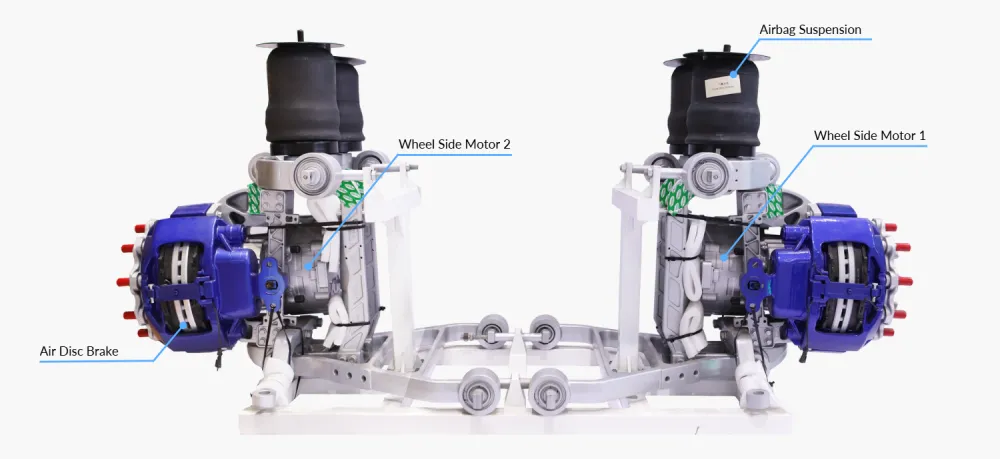
Key advantages:
- Lower Unsprung Mass: The elimination of the rigid axle structure reduces unsprung mass. A well-designed suspension can effectively transfer the motor’s mass to the vehicle body, improving ride comfort and handling.
- Enhanced Cabin Design: This configuration enables increased interior space, a wider aisle, and lower floor heights—critical factors in the design of modern low-floor city buses.
Benefits of Wheel-Side Drive Motors in Electric Buses
The adoption of a wheel-side drive motor for an electric bus powertrain – where flexible electrical connections replace some mechanical linkages – offers significant benefits in electric bus design and performance. Below are the primary advantages:
1. Increased Cabin Space and Lower Floor Height
Low-floor city buses are a growing trend. In these designs, the area from the front passenger door to the last axle forms a continuous, step-free zone. Lowering the interior floor not only reduces the number and height of steps – making boarding and movement inside the bus easier, safer, and more accessible for all passengers – but also increases headroom in key areas.
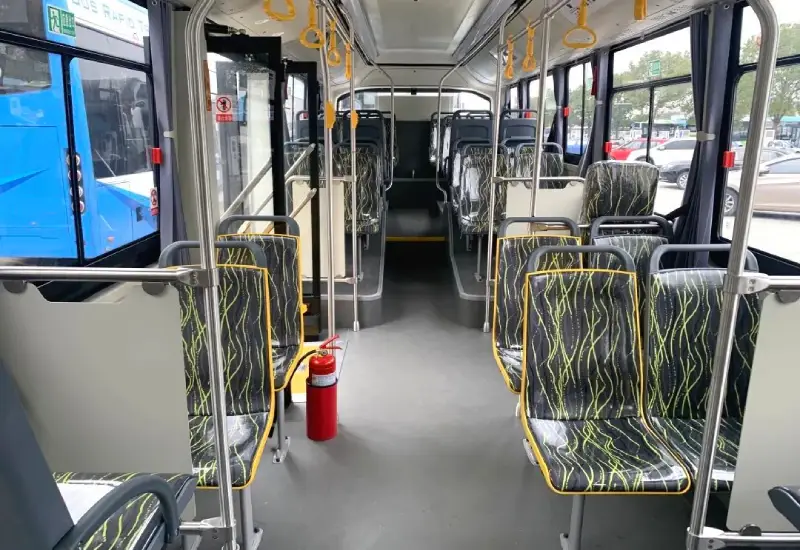
For instance, the structural dimensions of an integrated wheel-side drive axle can reduce floor installation height by approximately 70 mm, achieving a floor clearance as low as 290 mm. This enhanced design meets both interior space and passenger safety requirements.
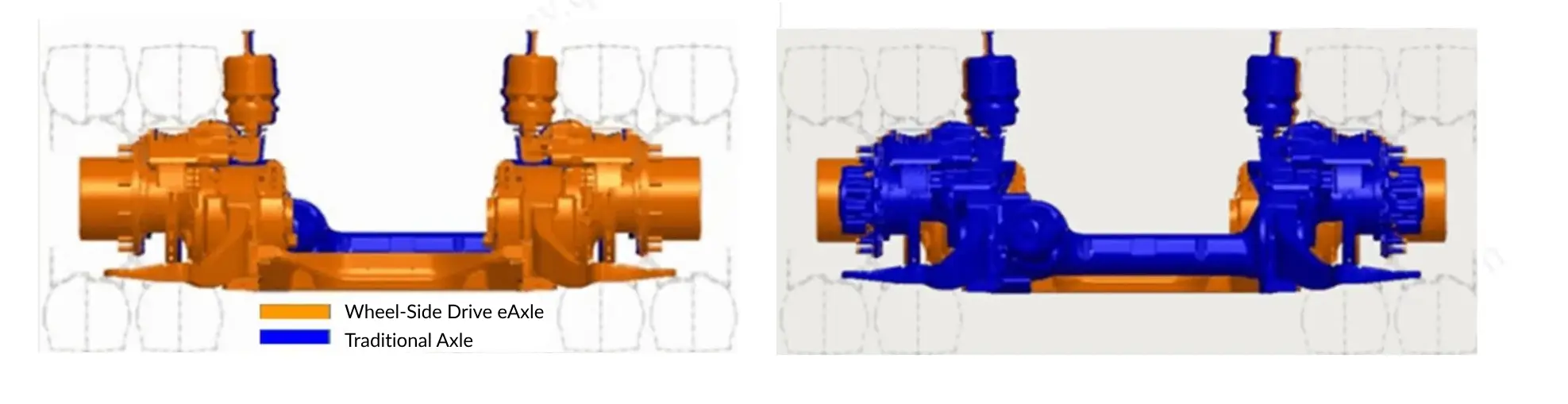
2. Vehicle Lightweighting
Reducing the overall vehicle weight directly contributes to lower energy consumption. Research indicates that a 10% reduction in vehicle weight can lead to a 6% – 8% reduction in energy consumption. The wheel-side drive motor configuration achieves significant weight savings through:
- High-speed motor design: Increased motor speeds allow for lower torque requirements, which in turn reduces cost and weight.
- System integration: Consolidating components (motor, reducer, controller) into an integrated design reduces the need for additional attachments and cabling, thereby lowering both the weight and cost of the powertrain.
3. Enhanced Vehicle Dynamics
Mainstream single-motor direct-drive configurations often struggle with steep climbs and mid-to-high-speed acceleration, while dual-motor systems face challenges in weight and cost. Additionally, motor+AMT configurations can suffer from power interruptions during gear shifts. In contrast, the wheel-side motor configuration:
- Dual-Motor Advantage: By deploying two motors, the power demand on each unit is reduced while maintaining overall system performance.
- Elimination of the Main Reducer: Replacing the main reducer with a high-reduction ratio gear system (using helical gears) not only simplifies the transmission patch but also improves strength, reduces manufacturing complexity, and lowers costs.
4. Improved Transmission Efficiency
Eliminating the traditional main reducer and differential from the electric bus powertrain means that power is transmitted through a shorter chain – enhancing efficiency. The use of helical gears in the wheel-side reducer further increases transmission efficiency and improves regenerative braking capabilities. Additionally, the independent control of multiple wheel-side actuators allows for dynamic optimization of output efficiency.
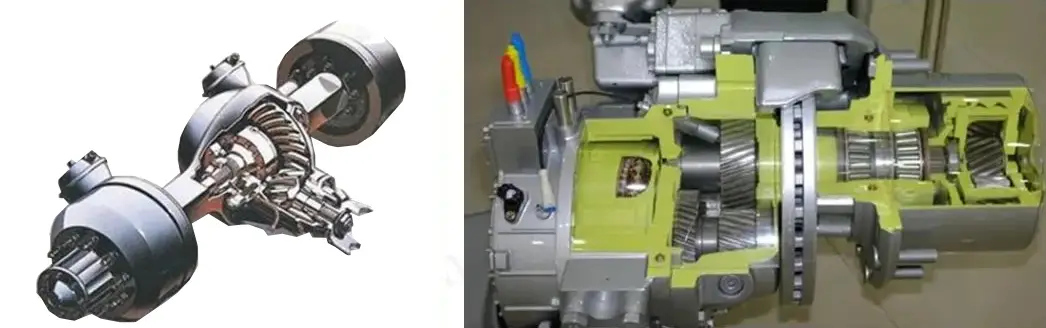
5. Mitigation of Main Reducer Challenges
Pure battery electric buses rely heavily on regenerative braking, which can exert significant stress on the axle and traditional main reducer assemblies. Common issues include unwanted noise, premature gear wear, and bearing damage. While e-axle manufacturers typically address these challenges through reinforced designs and tighter tolerances, these solutions often lead to increased manufacturing costs.
In contrast, the helical gear design used in wheel-side drive systems is easier to manufacture and optimize, resulting in smoother power transmission with reduced shock, vibration, and noise—thereby enhancing both longevity and reliability.
6. Greater Electric Bus Design Freedom
Without the constraints of drive shafts, gearboxes, or differentials, vehicle designers enjoy increased flexibility in the layout of the chassis and longitudinal beams. This freedom not only boosts overall vehicle safety but also allows for innovative designs that enhance comfort and interior space. For example, battery packs can be optimally placed on either the floor or roof to achieve better axle load distribution.
Furthermore, the highly integrated and modular nature of wheel-side drive systems makes them suitable for various vehicle types—including hybrid, fuel cell, and articulated buses. An 18-meter articulated bus, for instance, can be configured with either one or two wheel-side drive axles, offering significant versatility in design and application.
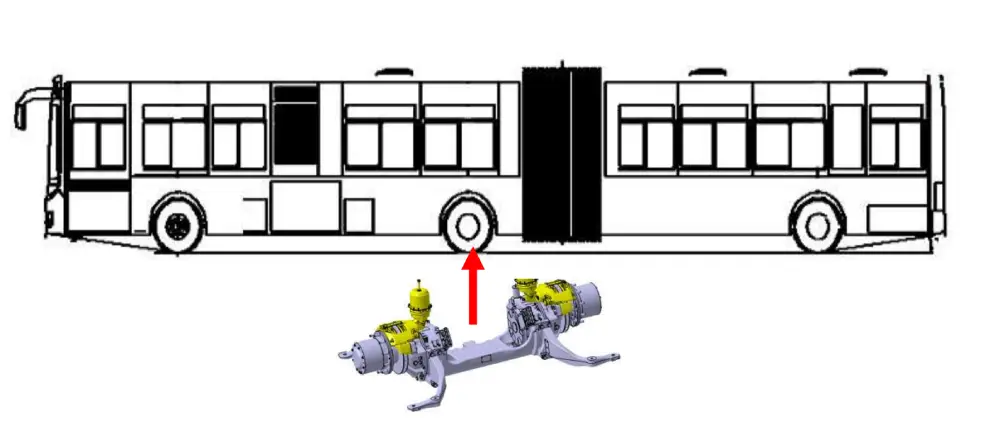
Application of Wheel-Side Drive Motors on Actual Electric Buses
BYD
Currently, BYD is the leading bus manufacturer promoting large-scale adoption of the wheel-side drive axles in buses. Since the inception of its wheel-side drive project in August 2009, BYD has progressively refined its technology – from road tests beginning in March 2010 to the first deliveries of pure electric buses equipped with wheel-side drive axles in July 2011. This success has led to widespread acceptance across cities.
BYD’s extensive product line now includes models ranging from 8 to 12 meters, and its wheel-side drive buses have been exported to markets in the United States, Japan, Europe, and South America – with over 50,000 battery electric buses delivered to partners across six continents, more than 50 countries, and over 300 cities.
For example, the 27-meter pure electric double-articulated bus – designed for Colombia’s BRT system – features two drive axles equipped with wheel-side drive systems. With four wheel-side drive motors, the bus is capable of maintaining normal operation even if one motor fails, thereby maximizing safety. Additionally, the bus can switch between two-wheel and four-wheel drive modes, ensuring stable performance on flat roads for energy savings and robust power output when climbing steep gradients.
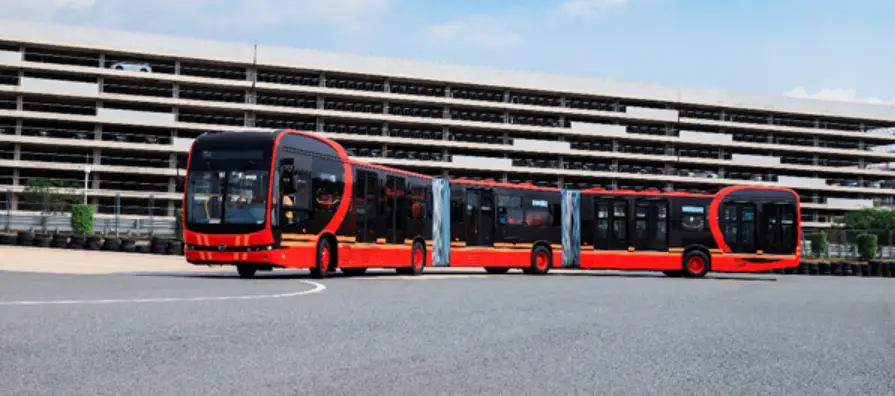
ZEV Auto
ZEV auto has pursued a different technical approach from BYD. Its wheel-side drive system uses a swing-motor configuration integrated with an independent air suspension system, effectively “de-axling” the drive system. (Read here: How an e-Axle with Independent Suspension is Shaping the Future of Electric Bus Design?)
Compared with the rigid axle structure, this method can further reduce system weight, while also providing a wider aisle and lower floor height. For instance, their 12-meter battery electric city bus employs a three-axle design with small wheels and a dual transverse-arm suspension featuring embedded rubber bearings. This configuration delivers excellent suspension dynamics, vibration isolation, handling, and ride comfort.
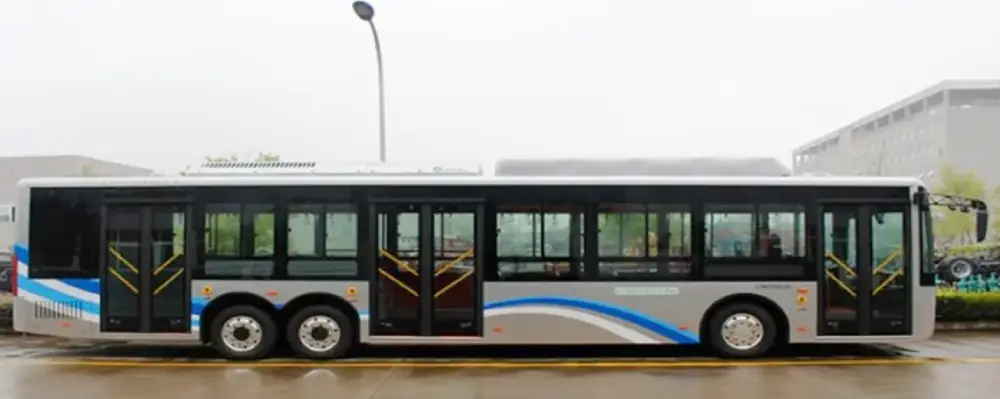
Other Electric Bus Manufacturers
Other electric bus manufacturers, such as Foton, and Ankai, have introduced buses equipped with the wheel-side drive axle, which currently serve major public transit systems.
Brogen's Wheel-Side Drive Solutions for Electric Buses
The wheel-side drive motor configuration offers a host of advantages, including reduced weight, higher integration, and improved energy efficiency. These benefits have led to its widespread adoption in large electric buses. As more bus manufacturers invest in research and development in this area, we can expect an increasing number of buses to adopt wheel-side drive systems in the future.
To empower bus manufacturers to remain competitive and lead in the decarbonization of public transport, we have introduced advanced distributed wheel-side drive solutions. These innovations not only shorten project timelines and accelerate both R&D and manufacturing processes but also help reduce overall costs. Already deployed on (hybrid) electric buses and rubber-tired metros both domestically and internationally, our solutions are designed to deliver superior performance and efficiency in the evolving landscape of sustainable transportation.
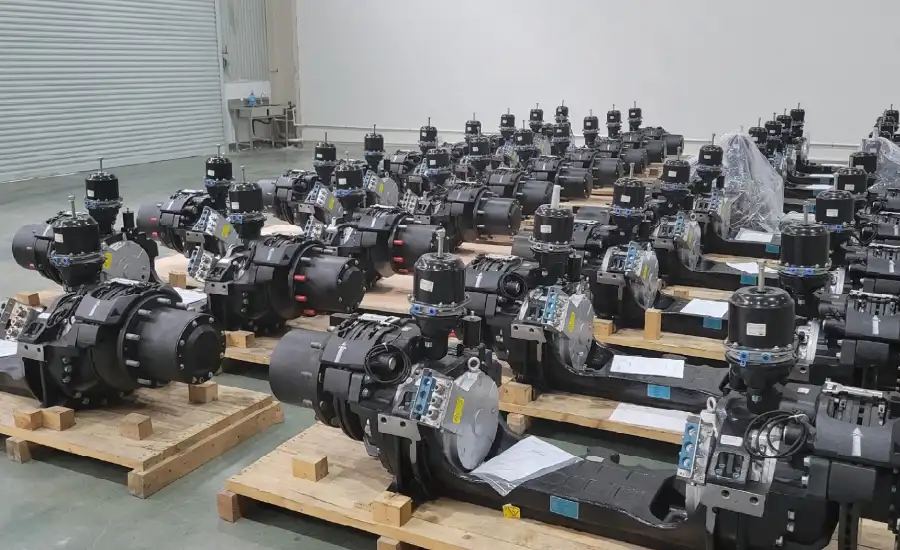
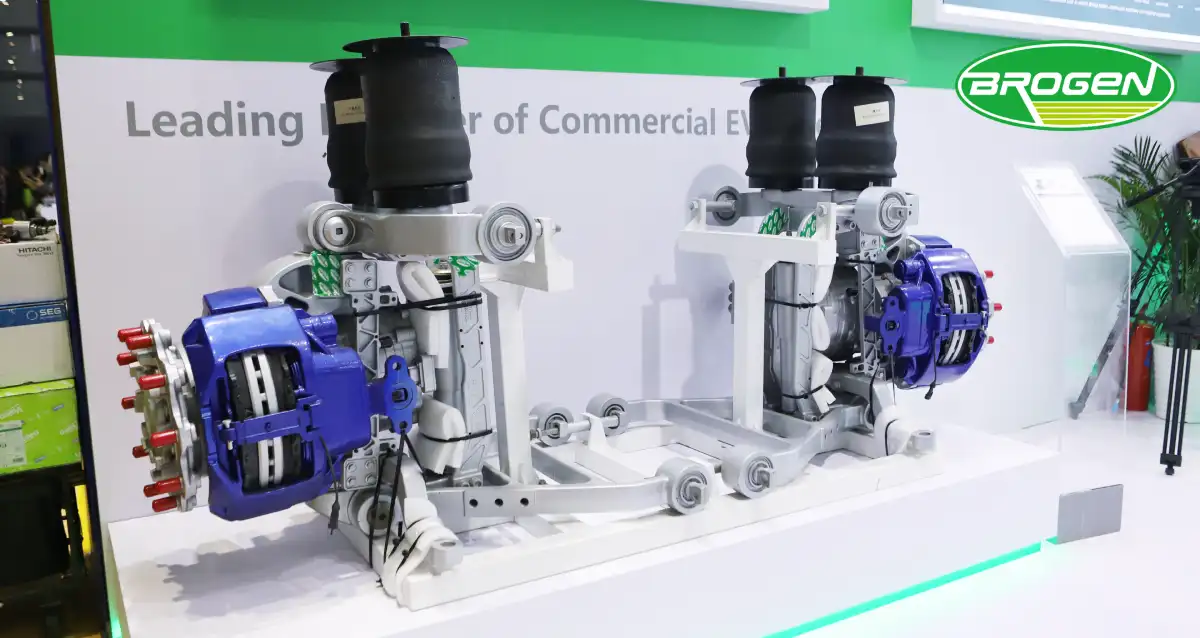
Discover our distributed drive e-axle solutions for buses here: https://brogenevsolution.com/distributed-electric-drive-axle-for-bus/
Business inquiry: contact@brogenevsolution.com or contact us through the table below.
Contact Us
Get in touch with us by sending us an email, using the Whatsapp number below, or filling in the form below. We usually reply within 2 business days.
Email: contact@brogenevsolution.com
Respond within 1 business day
Whatsapp: +8619352173376
Business hours: 9 am to 6 pm, GMT+8, Mon. to Fri.
LinkedIn channel
Follow us for regular updates >
YouTube channel
Ev systems introduction & industry insights >