Electric Axles for Buses
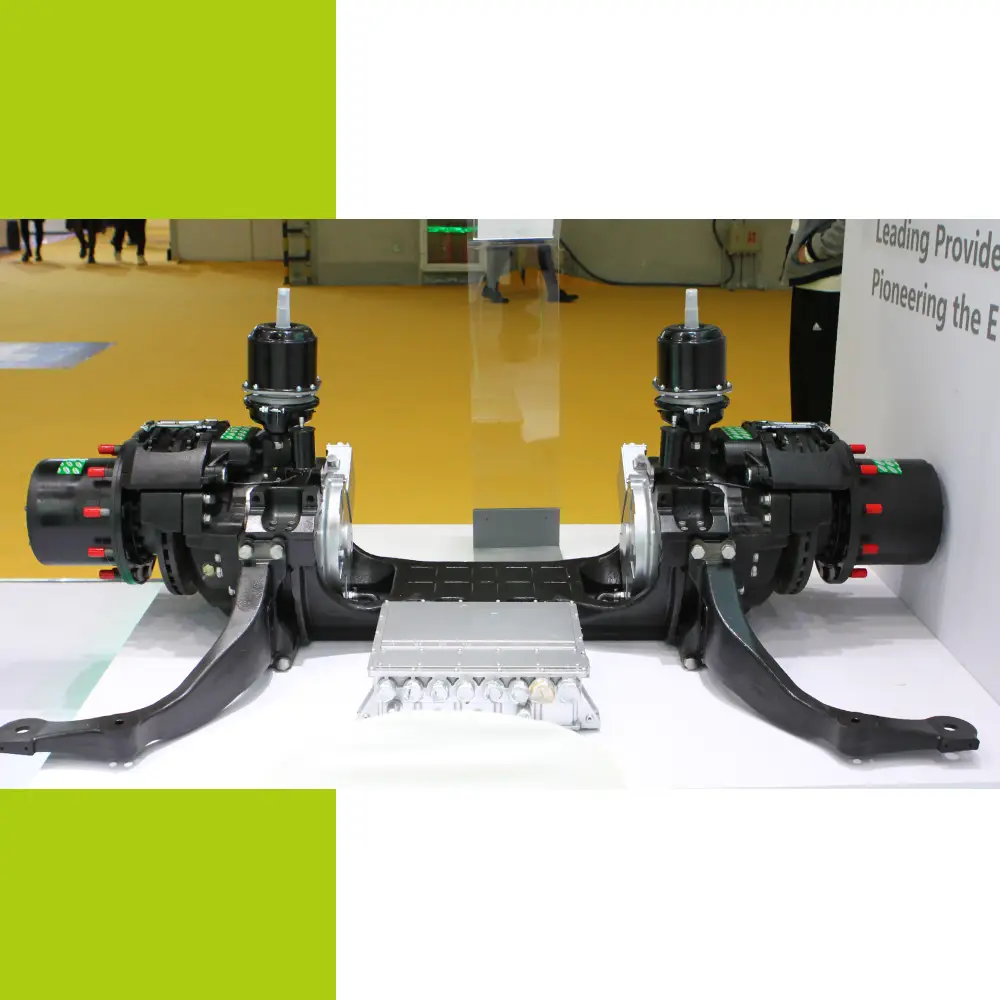
We offer a comprehensive range of electric axles for buses, tailored for public transport applications, including battery-electric, hybrid, and fuel cell city buses, as well as highway coaches, double-decker buses, trolleybuses, and articulated buses ranging from 6 to 18 meters and beyond.
Our solutions are available in multiple technical configurations to meet diverse operational requirements, including both centralized e-axles and distributed-drive electric portal axles. These e-axles support flexible drivetrain layouts, such as front-steering or independent suspension setups. They also enable modern low-floor designs with fully flat interiors, one-step entry, and wide aisles, enhancing passenger accessibility and improving boarding efficiency – key features in the evolution of next-generation public transportation.
Email: contact@brogenevsolution.com
Strengthen Your Electric Bus Design With eAxle Solutions
The adoption of electric axles for buses helps optimize vehicle design by enabling a fully flat low-floor layout, one-step entry, and wide interior aisles – enhancing passenger comfort and safety while improving operational efficiency.
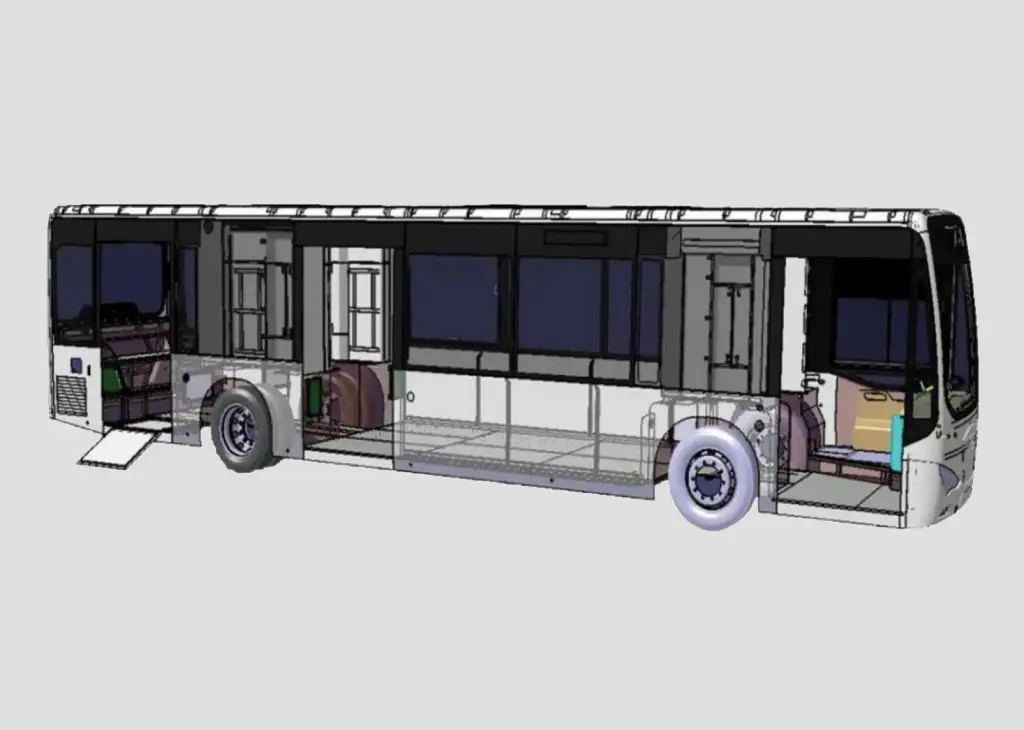
- Weight Reduction in Drivetrain: By integrating the motor, braking system, transmission, and rear axle, our solution eliminates the need for a traditional driveshaft - resulting in a more compact layout and reduced overall weight.
- Improved Efficiency: The reduced system weight contributes to higher overall vehicle efficiency, more flexible battery placement, and better road clearance. These improvements lead to increased passenger capacity and enhanced operational efficiency.
- Enhanced Ride Comfort: The integrated design enables a low-floor layout with wide interior aisles, improving accessibility and passenger flow, enhancing overall ride comfort.

Low-Floor Design
Adapts to the fully flat low-floor design and allows for easy one-step entry, providing a spacious aisle and reducing the risk of passenger falls.

IP67 Protection
An IP67 protection rating effectively prevents the intrusion of dust and water, providing enhanced performance in challenging conditions.

Lower Maintenance Costs
Utilizes maintenance-free wheel hub units, lowering maintenance costs. The advanced EDS ensures tire replacement intervals exceed 100,000 kilometers.
Brogen Solution Features
Wide Applications
We offer a complete range of electric drive axles suitable for buses from 6 meters to 18 meters, and more.
Scalable
Our modular e-axles support high-voltage platforms and can be customized to meet specific requirements.
Reliable
We implement advanced monitoring and alerting strategies to ensure the safety and reliability of our electric drive axles.
Versatile
We provide electric axles with different approaches such as distributed drive, central drive, catering to diverse needs.
Applicable Models
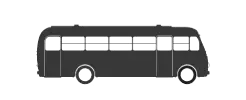
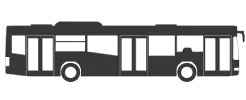
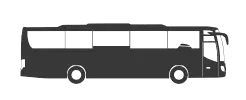
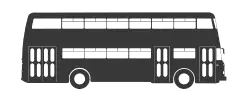
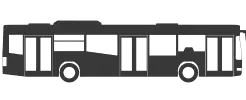
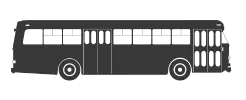
Brogen Solutions of Electric Axles for Buses
1. Parallel-Axis Electric Axles for Buses
For the parallel-axis eAxle system, the electric drive motor and reducer are mounted on the drive axle, with the motor positioned parallel to the axle housing. Utilizing cylindrical gear transmission for a high gear ratio, the integrated design removes unnecessary transmission components, resulting in a more compact structure and increased transmission efficiency.
*Parameters may differ depending on the configuration and vehicle model. Certain specifications can be customized. For more information, please contact us at contact@BrogenEVSolution.com
Model | OEEP5 | OEEP5A (steering) | OEEA30 | OEEA50 | OEEA60 | OEEA85 | OEEA95 |
 | ![]() | ![]() | ![]() | ![]() | ![]() | ![]() | ![]() |
Rated load capacity | 3500 kg | 2700 kg | 3000-3500 kg | 4000-5500 kg | 6000 kg | 8500 kg | 9500 kg |
Maximum output torque | 5400 N.m | 5400 N.m | 4433 N.m | 5730 N.m | 7412 N.m | 9214 N.m | 14415 N.m |
Gear ratio | 15.58/16.60 | 15.58 | 12.665 | 16.141 | 16.473 | 20.475 | 19.22 |
Rated/peak motor power | 60/115 kW | 60/115 kW | 60/120 kW | 65/120 kW | 80/160 kW | 80/160 kW | 200/320 kW |
Rated/peak motor torque | 135/325 N.m | 135/325 N.m | 160/350 N.m | 170/355 N.m | 235/450 N.m | 200/450 N.m | 350/750 N.m |
Rated/peak motor speed | 4244/12000 rpm | 4244/12000 rpm | 3580/12000 rpm | 3600/12000 rpm | 4100/12000 rpm | 3600/12000 rpm | 4093/12000 rpm |
Integrated One-Piece Formed Axle Housing (Expansion-Formed)
High load-bearing capacity, lightweight design, and reduced risk of oil leakage.
Optimized Housing Design
A single-piece housing minimizes oil leakage risks, while a smooth, curved inner cavity reduces oil churning losses.
High-Precision Two-Stage Helical Gear Transmission
Features dual-surface precision grinding for improved efficiency, lower noise, and extended lifespan.
Compact Motor and Axle Integration
Minimizes offset distance between the motor and axle housing, further reducing the risk of oil leakage at the reducer interface.
- Compact e-axle layout for better chassis integration
- Lightweight design for improved efficiency
- Precision-ground gears for low noise and comfort
- High transmission efficiency, reducing energy consumption
- 100,000 km interval oil change, maintenance-free wheel ends
- Real-time monitoring of key components for enhanced safety
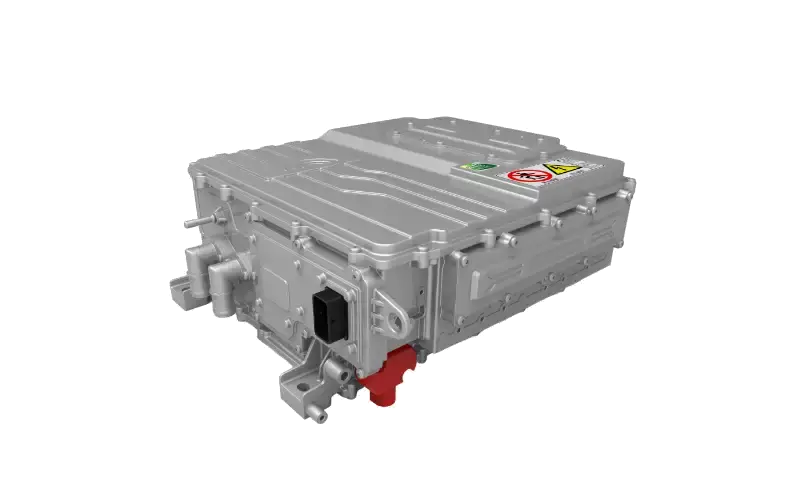
According to clients’ different requirements, we can provide standalone MCUs or high-voltage integrated controller systems, integrating MCU, PDU, DC-DC, and steering and braking DC/AC.Â
Note: Controllers are usually supplied as part of the electric powertrain system and are not sold separately.
ISO 26262 Compliance
Functional safety requirements and software/hardware development meet ASIL C standards.
Dual-Integration Design
Combines functional and physical integration to significantly reduce size, weight, and manufacturing costs.
Dual-Inverter Control Technology
Minimizes losses and achieves a maximum efficiency of 98.5%.
Modular & Scalable Architecture
Designed for flexibility and easy expansion.
Digital Simulation & Optimization
Uses digital modeling for simulation analysis, enabling more efficient and cost-effective component selection.
Advanced EMC Design
Multi-stage filtering, optimized wiring layout, enhanced shielding, and structural improvements ensure Class 5 compliance under no-load conditions.
2. Co-Axial Electric Axles for Buses
The coaxial electric axles for buses integrate the motor and axle into a single unit. The electric motor is arranged coaxially with the axle housing, resulting in a more compact structure and a highly concentrated power system. This design optimizes the chassis layout, reduces weight, increases transmission efficiency, lowers energy consumption, extends range, and enhances the reliability of the motor and core transmission components.
*Parameters may differ depending on the configuration and vehicle model. Certain specifications can be customized. For more information, please contact us at contact@BrogenEVSolution.com
Model | OEEP6 | OEEP8 | OEEP8-B | OEEP13 |
 | ![]() | ![]() | ![]() | ![]() |
Rated load capacity | 3500 kg | 5500 kg | 5500 kg | 8500 kg |
Maximum output torque | 5700 N.m | 7285 N.m | 5240 N.m | 13000 N.m |
Gear ratio | 16.5 | 14.57 | 14.57 | 19.89 |
Rated/peak motor power | 60/130 kW | 90/160 kW | 60/140 kW | 80/150 kW |
Rated/peak motor torque | 145/350 N.m | 200/500 N.m | 160/360 N.m | 230/650 N.m |
Rated/peak motor speed | 4000/12000 rpm | 4300/9000 rpm | 3580/12000 rpm | 3400/10000 rpm |
Coaxial Motor and Axle Integration
Industry-leading integration technology with the most compact chassis footprint and the lightest weight in its class.
Symmetrical Motor Layout
Ensures balanced unsprung mass distribution, minimizing impact on suspension load conditions compared to parallel-axis e-axles.
High-Precision Helical Gear Transmission
Highly integrated reducer for reduced weight, high efficiency, low noise, and extended lifespan.
High-Strength Cast Axle Housing
Designed for heavy loads, with a smooth curved inner cavity to reduce oil churning losses.
- Compact co-axial e-axle layout for better chassis integration
- Lightweight design for improved efficiency
- Precision-ground gears for low noise and comfort
- High transmission efficiency, reducing energy consumption
- 100,000 km interval oil change, maintenance-free wheel ends
- Real-time monitoring of key components for enhanced safety
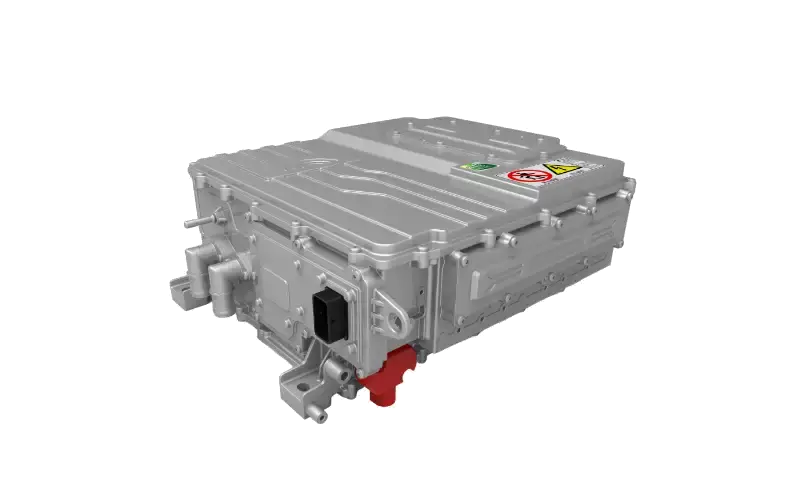
According to clients’ different requirements, we can provide standalone MCUs or high-voltage integrated controller systems, integrating MCU, PDU, DC-DC, and steering and braking DC/AC.Â
Note: Controllers are usually supplied as part of the electric powertrain system and are not sold separately.
ISO 26262 Compliance
Functional safety requirements and software/hardware development meet ASIL C standards.
Dual-Integration Design
Combines functional and physical integration to significantly reduce size, weight, and manufacturing costs.
Dual-Inverter Control Technology
Minimizes losses and achieves a maximum efficiency of 98.5%.
Modular & Scalable Architecture
Designed for flexibility and easy expansion.
Digital Simulation & Optimization
Uses digital modeling for simulation analysis, enabling more efficient and cost-effective component selection.
Advanced EMC Design
Multi-stage filtering, optimized wiring layout, enhanced shielding, and structural improvements ensure Class 5 compliance under no-load conditions.
3. Distributed Drive Electric Axles for Buses
*Parameters may differ depending on the configuration and vehicle model. Certain specifications can be customized. For more information, please contact us at contact@BrogenEVSolution.com
Model | OEEA1100K | OEEA1400K | OEEA2100N |
 | ![]() | ![]() | ![]() |
Rated Axle Load | 9000 kg | 9000 kg | 13000 kg |
Maximum Output Torque | 2×6142 N.m | 2×6142 N.m | 2×10776 N.m |
Maximum Output Power | 2×90 kW | 2×120 kW | 2×160 kW |
Maximum Wheel Speed | 540 rpm | 541 rpm | 430 rpm |
Tire Specs (Standard) | 305/70R22.5 | 275/70R22.5 | 275/70R22.5 |
Gear Ratio | 17.55 | 17.55 | 18.58 |
eAxle Assembly Weight | 750 kg | 850 kg | 1080 kg |
Rated Voltage | 540 VDC | 540 VDC | 540 VDC |
Electronic Differential System (EDS)
The advanced Electronic Differential System (EDS) has been proven over millions of kilometers
Electronic Acceleration Slip Regulation (EASR)
Leading torque control algorithm with millisecond response time enhances safety and reduces tire wear
Intelligent Regenerative Braking System (IRBS)
Ensure braking performance while recovering energy in various driving conditions to reduce energy consumption and extend driving range
Intelligent Electronic Stability System (IESS)
Adjust the torque of various components in real-time based on the vehicle status to ensure safety and stability under extreme conditions
- Compact e-axle layout for better chassis integration
- Enables a wide passage and low-floor design, enhancing overall vehicle safety and comfort
- Dual-tire configuration ensures driving stability
- Reliable electronic differential system with a tire replacement interval of over 100,000 km
- The gearbox's symmetrical forward and reverse torque improves energy regeneration efficiency by 100%, extending driving range
- The distributed drive approach enhances safety redundancy, ensuring that if one motor fails, the other continues to operate
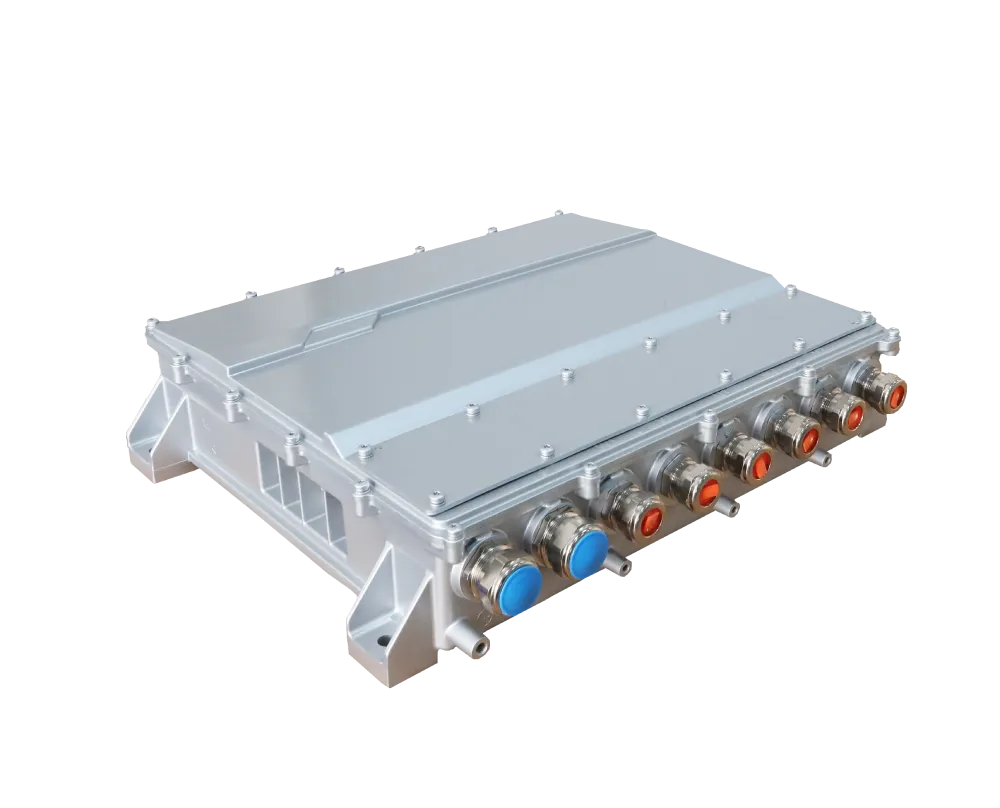
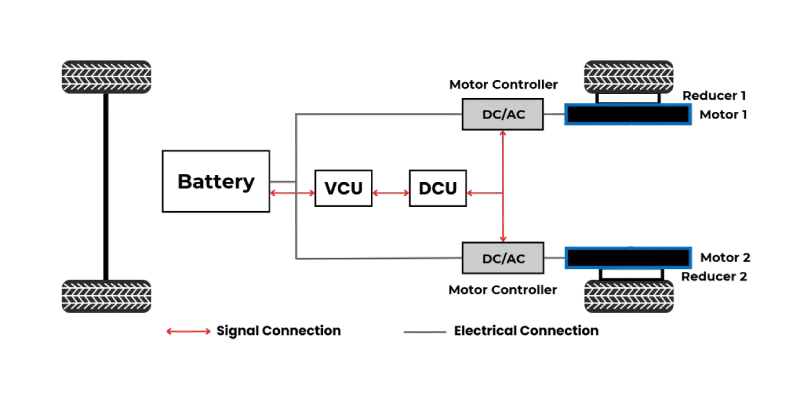
For distributed drive electric axles for buses, our solution includes the necessary controllers, such as the integrated motor control unit (MCU), and the distributed drive control unit (DCU), which also incorporates the transmission control unit (TCU).
Comprehensive Torque Control System
Ensures precise and efficient power distribution
Advanced Software Decoupling
Enhances system responsiveness and integration
Electronic Differential Module
Enables intelligent torque distribution between wheels
Electronic ASR (Anti-Slip Regulation)
Improves vehicel stability on low-traction surfaces, ensuring smooth starts and acceleration
Electronic ESP (Electronic Stability Program)
Enhances safety and maneuverability on icy or snowy roads by adjusting wheel torque and speed to optimize yaw control
Applications
Our electric bus axles have been successfully deployed at scale in both domestic and international public transport fleets. They are widely used in city buses, coaches, airport shuttles, and trolleybuses ranging from 10 to 18 meters in length. These systems have proven reliable in diverse operating environments – from hot climates like the United Arab Emirates to cold, high-altitude regions in Central Asia.
The system is now in mass production and ready for large-scale deployment.
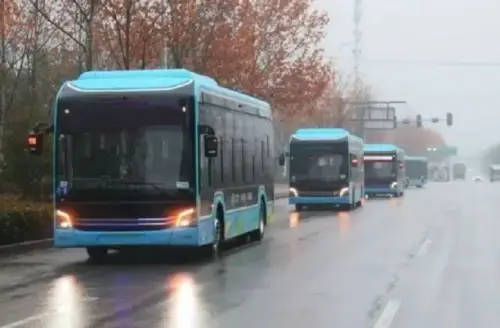
Hydrogen buses with 320 kW eaxles.
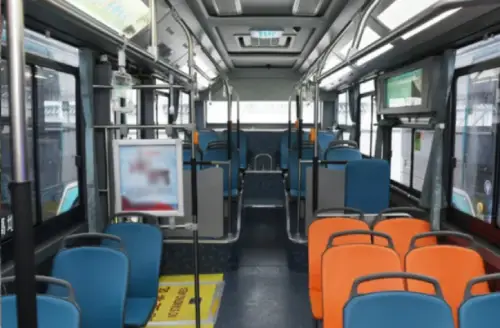
Buses with the low-floor design.

Airport shuttle bus with 14T eaxles.
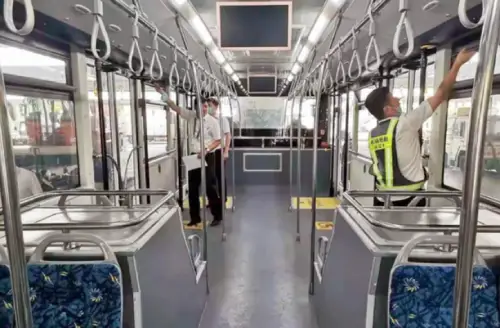
Pure electric buses with our eaxles.
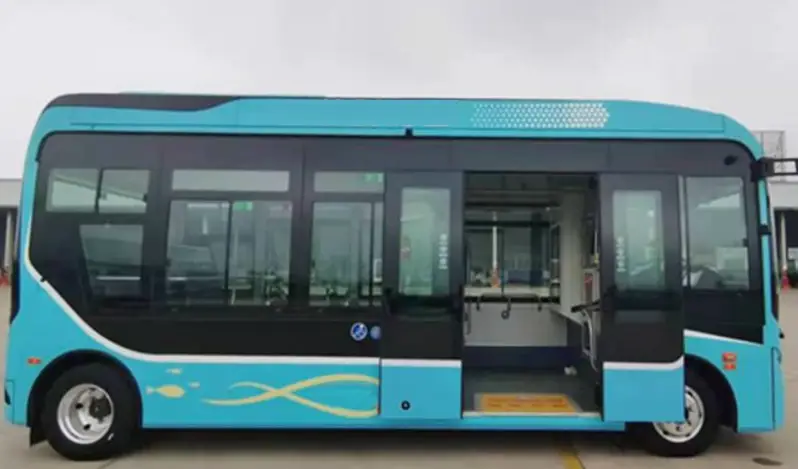
Minibus with 130 kW coaxial e-axle.
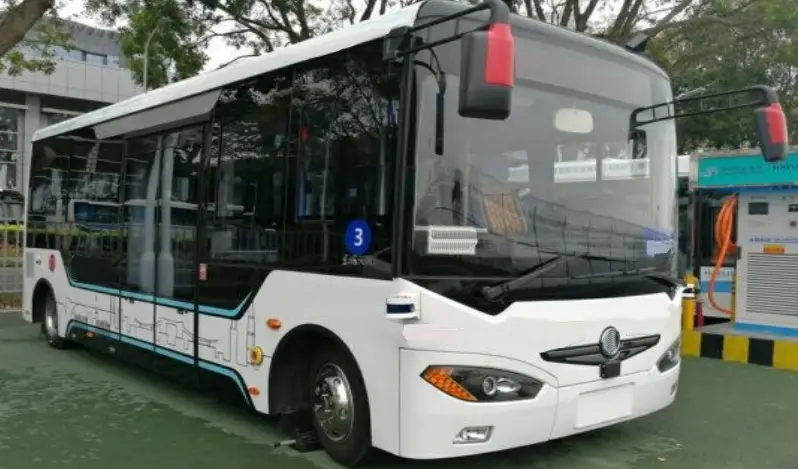
City bus with 130 kW coaxial e-axle.
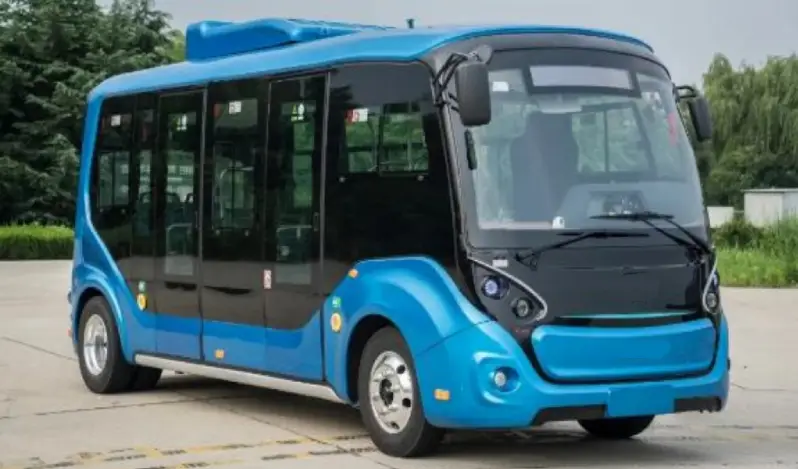
Minibus with 130 kW coaxial e-axle.
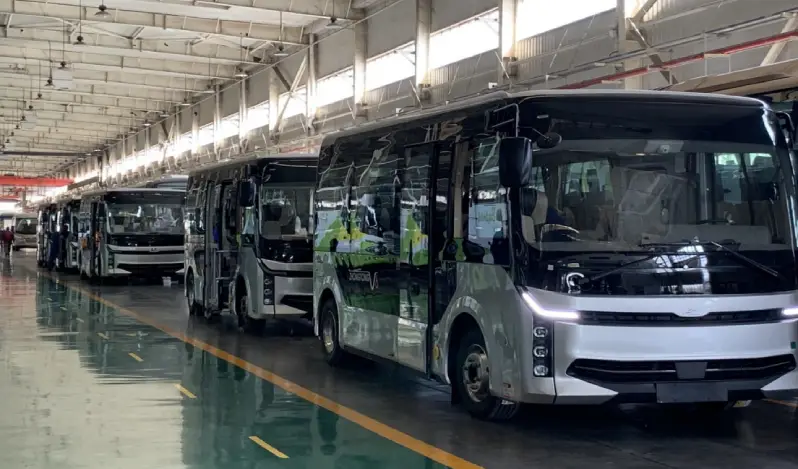
Minibus with 130 kW coaxial e-axle.
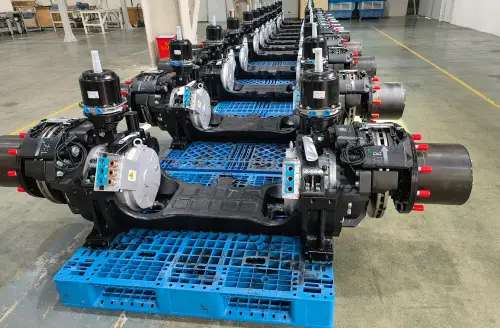
Electric Portal Axle Factory
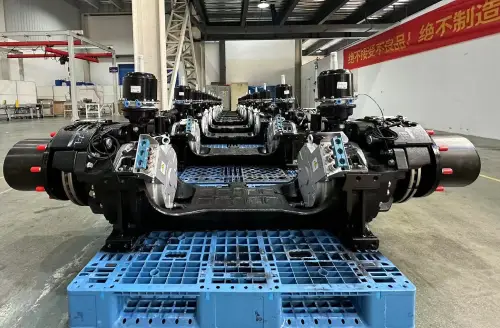
Electric Portal Axle Factory
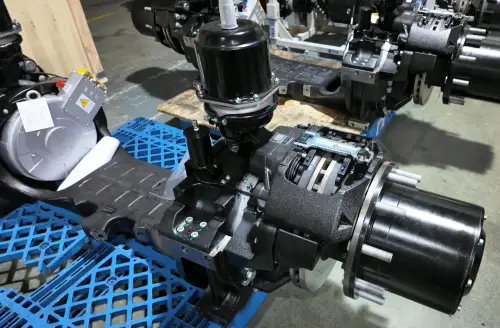
Electric Portal Axle Factory
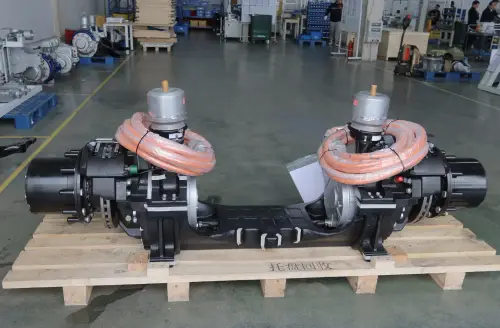
Electric Portal Axle Factory
How We Work
Navigating Our Process
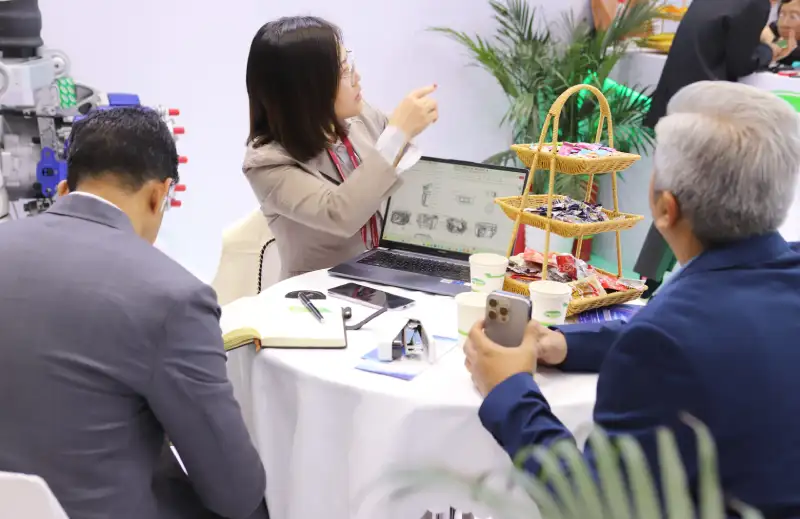
Demand Analysis & Project Evaluation
Once we receive your inquiry, our experts will connect with you within two business days to understand your specific requirements for the EV solution and conduct an initial feasibility evaluation of your project.
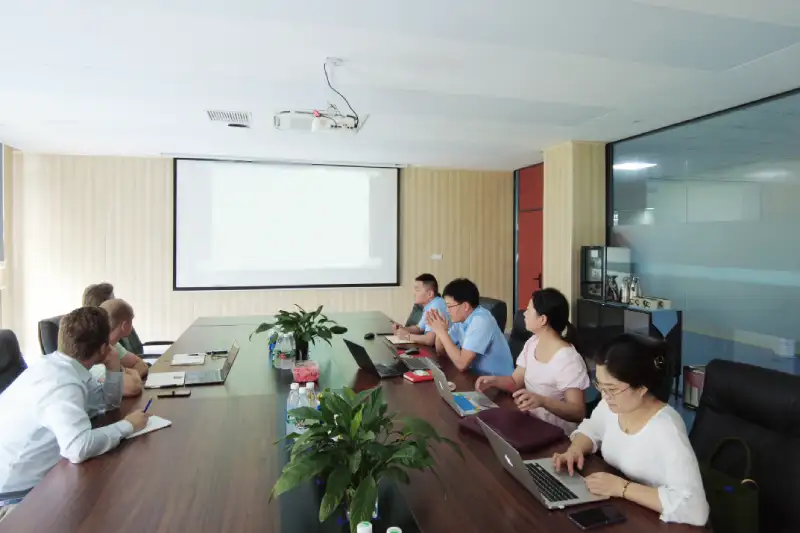
Project & Technical Coordination
If the project is deemed feasible, our engineering team will collaborate closely with your team on both hardware and software aspects to develop a viable solution. We will also provide a detailed quotation based on the technical requirements.
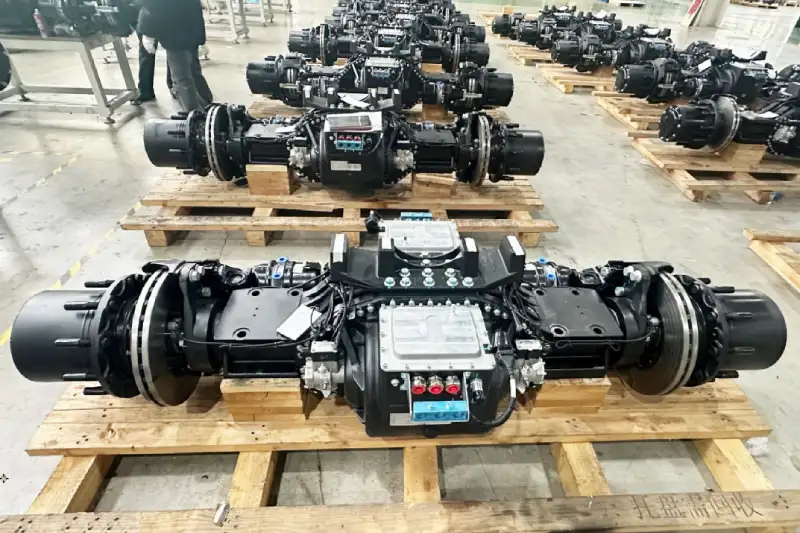
Development, Manufacturing & Testing
For customized or modified systems, we proceed with product development, including hardware and software adaptations. Our EV systems undergo rigorous testing to ensure quality, reliability, and full functionality before deployment.
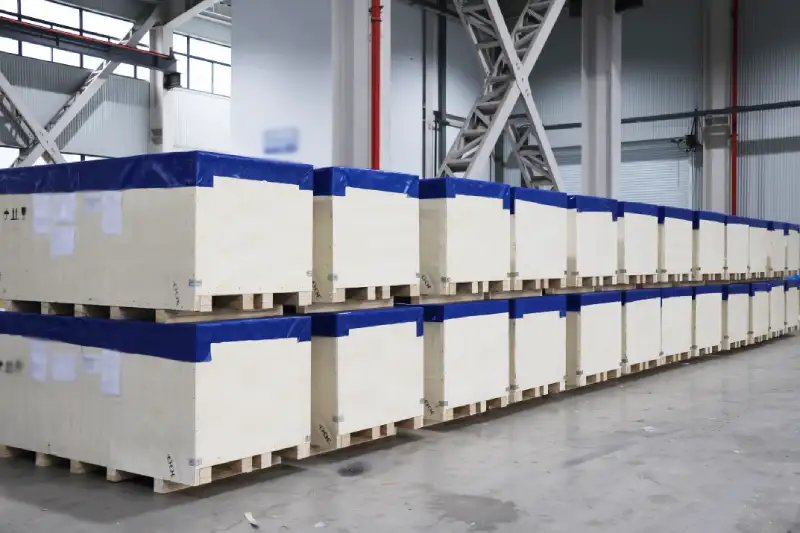
In-Time Global Shipping & Delivery
We have established strong partnerships with international shipping providers, ensuring safe and timely delivery of products to your specified location. This guarantees a smooth and efficient deployment of your EV project.
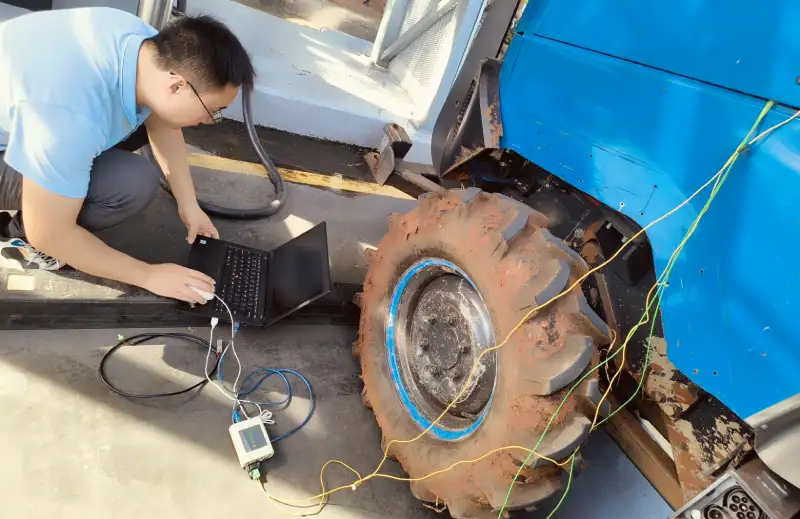
Full-Stage Remote/Onsite Technical Support
We provide technical support throughout the entire project lifecycle, including consultancy, hardware and software development, calibration, and both onsite and remote debugging, ensuring optimal performance and long-term success.
Frequently Asked Questions
Our e-axle solutions are at different stages depending on the model. Most of them are currently in mass production and have been widely deployed in both domestic and international markets. For details on a specific model or application, please contact us through the table below.
Our electric axles are suitable for public transport vehicles such as city buses, articulated buses, coaches, trolleybuses, rubber-tired metro trains, and more.
For bulk orders, we can replace components with the customer-specified brands upon request.
We follow a strict quality management system. However, for clients we haven’t yet partnered with, these documents are considered confidential and cannot be shared.
We provide standard or extended warranties depending on the product. For bulk orders, we prepare spare parts in advance to minimize downtime and ensure efficient handling of any warranty claims.
Contact Us
Get in touch with us by sending us an email, using the Whatsapp number below, or filling in the form below. We usually reply within 2 business days.
Email: contact@brogenevsolution.com
Respond within 1 business day
Whatsapp: +8619352173376
Business hours: 9 am to 6 pm, GMT+8, Mon. to Fri.
LinkedIn channel
Follow us for regular updates >
YouTube channel
Ev systems introduction & industry insights >