AMT Powertrain System for Battery Electric Buses: Enhancing Efficiency and Performance
The transition to battery electric buses has become a key focus for bus manufacturers and cities aiming to reduce emissions and improve public transport sustainability. In recent years, some bus manufacturers have shifted from traditional direct-drive systems to e-powertrain systems that include Automated Manual Transmission (AMT) for battery electric buses (BEB). But what does this mean for electric bus performance, and how does it affect the overall driving experience?
What is an AMT Powertrain System for BEB?
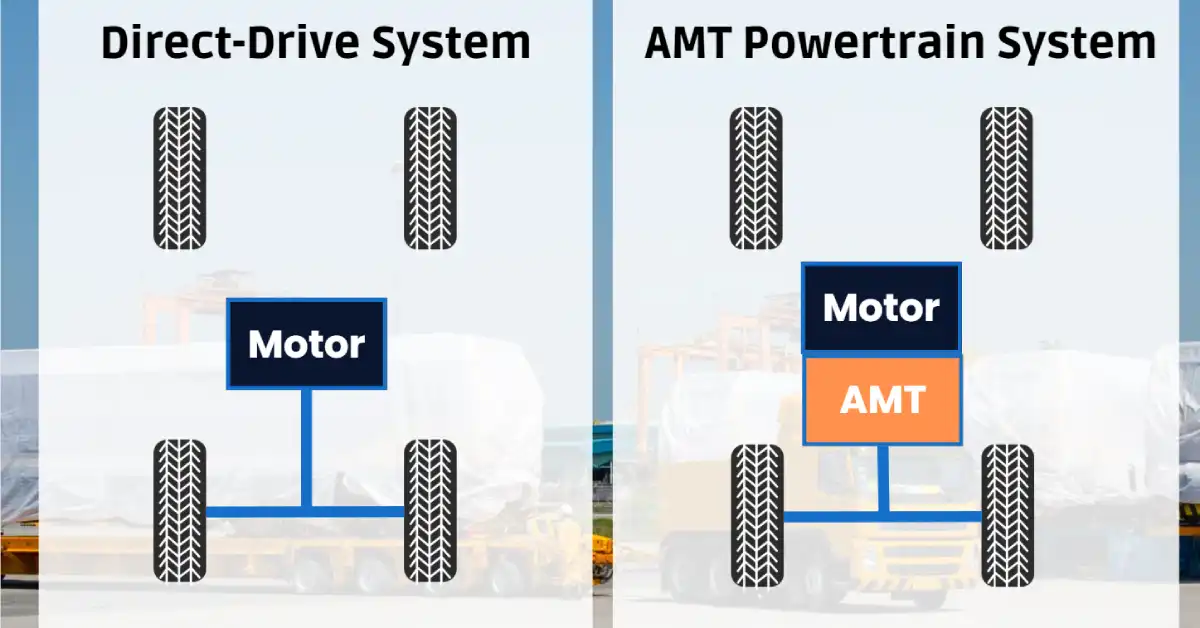
The direct drive system delivers power directly from the motor to the rear axle, offering a simple, reliable, and efficient design. In contrast, the AMT e-powertrain system utilizes a gearshifting mechanism to transmit motor torque to the rear axle, allowing for optimized performance and energy efficiency by adjusting the gear ratios.
AMT Powertrain System vs Direct Drive System: Performance
In fact, not all BEBs should be equipped with an AMT system. Compared to the conventional direct-drive system, electric buses with AMT have both advantages and disadvantages. Let’s take a 12-meter battery electric bus as an example to focus on the power performance comparison between AMT powertrain and direct-drive systems.
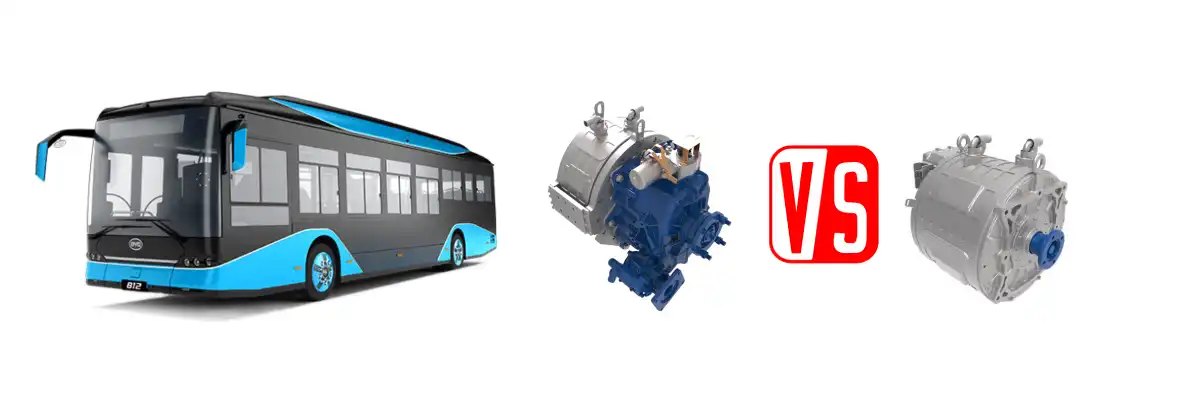
System Parameters | AMT Powertrain | Direct Drive System |
Total Weight | 260 kg | 364 kg |
Maximum Torque | 3730 N.m | 2800 N.m |
Length | 716 mm | 470 mm |
Width | 614 mm | 603 mm |
Height | 592 mm | 592 mm |
For a 12-meter BEB, the electric motor in the AMT powertrain system has a rated power of 80 kW, whereas the direct-drive system uses a more powerful 100 kW electric motor. However, the motor in the AMT system can reach a maximum speed of 3500 rpm, which is higher than the motor speed (3000 rpm) in the direct-drive system. Electric buses with AMT powertrain systems offer better hill-climbing ability (23%) and can achieve higher speeds (14%), though the acceleration time may be slightly longer due to the shifting process.
Motor Parameters | AMT Powertrain System | Direct-Drive System |
Rated Power | 80 kW | 100 kW |
Peak Power | 140 kW | 200 kW |
Rated Torque | 600 N.m | 1250 N.m |
Peak Torque | 1000 N.m | 2800 N.m |
Maximum Speed | 3500 rpm | 3000 rpm |
Maximum Gradeability | 23% | 14% |
Maximum Vehicle Speed | 116 km/h | 107 km/h |
0-50 km/h Time | 16 s | 13.4 s |
In terms of system efficiency during normal operation, the two types of systems are quite different. When comparing system efficiency at different speeds, we find that the direct-drive system performs more efficiently in the 40-60 km/h range, with lower overall energy consumption. However, in the speed ranges below 40 km/h and above 60 km/h, the AMT powertrain system outperforms, showing lower overall energy consumption. Overall, when considering a wider range of driving conditions, the AMT system tends to offer better energy efficiency.
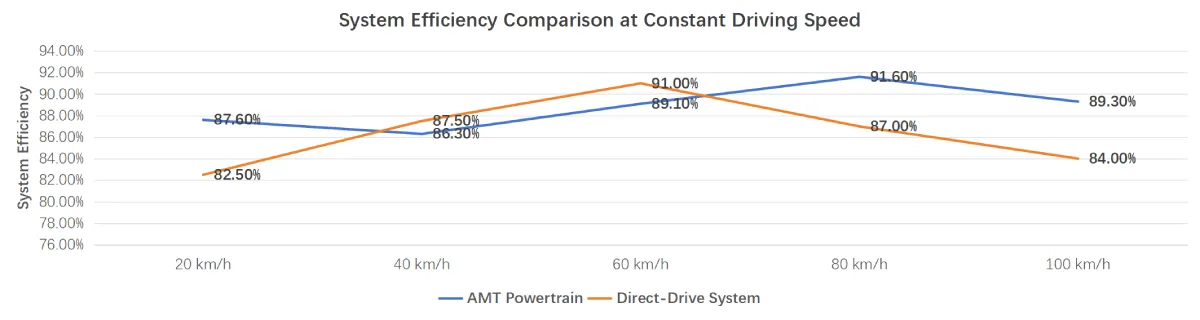
In typical urban driving conditions, the electric bus equipped with the AMT system has a simulated energy consumption of 68.3 kWh per 100 km, with actual test results showing 68.6 kWh per 100 km. In contrast, the electric bus using a direct-drive system has a simulated consumption of 72.5 kWh per 100 km, with test results showing 73.3 kWh per 100 km.
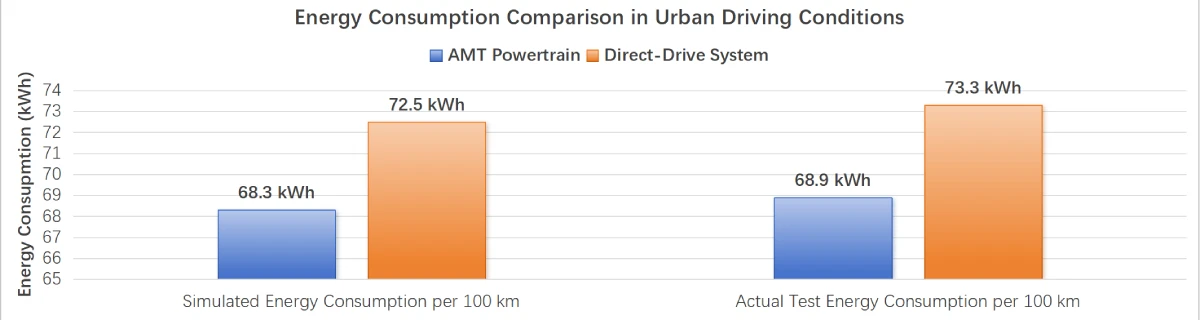
AMT Powertrain System vs Direct Drive System: Cost Considerations
Cost is another significant factor for bus manufacturers. While the AMT system offers enhanced perofrmance, the cost implications depend on the bus’s torque demands. For buses with lower torque requirements, the direct drive system may be more cost-effective. However, for high-torque applications, such as large electric buses, the AMT system proves more economical. By using smaller motors with the AMT system, bus manufacturers can reduce motor costs without sacrificing power, resulting in a more affordable overall vehicle.
In essence, when the required torque exceeds 1500 N.m, the AMT powertrain system becomes the more cost-effective choice. Larger buses with higher power demands benefit the most from AMT technology, offering both cost savings and better performance.
AMT Powertrain System vs Direct Drive System: Comfort & Reliability
Beyond performance and cost, comfort and reliability are crucial factors for any bus manufacturer. AMT powertrain systems do introduce gear shifts, which can cause slight interruptions in power delivery and reduce comfort compared to direct drive systems, which offer smoother acceleration. However, technological improvements in AMT design can mitigate these discomforts. For example, the shifting process can be optimized to minimize interruptions, thus improving the passenger experience.
From a reliability perspective, the complexity of the AMT system theoretically makes it less reliable than direct drive systems. However, through rigorous design and quality control, these concerns can be addressed. For instance, AMT products can be designed with durability in mind, achieving similar reliability levels as direct-drive systems. Additionally, the AMT system’s lightweight design, compared to traditional systems, contributes to overall vehicle weight reduction.
Our AMT Powertrain Systems for Electric Commercial Vehicles
At Brogen, we offer e-powertrain systems based on AMT technology, utilizing PMSM for drive. The AMT is co-axially connected to the motor, taking advantage of the gearbox’s speed control and torque-boosting features. This enables a smaller motor to achieve the same performance as a larger direct-drive motor, while also enhancing the vehicle’s adaptability and efficiency.
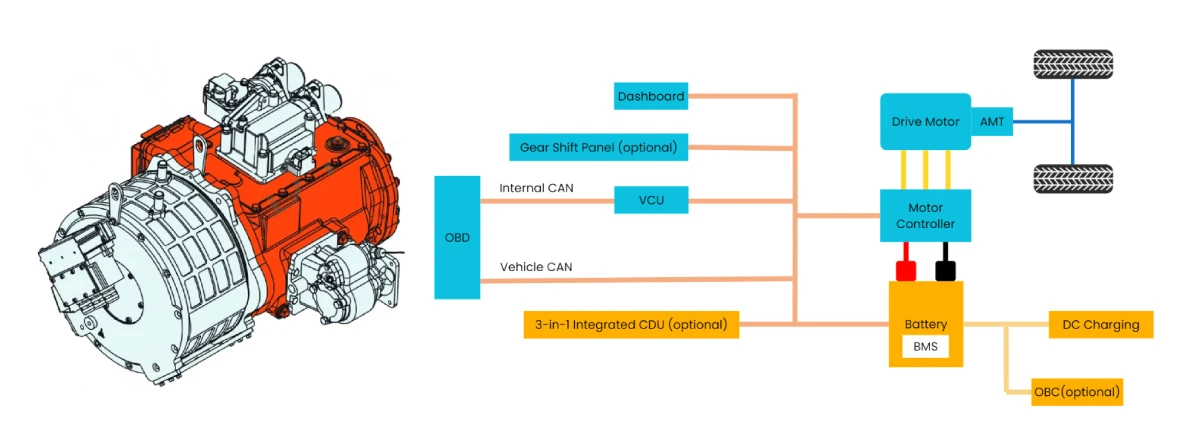
Our e-powertrain system with AMT ranges from 60 kW to 550 kW, making it suitable for applications in buses, trucks, heavy commercial vehicles, municipal vehicles, and loaders.
Motor Power / Torque | Transmission | Maximum Motor Speed | Maximum Output Torque | Applicable Vehicles |
300/500 N.m, 60/120 kW | 2-speed: 2.73/1 | 5000 rpm | 1365 N.m | 4.5-7T truck |
350/850 N.m, 75/120 kW | 2-speed: 2.741/1 | 5000 rpm | 2330 N.m | 7-12T truck |
500/1100 N.m, 80/160 kW | 2-speed: 2.741/1 | 4500 rpm | 3015 N.m | 8-10M bus, 11-14T truck |
500/1300 N.m, 120/185 kW | 2-speed: 2.741/1 | 3500 rpm | 3380 N.m | 10M, 12M bus |
500/1100 N.m, 100/185 kW | 4-speed: 6.61/3.52/1.89/1 | 3500 rpm | 7000 N.m | 14-18T truck, specialty vehicles |
850/1950 N.m, 180/300 kW | 4-speed: 8.39/3.54/1.74/1 | 3500 rpm | 16360 N.m | 25-30T truck |
1200/2400 N.m, 250/380 kW | 4-speed: 8.39/3.54/1.74/1 | 3500 rpm | 20136 N.m | 31-49T truck |
1500/2400 N.m, 270/405 kW | 4-speed: 8.39/3.54/1.74/1 | 3500 rpm | 20136 N.m | 35-60T truck |
1500/2400 N.m, 300/450 kW | 4-speed: 8.39/3.54/1.74/1 | 3500 rpm | 20136 N.m | 60-90T truck |
1500/2600 N.m, 280/420 kW | 4-speed: 8.39/3.54/1.74/1 | 3500 rpm | 21814 N.m | 50-70T truck |
1650/2800 N.m, 315/510 kW | 4-speed: 8.67/4.57/2.29/1 | 3500 rpm | 24276 N.m | 70-100T truck |
1800/2800 N.m, 360/550 kW | 4-speed: 8.67/4.57/2.29/1 | 3500 rpm | 24276 N.m | 70-100T truck |
440/1200 N.m, 140/200 kW | 2-speed: 5.43/1.95 | 8300 rpm | 6516 N.m | 5-6T loader |
540/1382 N.m, 158/340 kW | 2-speed: 5.43/1.95 | 7600 rpm | 7500 N.m | 7T loader |
In terms of smoothness of power delivery, we employ high-speed motors, with the shifting point raised to over 3500 rpm. In a single operational cycle, the number of gear shifts is reduced from 24 to 12, making the shift process virtually imperceptible to passengers, thus improving comfort. Regarding reliability, our innovative design and quality control ensure that the failure rate of AMT products is close to that of direct-drive systems. Currently, our powertrain systems have been supplied in bulk to various bus chassis manufacturers, such as Zhongtong, Golden Dragon, Foton, etc.
Discover our public transport solutions here: https://brogenevsolution.com/public-transport-electrification-solutions/
Business inquiry: contact@brogenevsolution.com
Contact Us
Get in touch with us by sending us an email, using the Whatsapp number below, or filling in the form below. We usually reply within 2 business days.
Email: contact@brogenevsolution.com
Respond within 1 business day
Whatsapp: +8619352173376
Business hours: 9 am to 6 pm, GMT+8, Mon. to Fri.
LinkedIn channel
Follow us for regular updates >
YouTube channel
Ev systems introduction & industry insights >