Blade Battery Technology
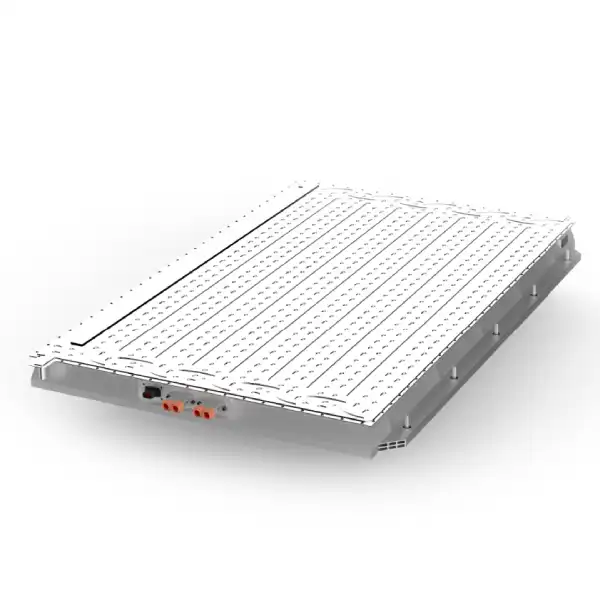
The Blade Battery technology, developed by BYD, is redefining what’s possible in EV energy storage. With its LFP chemistry and module-free design, it delivers over 50% higher volumetric efficiency, packing more energy into the same space while achieving energy density levels comparable to ternary lithium batteries. Beyond performance, Blade Batteries set a new benchmark for safety, with minimized heat generation, rapid heat dissipation, and outstanding results in puncture and durability tests.
At Brogen, we make this advanced technology accessible to small and mid-sized OEMs who often face challenges in sourcing top-tier batteries. Our Blade Battery Solutions are tailored for commercial vehicles – trucks, buses, construction equipments, and other specialty vehicles, helping EV manufacturers achieve greater energy density, enhanced safety, and improved competitiveness in the growing EV market.
Email: contact@brogenevsolution.com
Brogen Blade Battery Solution Features
Cost-Saving
LFP+CTP, fewer parts, lower costs for automotive manufacturers
Smaller Size
Reduced pack size, more flexible space for easier layout
Lightweight
Lighter weight of the pack for the lightweight of the whole vehicle
Wide Applications
Standardized battery pack design for all-field applications
Pickup Truck
Medium Truck
Heavy Truck
Passenger Car
Bus
Our Offerings of Blade Battery Solutions
Blade Battery Pack Configurations for Mini Trucks / Vans
The commercial EV battery pack, purpose-built for micro trucks and micro vans, combines advanced Blade Battery technology with a compact, high-safety design. It is widely used in last-mile logistics applications such as express delivery, supermarkets, restaurants, and fresh food distribution, providing customers with a safer, more reliable, and more convenience energy solution tailored to the demands of modern urban logistics.
- Application examples: micro truck, van, pickup truck
- Layout location: under the chassis
- Battery energy range: 10 kWh to 50 kWh
- With BMS+PDU
- Typically appears as a single pack
System Features
Exceptional Safety
Built with high-strength LFP Blade Cells, offering long life and outstanding protection.
High Energy Density
Up to 140 Wh/kg, enabling lighter vehicles, extended driving range, and increased payload capacity.
Flexible Configurations
Available in 10-50 kWh options, with interchangeable energy levels in the same pack size for easier vehicle integration.
All-Weather Performance
Standard electric heating and optional liquid cooling ensure efficient operation across a wide range of climates.
Technical Parameters
Pack | Energy | Voltage | Cell capacity | Size |
B01 | 10 kWh | 102.4 V | 100 Ah | 660*840*130 mm |
PC5 | 24 kWh | 243.2 V | 100 Ah | 1238*840*235 mm |
B04 | 35 kWh | 352 V | 100 Ah | 1000*840*210 mm |
B05 | 42.3 kWh | 313.6 V | 135 Ah | 1120*880*210 mm |
B06 | 44.9 kWh | 332.8 V | 135 Ah | 1120*880*210 mm |
B07 | 50 kWh | 332.8 V | 150 Ah | 1120*880*210 mm |
Blade Battery Pack Configurations for Light / Medium Trucks
These blade battery packs are purpose-built for light- and medium-duty trucks, and designed for the demands of urban short-haul logistics. Ideal for applications such as e-commerce, express delivery, moving services, and postal operations, it provides customers with a safer, more reliable, and more convenient end-to-end battery solution, ensuring worry-free use in daily operations.
- Application examples: light truck, medium truck
- Layout location: in the middle and on both sides of the vehicle, behind the driver’s cabin
- Battery energy range: 40 – 160 kWh
- 1P – 2P single pack or multiple packs in series connection
- 40 – 100 kWh for light trucks
- 80 – 160 kWh for medium trucks
System Features
Superior Safety
Powered by 7S Blade Batteries that have passed rigorous safety tests, including nail penetration, crush, overcharge, and furnace heating, with comprehensive active and passive protection.
High Energy Density
Up to 155 Wh/kg, enabling lighter vehicle design, longer driving range, and increased payload capacity.
High Integration
Mid-pack design with integrated power distribution module and BMS, enhancing vehicle performance and overall competitiveness.
All-Weather Reliability
Equipped with an electric heating system and optional direct cooling or liquid cooling, ensuring efficient operation in all conditions - whether extreme heat, cold, or rain.
Technical Parameters
Pack | Energy | Voltage | Cell capacity | Size |
B10 | 41.6 kWh | 268.8 V | 155 Ah | 1560*470*240 mm |
B11 | 22.6 kWh | 128 V | 177 Ah | 920*470*240 mm |
B12 | 27.1 kWh | 156.3 V | 177 Ah | 1060*470*240 mm |
B13 | 18.3 kWh | 381.6 V | 48 Ah | 1246*578*226 mm |
Blade Battery Pack Configurations for Heavy Trucks
This blade battery pack series is designed to cover mainstream applications in heavy-duty trucks, construction machinery, and specialty vehicles. It is widely deployed in urban construction waste transport, steel plant shuttling, mining operations, ports, and bulk material logistics such as coal and aggregates. Leveraging advanced Blade Battery technology, it delivers a safer, more reliable, and more convenient integrated energy solution, helping make green energy adoption seamless across industries.
- Application examples: heavy-duty truck, tractor, trailer, mining, construction equipment
- Layout location: behind the driver’s cabin, between the driver’s cabin and cargo
- Battery energy range: 100 – 900 kWh
- 1P – 6P multiple packs in series connection
System Features
Longer Lifespan
Large-format stacking technology combined with high-temperature resistant ceramic battery design ensures extended cycle life.
High Capacity
Industry-leading mass-produced packs with 96.2 kWh per unit, with multi-pack configurations to meet the energy requirements of most heavy-duty trucks.
Battery-Swap Ready
Supports integrated charging and swapping, with a triple-pack configuration that meets the market's standard 282 kWh demand, providing higher energy and longer range.
High Integration
Compared to traditional CTP designs, the B24 battery pack improves volumetric cell-to-pac k ratio (VCtP) by 10%, volumetric energy density (VED) by 20%, gravimetric energy density (GED) by 10%, and reduces components by 10%, delivering greater efficiency and simpler assembly.
Technical Parameters
Pack | Energy | Voltage | Cell capacity | Size |
B20 | 76 kWh | 230.4 V | 330 Ah | 1900*627*240 mm |
B21 | 75 kWh | 307.2 V | 244 Ah | 1900*627*240 mm |
B22 | 66.5 kWh | 201.6 V | 330 Ah | 1700*627*240 mm |
B23 | 65.6 kWh | 268.8 V | 244 Ah | 1700*627*240 mm |
B24 | 96 kWh | 601.6 V | 160 Ah | 2000*690*270 mm |
Blade Battery Pack Configurations for Buses
This blade battery pack series is designed for buses, coaches, construction machinery, and specialty vehicles, featuring high-safety Blade Battery Cells. Widely applied in city buses, airport shuttles, and other commercial vehicles, the packs are configured to match the vehicle’s total energy requirements, providing customers with a safer, more reliable, and more convenient integrated EV battery solution.
- Application examples: bus, coach
- Layout location: on the top, rear and bottom of the bus
- Battery energy range: 100 – 500 kWh
- Multiple packs in series & parallel connection
System Features
Enhanced Safety
Equipped with a fire suppresion system and high-safety LFP Blade Battery cells.
High Compatibility
Compact yet high-capacity design, fully compatible with mainstream battery enclosures.
Wide Coverage
Single-pack and multi-pack configurations cover 100-700 kWh, with multiple energy options in the same dimensions for minimal vehicles adaptation and greater flexibility.
High Energy Density
Advanced module-free CTP technology delivers energy density up to 170 Wh/kg, among the highest in the industry.
Technical Parameters
Pack | Energy | Voltage | Cell capacity | Size |
B30 | 37.5 kWh | 153.6 V | 244 Ah | 1050*627*240 mm |
B31 | 31.2 kWh | 128 V | 244 Ah | 905*627*240 mm |
B32 | 38 kWh | 115.2 V | 330 Ah | 1050*627*240 mm |
B33 | 31.7 kWh | 96 V | 330 Ah | 905*627*240 mm |
Advanced BMS Technology
Type | Image | Composition | Basic Functions | Accuracy |
High-speed Vehicle BMS High Voltage | ![]() |
|
|
|
Low-speed Vehicle BMS Low Voltage | ![]() |
|
| |
How We Work
Navigating Our Process
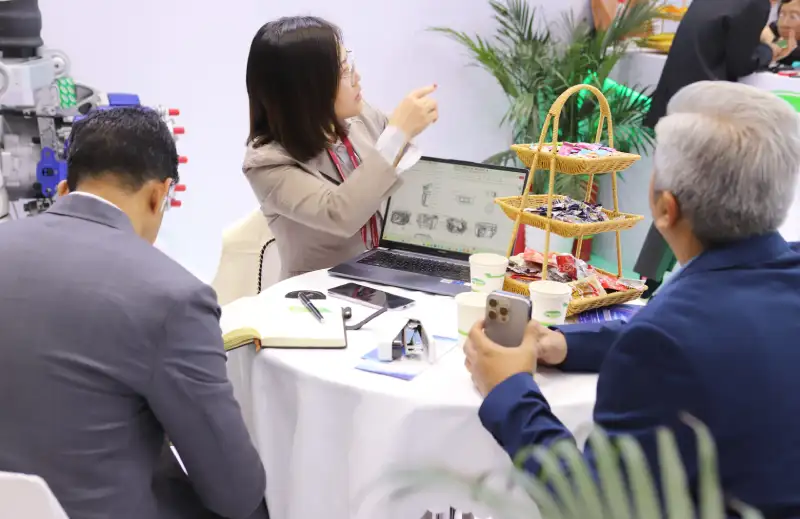
Demand Analysis & Project Evaluation
Once we receive your inquiry, our experts will connect with you within two business days to understand your specific requirements for the EV solution and conduct an initial feasibility evaluation of your project.
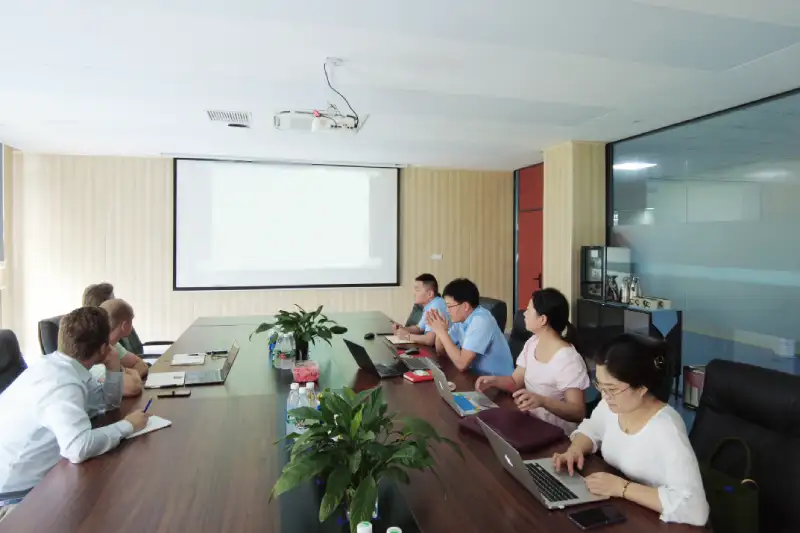
Project & Technical Coordination
If the project is deemed feasible, our engineering team will collaborate closely with your team on both hardware and software aspects to develop a viable solution. We will also provide a detailed quotation based on the technical requirements.
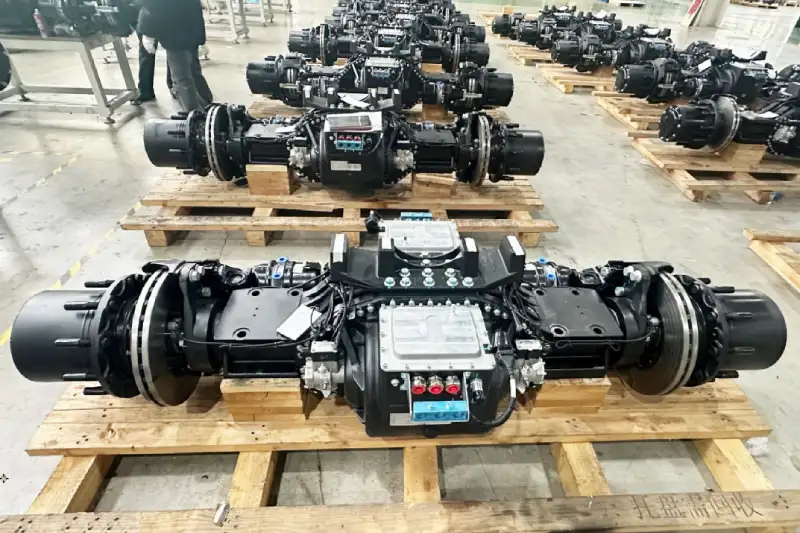
Development, Manufacturing & Testing
For customized or modified systems, we proceed with product development, including hardware and software adaptations. Our EV systems undergo rigorous testing to ensure quality, reliability, and full functionality before deployment.
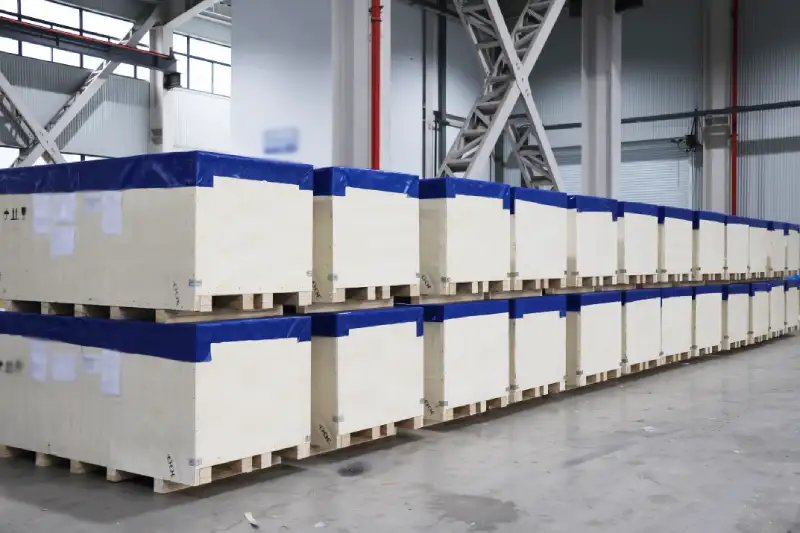
In-Time Global Shipping & Delivery
We have established strong partnerships with international shipping providers, ensuring safe and timely delivery of products to your specified location. This guarantees a smooth and efficient deployment of your EV project.
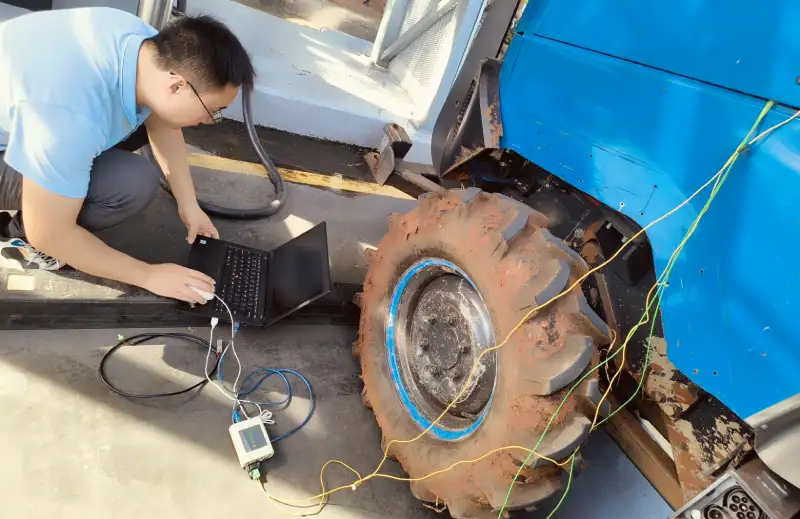
Full-Stage Remote/Onsite Technical Support
We provide technical support throughout the entire project lifecycle, including consultancy, hardware and software development, calibration, and both onsite and remote debugging, ensuring optimal performance and long-term success.
Case Study: Blade Battery Solution for Heavy-Duty Truck Electrification in Drilling Operations
Client Challenge
A leading company in the drilling sector was transitioning its heavy trucks to electric power. The key requirement was a high-capacity battery system of around 500 kWh. However, the available space for battery installation on the truck chassis was limited.
- Using conventional LFP battery packs with a standard C-box design, the maximum capacity achievable was only ~350 kWh with 10 boxes.
- Meeting the 500 kWh target would require developing a new mold, resulting in high development costs, longer lead times, and uncertainties with product maturity.
Brogen EV Solution
Leveraging our expertise and existing resources, we provided the client with the blade battery solution.
- Each blade battery pack delivers 100 kWh of energy, meaning only five packs were needed to achieve the required 500 kWh capacity.
- By adopting CTP (Cell-to-Pack) technology, the blade battery eliminates the need for traditional battery modules, significantly increasing energy density and system efficiency.
- The compact design reduced the overall space requirements, making it perfectly suited for the limited layout available on the heavy truck.
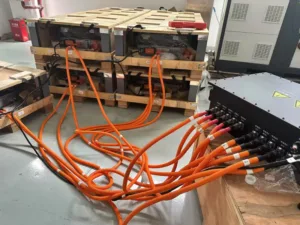
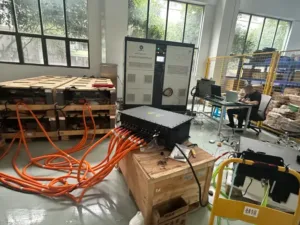
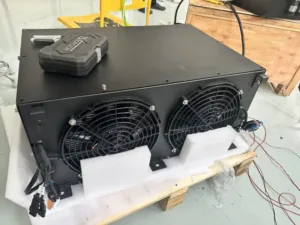
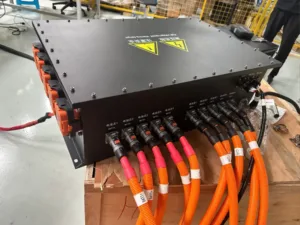
Why Blade Battery?
- Higher energy density: Optimized use of space compared to standard LFP packs.
- Improved efficiency: Fewer structural components, streamlined design.
- Cost-effective & reliable: Avoided the high cost and risks of developing a new mold or unproven product.
- Scalable for heavy-duty use: Designed to meet the demanding energy needs of industrial applications.
Frequently-Asked Questions on Blade Battery Technology
A blade battery is a structural innovation of the Lithium Iron Phosphate (LFP) battery. The battery cells are designed in a long, thin blade shape, hence the name "blade battery". While the blade battery retains the core characteristics of a traditional prismatic cell, it features a more elongated and slim design. The dimensions may vary slightly depending on the model.
The operating principle of a blade battery is similar to that of conventional lithium-ion batteries. during charging, lithium ions move from the positive electrode through the electrolyte to the negative electrode while releasing electrons. The discharge process is the reverse. The unique design of the blade battery allows lithium ions to move more quickly, enhancing both charge and discharge speeds and efficiency. This is consistent with the basic operating principle of all lithium-ion batteries, while the main innovation of the blade battery lies in its structural breakthrough.
The blade battery pack adopts a CTP (Cell-to-Pack) design, bypassing the need for traditional battery modules. Due to the change in cell structure, the battery pack design is also altered. The traditional casing is eliminated, with the blade cells themselves acting as the structural beams and energy storage units. The pack design uses a honeycomb aluminum plate, with two high-strength aluminum plates attached to the top and bottom, with blade cells arranged in between. This design eliminates the need for traditional modules, improving space efficiency and allowing more cells to fit within the same volume.
- Cost Efficiency and Energy Density: The blade battery eliminates the module design, reducing the number of secondary components by 40%. This not only significantly lowers material costs but also boosts the volumetric energy density of the battery pack.
- Structural Efficiency: Unlike traditional batteries that are wound, blade batteries use a stacked design. Compared to the wound structure, the stacked design provides more uniform current density and superior internal heat dissipation, making it more suitable for high-power discharge. As a result, blade batteries exhibit better cycle performance, safety characteristics, and energy density.
The blade battery’s greatest strength is its safety. After structural optimization, it can withstand the most demanding puncture tests without catching fire or exploding, meeting national safety standards.
Puncture tests are considered the most rigorous for power batteries. Even widely used ternary lithium batteries in electric vehicles have not passed these tests. However, blade batteries, when punctured, do not ignite or emit smoke, and the surface temperature remains between 30–60°C.
Additionally, under extreme weight tests, a 46-ton fully-loaded truck was able to crush the blade battery pack without causing leakage, deformation, or smoke. After this test, the battery pack was still functional when reinstalled in the vehicle. These extreme testing conditions demonstrate the blade battery's high safety and strength performance.
Blade batteries support over 5,000 charge and discharge cycles, with the accumulated mileage far exceeding the vehicle's expected service life.
Contact Us
Get in touch with us by sending us an email, using the Whatsapp number below, or filling in the form below. We usually reply within 2 business days.
Email: contact@brogenevsolution.com
Respond within 1 business day
Whatsapp: +8619352173376
Business hours: 9 am to 6 pm, GMT+8, Mon. to Fri.
LinkedIn channel
Follow us for regular updates >
YouTube channel
Ev systems introduction & industry insights >