Electric Axles for Light Trucks
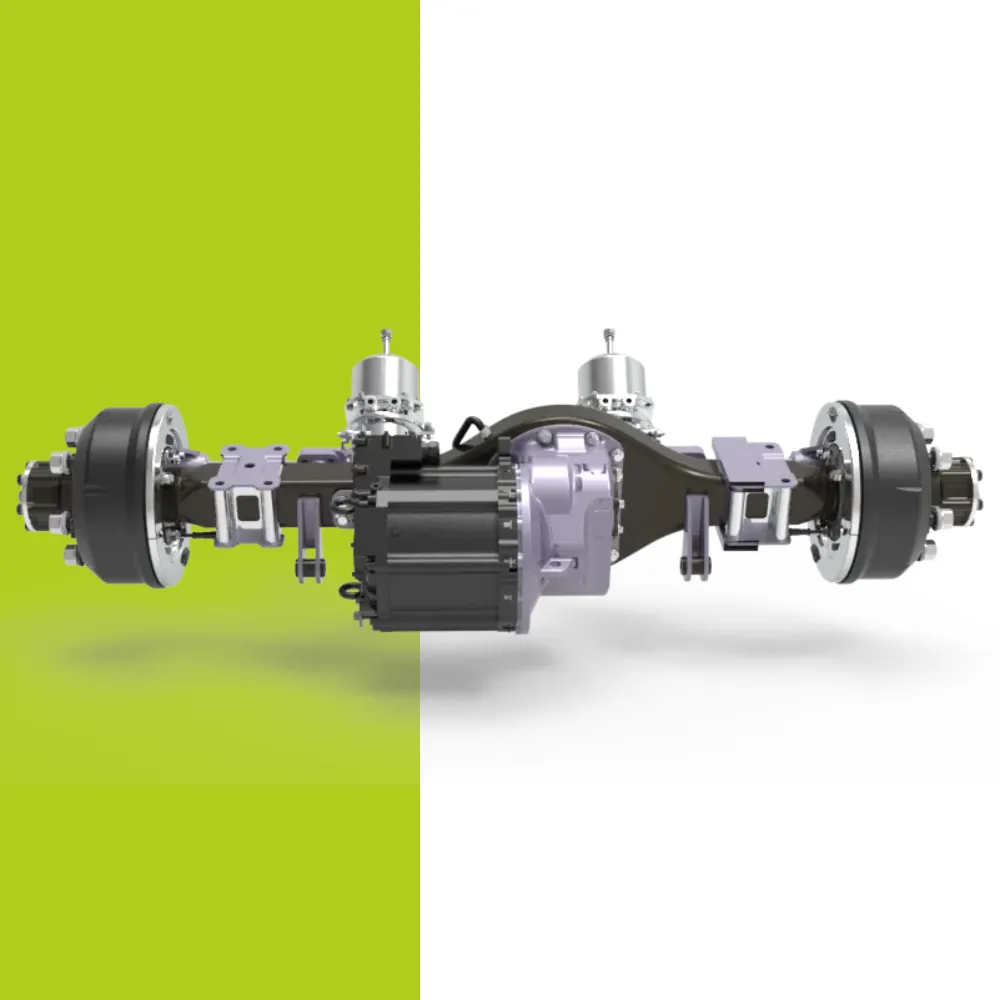
As with the electrification of passenger vehicles, the shift toward electric light commercial vehicles (LCVs) is marked by increasing system integration, higher performance, and enhanced reliability. Our electric axles for light trucks combine the drive motor, reduction gearbox, and drive axle into a single, compact, and lightweight unit.
By eliminating the traditional driveshaft, this design maximizes available space within the chassis, allowing for larger battery capacity and more flexible vehicle layout. The result is improved energy efficiency, extended driving range, and meaningful support for global carbon reduction efforts. Proven in real-world applications, our electric axle systems have been adopted by leading OEMs worldwide, demonstrating outstanding performance and durability.
Email: contact@brogenevsolution.com
Strengthen Your Electric Light Truck Design with eAxles
Central Direct Drive Layout
Motor (or+ Reducer) → Universal Driveshaft → Traditional Drive Axle Assembly (Main Reducer + Differential + Half Shafts) → Wheels
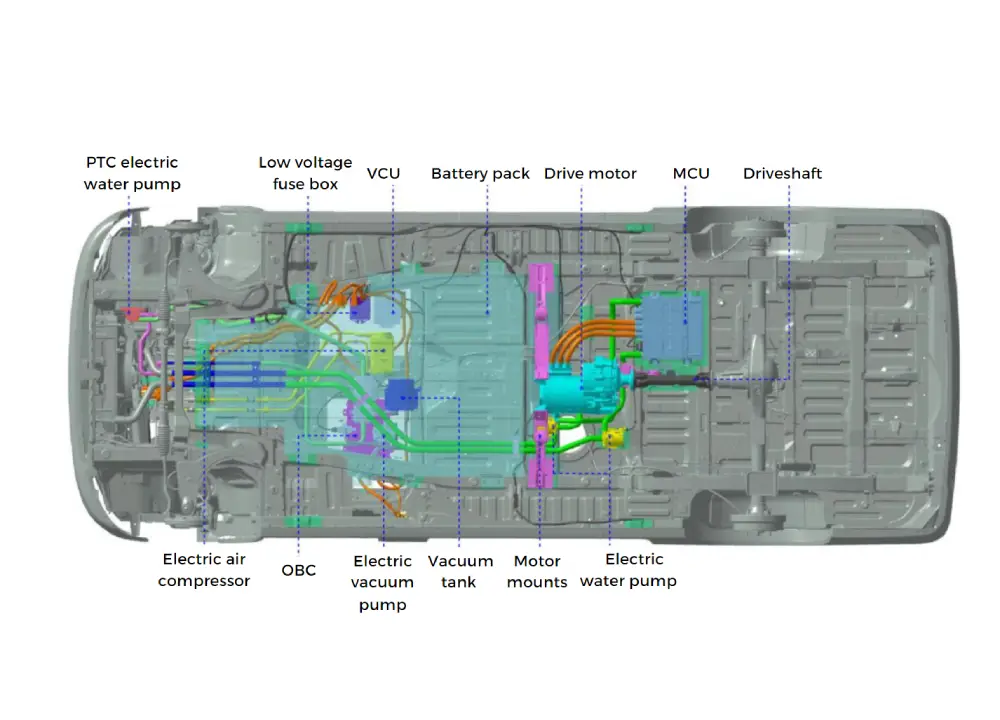
Same structure as the drivetrain of fuel-powered vehicles: use the drive motor to replace the engine. To increase the installation space for the battery pack, the size of the driveshaft is usually reduced and power is transmitted through the original vehicle’s drive axle.
- Short development time but high manufacturing cost.
- Takes up a lot of space in the X-direction, making battery placement difficult.
- Placing the battery up front creates an axle load imbalance, making the front heavier.
- The drive system isn't very light.
Electric Axle Solution Layout
Motor → Drive Axle Assembly (Cylindrical Gear Main Reducer + Differential + Half Shafts) → Wheels
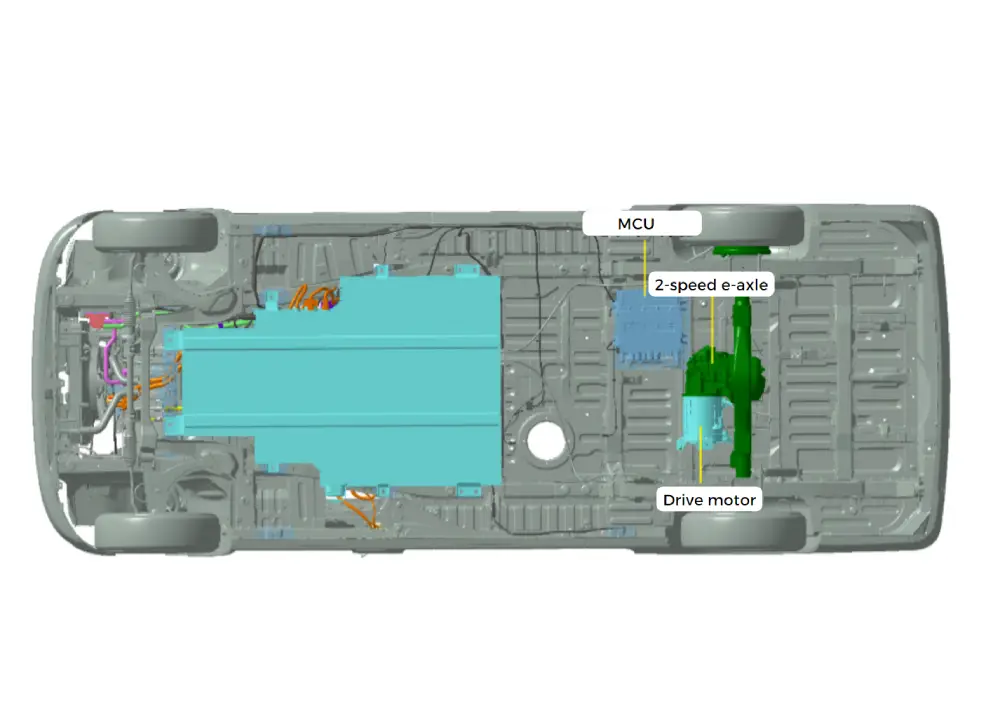
Take the 2.34 T logistic van as an example, the motor and the gearbox are integrated onto the rear axle, allowing for easy installation. This integration reduces the number of components required by 11 types and slashing the overall weight by about 33 kilograms.
- High integration: compact structure, efficient transmission.
- Fully release the X-direction space under the floor, conducive to battery layout.
- Due to the small space occupied, it's convenient to adjust the axle load of the whole vehicle.
- The overall performance is superior.
Brogen Solution Features
Lower Vehicle Integration Costs
By removing the traditional transmission components such as the driveshaft, reducer, fixed mounts, and suspension brackets, the installation cost is significantly reduced compared to traditional central motor direct-drive systems for light commercial vehicles.
Parallel-Axis eAxle Structure
The parallel-axis eAxle design eliminates the need for power redirection, allowing the entire transmission system to use cylindrical gears instead of bevel gears. This enhances braking capability from the traditional 30% to 100%.
Compact ePowertrain
Supports rear-mounted, rear-wheel-drive configurations for trucks and short rear-overhang designs for buses, optimizing space for battery pack placement, and reduce system weight by over 20% compared to motor+driveshaft+axle setups.
Applicable Models
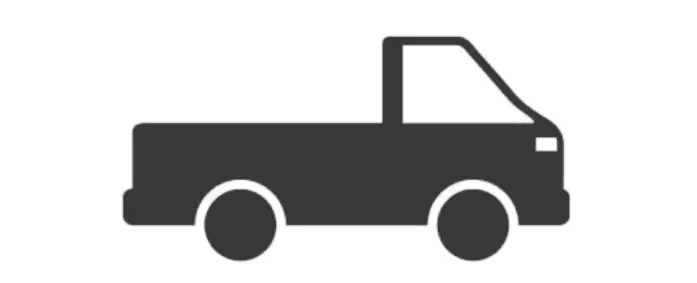
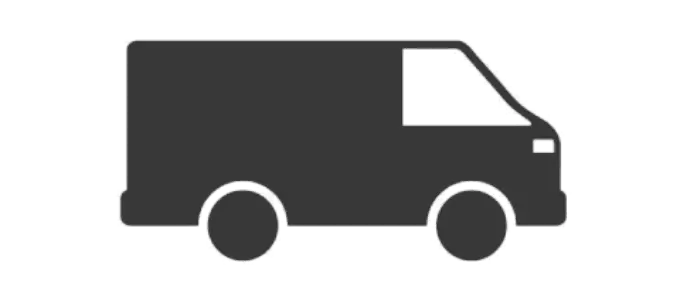
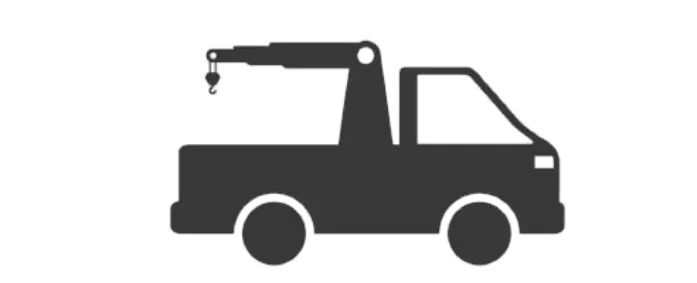
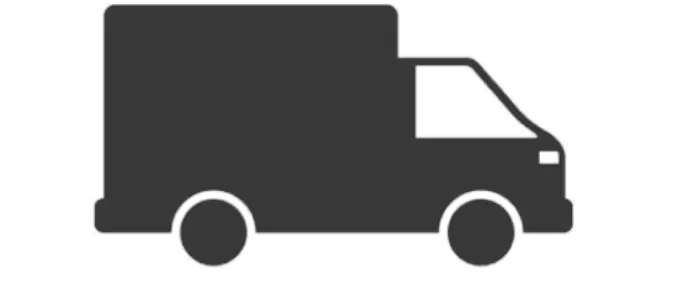
Brogen Solutions of Electric Axles for Light Trucks
For our electric axles for light trucks, the electric drive motor and reducer are mounted on the drive axle, with the motor positioned parallel to the axle housing. Utilizing cylindrical gear transmission for a high gear ratio, the integrated design removes unnecessary transmission components, resulting in a more compact structure and increased transmission efficiency.
*Parameters may differ depending on the configuration and vehicle model. Certain specifications can be customized. For more information, please contact us at contact@BrogenEVSolution.com
Model | Rated Axle Load Capacity | Maximum Torque | Gear Ratio | Motor Rated/Peak Power | Motor Rated/Peak Torque | Motor Peak Speed |
OEEP5 | 3500 kg | 5400 N.m | 15.58/16.60 | 60/115 kW | 135/325 N.m | 12000 rpm |
OEEP5-2 | 4500 kg | 5800 N.m | 16.60Â | 60/115 kW | 135/350 N.m | 12000 rpm |
OEEP5-E (front steering) | 2700 kg | 5400 N.m | 15.58 | 60/115 kW | 135/350 N.m | 12000 rpm |
OEEA50 | 5500 kg | 5775 N.m | 16.269 | 65/120 kW | 170/355 N.m | 12000 rpm |
OESTEA5300Z | 3500 kg | 5300 N.m | 16.6 | 70/130 kW | 146/314 N.m | 12000 rpm |
OEEA30 | 3500 kg | 4496 N.m | 12.665 | 80/166 kW | 170/355 N.m | 12000 rpm |
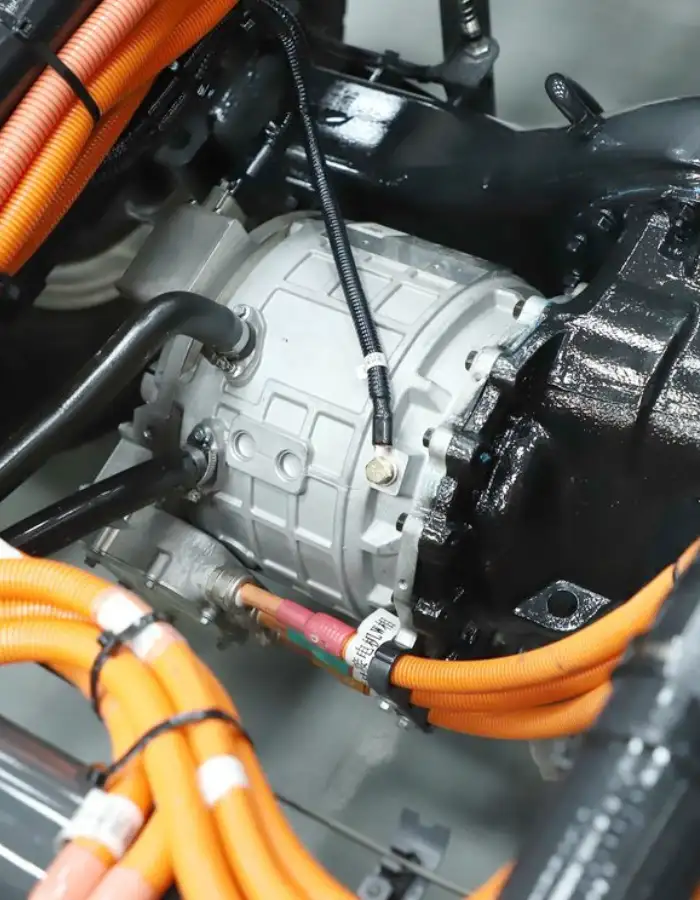
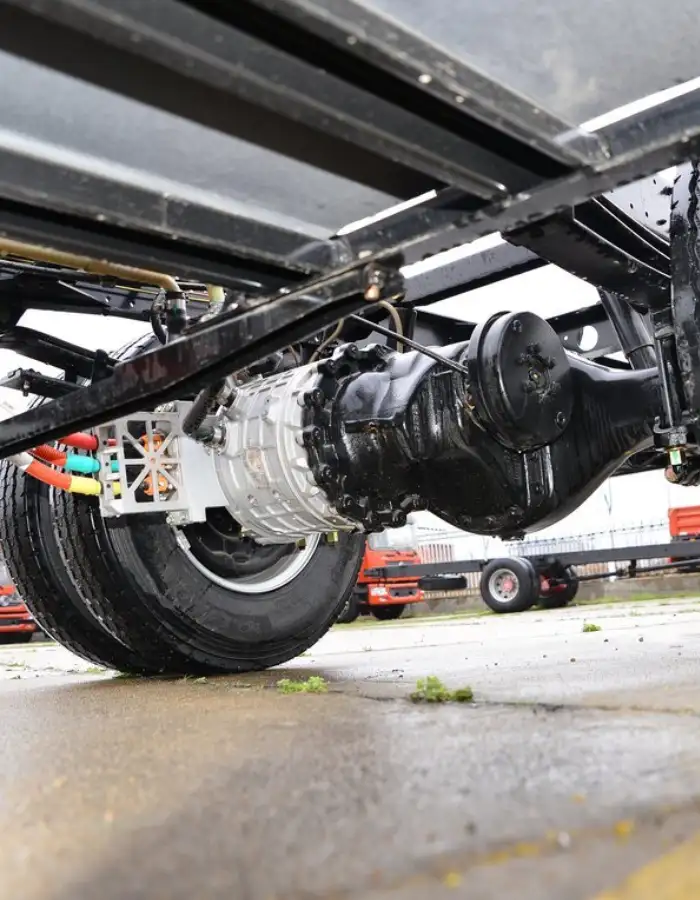
Integrated One-Piece Formed Axle Housing (Expansion-Formed)
High load-bearing capacity, lightweight design, and reduced risk of oil leakage.
Optimized Housing Design
A single-piece housing minimizes oil leakage risks, while a smooth, curved inner cavity reduces oil churning losses.
High-Precision Two-Stage Helical Gear Transmission
Features dual-surface precision grinding for improved efficiency, lower noise, and extended lifespan.
Compact Motor and Axle Integration
Minimizes offset distance between the motor and axle housing, further reducing the risk of oil leakage at the reducer interface.
Why Choose Brogen
Our product development follows a comprehensive and detailed process, including road profile data collection for specific vehicle segments, requirement analysis, and solution confirmation, theoretical validation, bench simulation testing, real vehicle testing, small-batch vehicle validation, bench simulation testing, real vehicle testing, small-batch vehicle validation, and final performance verification.
- Power and efficiency optimization
- Reliability and comfort enhancement
- Safety and protection validation
- High-speed noise reduction, sealing, lubrication, and thermal management development
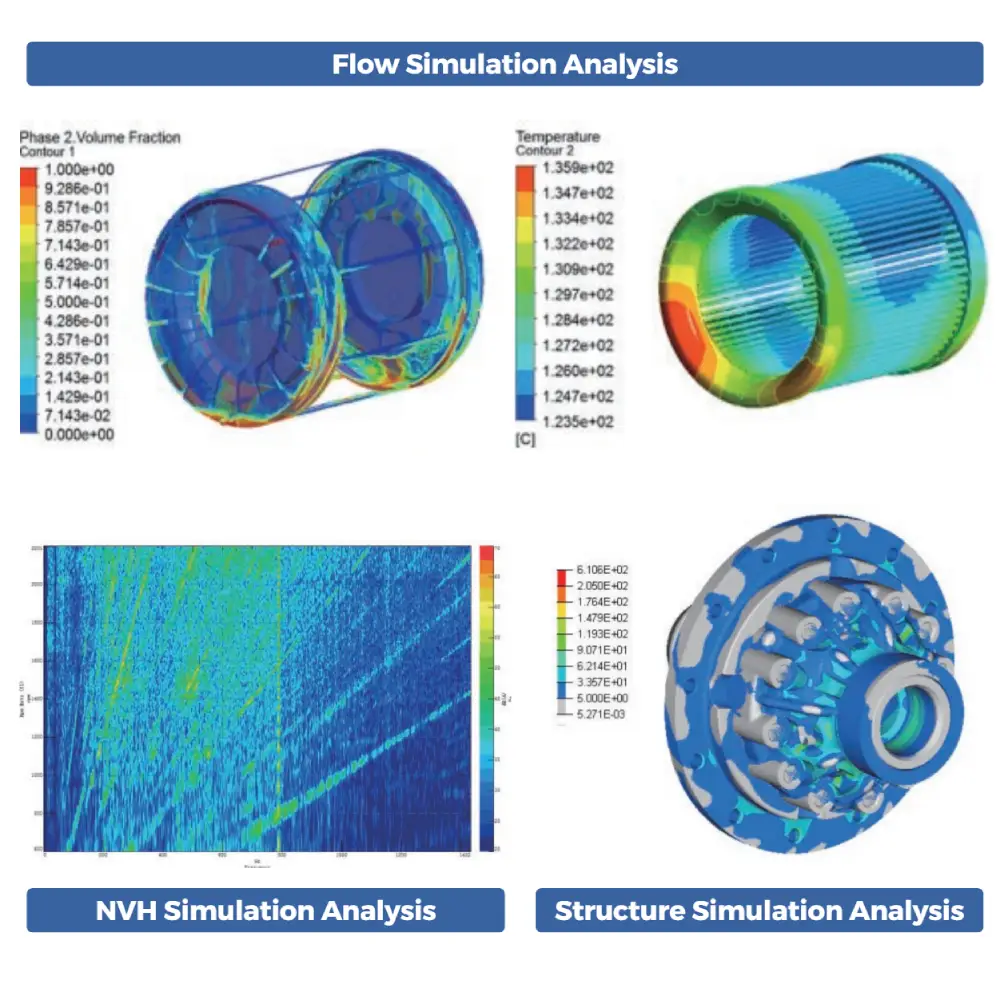
- Compact e-axle layout for better chassis integration
- Lightweight design for improved efficiency
- Precision-ground gears for low noise and comfort
- High transmission efficiency, reducing energy consumption
- 100,000 km interval oil change, maintenance-free wheel ends
- Real-time monitoring of key components for enhanced safety
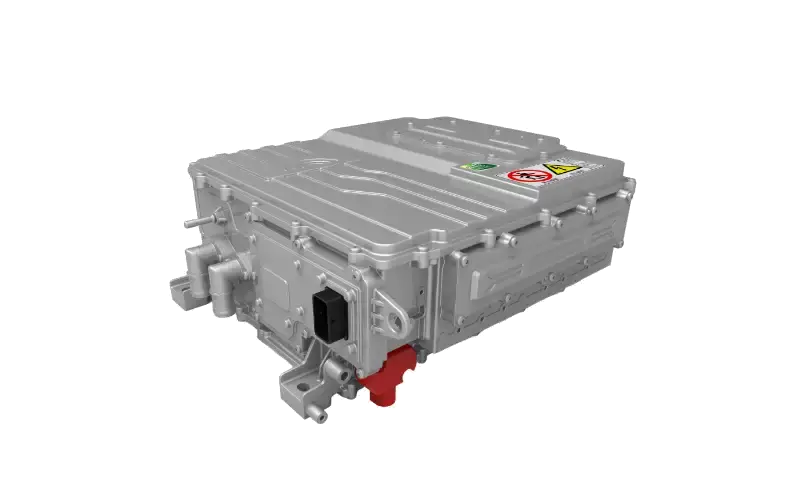
According to clients’ different requirements, we can provide standalone MCUs or high-voltage integrated controller systems, integrating MCU, PDU, DC-DC, and steering and braking DC/AC.Â
Note: Controllers are usually supplied as part of the electric powertrain system and are not sold separately.
ISO 26262 Compliance
Functional safety requirements and software/hardware development meet ASIL C standards.
Dual-Integration Design
Combines functional and physical integration to significantly reduce size, weight, and manufacturing costs.
Dual-Inverter Control Technology
Minimizes losses and achieves a maximum efficiency of 98.5%.
Modular & Scalable Architecture
Designed for flexibility and easy expansion.
Digital Simulation & Optimization
Uses digital modeling for simulation analysis, enabling more efficient and cost-effective component selection.
Advanced EMC Design
Multi-stage filtering, optimized wiring layout, enhanced shielding, and structural improvements ensure Class 5 compliance under no-load conditions.
Applications
Our electric axles for light trucks have been successfully deployed at scale in both domestic and international light commercial vehicle fleets. They are widely used in light trucks, cargo vans, pickup trucks, municipal vehicles, and more. The system is now in mass production and ready for large-scale deployment.
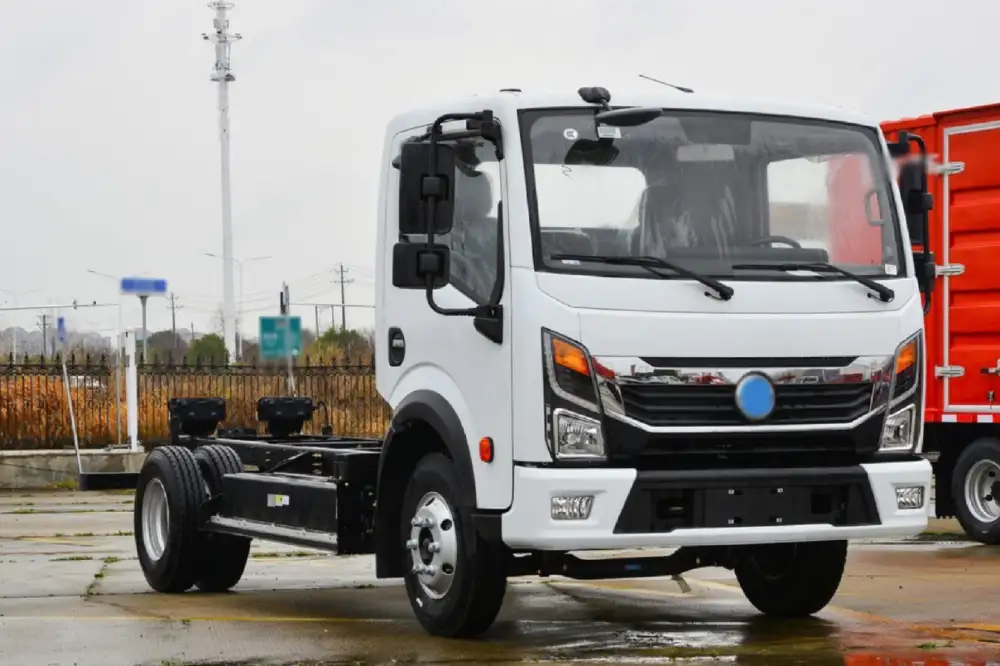
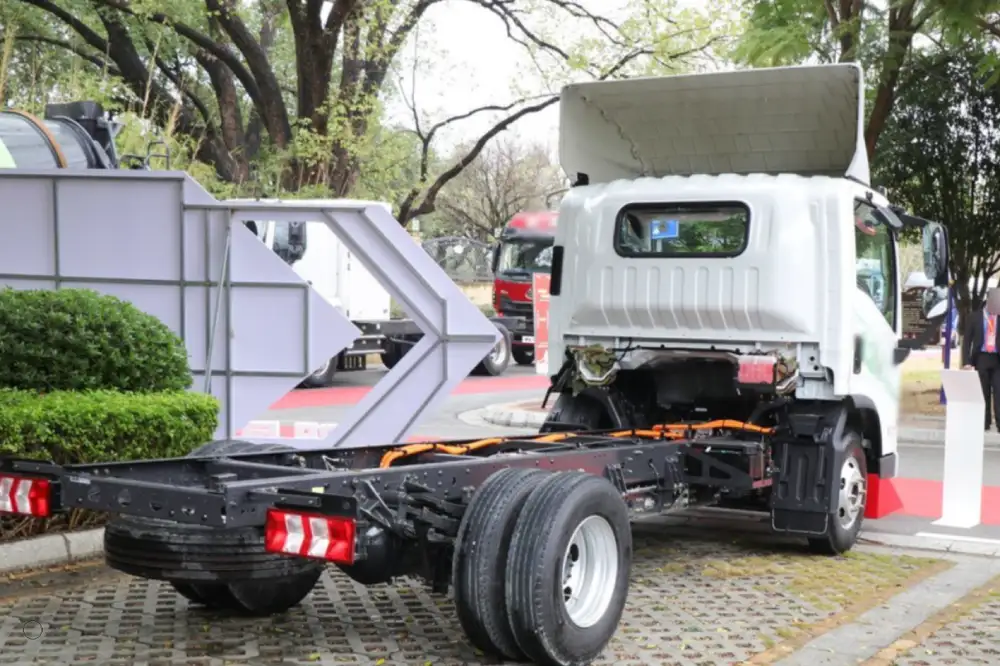
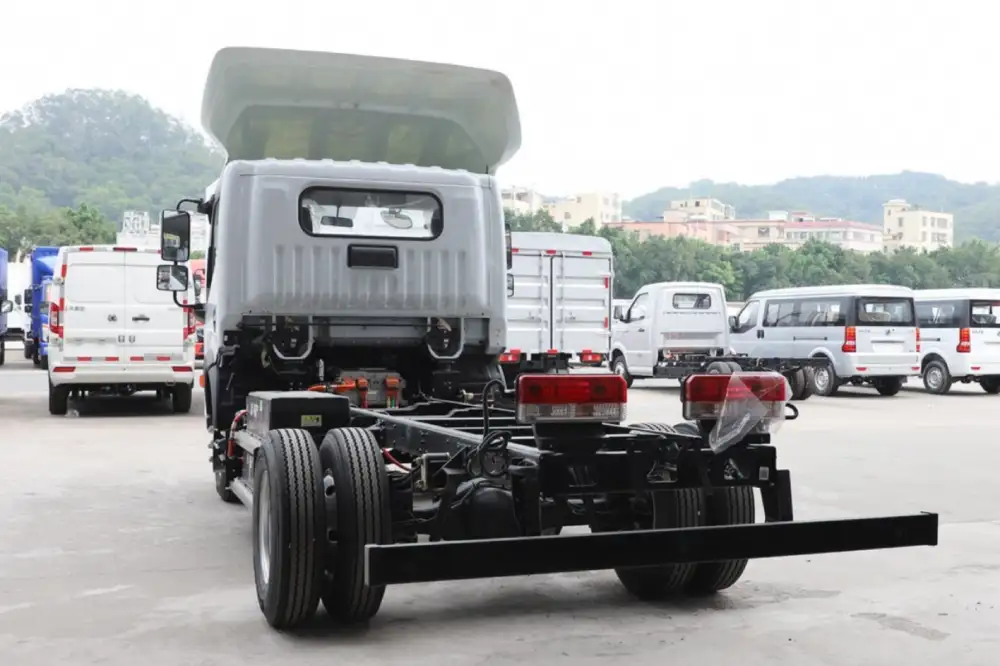
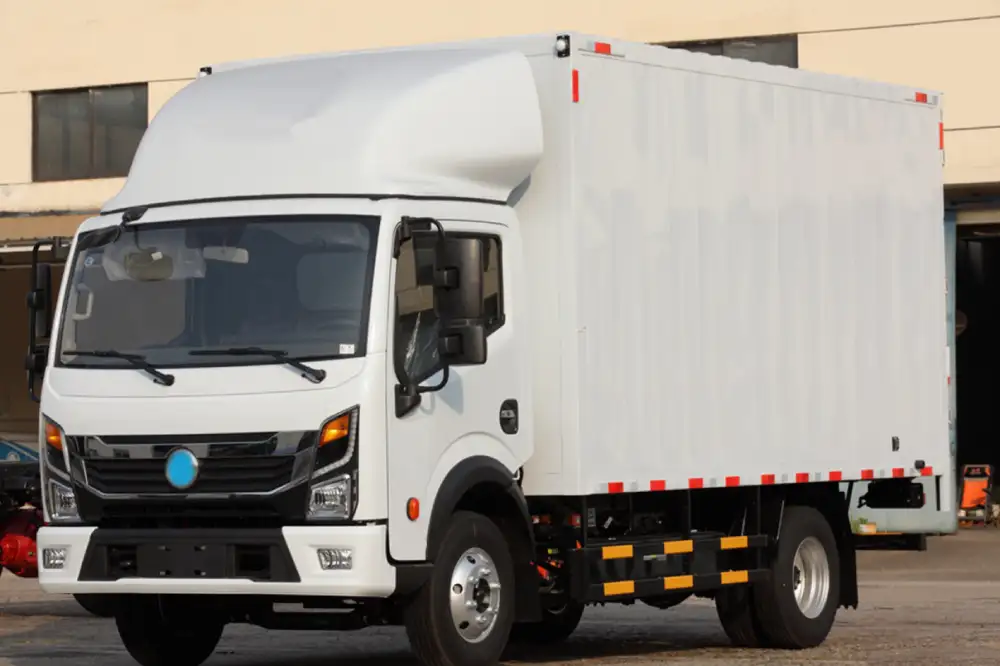
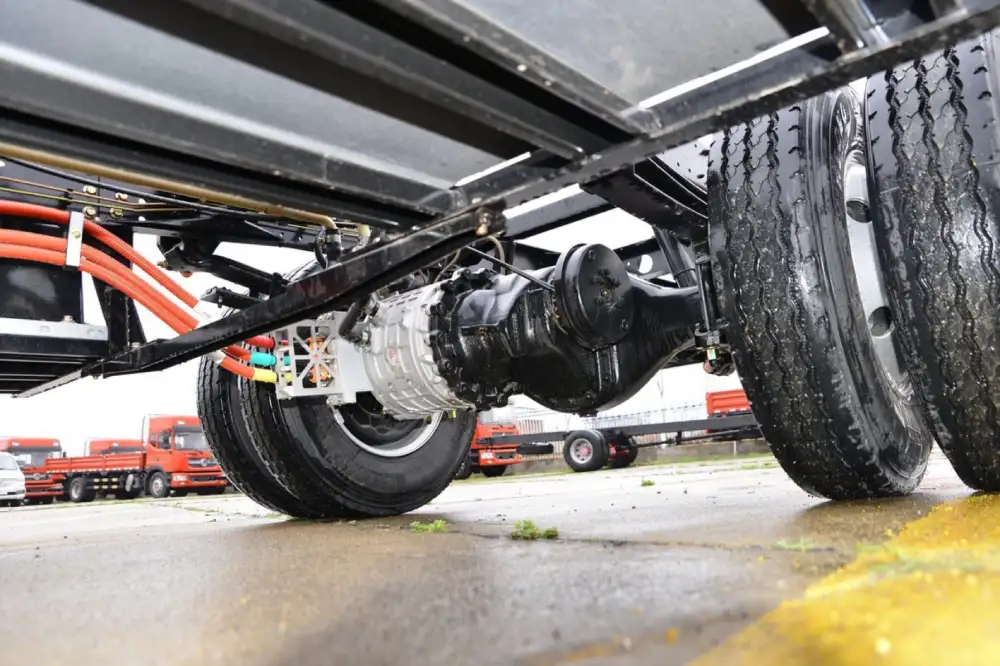
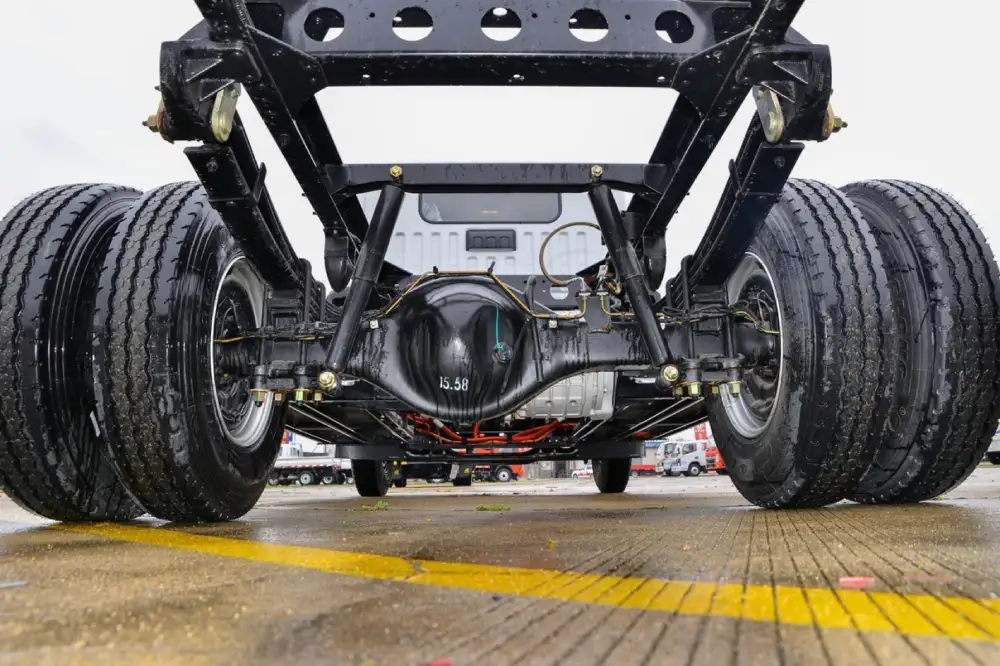
How We Work
Navigating Our Process
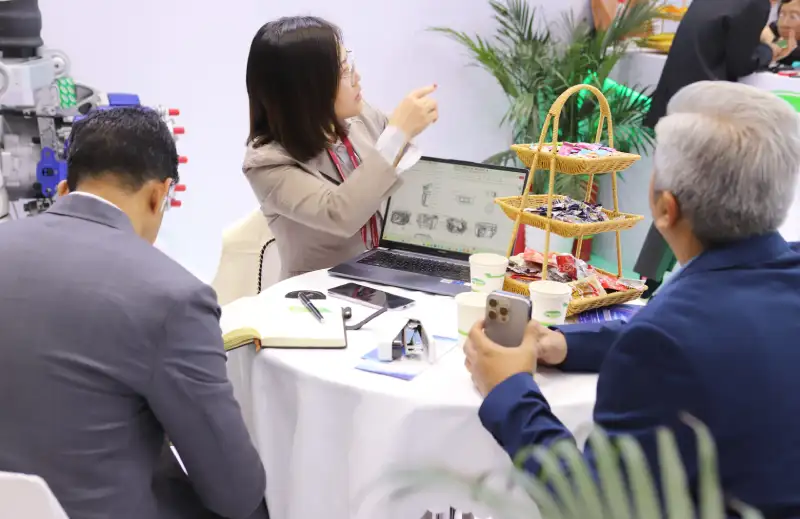
Demand Analysis & Project Evaluation
Once we receive your inquiry, our experts will connect with you within two business days to understand your specific requirements for the EV solution and conduct an initial feasibility evaluation of your project.
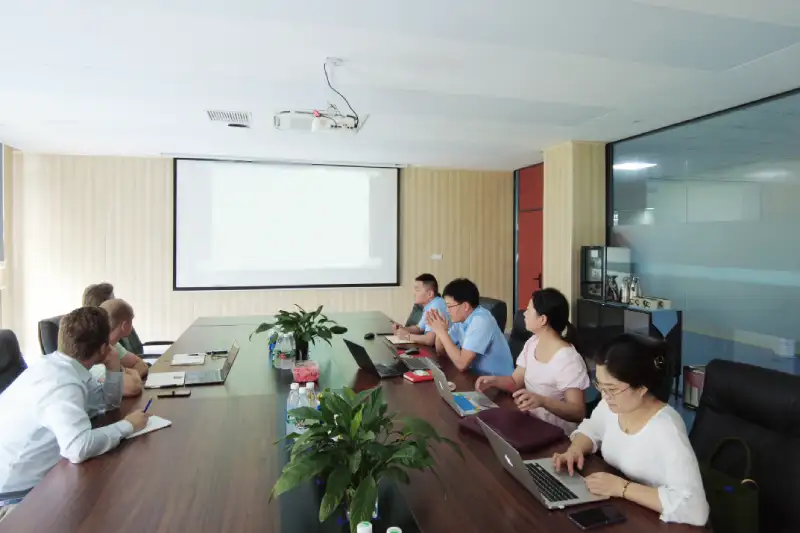
Project & Technical Coordination
If the project is deemed feasible, our engineering team will collaborate closely with your team on both hardware and software aspects to develop a viable solution. We will also provide a detailed quotation based on the technical requirements.
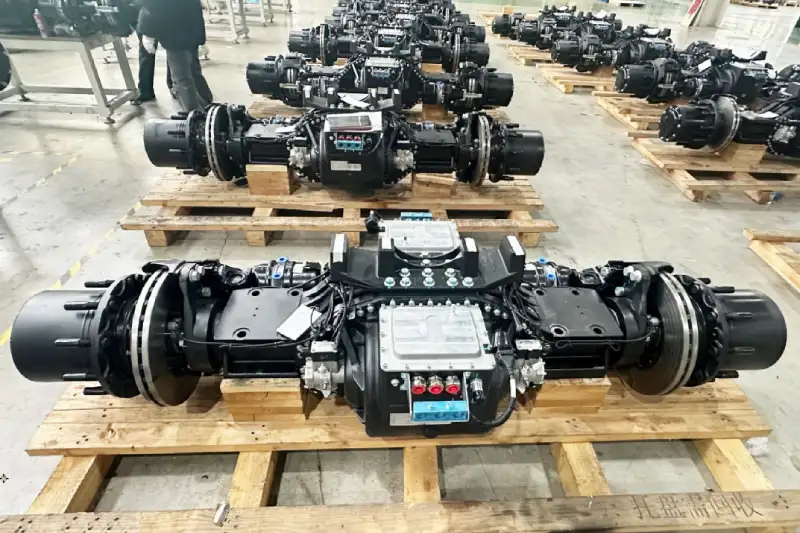
Development, Manufacturing & Testing
For customized or modified systems, we proceed with product development, including hardware and software adaptations. Our EV systems undergo rigorous testing to ensure quality, reliability, and full functionality before deployment.
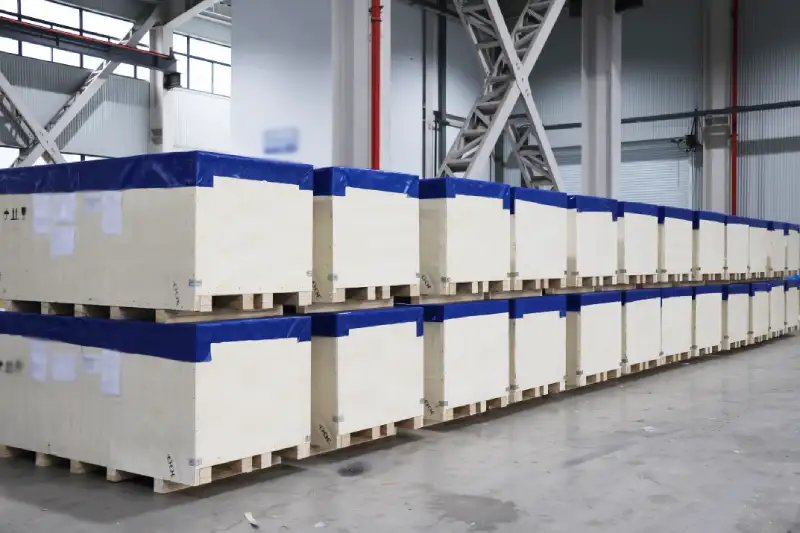
In-Time Global Shipping & Delivery
We have established strong partnerships with international shipping providers, ensuring safe and timely delivery of products to your specified location. This guarantees a smooth and efficient deployment of your EV project.
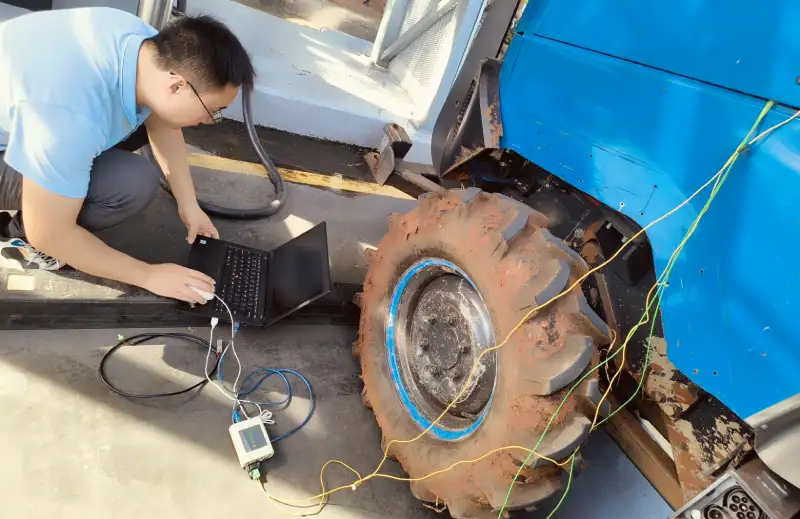
Full-Stage Remote/Onsite Technical Support
We provide technical support throughout the entire project lifecycle, including consultancy, hardware and software development, calibration, and both onsite and remote debugging, ensuring optimal performance and long-term success.
Frequently Asked Questions
Our e-axle solutions are at different stages depending on the model. Most of them are currently in mass production and have been widely deployed in both domestic and international markets. For details on a specific model or application, please contact us through the table below.
Our electric axles are suitable for light commercial vehicles such as minivans, vans, light trucks, pickup trucks, and more.
For bulk orders, we can replace components with the customer-specified brands upon request.
We follow a strict quality management system. However, for clients we haven’t yet partnered with, these documents are considered confidential and cannot be shared.
We provide standard or extended warranties depending on the product. For bulk orders, we prepare spare parts in advance to minimize downtime and ensure efficient handling of any warranty claims.
Contact Us
Get in touch with us by sending us an email, using the Whatsapp number below, or filling in the form below. We usually reply within 2 business days.
Email: contact@brogenevsolution.com
Respond within 1 business day
Whatsapp: +8619352173376
Business hours: 9 am to 6 pm, GMT+8, Mon. to Fri.
LinkedIn channel
Follow us for regular updates >
YouTube channel
Ev systems introduction & industry insights >