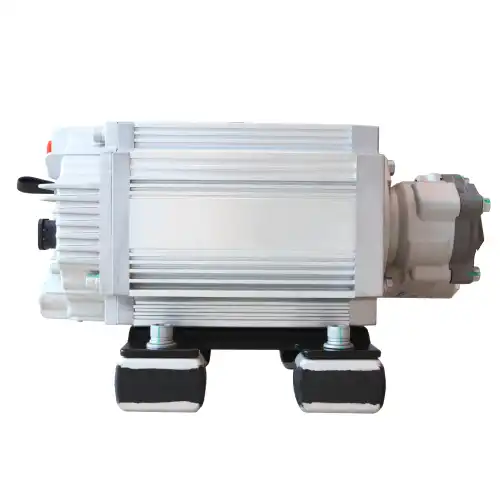
Electro-Hydraulic Power Steering System (EHPS)
The Electro-Hydraulic Power Steering (EHPS) system is an upgraded version of the traditional hydraulic power steering (HPS) system. In this system, the steering pump is no longer driven directly by the engine but by an electric motor, coupled with an electronic control unit. This allows the steering assist to be adjusted not only based on the steering angle but also in response to the vehicle’s speed, providing a more efficient and responsive steering experience.
At Brogen, we offer EHPS systems with rated power ranging from 1.5 kW to 5.5 kW and more, designed for a wide range of commercial vehicles, including buses, trucks, vans, tractors, and more.
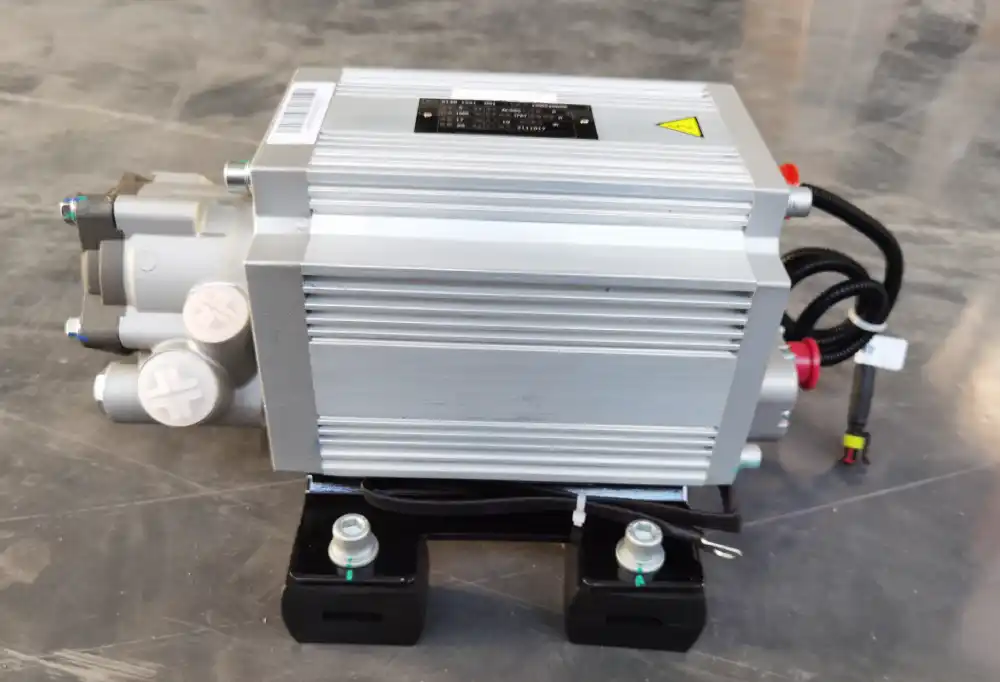
Dual-Power Source Electro-Hydraulic Power Steering System
We offer integrated dual-power source electro-hydraulic power steering solutions. The system employs a dual-system approach to provide steering assistance. During vehicle operation, if any component in the high-voltage system (such as the high-voltage steering controller, steering motor, or connected high-voltage plugs) encounters an issue, the low-voltage system can activate emergency steering. This significantly enhances the safety of the steering system.
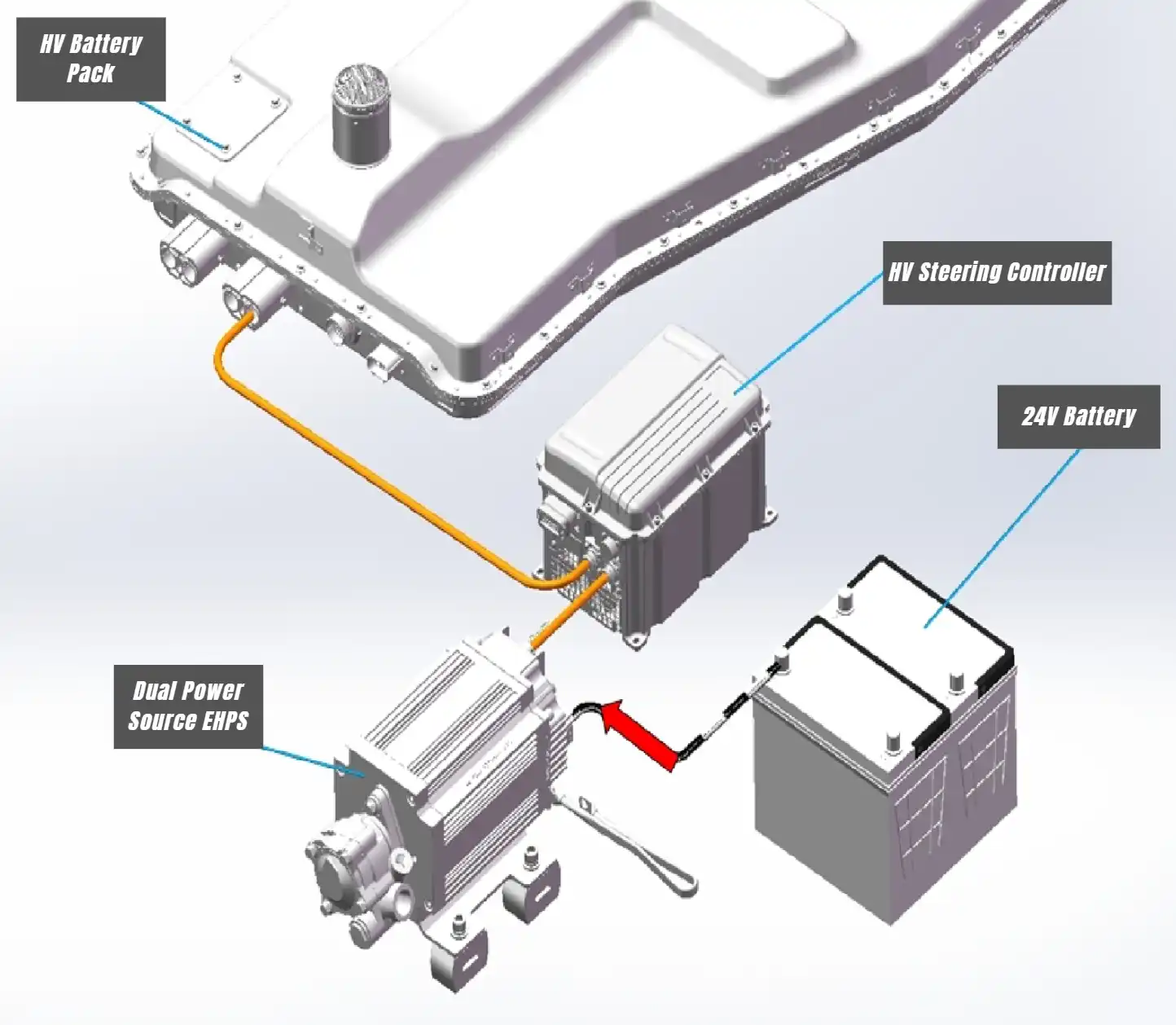
System Features
- Dual-Power Functionality: After a high-voltage power failure, the system seamlessly switches to low voltage, ensuring effective steering assistance during emergencies.
- Independent Circuits: The high-voltage and low-voltage circuits are completely independent, providing full redundancy.
- Integrated Solution: Lightweight and designed for easy installation within the vehicle chassis.
- Energy Efficiency: The low-voltage circuit intervenes only during high-voltage anomalies, ensuring safety without increasing energy consumption.
- Versatile Control: The controller supports terminal control and CAN bus control to meet customer control needs.
- Real-Time Monitoring: Communication terminals provide feedback on operational parameters for real-time monitoring of product status. It also includes protective features against under-voltage, overheating, overload, overcurrent, phase loss, and short circuits.
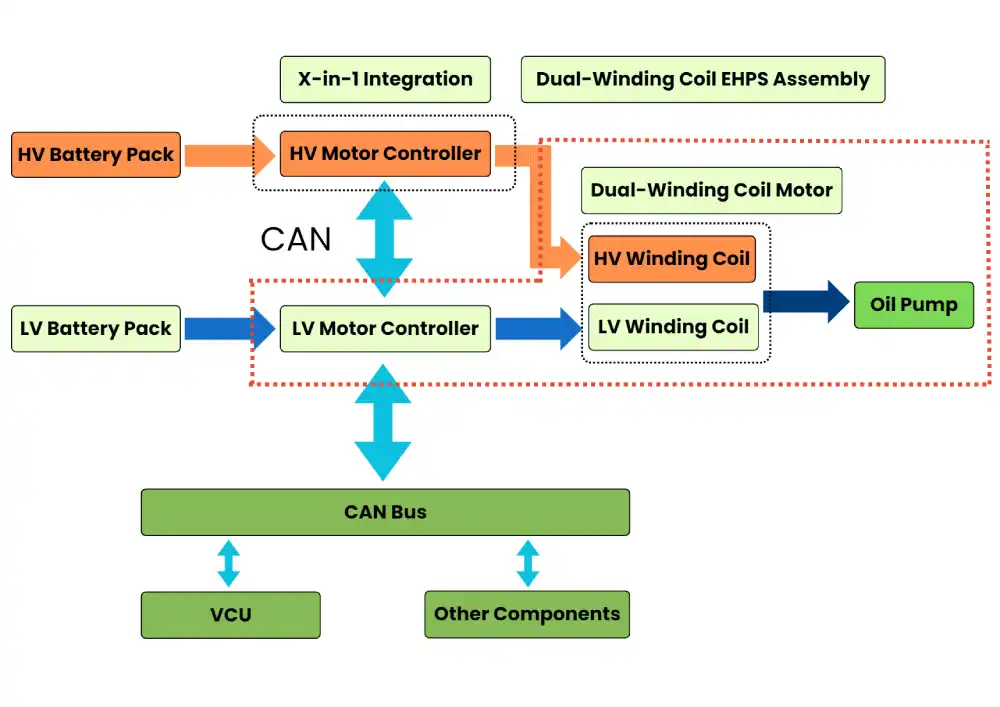
Working Principle
The dual-power source electro-hydraulic power steering assembly motor integrates both high-voltage and low-voltage winding coils, with each winding structure completely independent. The motor controller utilizes a high-voltage battery pack and a low-voltage battery pack as separate input sources, independently controlling the high-voltage and low-voltage windings of the dual-winding motor.
Under normal operating conditions, the high-voltage circuit drives the motor to provide steering, while the low-voltage controller continuously monitors the motor speed. In the event of a failure in the high-voltage power source, high-voltage motor controller, or high-voltage motor, the low-voltage motor control system immediately intervenes, ensuring uninterrupted operation of the steering system.
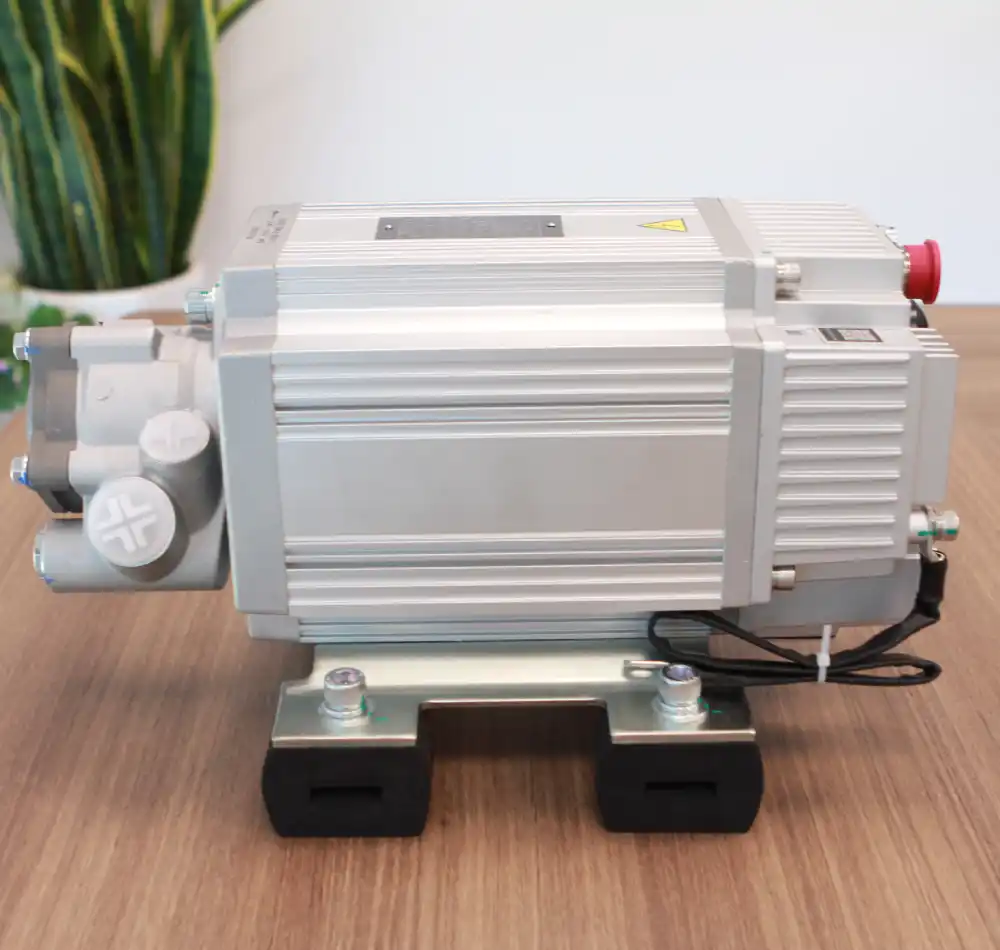
Example Configuration
- Rated power: 3 kW
- Peak power: 7.5 kW
- Rated current: 8.5 A
- Peak current: 22 A
- Rated voltage: 380 VAC
- Rated speed: 1500 rpm
- Peak speed: 1800 rpm
- Rated frequency: 100 Hz
- Controller voltage range: 400 - 700 VDC
- Peak power: 2 kW
- Rated voltage: 24 VDC
- Rated speed: 1300 rpm
- Rated frequency: 86.7 Hz
- Peak phase current: 120 A
- Theoretical displacement: 14 ml/r
- Maximum pressure: 16-17 MPa
- Oil pump efficiency: ≥80%
- Flow: 21±1.5 L/min (1500 r/min, 0.5 MPa); ≥16.8 L/min (1500 r/min, 13.6 MPa)
*More options are available upon request. Please reach out to us through the form below.
FAQ on Electro-Hydraulic Power Steering Systems
A Hydraulic Power Steering (HPS) system builds on a mechanical steering (MS) system by adding components such as a hydraulic pump and oil reservoir. In HPS, the hydraulic pump is directly connected to the engine's output. During steering, the engine provides power to drive the pump, which pressurizes hydraulic fluid. This pressurized fluid is then used to assist the steering mechanism, providing support to the driver.
In an Electro-Hydraulic Power Steering (EHPS) system, the basic principle is similar to HPS, but with one key difference: the hydraulic pump is no longer driven by the engine. Instead, it is powered by an electric motor, eliminating the problem of the steering system drawing power from the engine. Additionally, the electronic control unit (ECU) adjusts the motor speed and hydraulic fluid flow based on vehicle speed and steering angle velocity. This allows the steering assistance to be continuously adjustable, providing more assistance at low speeds (making steering easier) and less at high speeds (to prevent oversteering).
Advantages:
- It retains the precise handling and clear road feedback of HPS.
- Compared to HPS, it significantly reduces energy consumption.
- Steering assistance is more responsive, as it can be adjusted based on parameters like steering angle and vehicle speed.
Disadvantages of EHPS:
- The addition of several electronic components increases the system's overall complexity and slightly raises costs.
Our EHPS is ideal for commercial vehicles, including hybrid and battery electric trucks and buses.
Yes, our EHPS systems are used by leading global commercial vehicle manufacturers such as Foton, Geely, FFW, Chery, Golden Dragon, and more.
To get in touch, please send your project details and requirements via e-mail: contact@brogenevsolution.com or WhatsApp: +86 193 5217 3376.
Please note that our systems are designed for OEMs (automotive manufacturers), and we currently cannot accommodate individual projects.
Contact Us
Get in touch with us by sending us an email, using the Whatsapp number below, or filling in the form below. We usually reply within 2 business days.
Email: contact@brogenevsolution.com
Respond within 1 business day
Whatsapp: +8619352173376
Business hours: 9 am to 6 pm, GMT+8, Mon. to Fri.
LinkedIn channel
Follow us for regular updates >
YouTube channel
Ev systems introduction & industry insights >