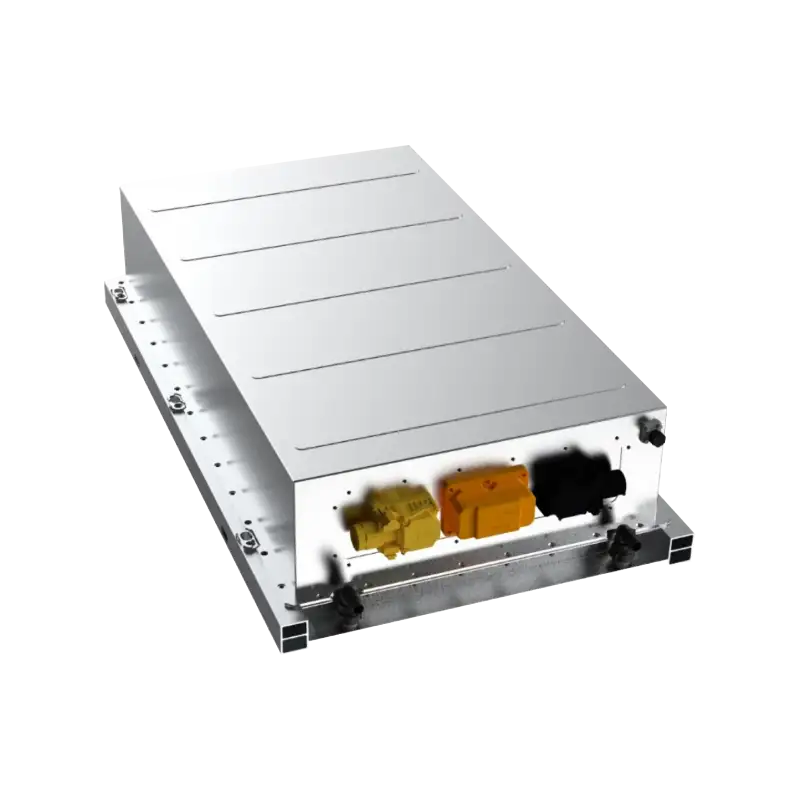
Standard EV Battery Pack for Electric Bus / HCV​
The EV battery system is the core component of a battery electric bus, and its importance cannot be overstated. Our standard EV battery pack for electric buses and HCVs is designed with modular flexibility, allowing tailored configurations to meet various vehicle requirements. This approach reduces redundant design and production efforts, enhancing efficiency across R&D, procurement, and manufacturing processes for OEMs (automotive manufacturers) and ultimately lowering costs. Additionally, the standardized battery pack design ensures high levels of protection, safety, and reliability, supporting large-scale production demands.
Whatsapp: +8619352173376
Email: contact@brogenevsolution.com
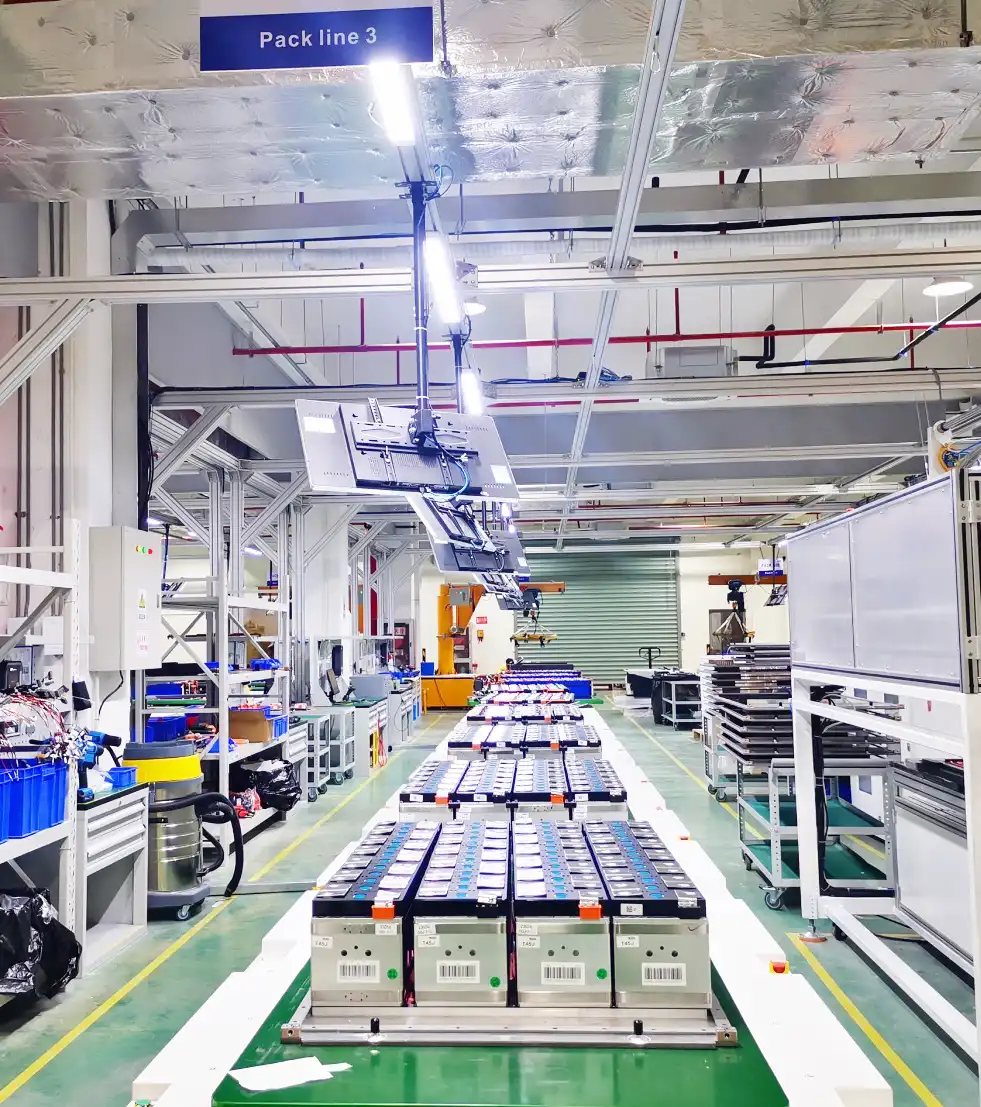
Our EV Battery System Features
Premium Battery Cell
We use battery cells from top global EV battery suppliers such as CATL, paired with a cushioning design in the battery cell and module space. This design quickly absorbs expansion due to battery "breathing" and provides added protection in collisions, enhancing overall battery safety.
Excellent Thermal Management
Our standard EV battery pack features a liquid-based thermal control system that manages heating and cooling. This system optimizes battery consistency, enabling efficient heat dissipation, high durability, and reliable long-term performance.
Lightweight Design
With aluminum alloy composites, the battery box achieves reduced material thickness without compromising structrual integrity. This approach ensures a lightweight design, further enhancing the energy density of the EV battery system.
Highly Integrated EV Battery Solution for Enhanced Quality, Efficiency, Safety
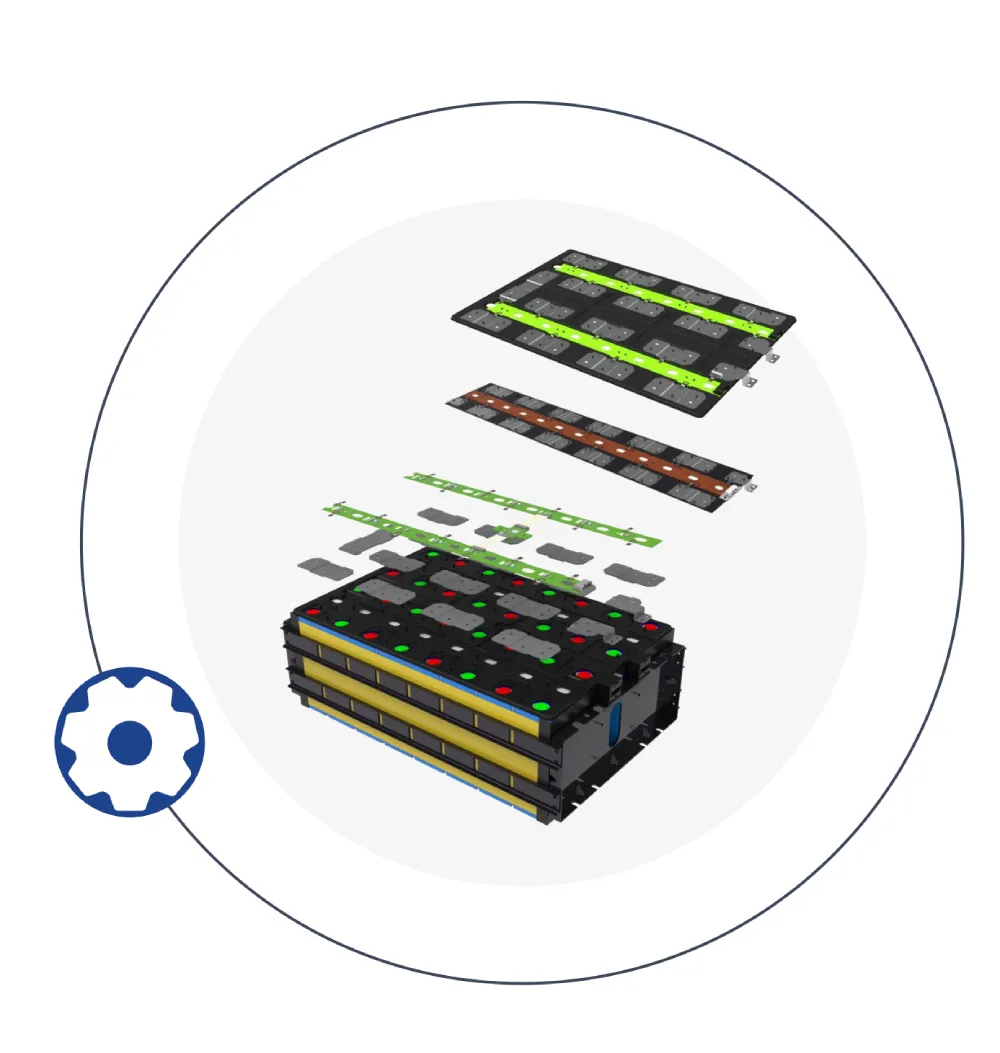
High Integration for Maximum Energy Density
- Comprehensive active safety system with integrated wiring harnesses, aluminum busbars, temperature sensors, pressure monitoring, explosion-proof valves, electrolyte detection, and BMS sensor board.
- Saves 5%-10% of battery pack space.
Enhanced Insulation & Voltage Resistance for Safety
- Meets 2000 V insulation standard between adjacent aluminum busbars and between busbars and temperature sensors.
- Meets 6000 V insulation standard between aluminum busbars and PC module.
- Significantly lowers risks associated with insulation aging, fractures, and short circuits commonly seen in traditional wiring harnesses.
Tailored EV Battery Solution
For commercial vehicles, we provide tailored EV battery solutions based on specific customer requirements. Our comprehensive solutions encompass battery packs, battery management systems (BMS), battery thermal management systems (BTMS), and cloud-based services for full lifecycle management.
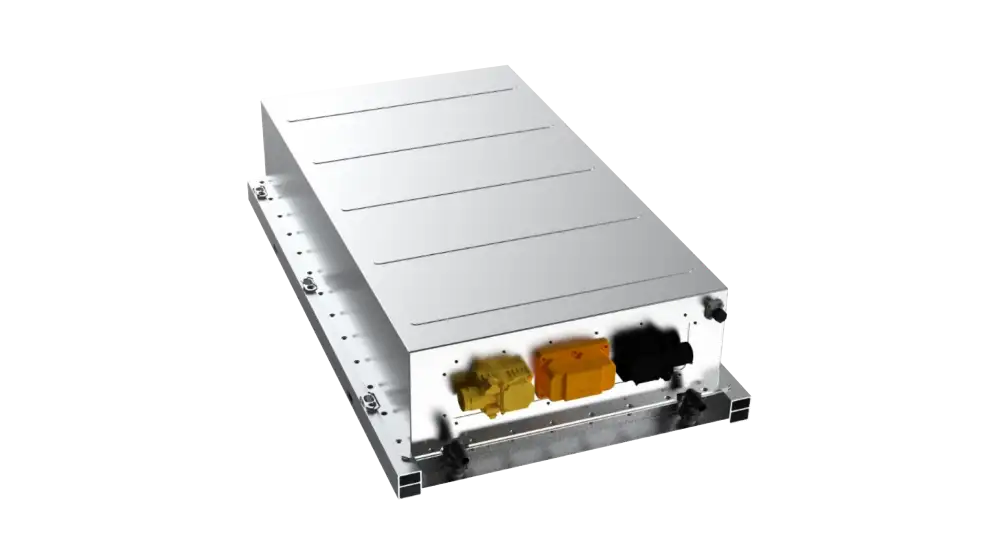
Our standardized EV battery packs are widely deployed across various applications. These packs are built using high-quality, industry-standard materials and proven manufacturing processes. With a standardized and modular design, we optimize the battery system structure layer by layer, achieving energy density levels that surpass the industry average for both battery modules and complete packs.
Solution Features
High Safety & Reliability
Built on a high-safety LFP system, with battery cells sourced from top-tier manufacturers such as CATL, EVE, and Gotion. The robust pack design meets relevant safety standards.
Wide Capacity Options
Offer multiple battery capacity configurations to meet diverse market demands, including extended range and high-load applications.
Lightweight & High Energy Density
Optimized design achieves an energy density of ≥140 Wh/kg, enhancing vehicle efficiency.
Superior Temperature Adaptability
Can be equipped with liquid cooling or heating systems based on customer requirements, ensuring reliable performance in extreme heat or cold conditions.
Strong Mechanical Protection
Features IP67-rated protection, making it highly resistant to harsh environmental conditions.
Advanced Technology
- Independently designed pack integration structure, adaptable to various battery cells and capacity requirements.
- Custom-designed electrical circuits and component selection, with in-house electrical testing capabilities to ensure compliance with industry standards.
- Highly integrated safety system, including harnesses, aluminum busbars, temperature sensors, internal pack pressure monitoring, explosion-proof valves, electrolyte leakage detection, and BMS collection boards, providing comprehensive and reliable active safety protection.
- Thermal runaway protection: equipped with insulation barriers between battery cells. If a cell reaches 900°C due to thermal runaway, the safety valve automatically releases pressure to prevent further hazards.
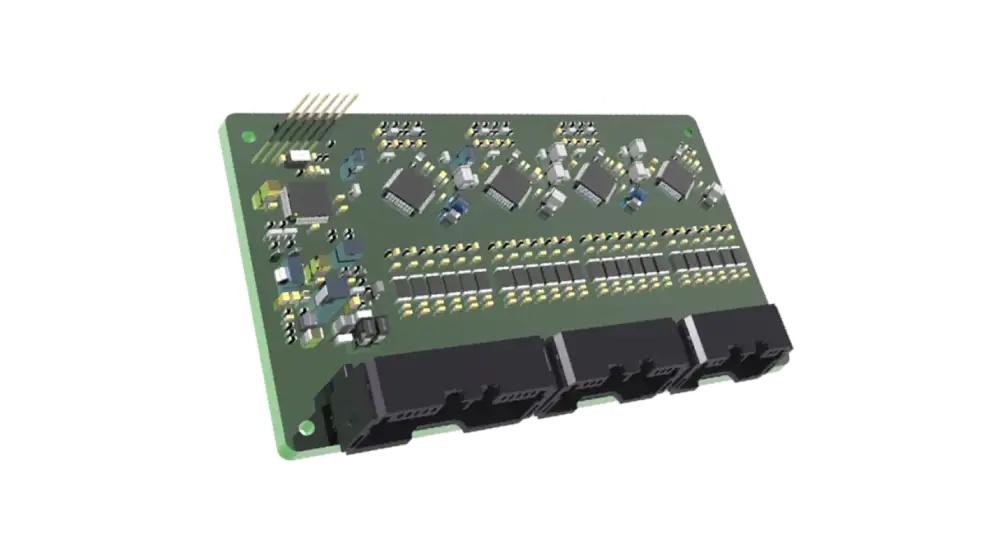
The Battery Management System (BMS) is a critical component designed to monitor and manage battery performance. Working alongside battery cells, the BMS acts as the system’s intelligent monitoring unit to ensure safety and efficient operation. Key functions of BMS include continuously tracking essential battery parameters, preventing overcharging and over-discharging, safeguarding the battery from potential damage; and optimizing performance and longevity by maintaining optimal operating conditions.
Our R&D Capabilities
- Independently develop BMS software for battery management control.
- Custom-designed control strategies and diagnostic analysis algorithms.
- Proprietary design of controller mainboards, control circuits, monitoring circuits, and communication circuits.
Advanced Technology
- High-Precision Calculations: SOC accuracy ≤3%; SOH health assessment accuracy ≤5%.
- Three-Tier Architecture: Ensures precise battery cell management, reduces error margins, and enables full lifecycle battery management.
- High-Speed Daisy-Chain Communication: Faster data transmission, lower power consumption, enhanced stability, strong anti-interference capability, and high voltage resistance.
- High Integration: BMS and PDU integration increases battery energy density, saving approximately 30% of space and reducing weight by 10%.
- Comprehensive Smart BMS Platform: Covers the entire system, from BMS controller software to an integrated edge-side BMS+EMS system and an EMS/battery management cloud platform, ensuring full-process security and control.
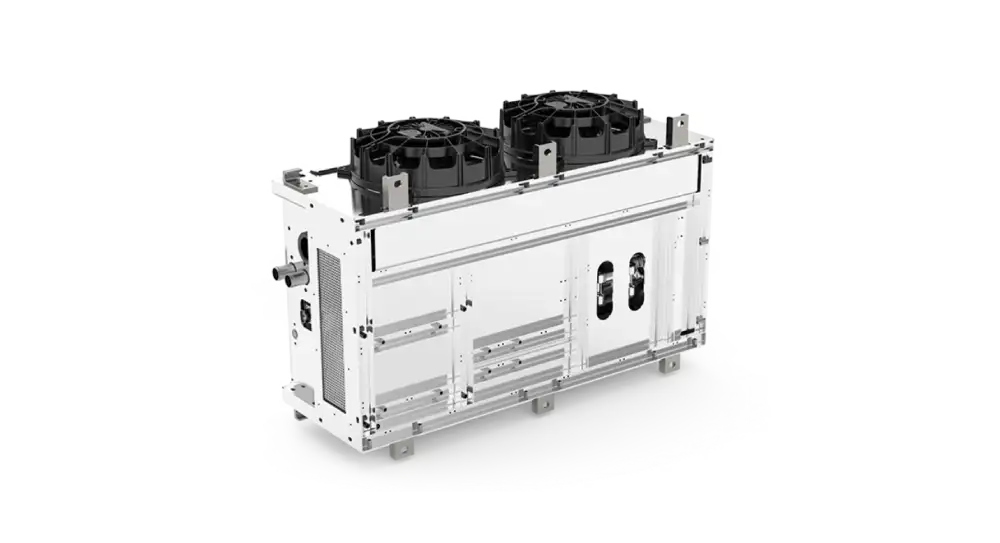
The Battery Thermal Management System (BTMS) is an integrated cooling and heating system designed to regulate the temperature of onboard batteries. The primary goal of BTMS is to keep the battery pack within an optimal temperature range, ensuring peak performance and longevity. By managing thermal energy across the vehicle, the system effectively reduces waste heat emissions, enhances energy efficiency, and minimizes environmental impact.
Solution Features
- Accurately measures and tracks battery temperature in real time.
- Effectively dissipates heat when battery temperature is high, preventing thermal runaway.
- Warms the battery in low temperatures to ensure safe and efficient charging and discharging.
- Reduces temperature differences within the battery pack, preventing localized overheating and extending overall battery lifespan.
Advanced Technology
- Aluminum alloy frame reduces weight and improves efficiency.
- Optional PTC liquid heater with standby, cooling, heating, and self-circulating modes.
- CAN bus communication for real-time fault self-diagnosis and status updates.
- Optional add-ons: tube-fin condenser, DC-DC, expansion tank.
Standard EV Battery Pack Offerings
More options are available upon request. Please contact us at contact@BrogenEVSolution.com
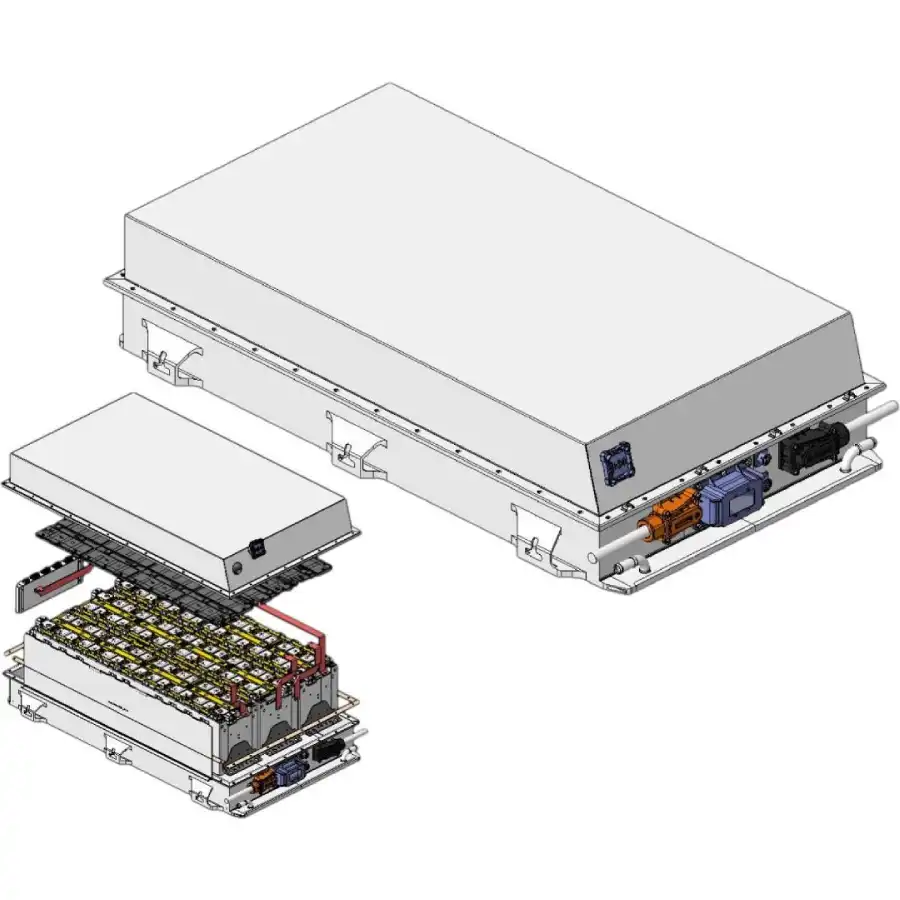
System Features
- Independent slave control: simplifies installation and maintenance.
- Integrated liquid cooling: strong adaptability in high-temperature environments.
- All-aluminum casing: lightweight design with high energy density.
- Protection level: IP67.
- Standard charging: 1C.
- Standard equipped with heating film.
EV Battery Pack Parameters
Dimension (mm) | 1060*630*240 | ||||
Cell Capacity (Ah) | 105 | 173 | 230 | 280 | 304 |
Battery Packing Scheme | 2P48S | 1P63S | 1P48S | 1P36S | 1P36S |
System Capacity (Ah) | 210 | 173 | 230 | 280 | 304 |
Nominal Voltage (V) | 153.6 | 202.86 | 153.6 | 115.2 | 115.2 |
Energy (kWh) | 32.256 | 35.095 | 35.328 | 32.256 | 35.02 |
Custom EV Battery System Example Configurations
Battery System | Parameters | Note | |
System nominal voltage | 614.4 V | The monomer is 3.2 V | |
System operating voltage range | min | 480 V | Monomeric 2.5 V~3.65 V |
max | 700.8 V | ||
System rated capacity | 460 Ah | 25 ± 2℃, 1 / 3C, 100% DOD, the shipment capacity is not less than 98% of the rated capacity | |
System storage energy | 282.62 kWh | 25 ± 2℃, 1 / 3C, 100% DOD, the shipped power is not less than 98% of the rated power | |
System life end remdual capacity | ≥368 Ah | 5 years, not less than 80% of the rated capacity | |
System group mode | 2P192S | Series and parallel connection | |
Battery system weight | About  1920 kg | ||
Specific energy of the system | About 150 Wh/kg | ||
Maximum continuous charging current | 230 A | Maximum duration of 0.5C | |
Maximum pulse charging current (30s) | 460 A | 30s max. 1C | |
Maximum continuous discharge current | 460 A | Maximum duration of 1C | |
Maximum pulse discharge current (30s) | 920 A | 30s maximum of 2C | |
Maximum allowable feedback charging current (10s) | 920 A | 50% SOC, 20 – 55℃ / 10s max 2C | |
SOC working range | 10~100 % | ||
Insulation requirements | ≥200 MΩ | 500 VDC, total positive / negative against the shell | |
Protection level of the battery box body | IP67 | ||
System cooling mode | water cooling system | ||
System heating mode | water cooling system | ||
Charge on shipment (SOC) | 20%~50% | The SOC status is consistent with the same batch of shipment |
Battery System | Parameters | |
System nominal voltage (V) | 576 V | |
System operating voltage range | min | 450 V |
max | 657 V | |
System rated capacity | 608 Ah | |
System storage capacity | 350.21 kWh | |
System end of life remaining Capacity | ≥ 212 Ah | |
System grouping | 1P180S | |
Shipment Charge Capacity (SOC) | 20%~50% | |
System specific energy | about 145 Wh/kg | |
Maximum continuous charging current | 304 A | |
Maximum pulse charging current (≤30s) | 608 A | |
Maximum continuous discharge current | 608 A | |
Maximum pulse discharge current (≤ 30s) | 1200 A | |
Maximum allowable feedback charging current (≤10s) | 608 A | |
SOC working range | 10~100% | |
Insulation requirements | ≥ 200 MΩ | |
Protection level of battery box | IP67 | |
System cooling method | Natural cooling | |
System heating method | Heating film |
Why Choose Us
Exceptional R&D Expertise
Our Battery Engineering Research Institute boasts a team of over 80 R&D professionals, with more than 30% holding master’s or doctoral degrees. Equipped with state-of-the-art infrastructure, advanced testing equipment, highly skilled technical personnel, and a stringent quality management system, we ensure excellence at every stage of development.
Battery Research Institute | Product Research Institute | Materials Research Institute | R&D Laboratory | Technology Management |
|
|
|
|
|
BMS Design & Development
Independently develop BMS software; design control strategies and diagnostic analysis algorithms in-house; design the controller main board, control circuits, monitoring circuits, and communication circuits
Pack Structural & Electricial Design & Development
Independently design integrated battery pack structures to accommodate various battery cell types and capacity needs; independently design electrical circuits and select components, with electrical testing and verification environments to ensure compliance with standards
Battery System Integration Design & Development
Independently design electrical systems and structures; capable of integrating third-party systems, equipment, and components
Strong Manufacturing Capabilities
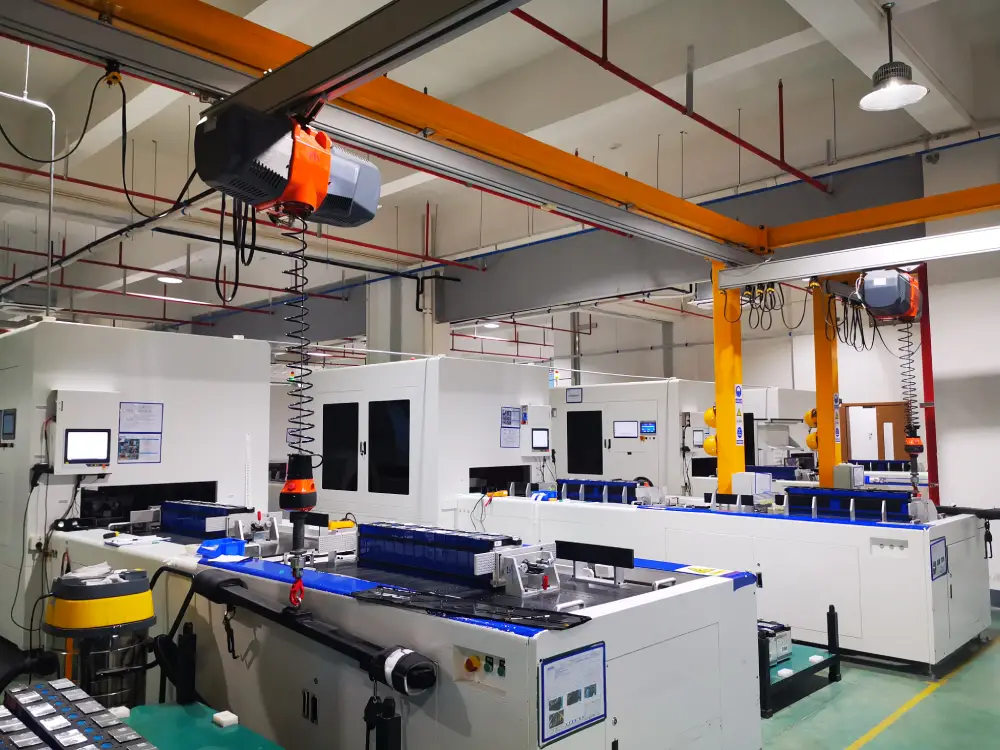
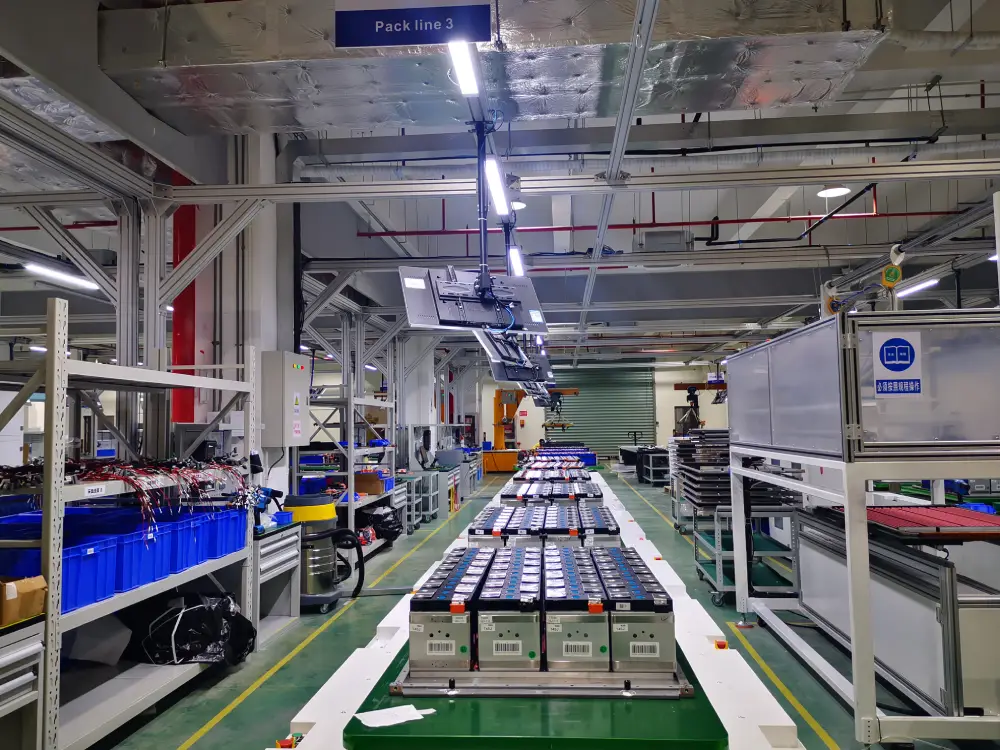

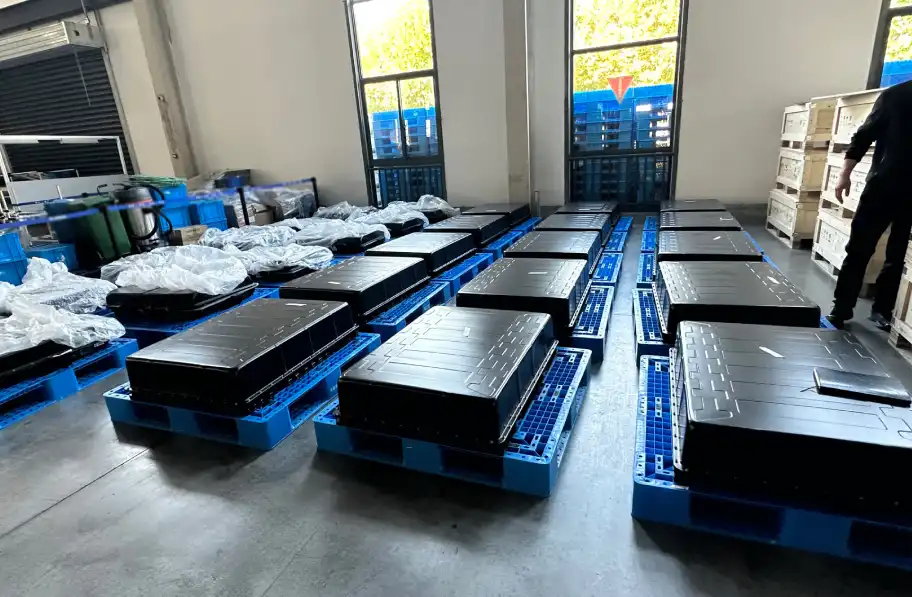
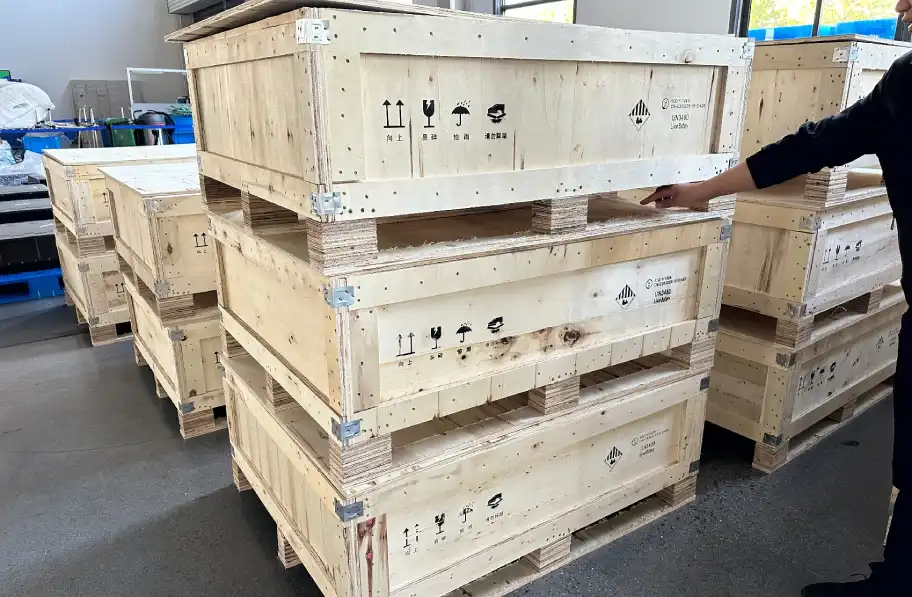
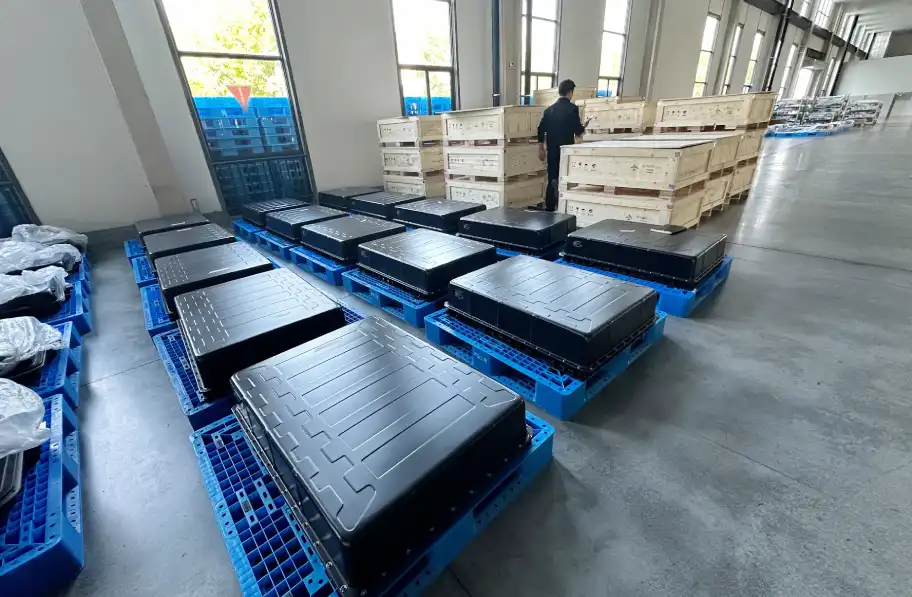
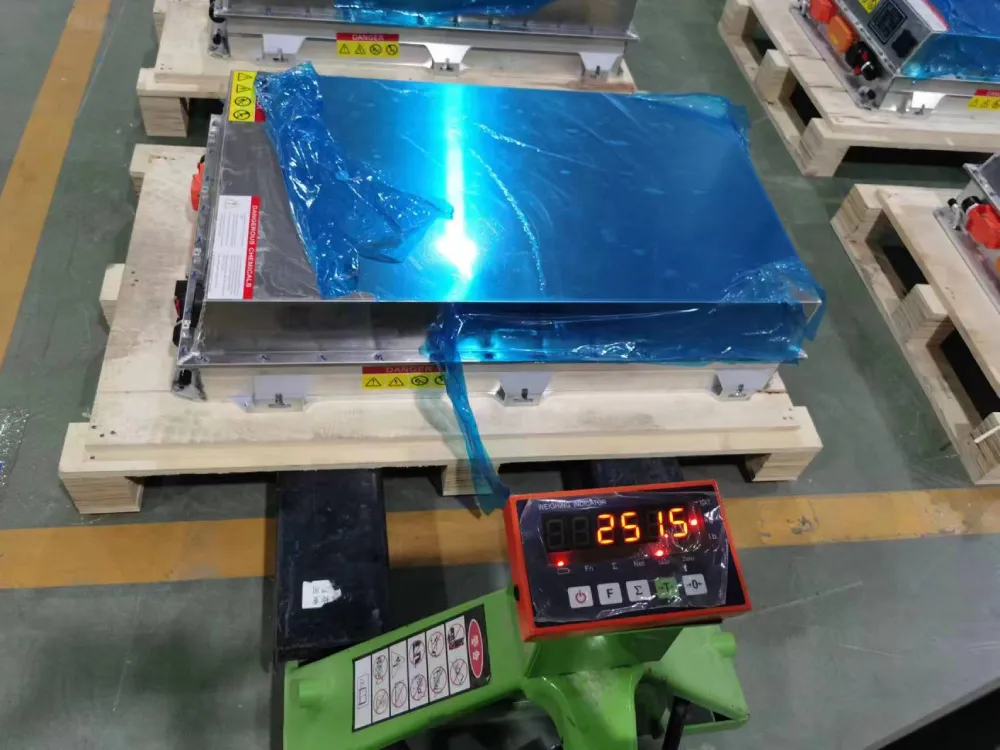
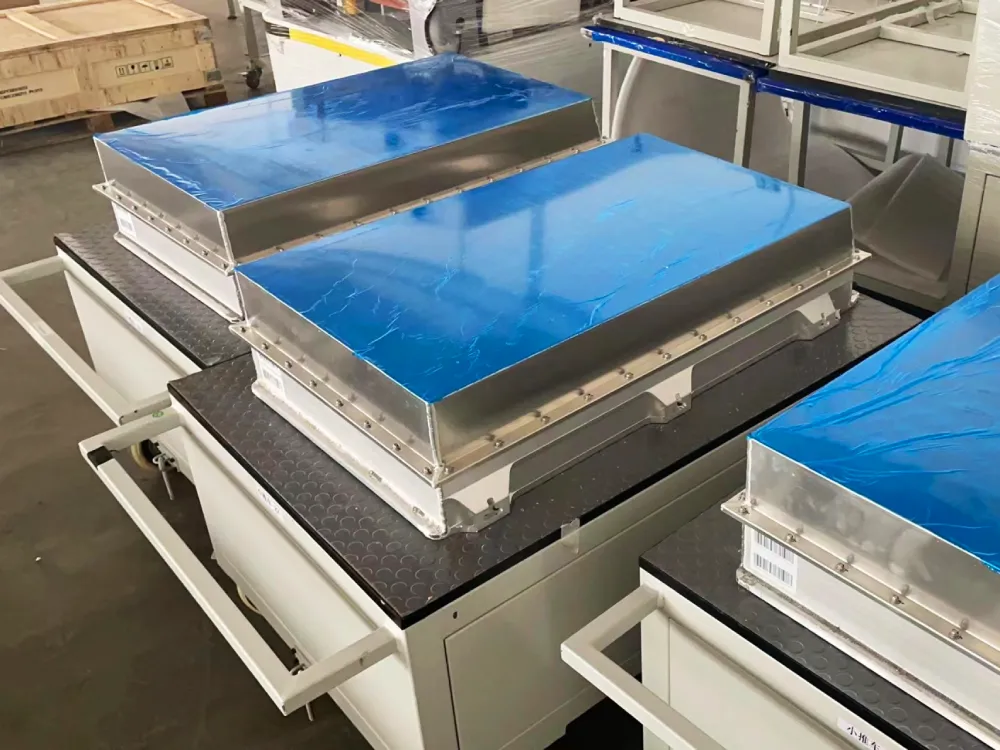
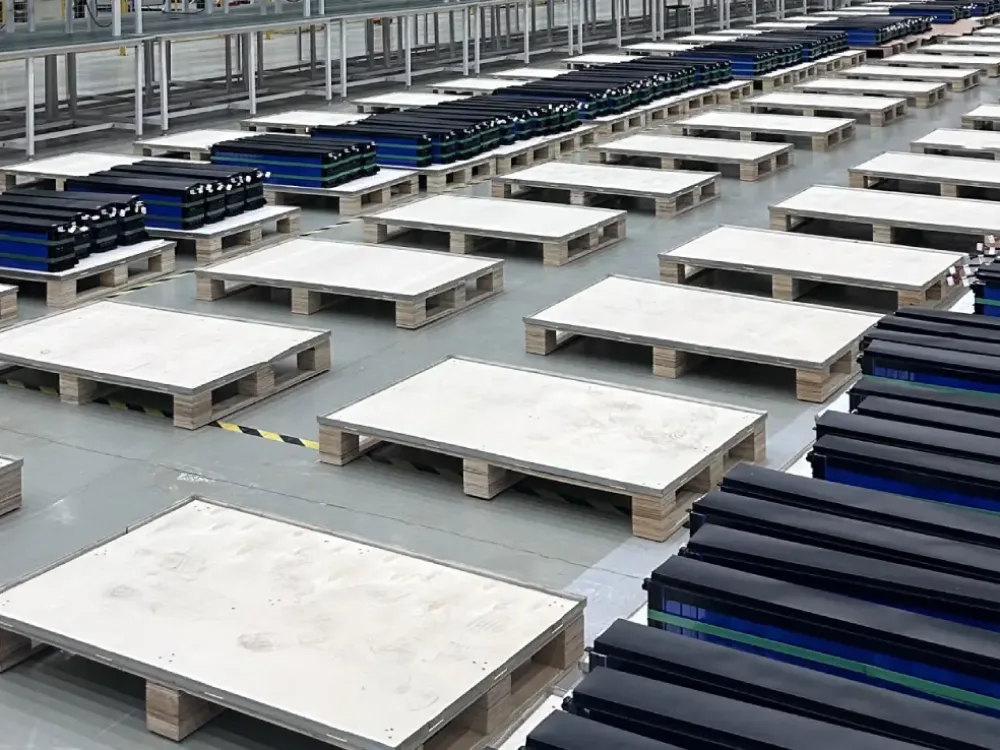
Case Study

8-Meter and 12-Meter Electric Bus Project in Turkey
In 2022, a leading commercial vehicle manufacturer in Turkey approached us for a custom EV solution for their 8-meter and 12-meter electric bus project. Drawing on our expertise in EV battery systems, we delivered a tailored solution that included a 282 kWh battery system, a custom Battery Management System (BMS) with a Power Distribution Unit (PDU), and Battery Thermal Management System (BTMS).
This battery system was adapted from our standard EV battery packs, but the buses’ 700 V high-voltage motors posed a unique challenge, as this voltage is uncommon in battery packs. To address this, our engineering team conducted detailed simulations and calculations based on the vehicle specifications and developed custom battery packs with varied capacities to meet the specific requirements of each bus model.
Key Partners
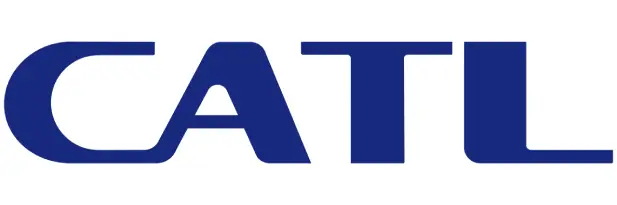
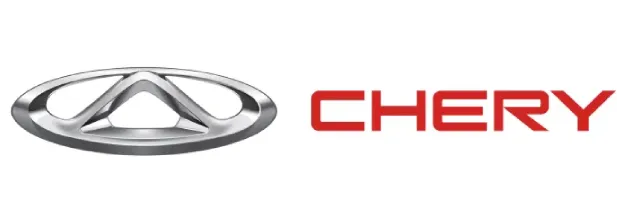
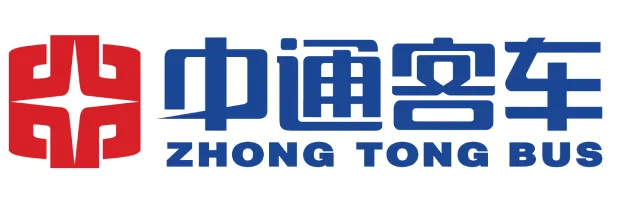
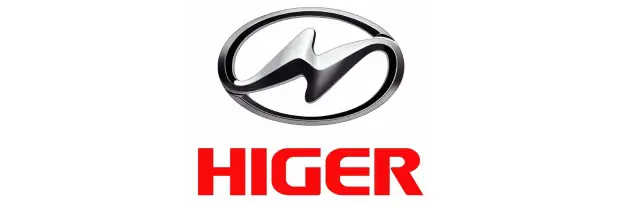
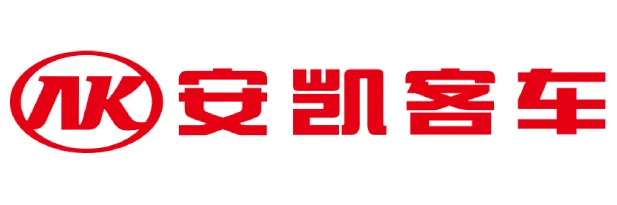
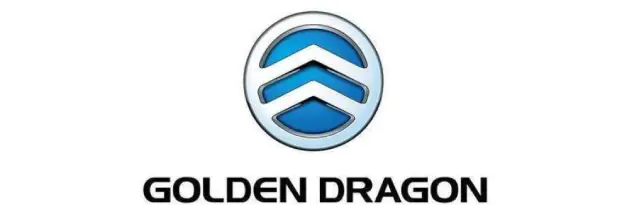
Contact Us
Get in touch with us by sending us an email, using the Whatsapp number below, or filling in the form below. We usually reply within 2 business days.
Email: contact@brogenevsolution.com
Respond within 1 business day
Whatsapp: +8619352173376
Business hours: 9 am to 6 pm, GMT+8, Mon. to Fri.
LinkedIn channel
Follow us for regular updates >
YouTube channel
Ev systems introduction & industry insights >