Everything You Need to Know About The On Board Charger for Electric Vehicles
What is an on-board charger?

An On Board Charger (OBC) is a device that converts AC power into DC power. It transforms the AC voltage from charging stations into the DC voltage required by the battery. OBCs are installed in electric vehicles (EVs) and plug-in hybrid electric vehicles (PHEVs). They enable these vehicles to be charged using AC power from residential or public charging stations. The output power of an OBC typically ranges from 3.3 kW to 22 kW. A significant advantage of OBCs is their ability to charge electric vehicles using standard household outlets.
What are the different methods of charging an electric vehicle?
Electric vehicle charging stations can be broadly categorized into two types: AC charging stations and DC charging stations.
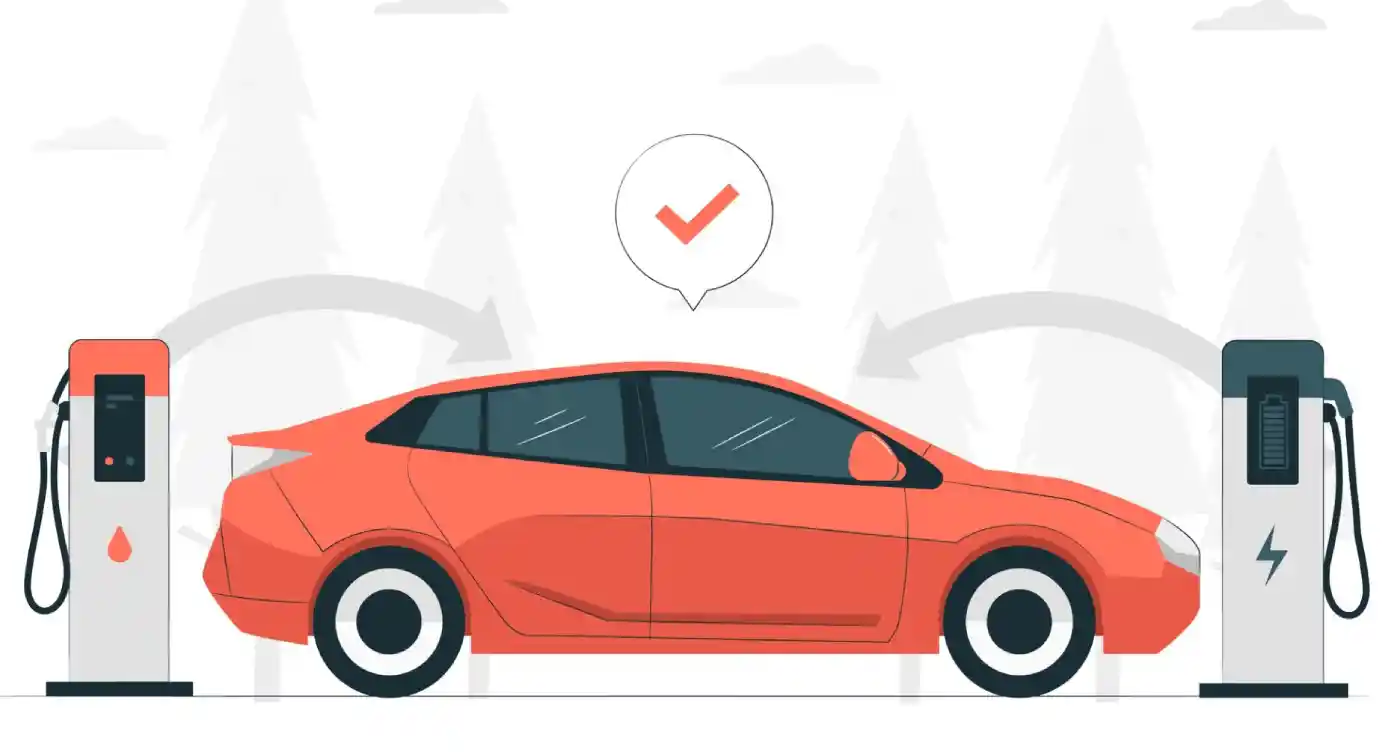
AC Charging Stations
As the name suggests, AC charging stations provide alternating current (AC) from the electrical grid to electric vehicles. The onboard charger then converts the AC to direct current (DC) to charge the vehicle’s battery. These stations, also known as Level 1 and Level 2 chargers, are used in residential and commercial applications. The advantage of AC charging stations is that the OBC can adjust the voltage and current according to the vehicle’s needs. This eliminates the need for the charging station to communicate with the electric vehicle. However, the disadvantage is their low output power. It results in longer charging times. AC power from the grid is delivered directly to the OBC via an Electric Vehicle Supply Equipment (EVSE), which then converts it to DC and charges the battery via the Battery Management System (BMS).

DC Charging Stations
DC chargers take AC power from the grid and convert it to DC, bypassing the OBC to charge the battery pack directly. These chargers typically deliver high voltages up to 600V and currents up to 400A. Unlike AC chargers, which take 8-16 hours to charge a vehicle, DC charging stations can fully charge an electric vehicle in approximately 30 minutes. These stations are also known as Level 3 chargers, with the chargers referred to as DC Fast Chargers (DCFC) or Superchargers. The main advantage of DC chargers is their fast charging time. However, they are technically complex and need to communicate with the electric vehicle to charge it efficiently and safely. As shown in the typical DC charging system diagram, the EVSE bypasses the OBC and delivers DC power directly to the battery pack.
The standard capacity of a DC charging station ranges from 50 kW to 300 kW. It’s more than 6 times the capacity of a single-phase on-board charger. However, AC charging through the OBC has less impact on the battery and minimizes battery aging.
What are the functions of the onboard charger?
- The primary function of the OBC is to manage the charging process from the power grid to the vehicle’s battery. The OBC is designed to charge the battery as quickly as possible while minimizing battery degradation. It offers two charging methods: constant current charging and constant voltage charging.
- Constant current charging: this method charges the battery faster, but cannot fully charge the vehicle.
- Constant voltage charging: also known as trickle charging, this method charges the battery more slowly but with greater control, allowing the vehicle to reach a full charge.
To optimize charging speed, the OBC uses constant current charging at the beginning of the charge cycle and switches to constant voltage charging toward the end.
- The OBC also plays a critical role in the bi-directional charging mode available in some vehicles. This capability allows it to convert DC power from the high-voltage battery pack back to AC power, supporting AC loads (Vehicle to Load, V2L), grid power (Vehicle to Grid, V2G), and even home power (Vehicle to Home, V2H).

Hardware architecture of the OBC
The OBC primarily consists of the following hardware components:
- Input Voltage Measurement Circuit: Measures the input voltage to control the conversion circuit.
- Input Filter: Suppresses internal noise or noise from external devices.
- Full-Wave Rectification Circuit: Converts AC voltage to DC voltage.
- Power Factor Correction (PFC) Circuit: Improves power efficiency degraded by waveform phase shifts.
- Voltage Conversion Circuit: Converts voltage using components such as an isolation transformer and field-effect transistor (FET) switches.
- Output Filter: Suppresses noise generated internally.
- Output Voltage Measurement Circuit: Measures the output voltage to control the conversion circuit.
- Control Circuit: Manages the conversion circuit and other components.
- DC/DC Converter: Provides power to the control circuit.
- Communication Interface: Facilitates communication with external devices.

What are the trends and challenges in OBC development?
The OBC is a critical component for both battery electric vehicles (BEVs) and plug-in hybrid electric vehicles (PHEVs). As the number of electric vehicles increases, the number of vehicles equipped with OBCs will also increase. At the same time, more electric vehicles will be equipped with DC fast charging capabilities.
Key trends and challenges in OBC development include:
- Adaptation to 800V High-Voltage Platforms: OBCs will be compatible with these high-voltage systems.
- Increased Output Power: As 800V platforms become more common and battery capacities grow, OBCs will need to provide higher output power. Future OBCs will need to feature high voltage (high withstand voltage), high current, low loss, high heat resistance, and compact size.
- Bidirectional Charging Capability: OBCs will need to support bidirectional charging, allowing the conversion of DC power from high-voltage battery packs into AC power to support external AC loads.
- Use of Discrete High-Voltage Components: These components will be widely used in OBCs to enhance performance.
- Increased Power Requirements: The trend towards fast charging will significantly increase the power requirements of OBC topologies.
Our On Board Charger Systems
Engineered for top-tier power conversion efficiency and remarkable power density, our chargers cover a broad power spectrum, ranging from 3.3 kW to 40 kW. Whether you’re driving a passenger car, bus, van, or LCV, or require upfit power supply for specialized vehicles, our comprehensive solutions ensure seamless integration and optimal performance.Â
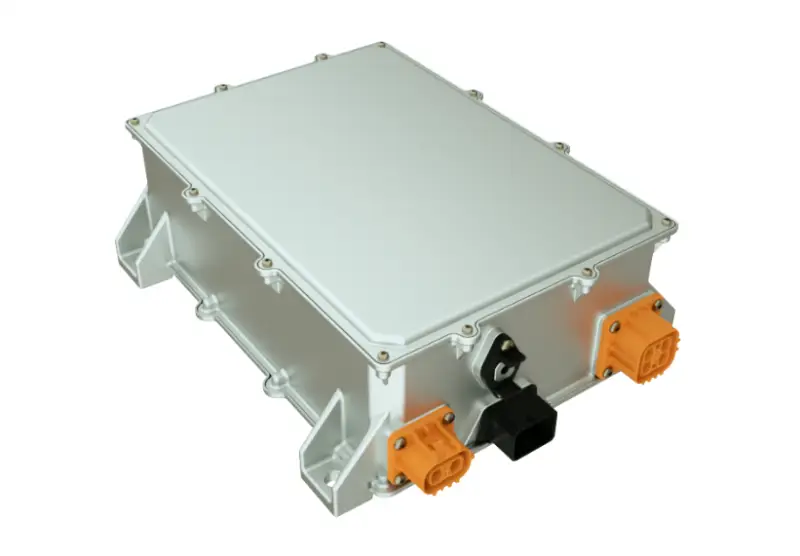
- Applicable for both PHEV and BEV
- Wide input range, 1 phase and 3 phase
- Bidirectional options available (V2X)
- 400 V and 800 V versions for different output voltage ranges
- OBC power 3.3 kW / 4 kW / 6.6 kW / 11 kW / 20 kW / 40 kW
- Integrated system with DC/DC Converters & PDU
- Customizable OEM / ODM service
Discover our on board charger systems here: https://brogenevsolution.com/obc-dcdc-pdu/
Business inquiry: contact@brogenevsolution.com
Contact Us
Get in touch with us by sending us an email, using the Whatsapp number below, or filling in the form below. We usually reply within 2 business days.
Email: contact@brogenevsolution.com
Respond within 1 business day
Whatsapp: +8619352173376
Business hours: 9 am to 6 pm, GMT+8, Mon. to Fri.
LinkedIn channel
Follow us for regular updates >
YouTube channel
Ev systems introduction & industry insights >