Introduction of the Electric Drive Axle for Heavy Duty Trucks
Sales of electric trucks have continued to rise in 2023 compared to 2022, driven by strong and ambitious government policies. For heavy-duty vehicle manufacturers, adopting a reliable and powerful electric powertrain system is crucial to staying competitive in this rapidly expanding market. As demand for sustainable transportation grows, integrating advanced electric systems will be key to their long-term success.
The Evolution of the Electric Drive Axle for Heavy Duty Trucks
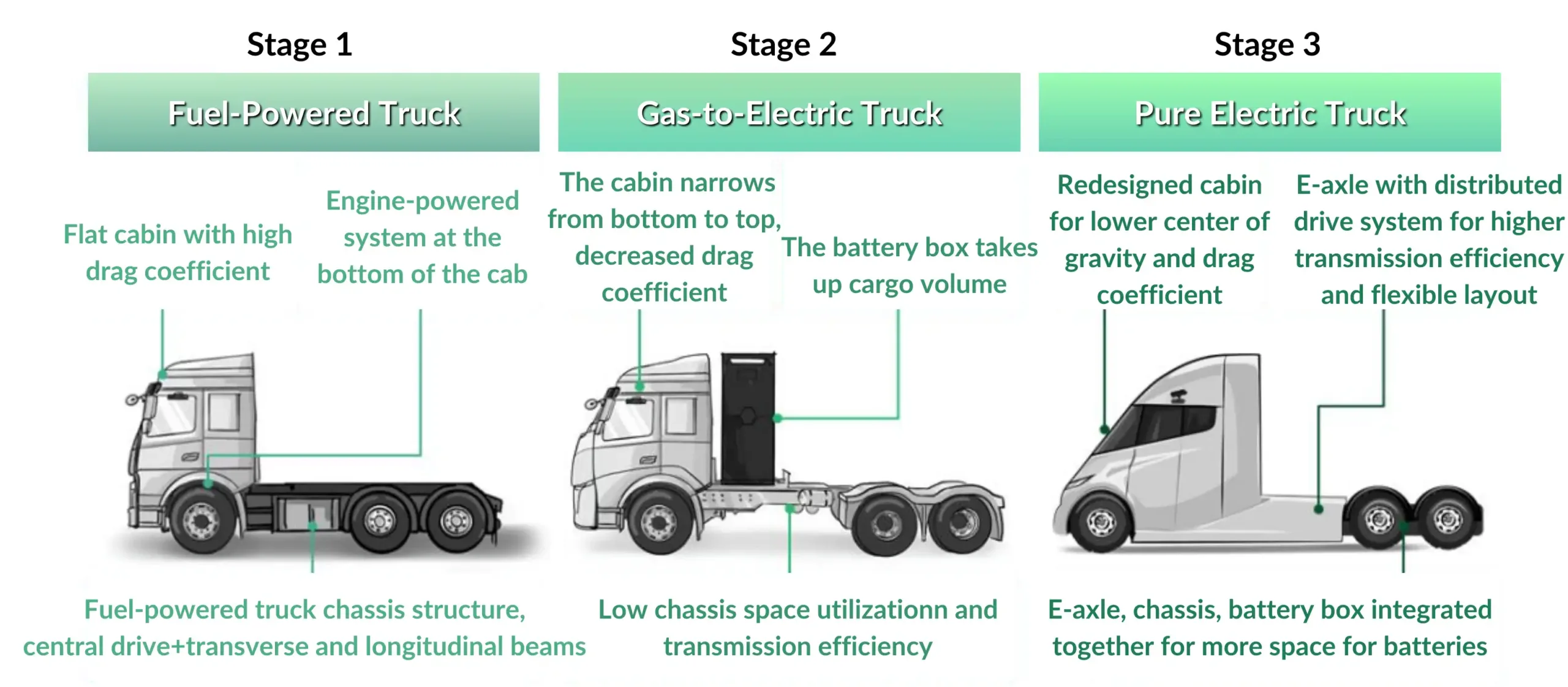
The evolution of heavy-duty trucks has gone through three distinct phases, with a vision of the future of electric mobility shaping the landscape. First, traditional fuel-powered trucks dominated the roads, with cabs that were flat and high drag coefficient. These trucks relied on engine-based power systems located at the bottom of the cab.
The next phase saw the emergence of gas-electric heavy-duty trucks, which retained the central drive model but swapped the engine for electric motors. However, these vehicles retained conventional propulsion systems that were bulky, inefficient, and compromised cargo space due to rear-mounted battery boxes.
Today, all-electric heavy-duty trucks typically use the electric axle as the e-powertrain system. EV solutions with electric drive axles provide increased transmission efficiency and space flexibility. At the same time, cabin structures are redesigned to lower the center of gravity and improve aerodynamics.
Why The Electric Drive Axle is a Better Choice for Battery-Electric Trucks
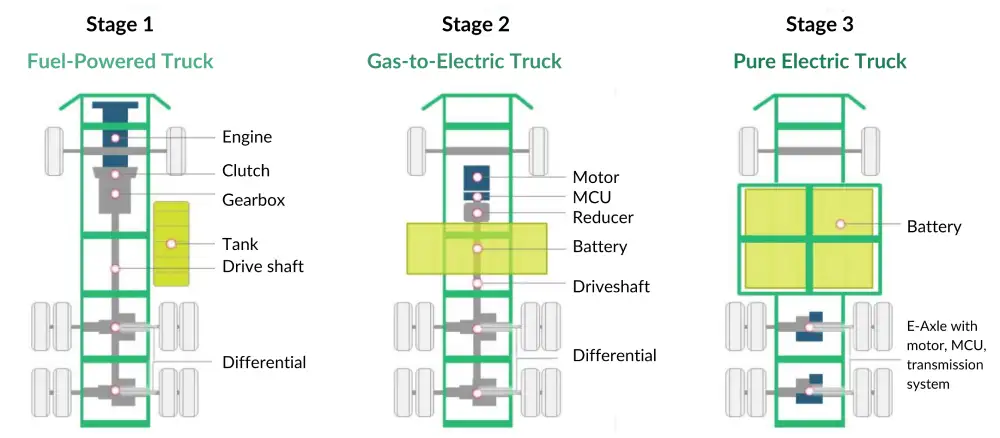
Building on the advanced design of the electric axle drive system, the structural design of the chassis for pure electric heavy-duty trucks can be further optimized, resulting in more efficient use of space. For example, all-electric heavy-duty trucks using our e-axle solution can eliminate traditional driveshafts, allowing the chassis structure to be redesigned to accommodate the battery spread flat across the chassis. This layout has many advantages:
- Placing the battery flat at the bottom allows for a larger battery capacity, extending the range while minimizing intrusion into the cargo area.
- By using a box-shaped beam frame structure, the battery pack is placed within the box frame structure, ensuring both battery safety and full utilization of the chassis load capacity.
- Lowering the vehicle’s overall center of gravity reduces the risk of rollover during cornering and improves driving stability and maneuverability.
- The overall appearance of the vehicle is improved.
Analysis of Different Electric Powertrain Systems for Heavy Trucks
At present, the primary e-powertrain configurations for electric heavy trucks encompass several distinct forms:
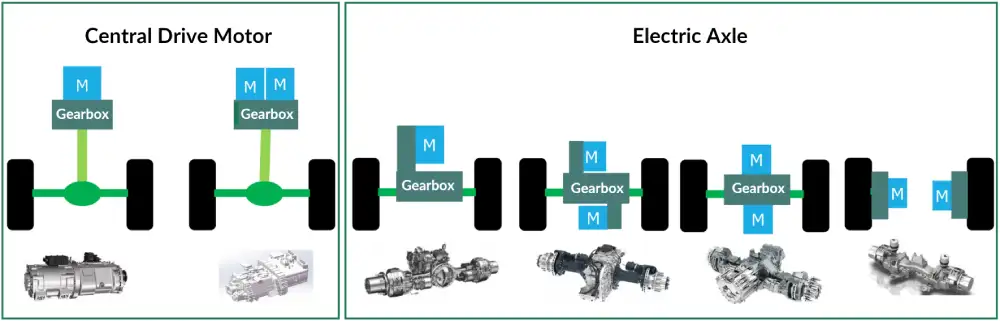

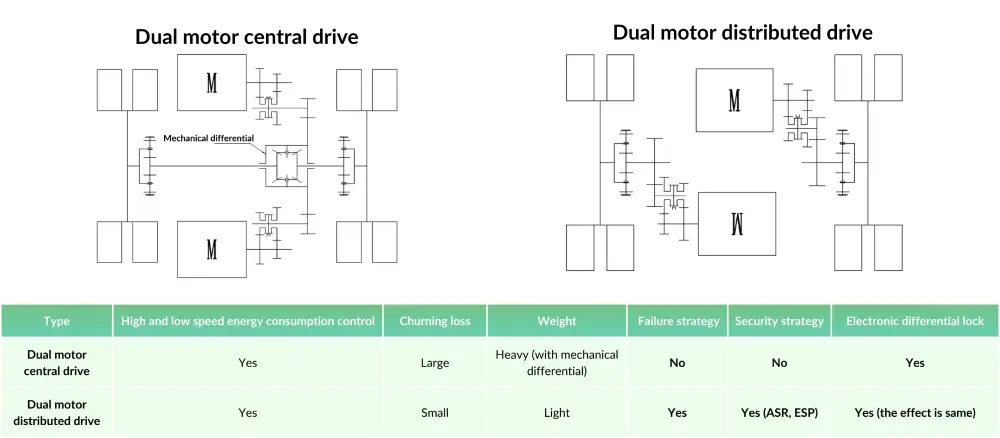
An Example of Our Electric Drive Axle for Heavy Duty Trucks
Let’s take our 360 kW eAxle as an example, which is suitable for 6×4 and 4×2 tractors and heavy-duty trucks. Compared to similar eAxle products on the market, our eAxle integrates two motors, providing higher system power and torque with a smaller footprint, and has 100% regenerative braking capability, eliminating mechanical differentials. This results in lower space requirements, weight, and cost.
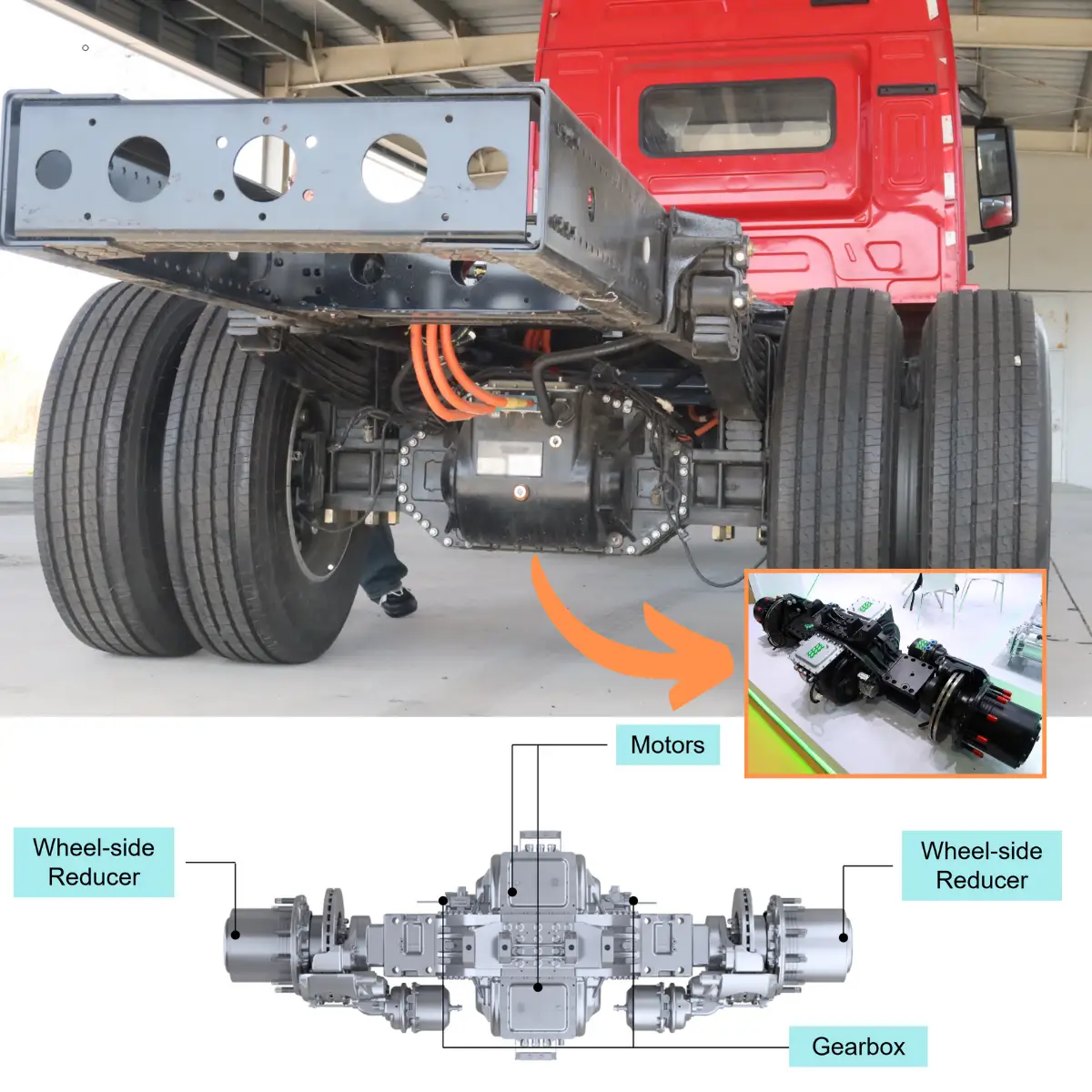
Additional Safety Redundancy
In addition, our distributed drive system minimizes layout losses, reduces weight, and incorporates fault and safety strategies. The two drive systems are completely independent, consisting of a motor + 2-speed AMT and wheel-side reducer, using electronic differential technology and independently controlling the left and right drive systems. In the event of a single motor failure, the other motor can continue to operate normally, ensuring system safety.
23% System Weight Reduction
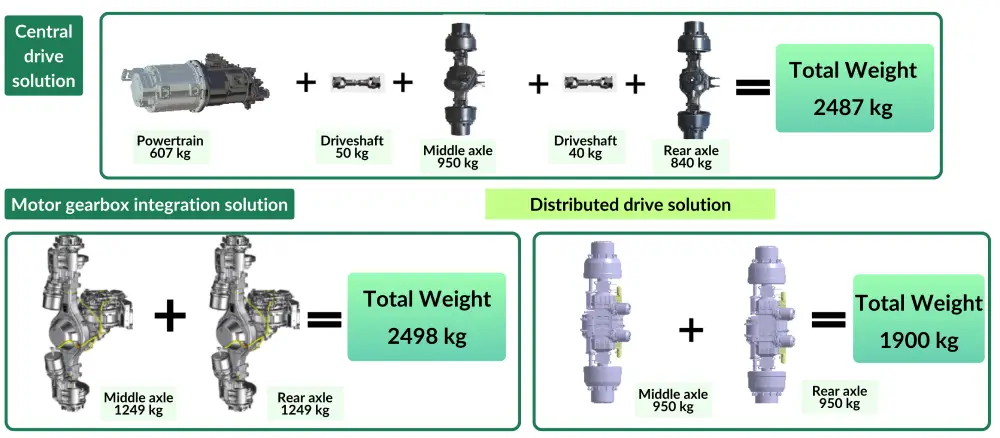
In contrast to the central drive system, our distributed drive system has achieved a weight reduction of 23.6%. Similarly, compared to the motor gearbox integration system, our distributed drive system has managed to reduce weight by 23.9%.
Good Passability

The distributed drive system boasts a 7.3% increase in ground clearance compared to the central drive system. Moreover, it achieves an even greater elevation of 11.7% when compared to the motor gearbox integration system.
Higher Transmission Efficiency
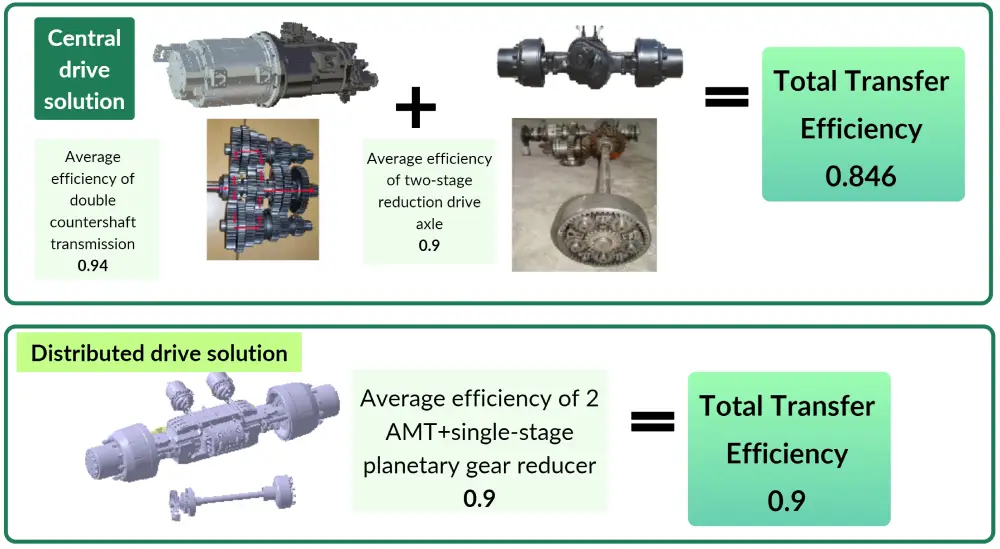
Compared to the central drive system, our distributed drive system demonstrates a 6% enhancement in overall transmission efficiency.
High Security

Currently, heavy-duty trucks are only equipped with ABS and lack ASR, ESC, and EDL. With our EV motor’s electronic differential system strategy control, heavy trucks can be equipped with ASR/ESC safety configurations, improving vehicle traction, stability, and safety.
Technical Parameters for Brogen Electric Drive Axle for Heavy Duty Vehicles
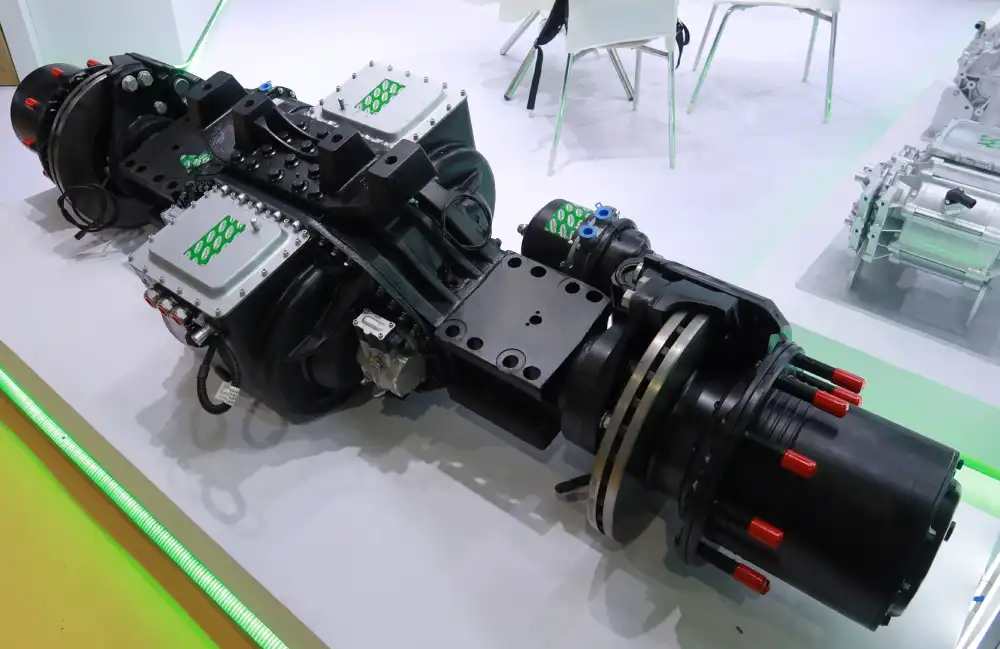
- Motor power (peak/rated): 2×180 kW / 2×80 kW
- Motor speed (max.): 9500 rpm
- Motor torque (peak/rated): 2×520 N.m / 2×260 N.m
- Maximum output torque: 50000 N.m
- Rated voltage: 540 VDC
- Axle weight: 950 kg
- Rated axle load: 13000 kg
- Wheel speed (max.): 620 rpm
- Gear ratio: 49.4/15.3
Solution Advantages
- The dual motor structure ensures uninterrupted power during gear shifts.
- Reduces vehicle weight by 300 kg, boosting loading capacity.
- A compact design saves chassis space and lowers the center of gravity for better stability.
- Maximum output torque of 50,000 N.m, ideal for 4×2 tractors.
- Passed 1 million load-bearing tests with 2.5 times load capacity, ensuring reliability.
- Equipped with ASR function for enhanced grip on slippery surfaces, ensuring safer driving.
Relevant Solution
- All Posts
- Autonomous Vehicles
- EV Industry
- Heavy Transport
- Industry Insight
- Light Commercial Vehicles
- Marine Electrification
- Public Transportation
- Specialty Equipment
- Technologies
Contact Us
Get in touch with us by sending us an email, using the Whatsapp number below, or filling in the form below. We usually reply within 2 business days.
Email: contact@brogenevsolution.com
Respond within 1 business day
Whatsapp: +8619352173376
Business hours: 9 am to 6 pm, GMT+8, Mon. to Fri.
LinkedIn channel
Follow us for regular updates >
YouTube channel
Ev systems introduction & industry insights >