4 Motors With 1000 HP for Electric Heavy Trucks? Our Electric Truck Axle May Exceed Your Expectations
The semi-truck shown here is a battery-swapping electric tractor equipped with our 360 kW electric truck axles. It features two rear electric drive axles, each e-axle housing two motors, delivering 180 kW of peak power per motor. Together, they generate a total of 720 kW, nearly 1000 horsepower. And there’s even more beneath the surface.
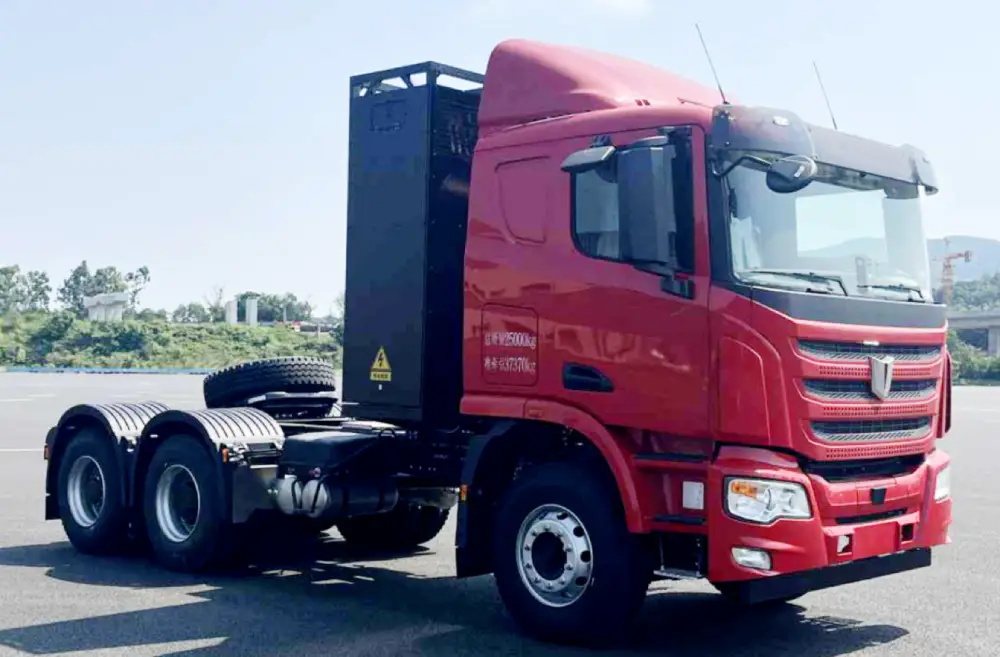
Our electric axle integrates the motors, along with key components such as the speed reducer and differential gear, directly into the rear axle. The total weight of the electric axle is 950 kg, with each axle capable of delivering up to 50,000 N.m of torque, ensuring abundant power for heavy-duty operations.
One of the unique features of this e-axle is its distributed drive system. This means that each motor operates independently, providing added safety redundancy—if one motor fails, the other can continue to function normally.
There are additional benefits as well. To improve efficiency, the vehicle’s design allows for both motors to work simultaneously or to alternate between them. When the truck is unloaded, only a minimal amount of power is used, as the motors take turns powering the vehicle. During start-up or climbing, both motors can work together, delivering maximum power. This cooperative strategy is coordinated with the vehicle’s overall control system.
For fully electric trucks carrying heavy loads, alternating between the two motors helps prevent overheating, keeping both motors within their optimal operating range. This not only enhances reliability but also enables the motors to work together to deliver ideal power and torque when high demand is required. For example, the maximum torque output of our single electric axle reaches an impressive 50,000 N.m, an extraordinary figure for a heavy-duty tractor.
We all know that traditional motor layouts are often limited by space and require numerous components. In contrast, the integrated design of our electric axle, with its compact central structure, reduces the number of parts needed. For example, our e-axle weighs 950 kg, contributing to a vehicle weight reduction of 300 kg.
The highly integrated design also frees up valuable chassis space in electric trucks, a critical factor given the current focus on maximizing battery capacity for longer range. This central, compact electric axle allows for more or larger battery packs, improving range. It is also compatible with a variety of suspension systems, including air suspensions and multi-leaf springs, making it adaptable to different truck platforms.
By integrating the entire axle assembly into the chassis, and using a highly compact dual-motor design, we’ve reduced the number of parts in the drivetrain, leading to higher transmission efficiency and more effective regenerative braking—both of which contribute to extending the vehicle’s range.
This central, integrated electric axle not only offers higher reliability but also benefits from reduced weight, increased chassis space, and higher transmission efficiency. With the rise of hydrogen fuel cell systems, which require even more chassis space than pure electric trucks, this axle design is undoubtedly poised to become the mainstream choice, offering tremendous market potential in the future.