Electric Heavy-Duty Truck Design: Which E-Powertrain is Better?
At Brogen, we’ve spent a lot of time developing electric axle systems for commercial vehicles, particularly in heavy-duty applications like semi-trucks, tractors, and trailers. In this article, we’ll explore different electric powertrain systems, compare solutions, and discuss the pros and cons of each.
1. Types of E-Powertrain Systems
Electric powertrain systems for heavy-duty vehicles can be categorized into three main configurations based on motor layout:
- Central Direct Drive:
- Direct drive motor
- Electric Drive Axles:
- Parallel-Axis E-Axle
- Coaxial E-Axle
- Vertical-axis E-Axle
- Distributed Drive Systems
- Wheel-End Drive
- Wheel-Hub Drive
Each system offers unique advantages, and we’ll explore them in more detail below. But first, let’s look at some broader trends driving innovation in e-powertrain systems.
2. Key Trends in E-Powertrain Systems
2.1 Increasing Integration of E-Powertrain Systems
More and more, motors, gearboxes, controllers, and other key components are being integrated into compact units. This not only reduces weight and space but also improves overall system efficiency and reliability. For example, our 360 kW drive assembly integrates the motor and gearbox into a single unit, which optimizes the layout for heavy-duty trucks and saves valuable space. Similarly, our 360 kW electric axle for heavy commercial vehicles combines the drive system, transmission, braking, and other key components into a compact, efficient assembly.
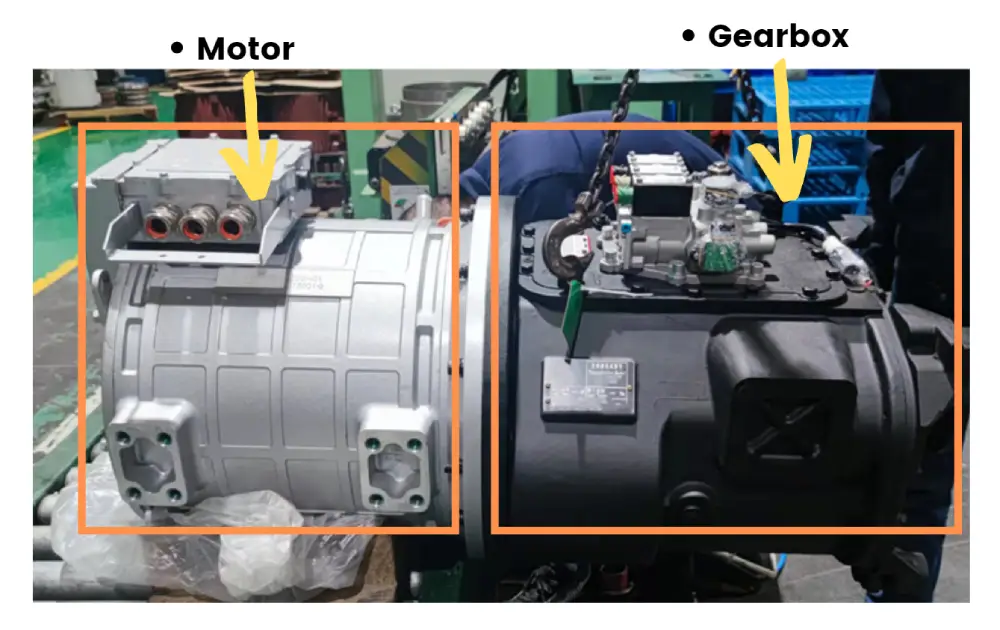
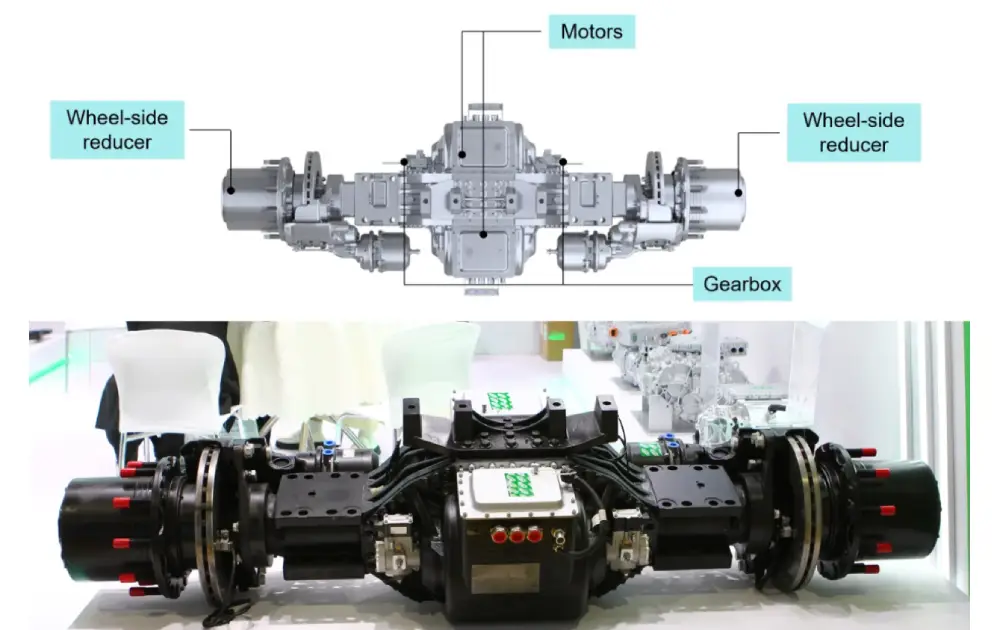
2.2 Adoption of Dual-Motor E-Powertrain Systems
Dual-motor setups are becoming increasingly popular, especially in high-end and specialized trucks. These systems offer better power distribution, improved energy efficiency, and enhanced performance for heavy loads. Our dual-motor drive assembly is a prime example, delivering continuous power during demanding conditions, such as hill climbs, while maximizing operational efficiency.
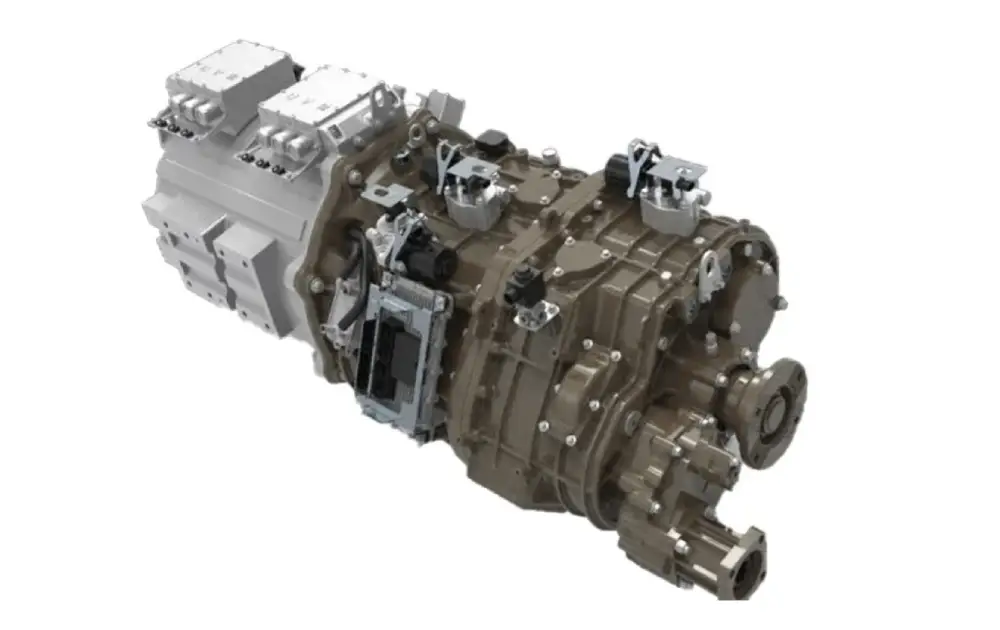

3. Central Direct Drive Systems: A Cost-Effective E-Powertrain Solution
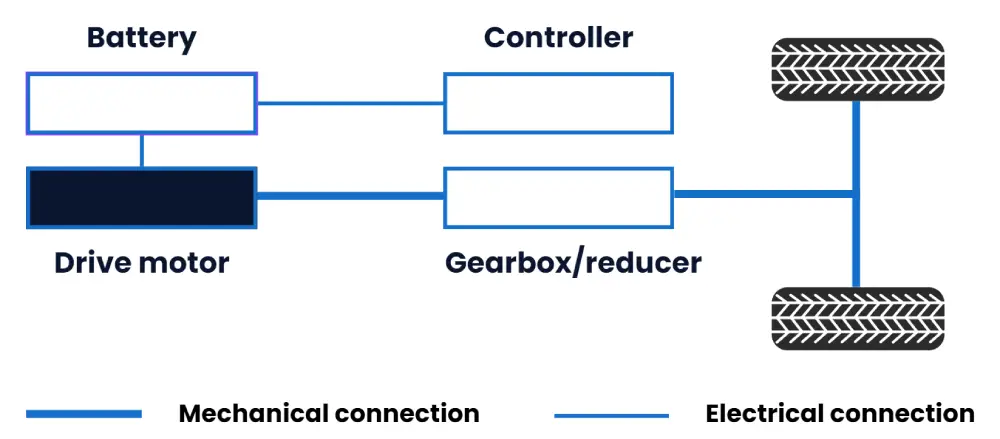
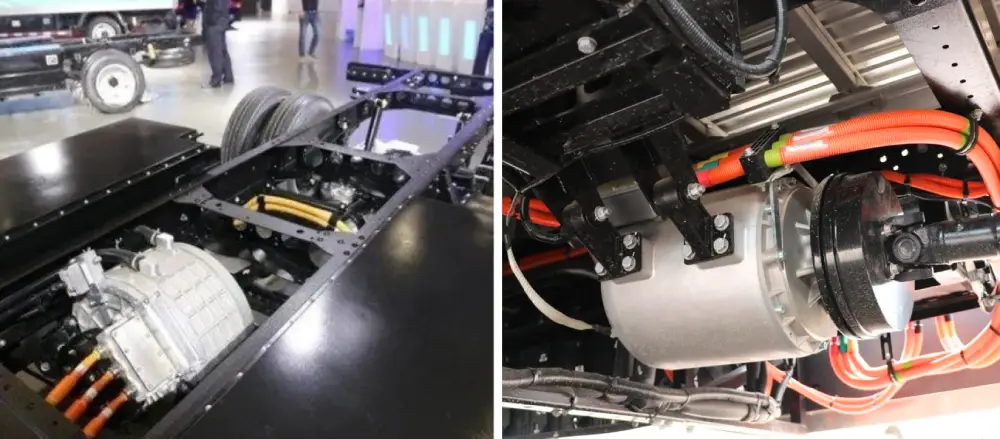
Central direct drive systems are primarily used to convert traditional fuel-powered trucks into electric vehicles. In this configuration, the engine is replaced with an electric motor, along with an electric drive unit (EDU), battery packs, and other key components. The original chassis remains largely unchanged, making this solution adaptable for a wide range of commercial vehicles.
Pros:
- Cost-Effective & Quick to Market: This is the most economical and fastest way to electrify existing vehicle platforms without extensive redesigns.
- Ease of Conversion: Many manufacturers opt for this approach as it allows them to enter the EV market without the significant financial and time investments required for developing a new platform.
Cons:
- Limited Battery Space: Since the original chassis isn’t significantly altered, space for battery packs is restricted, which limits driving range and affects battery cooling system layout.
- Compromised Handling & Comfort: Converted models often have poor weight distribution, leading to increased braking distances and reduced driving comfort.
Central direct drive systems are commonly used in short-distance transportation scenarios, such as ports, steel mills, power plants, and mines. They are less suited for medium- or long-distance travel.
4. Electric Drive Axles: Optimizing Space & Efficiency
In contrast, electric drive axles (e-axles) eliminate the need for a drive shaft, reducing vehicle weight and improving system efficiency. E-axles also allow for better space optimization for battery packs, increasing driving range and better overall efficiency.
Among the different types of electric drive axles, three main configurations stand out: parallel-axis, coaxial, and vertical-axis. Each configuration offers distinct advantages and challenges, making them suitable for various vehicle types and operational needs.
4.1 Parallel-Axis E-Axle


The parallel-axis electric drive axle is currently the most widely adopted configuration for electric axles in the market. In this system, the motor is positioned parallel to the axle, and the motor, drive axle, and AMT are integrated into a single unit.
This design eliminates the need for a drive shaft, reducing overall system weight and improving transmission efficiency. Additionally, this configuration uses helical gears, which significantly enhance reverse braking capability—from the typical 30% to an impressive 100%.
By removing traditional components such as the universal drive shaft, reducer, and suspension brackets, installation costs are significantly reduced compared to central direct drive systems. This compact design also saves weight and space, allowing for better battery placement and increased driving range.
However, there are drawbacks. The large unsprung weight of the system, combined with its offset configuration, can negatively impact the vehicle’s handling, especially in heavy-duty applications.
4.2 Coaxial Electric Drive Axle
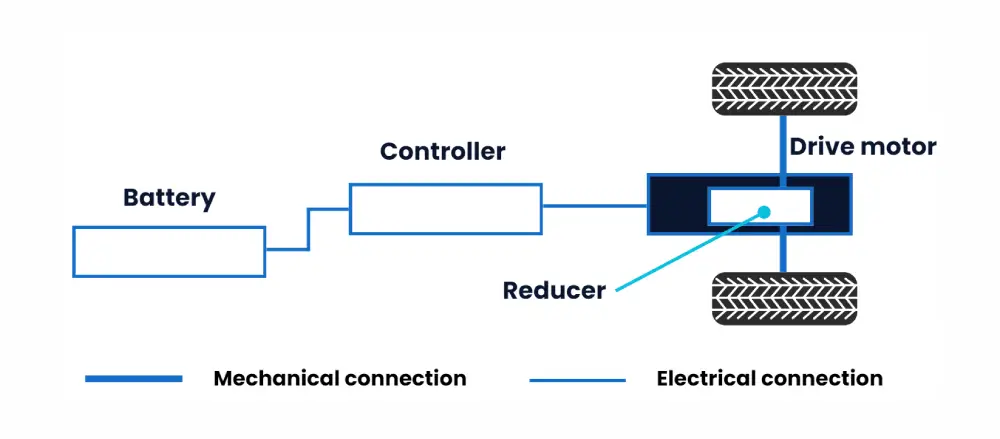
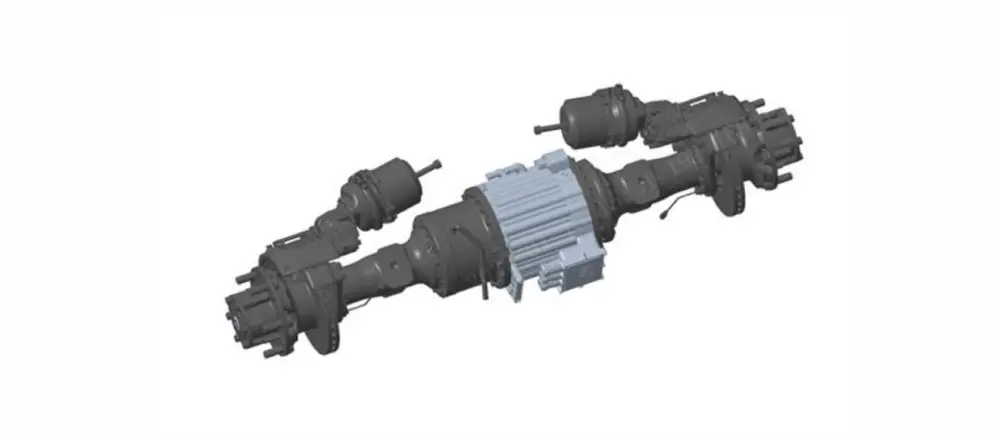
The coaxial electric drive axle features a motor aligned directly with the axle housing. This configuration creates a more compact and concentrated power system, which optimizes the vehicle’s overall chassis layout.
Due to its efficient space utilization, coaxial e-axles are ideal for smaller commercial vehicles like light vans and trucks weighing under 4.5 tons. However, their compact nature and lower power density make them unsuitable for heavy-duty vehicles, which require more robust power systems.
4.3 Vertical Axis Electric Drive Axle
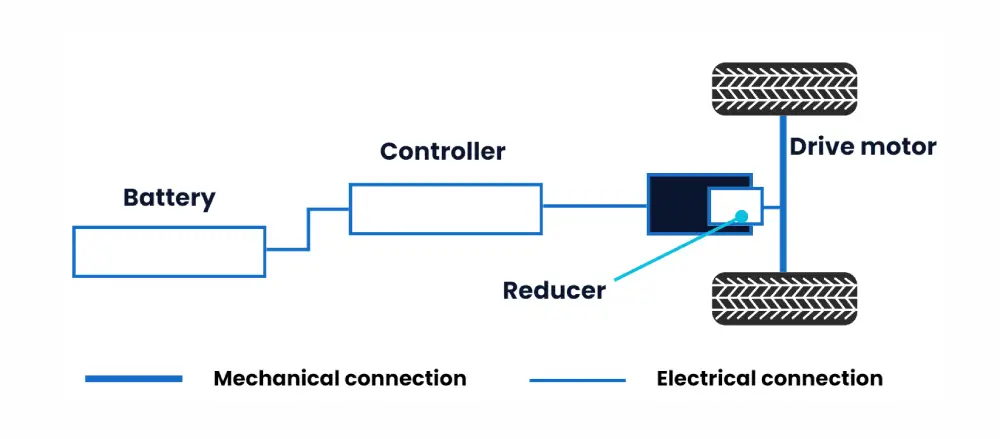
In the vertical axis electric drive axle, the motor is connected to the drive axle at a perpendicular angle. This setup offers some key advantages, such as lower installation costs and the efficient use of longitudinal space, which allows for better battery pack arrangement.
Despite these benefits, there are significant trade-offs. The vertical axis design has lower transmission efficiency compared to parallel-axis e-axles, and its system power density is not as high. Additionally, the use of hypoid gears for speed reduction results in a smaller speed ratio and poorer performance in NVH (noise, vibration, and harshness). As a result, this configuration is more commonly used in medium- and heavy-duty commercial vehicles.
5. Distributed Drive Systems
As electric vehicles continue to evolve, distributed drive systems are emerging as a powerful alternative to traditional powertrains. Distributed drive systems can be divided into two main types: wheel-end drive and wheel-hub drive. Each of these technologies offers distinct advantages, as well as unique challenges, making them particularly suitable for different types of vehicles, including buses, trucks, and electric cars.
5.1 Wheel-End Drive System
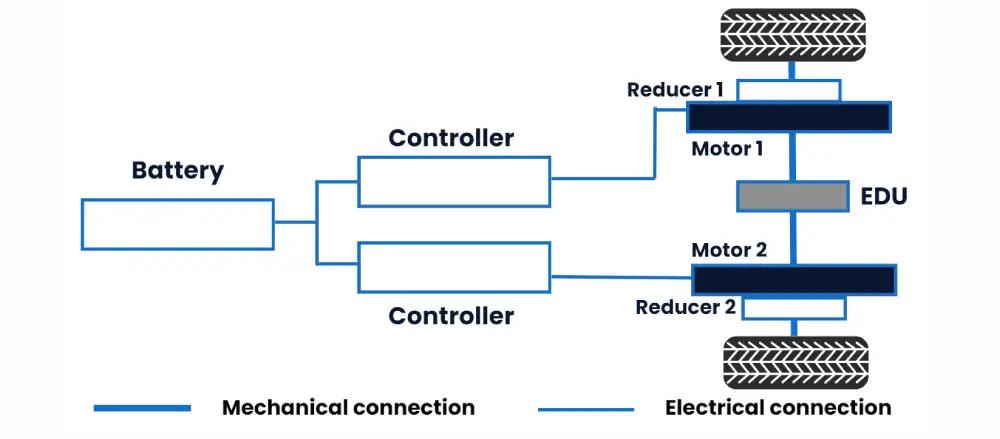
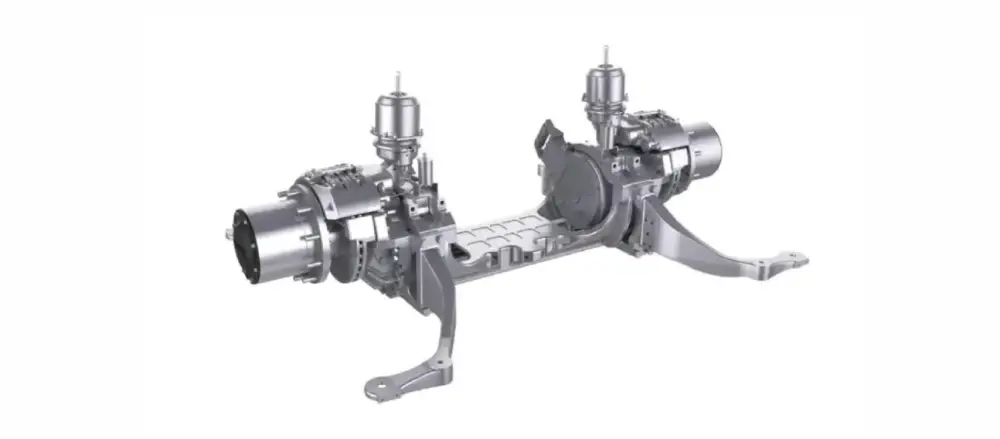
The wheel-end drive system has seen its first applications in buses and heavy trucks. This system places two drive motors on either side of the axle, with side reducers and wheel-side reducers working together to reduce speed and increase torque. This setup allows the wheels to be driven directly, providing quick response times—a major advantage for intelligent driving systems.
However, controlling a distributed system like this presents significant technical challenges. The most pressing issue lies in motor control: determining which motor should operate and when based on the driving conditions. This challenge requires advanced research and development, as it eliminates the need for a traditional differential. Instead, an electronic differential controller must be implemented to manage turning and ensure smooth handling.
Despite its complexity, the wheel-end drive system offers high precision, allowing torque and force to be finely controlled. However, this precision comes at the cost of increased complexity. Additionally, the higher unsprung weight of the motors negatively impacts ride comfort, making it less attractive to some vehicle manufacturers. As a result, only a limited number of bus manufacturers have adopted this technology so far.
5.2 Wheel-Hub Drive System
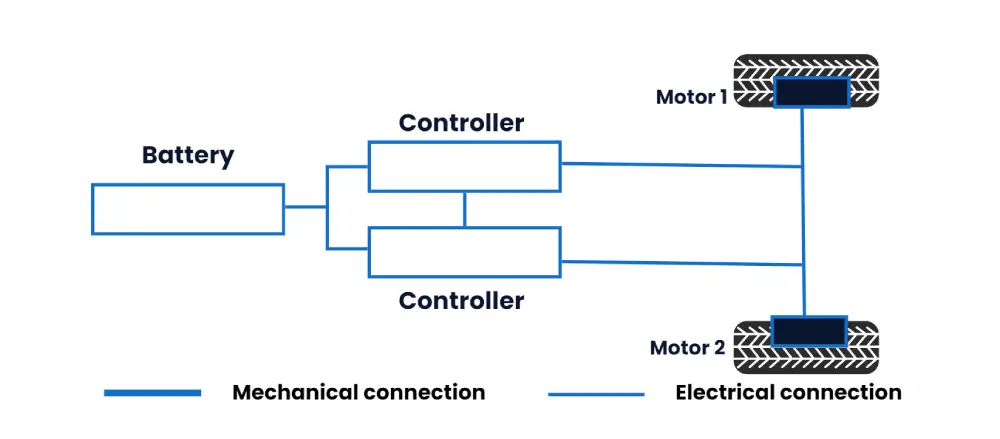
The wheel-hub drive system is not a new concept. In fact, as early as 1900, electric vehicles equipped with wheel hub motors were already being developed. By the 1970s, this technology was applied to mining transport vehicles, and today, it has resurfaced as a potential solution for modern electric vehicles.
Pros:
- Simplified Vehicle Structure: By eliminating traditional transmission components, wheel-hub drives simplify the vehicle’s mechanical setup, reducing complexity.
- Enhanced Space Utilization: With fewer components, these systems allow for better use of space within the vehicle, potentially improving interior design and cargo capacity.
- Higher Transmission Efficiency: The direct integration of motors into the wheels increases transmission efficiency by reducing power losses associated with conventional drivetrains.
- Flexible Drive Configurations: Wheel-hub drives enable versatile drive setups, including front-wheel drive, rear-wheel drive, and full-time all-wheel drive, with each wheel powered independently.
- Ideal for Electric and Hybrid Vehicles: They can serve as the primary power source for fully electric, fuel cell, or range-extended electric vehicles and provide additional support in hybrid systems for enhanced acceleration and performance.
Cons:
- Increased Unsprung Mass: The addition of hub motors increases the vehicle’s unsprung mass, which can negatively affect handling and ride comfort.
- Limited Braking Capacity: The braking performance of wheel-hub systems is often insufficient on its own, necessitating additional mechanical brakes to ensure safe and effective stopping power.
- Durability Concerns: Operating in harsh environments exposes hub motors to water, dust, and debris, requiring robust sealing and durable design to maintain long-term functionality.
- Cooling Challenges: Effective cooling is crucial due to the unique heat dissipation requirements of hub motors, which can complicate the design and maintenance of the cooling system.
6. Comparing E-Powertrain Systems: Central Direct Drives vs. E-Axles
In our previous discussions, we explored the main types of e-powertrain systems and their advantages and disadvantages. Here, we focus on a detailed comparison between central drive systems and e-axles, highlighting their key benefits and current market trends.
6.1 Advantages of E-Axles Over Central Direct Drive Systems
- Streamlined Drivetrain: E-axles eliminate the need for a traditional drive shaft, which shortens the drivetrain and enhances overall system efficiency.
- Reduced Vehicle Weight: By integrating the motor and drivetrain components, e-axles help lower the vehicle’s total weight.
- Optimized Battery Placement: E-axles allow for battery installation inside the vehicle frame, improving safety and maximizing space for additional battery capacity.
- Increased Loading Space: With the drive shaft removed, e-axles free up valuable cargo space, which is crucial for loading and transport.
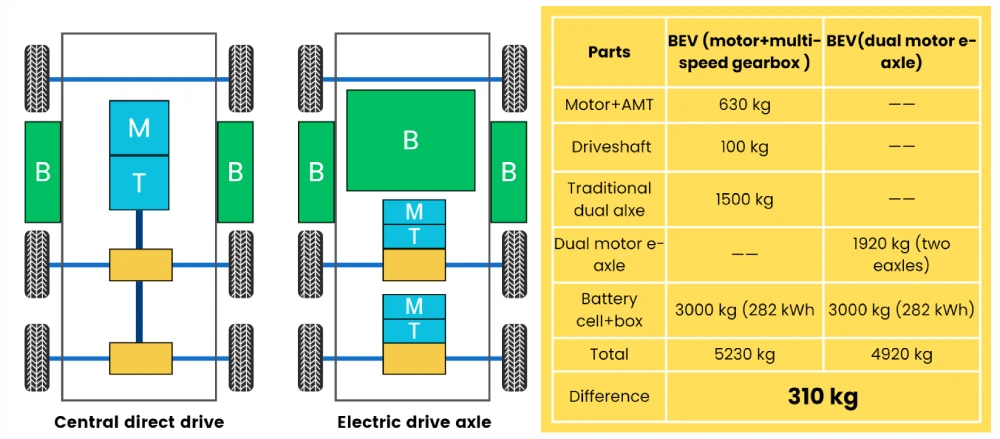
When comparing the weight of different e-powertrain setups, a notable difference emerges. For instance, a battery-electric truck with a central direct drive system, which includes a motor and multi-speed gearbox, has a powertrain weight of approximately 5,230 kilograms. In contrast, a truck equipped with two e-axles—each featuring dual motors—has a powertrain weight of around 4,920 kilograms with the same battery capacity. This setup reduces the overall weight by about 310 kilograms due to the elimination of the drive shaft.
7. Market Trends and Applications
Currently, both central direct drive systems and e-axles are prevalent in fully electric trucks, and both technologies are expected to coexist for the foreseeable future. E-axles are becoming increasingly popular, especially in light trucks under 4.5 tons, due to their higher integration and efficiency. They are particularly well-suited for standard highway applications and large-capacity trucks, where saving loading space is a significant advantage.
For heavy-duty and off-road applications, central direct drive systems combined with traditional drive axles remain a valuable solution. Their robustness and suitability for challenging environments ensure that they will continue to play a key role in the electric vehicle market.
In summary, while e-axles offer distinct advantages in terms of weight reduction, space optimization, and efficiency, central drive systems continue to be a complementary solution for specific applications. As electric vehicle technology advances, both systems will contribute to the ongoing evolution of sustainable transportation solutions.
8. Brogen's Advanced E-Powertrain Systems for Heavy-Duty Vehicles
At Brogen, we specialize in delivering cutting-edge e-powertrain systems designed to cater to the diverse requirements of heavy-duty vehicles, ranging from 12 tons to over 120 tons. Our portfolio includes central direct drive assemblies, integrated electric axles, and distributed electric axle solutions, with power outputs spanning from 144 kW to 800 kW.
8.1 Uninterrupted Power System
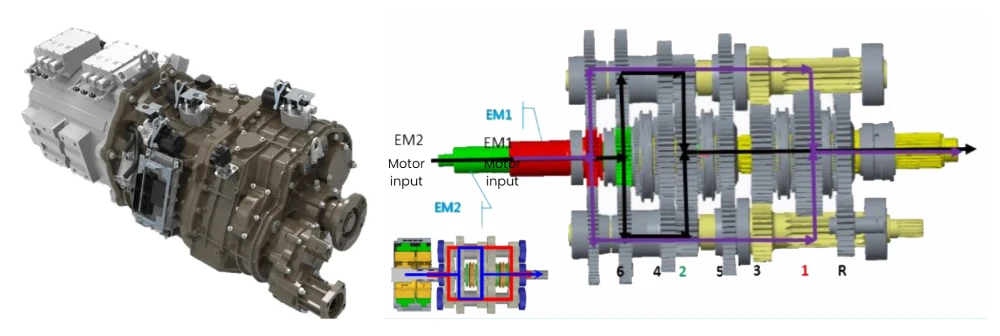
Our Uninterrupted Power System stands out for its innovative approach. This system utilizes a dual-winding motor paired with a dual-input gearbox, allowing both motors to function simultaneously. This design ensures that power remains uninterrupted during gear shifts. The dual-gear system operates with decoupled power sources, delivering high torque output and enhanced efficiency. Key benefits of this system include:
- Increased Hill-Climbing Speed: Approximately 20% higher compared to traditional manual transmission vehicles with the same horsepower.
- Enhanced Torque Output: More than 20% greater than comparable products.
- Significant Energy Savings: Over 40% savings on downhill slopes when fully loaded and 10-20% savings when empty.
8.2 Distributed Drive Electric Axle
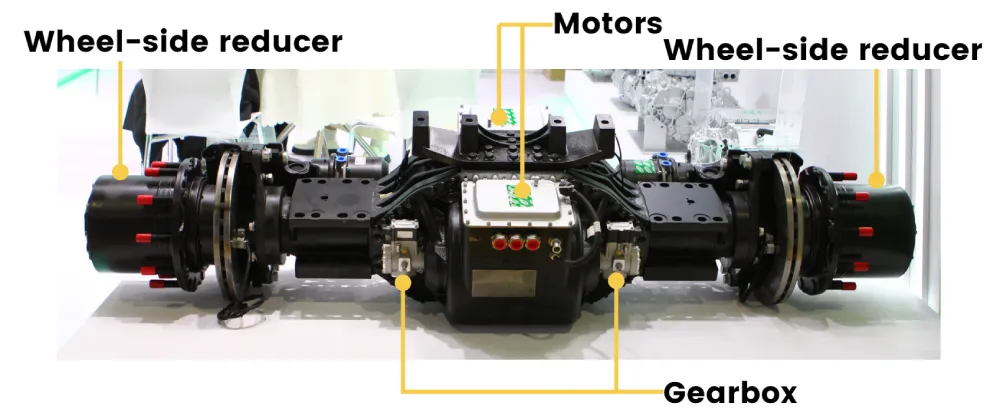
Our distributed drive electric axle is designed specifically for heavy-duty applications. It features a dual-motor distributed drive with completely independent power systems for each side. Each power unit includes a motor, a 2-speed AMT, and a wheel reducer. This system incorporates advanced electronic differential technology, allowing for precise control of the left and right drive systems. Advantages of this system include:
- Torque Recovery: 100% torque recovery with the IRBS.
- Energy Efficiency: 10-15% reduction in energy consumption compared to direct drive systems.
- Increased Cargo Capacity: A 10% increase over traditional models.
The distributed drive electric axle is particularly notable for its superior torque, reduced weight, regenerative braking capability, and torque vector control. With the growing adoption of hydrogen fuel cell systems, which demand even more chassis space than pure electric trucks, this axle design is set to become a mainstream choice, offering substantial market potential.
Contact Us
Get in touch with us by sending us an email, using the Whatsapp number below, or filling in the form below. We usually reply within 2 business days.
Email: contact@brogenevsolution.com
Respond within 1 business day
Whatsapp: +8619352173376
Business hours: 9 am to 6 pm, GMT+8, Mon. to Fri.
LinkedIn channel
Follow us for regular updates >
YouTube channel
Ev systems introduction & industry insights >