When it comes to the pure EV truck, understanding the differences between traditional electric motor structures and modern e-axle systems is crucial. Let’s use an electric dump truck as an example to explore these differences.
Traditional Drivetrain Structure – Direct Drive Motor
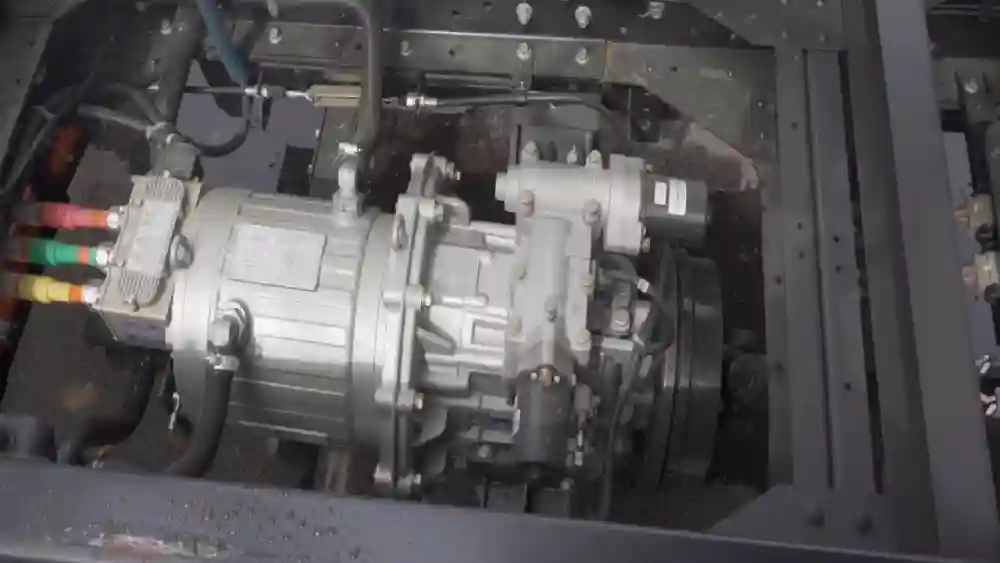
The traditional drivetrain in electric trucks closely resembles the layout found in conventional vehicles. The drive motor, equivalent to a diesel engine, is the heart of this system. Directly behind the motor is a reducer, functioning similarly to a traditional gearbox. The reducer’s job is to increase torque by reducing the motor’s speed, effectively amplifying power. This amplified power is then transmitted through a driveshaft to the rear axle. The rear axle, with a gear ratio of approximately 5.857, is comparable to that of traditional dump trucks.
How It Works
- Motor Output: The electric motor produces high-speed, low-torque power.
- Torque Amplification: The reducer uses gears to lower speed and increase torque.
- Power Transmission: This amplified torque is transmitted through the driveshaft to the rear axle.
- Final Drive: The rear axle further amplifies the torque and delivers it to the wheels, propelling the truck forward.
A notable feature of this system is the two-speed function of the reducer, which allows the vehicle to switch between different gear ratios based on the load, similar to shifting gears in a traditional transmission. This functionality provides both speed and power as needed.
E-Axle System
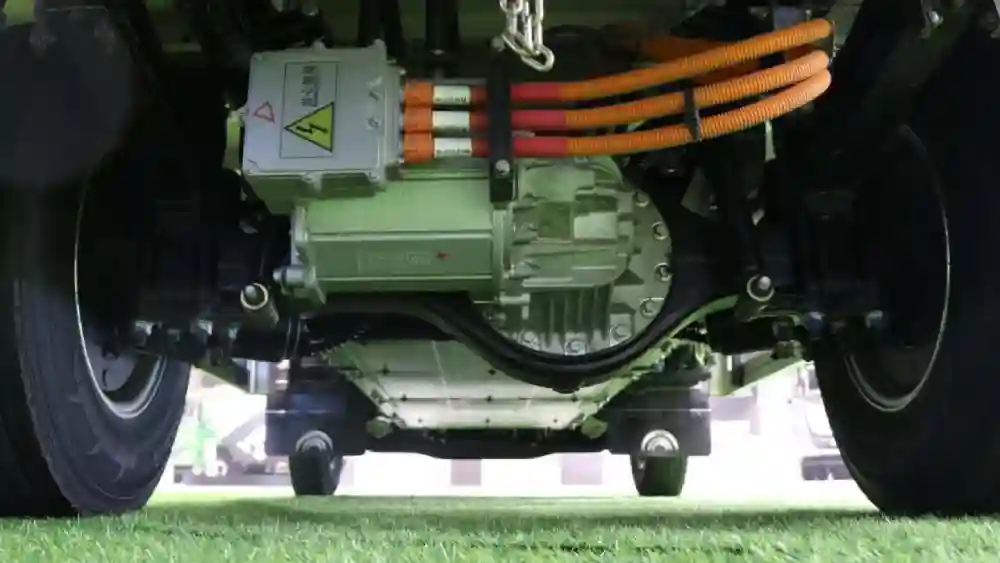
Now, let’s delve into the e-axle system. An e-axle integrates the electric motor with the rear axle, combining four major functions: the motor, rear axle, transmission, and differential. This integration brings several significant advantages:
- Lighter Weight: By eliminating the reducer and driveshaft, the e-axle reduces overall weight, allowing the truck to carry more cargo.
- Better Energy Efficiency: Directly driving the rear axle eliminates power loss associated with traditional setups, enhancing transmission efficiency and extending the vehicle’s range by approximately 20 kilometers.
- Increased Space Flexibility: Removing the motor, driveshaft, and gearbox frees up space within the chassis for additional batteries, further extending the vehicle’s range.
- Simplified Structure and Improved Reliability: With fewer complex and redundant parts, the e-axle is simpler and more reliable, resulting in lower failure rates.
However, the e-axle system does present challenges. Integrating the motor with the rear axle reduces space for torque amplification mechanisms, potentially limiting the power output compared to traditional setups with a gearbox. Achieving high power levels with an e-axle requires advanced design and engineering capabilities.
Brogen’s Solutions
At Brogen, we supply traditional drive motor and e-axle systems for electric vehicle builders. Our e-axle for heavy-duty trucks can deliver a maximum output torque of 50,000 Nm, providing ample power for these vehicles. Our electric motors offer power options ranging from 165 kW to nearly 800 kW, catering to various commercial vehicles, including light trucks, tractors, concrete mixers, and more.
Explore our cutting-edge electric axle solutions and see how Brogen can help you achieve success in the rapidly expanding e-mobility sector.