How to Choose the Right Electric Forklift Battery: The Complete Guide
Introduction
For businesses that rely on forklifts, the choice of electric forklift battery can significantly impact overall operational efficiency and, in the long run, influence substantial time and financial costs. By selecting the appropriate forklift battery, forklift manufacturers can ensure the safety and performance of their products in a competitive market. This guide will walk you through the various types of electric forklift batteries, their key differences, price ranges, and how these battery options can affect your business’s daily operations.
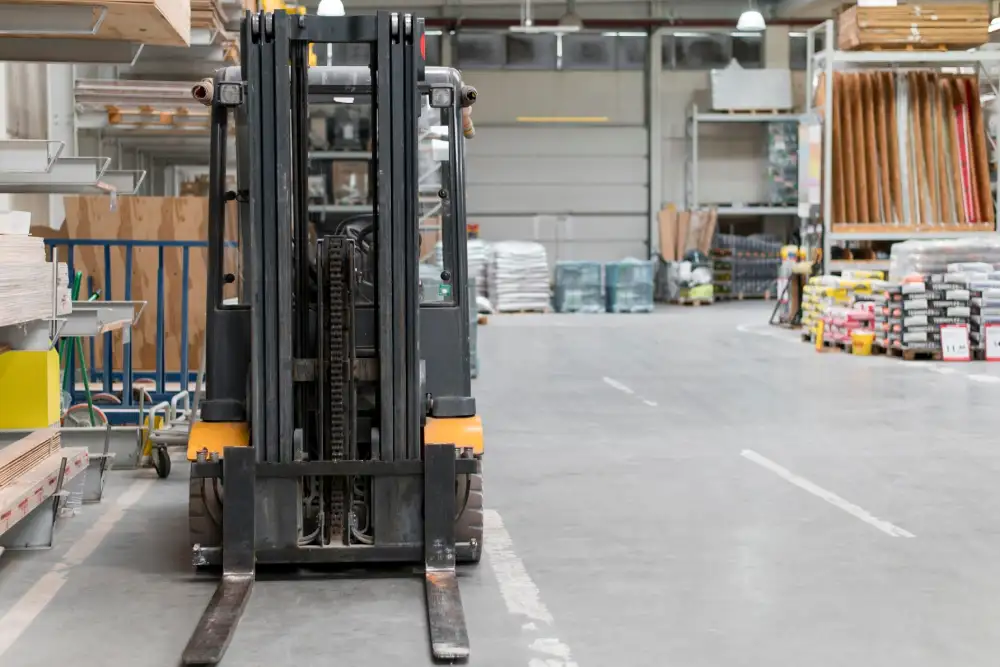
Quick Access
- Types of Electric Forklift Batteries
- Electric Forklift Battery Lifespan
- Electric Forklift Battery Maintenance
- Requirements for Forklift Battery Charging Stations
- Safety Comparison
- Price
- How to Determine if Lithium-Ion Batteries are Suitable for Your Forklifts
- How to Choose the Right Electric Forklift Battery
- Brogen's Electric Forklift Battery Solutions
- Contact Us
Types of Electric Forklift Batteries
There are two primary battery types powering electric forklifts: lead-acid and lithium-ion.
Lead-Acid Batteries
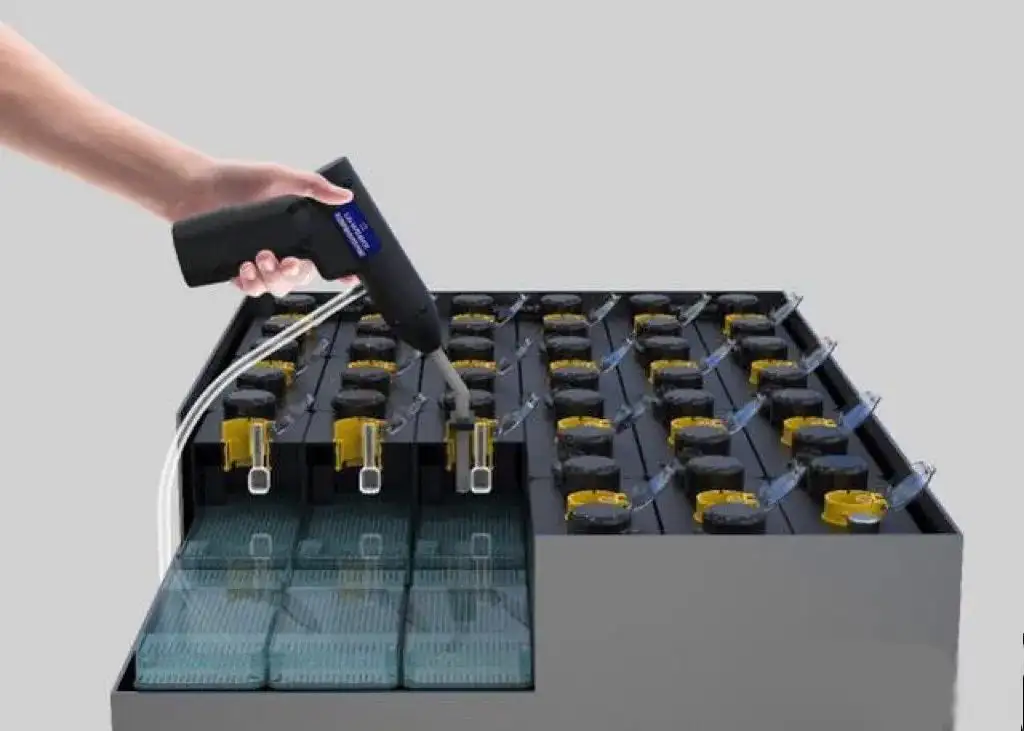
As the traditional choice for forklift power, lead-acid batteries utilize a chemical reaction between lead plates and sulfuric acid to generate electricity. These batteries are characterized by their bulky size, liquid electrolyte, and requirement for regular maintenance. Key components include cells, bars, plates of lead dioxide, cables, and electrolytes. The electrochemical reaction between the lead plates and the electrolyte solution allows for the flow of ions, producing an electric current.
Lithium-Ion Batteries (Primarily Lithium Iron Phosphate)
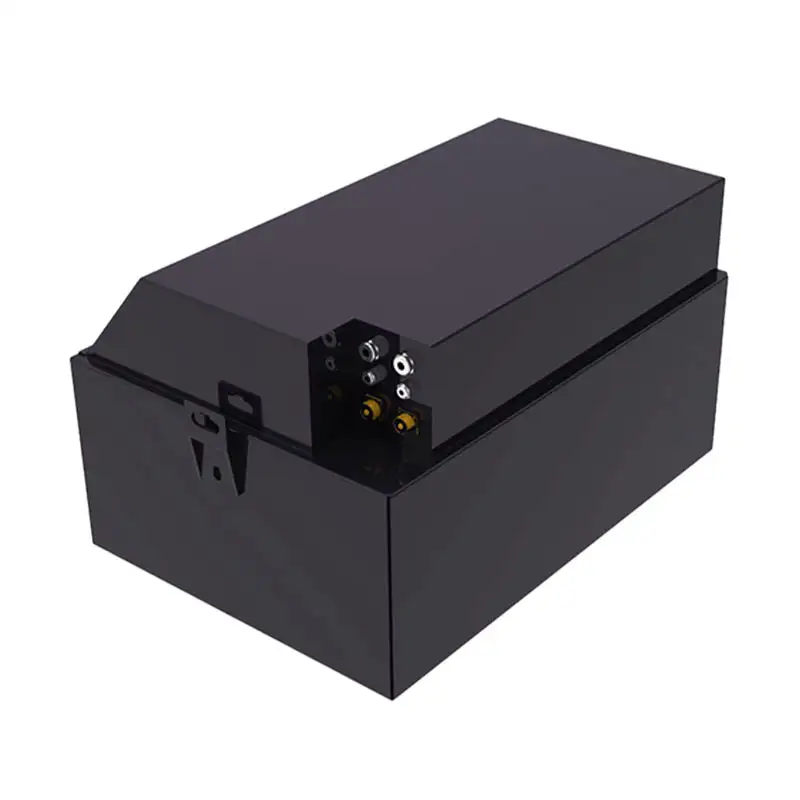
Introduced in the early 1990s, lithium-ion batteries, particularly Lithium Iron Phosphate (LFP), have gained significant popularity in the material handling industry. These batteries offer higher energy density and a more compact design compared to lead-acid batteries. They are sealed and require minimal maintenance. Lithium-ion batteries operate on the principle of lithium-ion movement between the anode and cathode through an electrolyte. During discharge, lithium ions move from the anode to the cathode, generating electricity.
Electric Forklift Battery Lifespan
Like any business expense, electric forklift batteries are a cost that needs to be managed over time. The type of battery a forklift uses determines how often the battery needs to be manually replaced. Lead-acid and lithium-ion batteries have different lifespans:
Lead-Acid Batteries: 1000 - 1500 cycles
Lead-acid batteries have a longer charging time compared to lithium-ion batteries. They are primarily charged using traditional charging methods, typically overnight after a shift, using a low current charge for approximately 8 to 10 hours until fully charged. After a long charging period, the batteries need to cool for 6 to 8 hours before they can be used again.
Traditional charging is mostly done overnight, making it suitable for single-shift operations. This also means that lead-acid batteries typically do not undergo opportunity charging. Doing so can quickly damage the battery, wear it out faster, and reduce the number of cycles. Overall, lead-acid forklift batteries can last 3 to 5 years (or 1000 to 1500 charge cycles) with a normal weekly operation of 40 hours.
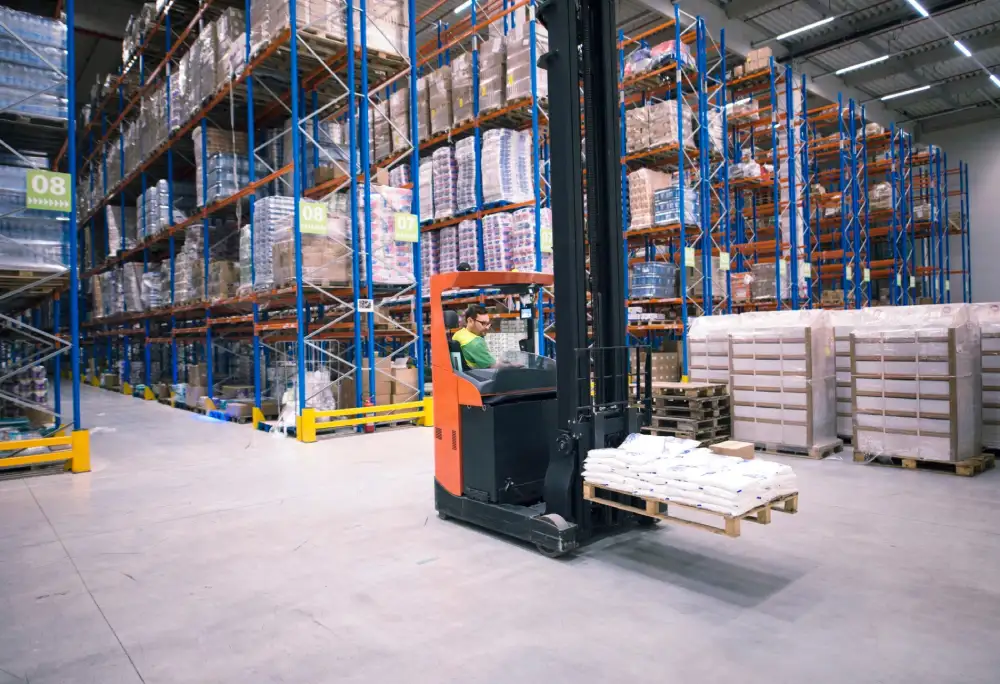
Lithium-Ion Batteries: 3500 cycles
Lithium-ion batteries can be easily charged using opportunity charging because they can be fast-charged. This type of charging involves using a specialized high-current charger to quickly recharge the battery. Opportunity charging can be done as needed or at convenient times, making lithium-ion batteries more efficient. If properly maintained, lithium-ion forklift batteries can last 2000 to 3000 cycles, or approximately 7 to 10 years (assuming 300 working days per year).
Electric Forklift Battery Maintenance
To ensure that lithium-ion and lead-acid batteries perform at their best, proper maintenance is essential. Without appropriate forklift battery maintenance, their lifespan can be significantly reduced. To maximize lifespan and overall battery capacity, users of both types of batteries should follow certain practices. However, lead-acid batteries require more care and attention compared to lithium-ion batteries.
Lead-Acid Forklift Battery Maintenance Requirements
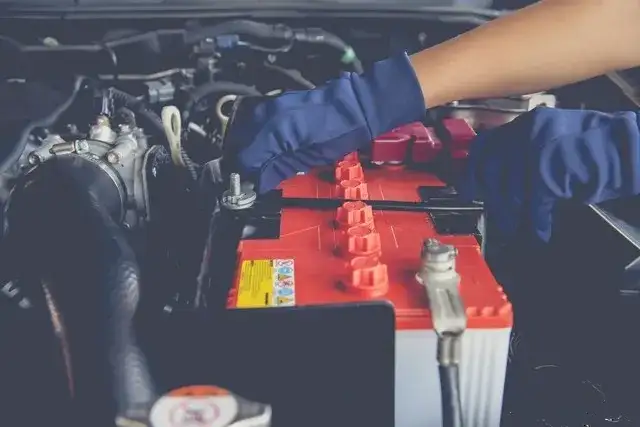
- Equalization (Battery Balancing): In traditional lead-acid batteries, internal acid, and water can often stratify (separate horizontally, with more concentrated acid near the bottom). This can lead to the formation of sulfate crystals at the bottom of the battery, reducing its ability to hold a charge. Equalization helps break down these crystals, but if the battery is left too long, the crystals may not break.
- Temperature Control: Lead-acid batteries must be kept within a certain temperature range to avoid shortening their lifespan. They can become very hot during charging, requiring a temperature-controlled space for charging and storage. Typically, using lead-acid batteries requires a significant fixed space to store the batteries.
Water Level Management: These batteries need to be checked approximately every 10 charge cycles to ensure they have enough water. “Watering” the battery can be a tedious and time-consuming task for individual batteries.
Lithium-ion Batteries Maintenance
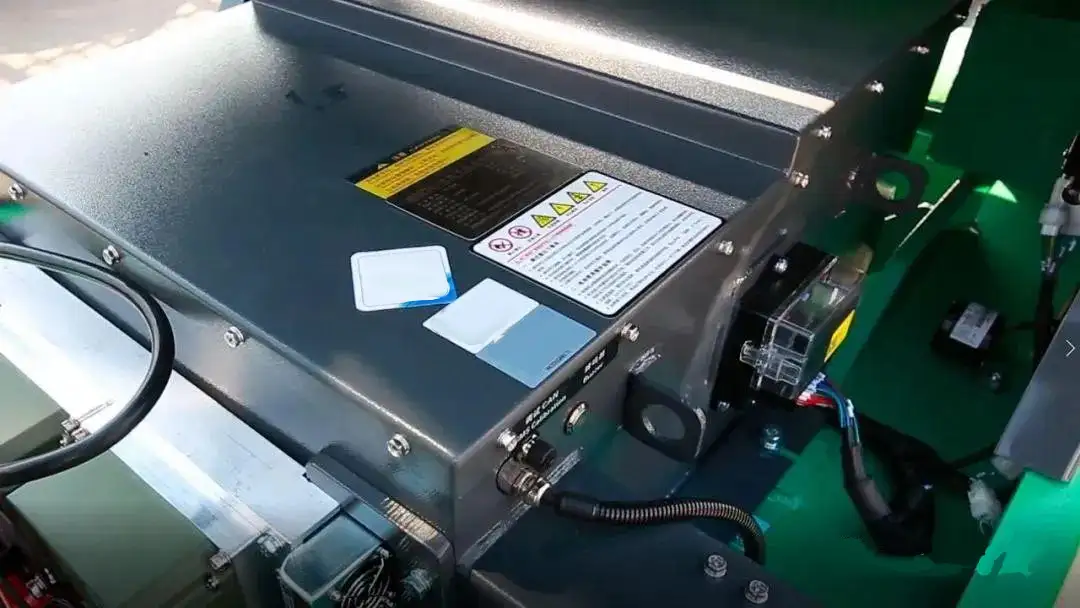
In comparison, lithium-ion batteries require much less maintenance. They come equipped with a Battery Management System (BMS) that automatically balances the cells, operate well at higher temperatures (making temperature control less of an issue), and do not require any water level management.
Requirements for Forklift Battery Charging Stations
Lead-Acid Forklift Battery
Lead-acid forklift batteries must be completely removed from the forklift and placed onto a separate forklift battery charger. Many of these chargers can perform equalization. If there are many forklifts in operation, multiple chargers are needed, and sufficient space is required for cooling several units after charging.
This process involves employees using specialized lifting equipment to swap out discharged batteries for charged ones regularly. While not physically demanding, this task can be time-consuming and may impact operational efficiency for those looking to optimize productivity.
Additionally, lead-acid batteries require dedicated charging areas with proper ventilation and temperature control. This is because they can become very hot and release harmful fumes during charging.
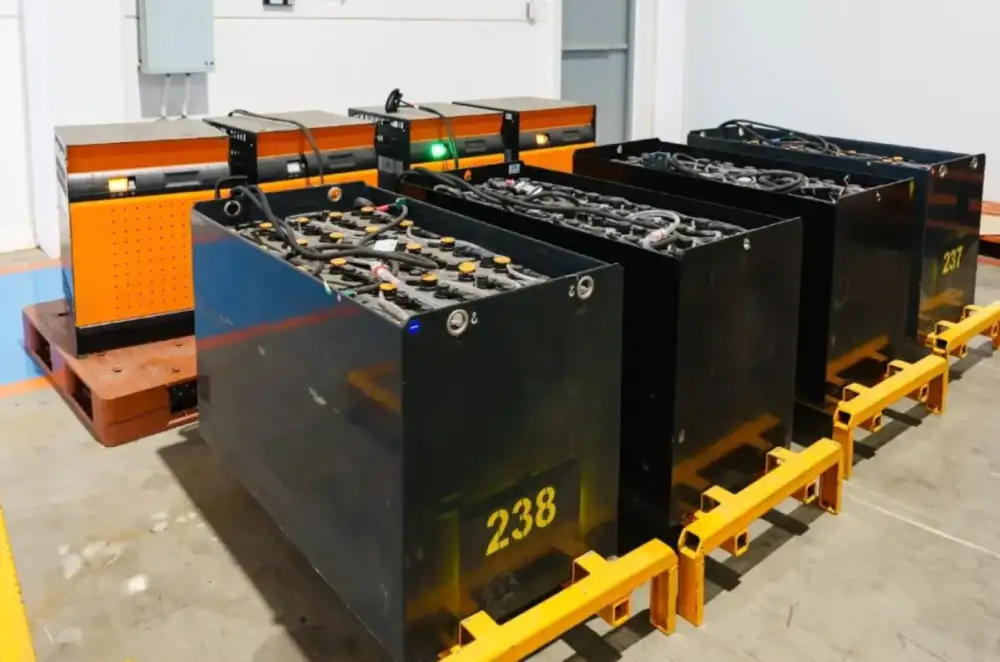
Lithium-ion Battery
In contrast, lithium-ion forklift batteries do not require separate charging spaces, cooling, or a fully charged backup battery when another is fully discharged—they can be plugged directly into the charger without needing to be removed from the forklift, making the charging process straightforward with no further actions required.
Safety Comparison
Safety Risks of Lead-Acid Forklift Batteries
Spillage: Lead-acid batteries contain highly toxic sulfuric acid, which can spill, especially since these batteries require weekly watering. If the watering process is not handled safely, employees could be exposed to serious risks. This necessitates the installation of wash stations in the workplace for emergency decontamination.
Overheating: During charging, lead-acid batteries can become extremely hot and may emit explosive gases when they reach peak charge. Proper temperature control is crucial for safety, and it is essential to carefully manage the safety protocols at forklift lead-acid battery charging stations.
- Hazardous Gases: Overcharging lead-acid batteries can release specific hazardous gases into the air, creating a highly dangerous situation, particularly in poorly ventilated areas. The primary gases released are hydrogen sulfide, hydrogen, and sulfur dioxide. A rotten egg smell indicates the presence of hydrogen sulfide, signaling the need for immediate precautions. Standard catalytic LEL (Lower Explosive Limit) gas sensors should be installed above the gas level in the charging room, or hydrogen-specific electrochemical sensors can be used. Since hydrogen is lighter than air, these sensors must be appropriately positioned.
Safety of Lithium-Ion Forklift Batteries
Lithium-ion forklift batteries are sealed, preventing acid leaks, corrosion, sulfation, or any type of contamination in the workplace. They are safe to use and charge, requiring minimal management from personnel.
Price
The cost of lithium-ion batteries varies significantly based on capacity, model, and performance, typically ranging from over $1,500 to over $5,500. On average, they can be twice as expensive as lead-acid batteries. However, in the long term, lithium-ion batteries are more cost-effective, particularly for forklift operators and rental companies.
Labor Cost Savings
Labor costs play a crucial role in determining the overall cost of a battery system. Lithium-ion batteries can be quickly and efficiently opportunity charged, significantly reducing labor expenses. This is because lithium-ion batteries:
- Stay in the equipment during charging.
- Do not need to be transported to a separate charging area.
- Do not require additional time for electrolyte solution replenishment.
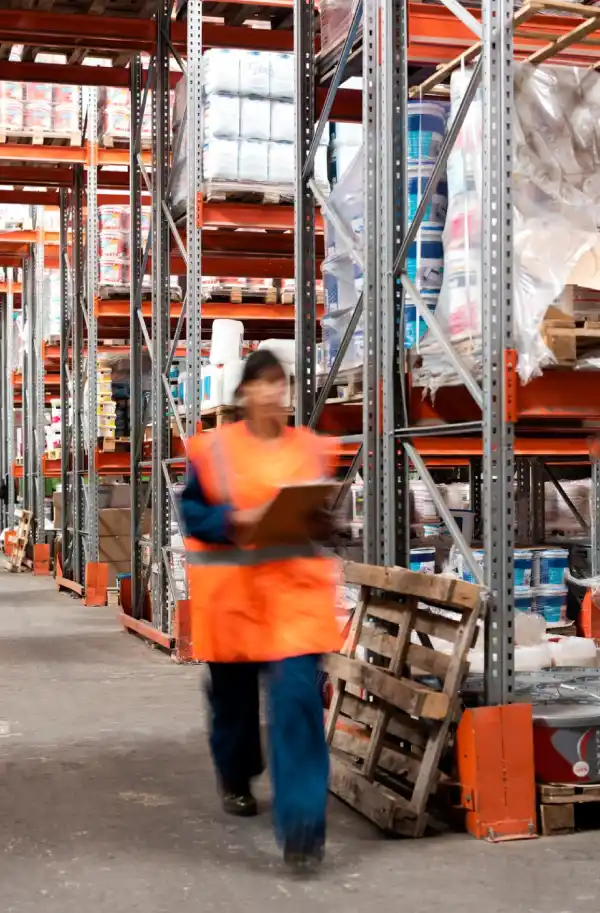
In contrast, charging lead-acid batteries involves:
- Operators using specialized lifting equipment to remove the heavy batteries and place them on storage racks for charging, which takes about 8 hours.
- A cooling phase that begins after charging and lasts another 8 hours.
- Transporting the batteries to a designated cooling area if the battery room needs space for charging other batteries.
Many forklift operators have found that switching to lithium-ion batteries can save over 140,000 USD annually, primarily due to eliminating productivity losses associated with the time-consuming charging process for lead-acid batteries.
How to Determine if Lithium-Ion Batteries are Suitable for Your Forklifts
In material handling operations, efficiency and productivity are crucial for success. With limited time each day, finding ways to accomplish more work in less time can provide a competitive advantage. Lithium-ion forklift batteries may help achieve this. Here are some factors to consider:
1. Do You Have Multi-Shift Operations?
Industries with multi-shift applications, such as manufacturing, third-party logistics (3PL), food processing, and other 24/7 material handling operations, benefit more from lithium-ion batteries. In these environments, lithium-ion batteries can pay for themselves in as little as 36 months. For single-shift operations, the return on investment for lithium-ion forklift batteries may take five years or longer.
2. Do You Operate in Freezer/Cold Storage Environments?
Lead-acid batteries do not perform well in cold or freezing conditions, with their capacity dropping by at least 35%. In contrast, lithium-ion forklift batteries maintain their capacity much better in cold temperatures and can charge quickly, even in cold storage. Thus, operations running forklifts in cold or freezing environments can quickly benefit from lithium-ion batteries.
3. Are You Operating on Tight Margins?
If your profit margins are slim, switching to lithium-ion forklift batteries can be advantageous. Why? By transitioning to lithium batteries, you can reduce energy costs, reclaim valuable space, and increase productivity. These changes can have an immediate impact. Lithium-ion forklift batteries can be up to 40% more energy-efficient than lead-acid batteries and up to 88% more efficient than diesel batteries.
While lead-acid forklift batteries may have a lower upfront cost, they come with higher maintenance costs. Increasing productivity and reducing energy costs are two key ways lithium-ion forklift batteries can save money.
How to Choose the Right Electric Forklift Battery
When selecting a forklift battery, it’s crucial to consider several factors to ensure you make the best choice for your needs:
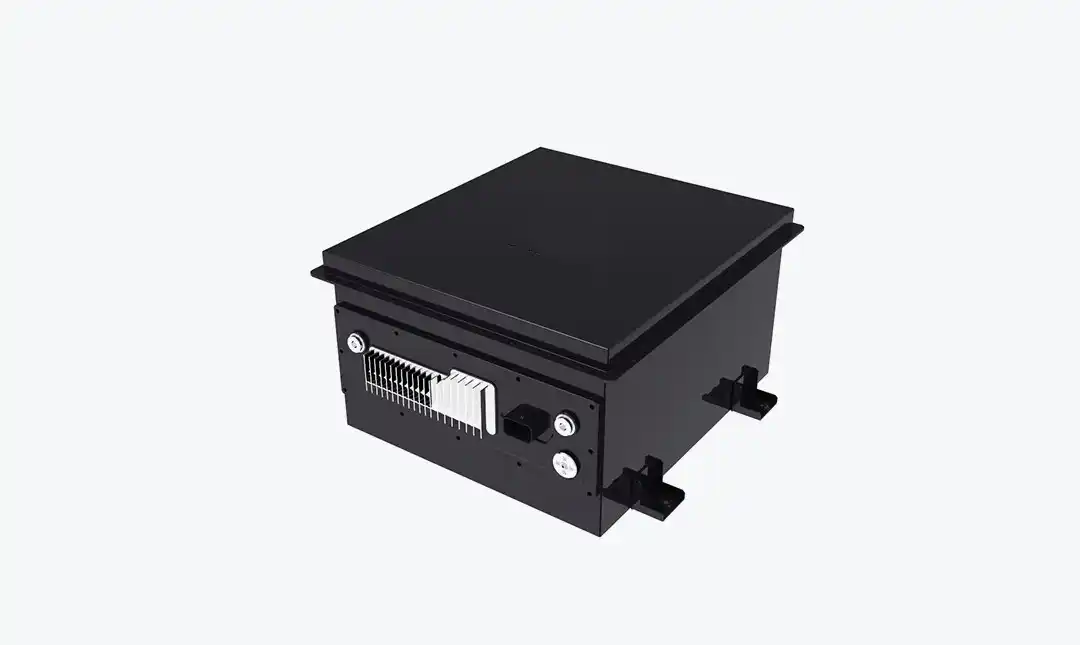
Forklift Battery Warranty
The cost of a new forklift battery is just one aspect to consider; the warranty is equally important. Opt for a battery with an extended warranty period and thoroughly review the warranty terms. Ensure that the warranty covers battery replacement in case of issues and includes replacement parts if needed.
Forklift Battery Compartment Size
Before purchasing a new battery, measure the width, depth, and height of your forklift’s battery compartment and record these dimensions. Avoid using the measurements of the previous battery to ensure you don’t limit yourself to the same model and have more options to choose from.
Forklift Voltage
Determine the voltage your forklift requires before buying a new battery. Most forklifts have their acceptable voltage range marked on an external panel. You can also refer to the manufacturer’s technical specifications. Choosing the wrong voltage battery can damage both the battery and the forklift. For example, lithium-ion forklift batteries are available in 24V, 36V, 48V, 72V, 80V, 90V, and 96V platforms to meet various forklift power needs.
Forklift Counterweight Requirements
Each forklift has a minimum battery weight requirement for safe operation. The counterweight provided by the forklift battery is essential for stability. You can find this data on the forklift’s nameplate or technical specifications. Generally, lithium batteries are lighter than lead-acid batteries, which is one of their main advantages. This ensures they can provide more power for the same size and weight.
Load and Travel Distance
In general, the heavier the load, the higher the lifting height, and the longer the travel distance, the larger the battery capacity required. If you want to maintain reliable output during a standard 8-hour shift, lithium batteries are a good performance choice.
Forklift Attachment Type
In addition to the load, the type of attachments used with the forklift is another factor to consider. Heavier loads require heavier attachments, which means you will need a larger capacity battery to provide sufficient power for reliable operation.
Connector Type
When choosing a forklift battery, the connector type is an important consideration. You need to know the position of the cables, the required length, and the type of connectors.
Forklift Operating Environment Temperature
Besides the cost of the battery, consider the typical operating environment temperature of the forklift. Lead-acid batteries work best between 15-25°C, and their capacity can significantly decrease if the temperature exceeds 40°C or falls below 0°C, affecting charge and discharge performance. Lithium batteries have better thermal stability and typically feature thermal management systems, performing well in a wide temperature range from -20°C to 55°C.
Our Solution
Delivering Powerful Electric Forklift Battery Solutions for Your Business
At Brogen, we specialize in providing customized OEM / ODM lithium-ion battery solutions for electric forklifts. We offer custom-designed lithium battery packs and BMS to replace lead-acid batteries, catering to the specific needs of our customers’ end products.
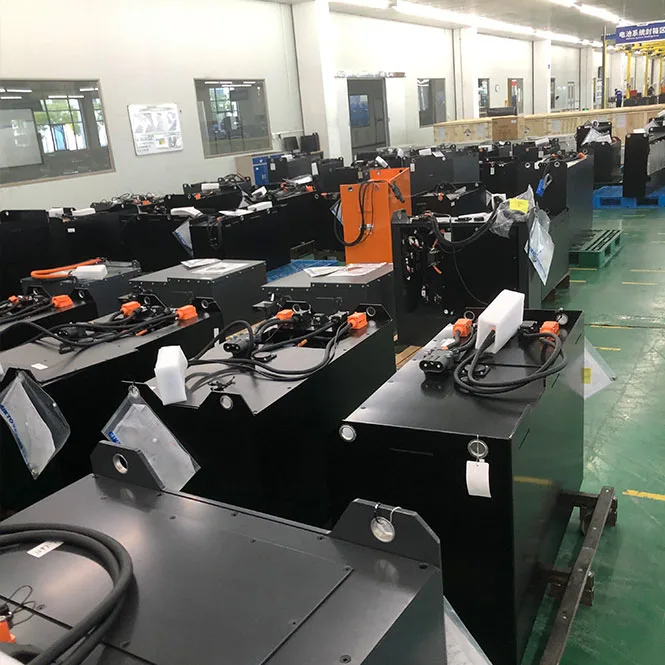
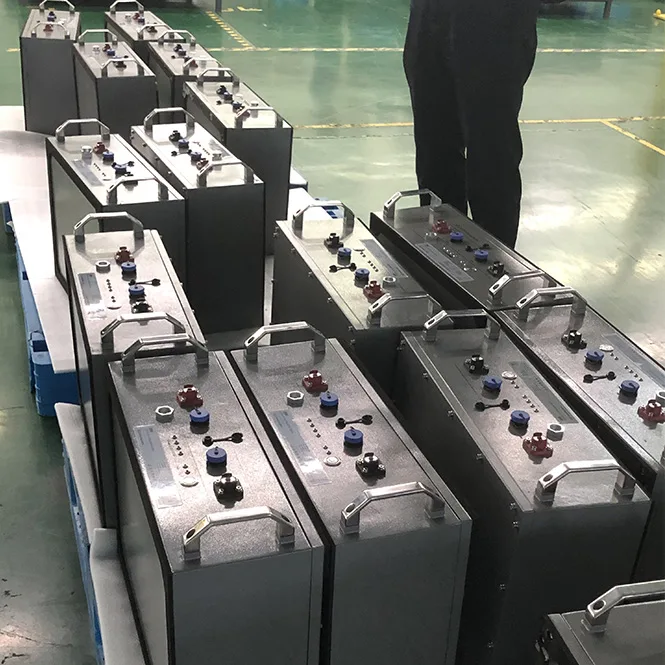
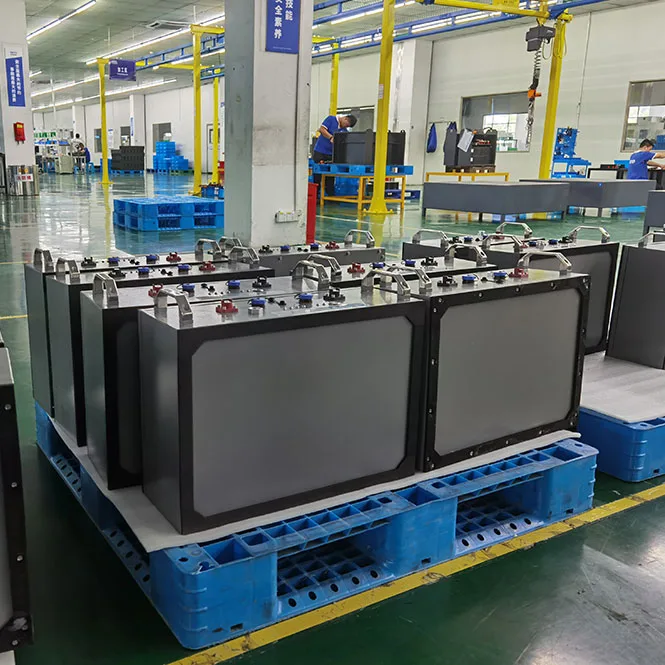
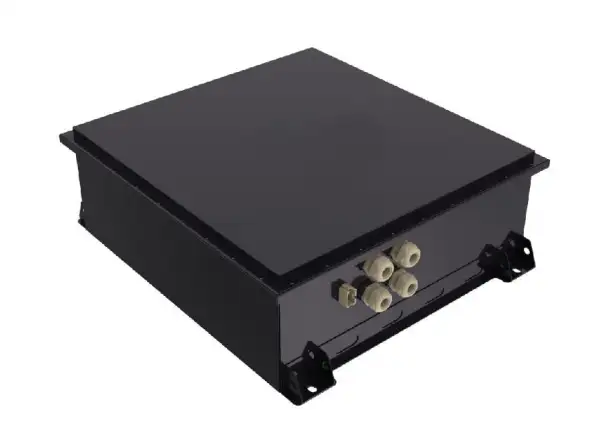
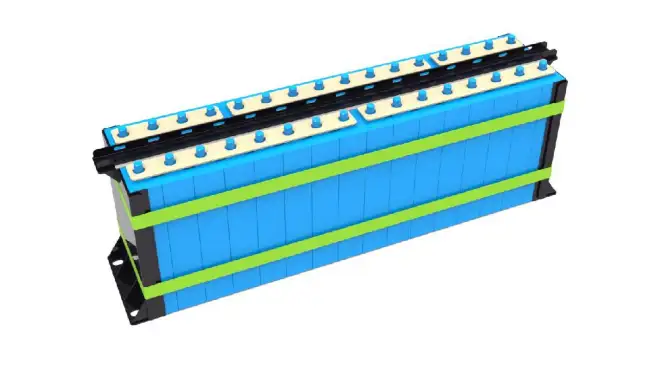
Advanced Design Strategy
- Multi-level battery modeling and simulation technology
- Efficient active and passive balancing technology
- Functional safety and redundancy design
- High system integration technology
- Accurate state estimation technology
Our Strength
Rich Project Experience & Best Features
Our core R&D team members possess extensive experience in lithium battery development. Our electric forklift batteries are manufactured using advanced laser welding technology, ensuring high quality and seamless integration. With a high IP rating, these batteries are designed to perform reliably even in challenging environments. We employ sophisticated CAE simulation and structural optimization to enhance durability and resistance to vibrations and pressure.
We maintain a stable and robust capacity for large-scale production, and our battery products are succesfully exported to countries such as Turkey, Brazil, India, the UAE, etc.
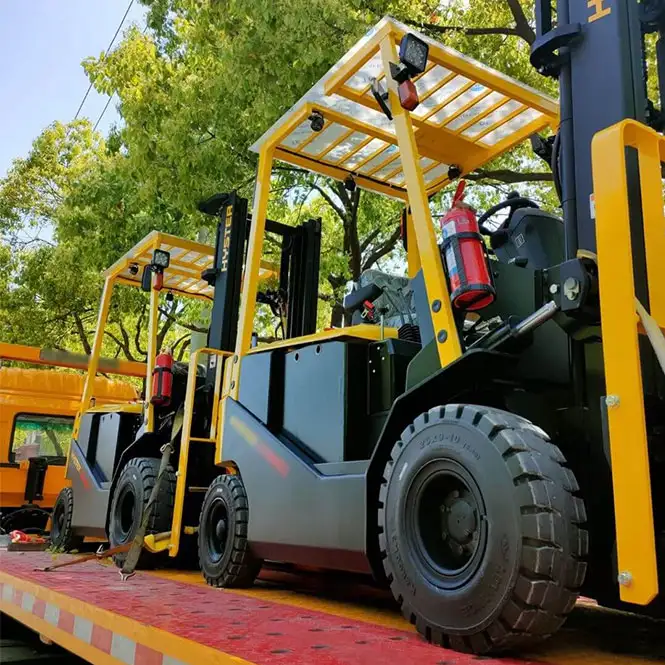
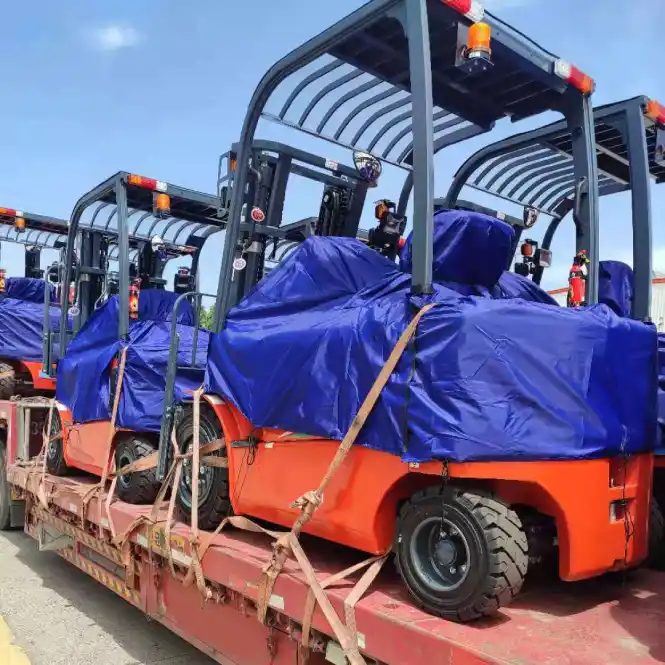
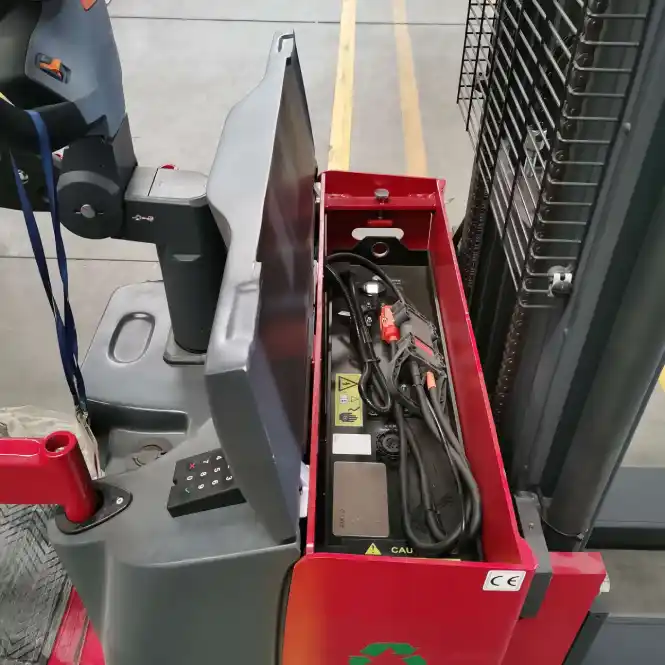
Our Offerings
- 24 V: 105 Ah / 140 Ah / 180 Ah / 190 Ah / 205 Ah
- 48 V: 405 Ah / 450 Ah
- 51.2 V: 105 Ah / 400 Ah
- 76.8 V: 280 Ah / 420 Ah
- 80 V: 315 Ah / 420 Ah
*More options are available upon request.
Example Configurations
- Cell: 105 Ah LFP
- Grouping: 2P8S (6 modules in 1 system)
- System rated voltage: 80 V (24S)
- System capacity: 420 Ah
- System energy: 32.256 kWh
- Voltage: 60 - 87.6 V
- Continuous charge/discharge current: charge 210 A; discharge 420 A (room temperature 25°C)
- Cooling method: natural cooling
- Heating method: PI heating film
- Dimension: 873*628*510 mm
- Cell: 205 Ah LFP
- Grouping: 1P8S
- System rated voltage: 25.6 V (8S)
- System capacity: 205 Ah
- System energy: 5.248 kWh
- Voltage: 20 - 29.2 V
- Continuous charge/discharge current: 200 A (room temperature 25°C)
- Cooling method: natural cooling
- Heating method: PI heating film (optional)
- Dimension: 415*335*235 mm
Discover more of our EV battery solutions here.
Contact Us
Get in touch with us by sending us an email, using the Whatsapp number below, or filling in the form below. We usually reply within 2 business days.