Two Major E-Powertrain Solutions for LCVs
Electric power has become the primary driving force for new energy light trucks. These trucks typically employ two main power layouts: one utilizes a traditional drive motor paired with a gearbox and rear axle, while the other employs a combination of a motor and an electric drive axle.
Initially, many automakers adopted the former approach to capitalize on emerging opportunities driven by policies and market demands. This involved directly modifying the architecture of conventional fuel-powered light trucks to create pure electric models, maintaining consistency with traditional fuel-based layouts.
Developing an entirely new platform for new energy light trucks entails significant investments in manpower and finances, along with lengthy product validation processes. The “gas-to-electric” conversion model streamlines this process by simply replacing the original engine and transmission assembly with a motor and single-stage reducer. This not only reduces development time but also simplifies post-vehicle maintenance, resulting in lower costs. Moreover, the motor + reducer + rear axle combination closely resembles the power structure of diesel vehicles.
The electric drive axle represents a novel technical solution that integrates components like the motor, reducer, and differential, enabling the axle to generate power output. Its major advantages lie in reducing vehicle weight and significantly increasing chassis space due to its high integration, thereby enhancing overall efficiency.
Currently, traditional “gas-to-electric” new energy LCVs remain the preferred choice for EV builders due to their lower procurement and maintenance costs. Although they may be less technologically advanced than electric LCVs utilizing e-axle technology, their minor modifications to traditional power layouts ensure stronger reliability and stability by retaining the original vehicle structure.
Brogen’s Direct Drive System for EV LCVs
At Brogen, we offer both direct drive systems and electric axle systems. For our direct drive motor systems, in addition to single motor + controller systems, we also offer high-speed motor + controller + reducer systems, available in both high voltage and low voltage platforms. MCU, DCDC, Brake DCAC, Steering DCAC, and PDU functions are integrated into the high-voltage controller. Benefits include
- High reliability: our direct drive systems have been matched with renowned domestic OEMs for nearly 8 years, boasting a very low failure rate and passing all DVP tests. They are currently in mass production.
- Good power performance: our direct drive motors are simple, efficient, and responsive, ensuring smooth vehicle operation with no jerking. The medium-speed direct-drive motor, when paired with a speed ratio gear axle, delivers ample total output torque, ensuring excellent climbing ability and acceleration performance.
- Low energy consumption: the system’s maximum efficiency reaches over 95%, with a wide efficient operating range, allowing the motor to work more in the high-efficiency zone, improving the overall efficiency of the system.
- Wide range of applications: suitable for municipal vehicles (street sweepers, garbage trucks, etc.), short-haul trucking, urban delivery, extended-range vehicles, and construction equipment retrofits.
Example Configurations
Motor + Controller
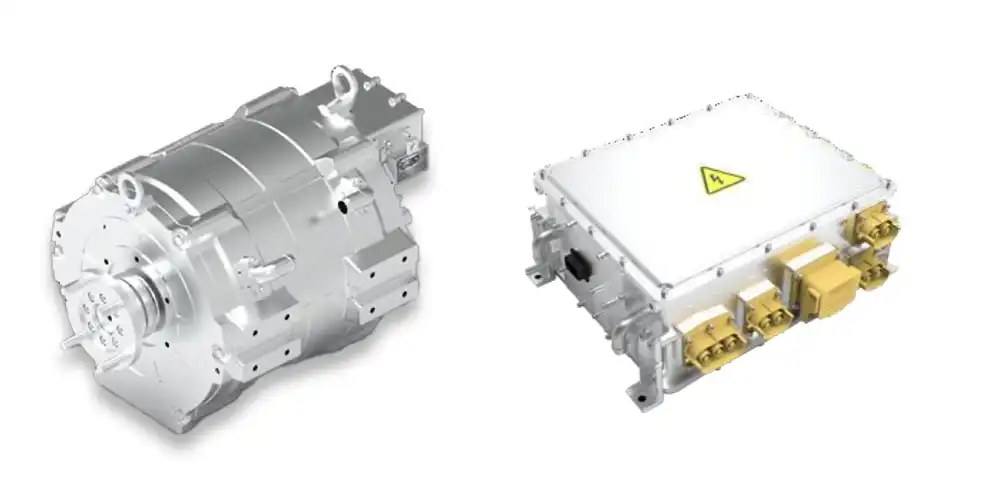
- Motor rated / peak power: 60 / 120 kW
- Motor rated / peak torque: 635 / 1200 N.m
- Motor rated / peak speed: 900 / 3800 rpm
- Motor dimensions: 600*400*380 mm
- Motor weight: 142 kg
- Controller voltage range: 450~750 V
- Controller current module: 600 A
- Controller dimensions: 540*470*220 mm
- Controller weight: 28 kg
- Controller integration: MCU+DCDC+braking DCAC+steering DCAC+PDU
- Applicable models: 6-ton ~ 7.5-ton trucks
Motor + Gearbox + Controller
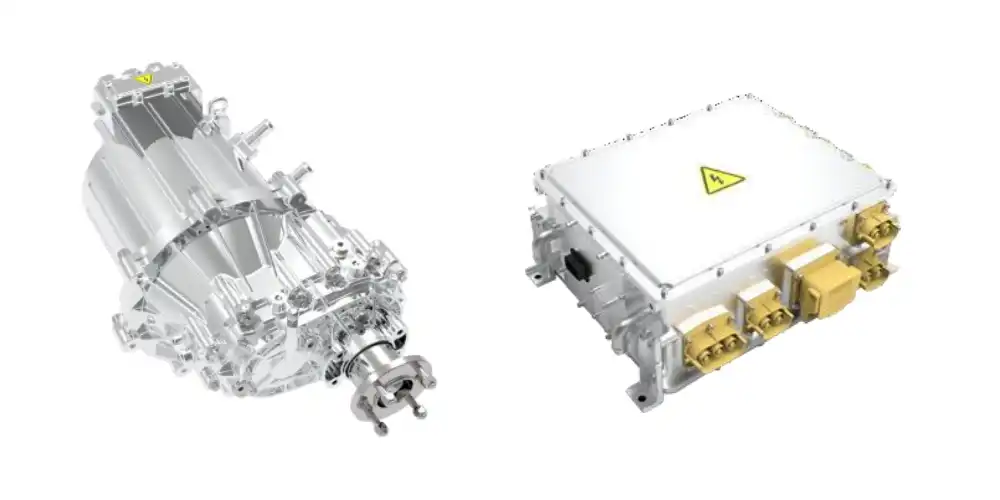
- Motor rated / peak power: 60 / 120 kW
- Motor rated / peak torque: 150 / 350 N.m
- Motor rated / peak speed: 4500 / 12000 rpm
- Reducer speed ratio: 3.04 (SNC)
- Reducer max. input torque: 350 N.m
- Reducer max. input speed: 12000 rpm
- ePowertrain system peak torque: 1050 N.m
- ePowertrain system peak speed: 4000 rpm
- ePowertrain system dimensions: φ368*680 mm
- ePowertrain system weight: <85 kg
- Controller voltage range: 450~750 V
- Controller current module: 450 A
- Controller dimensions: 540*470*220 mm
- Controller weight: 28 kg
- Controller integration: MCU+DCDC+braking DCAC+steering DCAC+PDU
- Applicable models: 4.5-ton ~ 6-ton trucks
More EV Systems for LCVs
Contact
Struggling to find the perfect EV solution for your project? No need to fret! Simply fill out the form below, and we’ll tailor a solution to suit your needs. Alternatively, you can reach out to us directly at contact@brogenevsolution.com. Rest assured, we strive to respond promptly within 2 business days to ensure the seamless progress of your EV program. Let’s work together to make your electric vehicle vision a reality!