Electric Power Recirculating Ball Steering (eRCB) for Commercial Vehicles
As the commercial vehicle industry trends towards electrification, intelligent systems, and connectivity, the power steering systems in commercial vehicles are also moving towards electrification. The evolution of commercial vehicle steering technology has progressed through several stages: from mechanical steering, to hydraulic steering, to electro-hydraulic steering, and now to fully electric steering, such as the electric power recirculating ball steering.

What is the Electric Power Recirculating Ball Steering (eRCB) System?
Unlike traditional mechanical recirculating ball steering systems, the electric power recirculating ball (eRCB) steering system integrates an electric motor and a reduction mechanism at the input end of the mechanical recirculating ball steering gear. This system uses steering signals, vehicle speed signals, and active control commands to control the motor, generating steering torque. This allows for different levels of power assistance and enables active steering functions.
How Does the Electric Power Recirculating Ball Steering Work?
When the steering wheel is turned, a torque sensor sends a torque signal to the controller. This signal is generated by a torsion bar inside the steering shaft, where the ends of the bar twist relative to each other under external force, reflecting the angle of twist to the torque sensor. The steering torque is directly proportional to the torsion bar’s twist angle.
A vehicle speed sensor sends a speed signal (a square wave signal) to the controller. The controller then processes the torque signal and the speed signal from the dashboard and uses a pre-set force model to control the DC motor. By adjusting the current to the motor, the output torque changes, which is amplified by the reduction mechanism to directly assist the steering gear.
What Are the Advantages of Electric Power Recirculating Ball Steering Systems?
Compared to traditional hydraulic power steering, electric power recirculating ball steering offers the following advantages:
1. Reduced Procurement Costs
Traditional hydraulic power steering systems for electric vehicles require an additional electric motor and controller, as there’s no engine-driven hydraulic pump. This setup can cost significantly more than electric steering.
2. Fewer Components and Lighter Weight
Hydraulic steering for electric vehicles requires extra components like hoses, reservoirs, pumps, motors, and controllers. In contrast, electric power steering is an integrated system that saves time and effort during assembly. It’s approximately 50% lighter than hydraulic steering, making it easier to install and maintain, while also enhancing vehicle layout and safety.
3. Extended Driving Range by 25%
Hydraulic steering systems need a motor with at least 2 kW power that runs continuously. In contrast, electric steering only requires a 12V (or 24V) power source, with a bus only needing around a 400W motor. The system only consumes power when steering, leading to minimal energy loss. Tests show that this can extend the driving range by over 25%.
4. Improved Steering Ease and Stability
The eRCB system adjusts the steering assistance based on vehicle speed—light and easy steering at low speeds and stable, secure handling at high speeds, improving vehicle stability and control.
5. No Hydraulic Fluid, No Leaks
- Since the eRCB system doesn’t use hydraulic fluid, it eliminates the risk of leaks and reduces environmental pollution.
6. High Reliability and Maintenance-Free
The eRCB system is highly reliable, maintenance-free, and performs well even in low temperatures.
7. Broad Applicability
The eRCB system is versatile, suitable for fuel-powered vehicles, and hybrid vehicles, and is the ideal choice for pure electric vehicles.
Brogen's eRCB Solutions
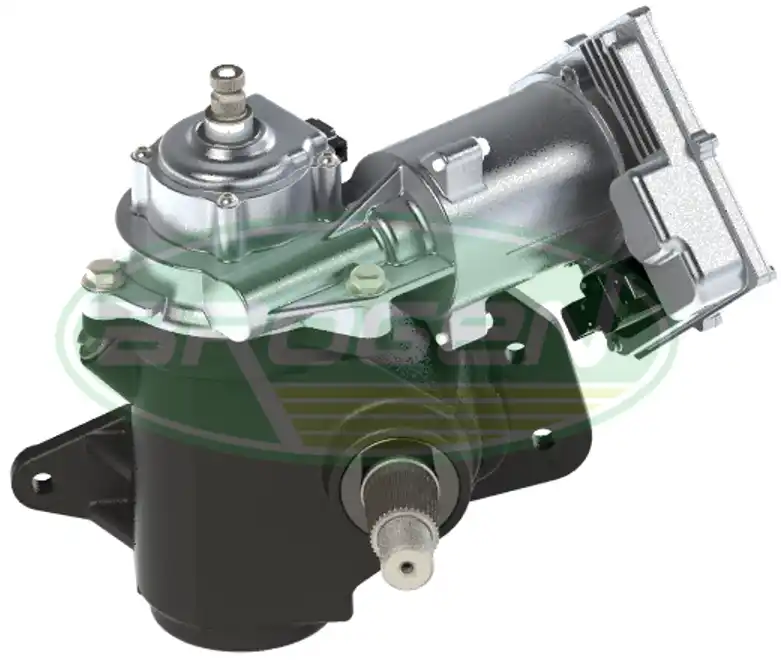
System Functions
- Speed-sensitive power assistance
- Active return
- Dampling compensation function
- Friction compensation function
- Rack end protection function
- Inertia compensation function
- Temperature management
- Motor thermal protection
System Advantages
- Provides eRCB products supporting L2 autonomous driving
- Configurable interfaces, compatible with various TAS sensor types
- Supports CAN/CANFD interface
- Supports Cybersecutiry hardware encryption
- Supports OTA upgrades
Contact Us
Get in touch with us by sending us an email, using the Whatsapp number below, or filling in the form below. We usually reply within 2 business days.
Email: contact@brogenevsolution.com
Respond within 1 business day
Whatsapp: +8619352173376
Business hours: 9 am to 6 pm, GMT+8, Mon. to Fri.
LinkedIn channel
Follow us for regular updates >
YouTube channel
Ev systems introduction & industry insights >