Electric Truck Axle Guide: How to Choose the Right E-Axle for Heavy-Duty Trucks?
As electric heavy-duty trucks continue to gain market share, a clear understanding of key drivetrain systems—especially the electric truck axle—is becoming increasingly important for OEMs and commercial EV developers.
What types of electric truck axles are available today, and what technical factors should be considered when selecting the right solution?
In this article, we explore the core dimensions of electric truck axle selection, including structural layout, motor configuration, transmission stages, and PTO integration. This guide is designed to support engineering and product teams in making informed decisions when developing or sourcing electric heavy truck platforms.

1. The Structure of Electric Truck Axle
Traditionally, a drive axle consists of four main subassemblies.
- Axle Housing: As the core load-bearing structure, the housing plays a critical role in supporting the entire axle system. Depending on the manufacturing process, axle housings can be categorized into three main types:
- Stamped and Welded Steel Plates: Known for their cost-effectiveness and relatively low weight, this method is commonly used in light-duty applications.
- Hydroformed Structures: This process enables superior lightweight performance, making it ideal for applications with strict weight constraints.
- Precision Cast Housings: These offer high structural strength and load-bearing capacity, which is essential for heavy-duty operations and demanding terrains.
- Final Drive (Main Reducer): It converts torque from the driveshaft into torque at the drive wheels. One of the key performance indicators of the final drive is the diameter of its ring gear – the larger the diameter, the greater the vehicle’s load capacity and wheel-end output torque. Additionally, the gear ratio of the final drive is a critical factor affecting the vehicle’s power delivery and energy efficiency. Inside the final drive, there is also a differential, which allows the left and right wheels to rotate at different speeds when the vehicle is running.
- Wheel End: This assembly connects directly to the tires and is responsible for high-speed rotation. In older designs, wheel ends required grease lubrication, which routine maintenance typically needed every 50,000 km. Today, most heavy-duty truck axles have adopted maintenance-free wheel ends, significantly reducing service requirements and improving uptime.
- Braking System: It typically comes in drum or disc configurations. Among drum brakes, there are two common types: S-cam brakes and wedge brakes. Thanks to their simpler structure, faster response, and better space efficiency (especially in tight chassis layouts), wedge-type drum brakes have become the preferred solution in modern heavy-duty trucks.

From a structural standpoint, electric truck axles are fundamentally similar to traditional diesel axle systems. There are tow primary structural configurations commonly used in the industry:
Configuration 1: Integrated Axle Housing Structure
This design retains the conventional layout of the axle housing, wheel hubs, and braking system – essentially mirroring a traditional diesel drive axle. The only major difference is the addition of an electric motor and gearbox assembly, which is mounted at the front flange of the axle. The motor delivers torque, which is then stepped down and amplified by the gearbox before being transmitted to the axle to propel the vehicle forward or in reverse.

The key advantage of this configuration lies in its simplicity. It leverages proven components from diesel truck platforms – including the axle housing, wheel ends, and braking system – which helps reduce development time and keeps costs relatively low.
However, there are notable trade-offs. Due to space limitations, it’s difficult to integrate a multi-speed gearbox – typically restricted to two or three gears at most – and there’s usually no room for a PTO. Another major drawback is that the center of gravity of the entire e-axle assembly is offset from the axle line, which can lead to undesirable dynamic behaviors during rapid acceleration or braking. These include pitching motions such as axle lift (front-up) during acceleration and nosedive during deceleration.
Configuration 2: Three-Piece Axle Housing Structure

This design features square-section axle housings on both sides, with the electric motor and multi-speed gearbox mounted in the center. The three segments are connected via flanges and bolts.
The main advantage of this architecture is its compact layout, which allows the gearbox to be designed with 3, 4, or even 6 speeds. This enables improved vehicle performance and energy efficiency, particularly under varying load and terrain conditions.
The primary drawback is the increased overall weight due to the bolted flange connections between the three sections. However, the structural integrity of this design is not compromised – the axle can support up to 13 tons, making it fully suitable for heavy-duty applications.

From a cost perspective, Configuration 1 is more economical and is currently more common in the market. However, from a technological and performance standpoint, the three-piece structure – with its modular layout and support for multi-speed transmissions – is emerging as the mainstream trend in electric axle development for heavy-duty trucks.
2. Choosing the Number of Motors
Due to space constraints, electric truck axles typically integrate a single motor. For example, our latest e-axle features a single motor delivering 300 kW peak power (407 hp) and 200 kW rated power (271 hp). It utilizes an oil-cooled system and achieves a maximum output torque of 38,483 Nm. With its integrated axle housing design, it supports a maximum axle load of up to 16,000 kg.

To further increase power output, dual-motor configurations are required. These can be arranged in two main ways:
- Inline configuration: Two motors positioned front and rear, jointly driving the central final drive.
- Distributed design: Similar to the layout in the Tesla Semi, where the second axle is used as the drive axle. It employs two motors, each driving one half-shaft independently, using an electronic differential system (EDS). This setup calculates the optimal wheel speed on each side of the axle based on steering input, eliminating the need for a mechanical final drive.

Dual-motor systems offer enhanced flexibility and energy optimization. For instance, during vehicle launch, rapid acceleration, or heavy-load hill climbing, both motors operate simultaneously to deliver maximum torque. During steady-state cruising, only one motor runs near its optimal efficiency point, while the other motor shuts down to reduce energy consumption – improving overall economy.
The decision between a single-motor and dual-motor e-axle should be based on real-world operating conditions. For applications in flat regions, a single-motor setup is generally sufficient. For operations in mountainous terrain, dual motors are recommended for better torque delivery and drivability.
3. Number of Transmission Gears
In theory, the more gears a transmission has, the wider its gear ratio spread – from a larger reduction in the first gear to a lower ratio in top gear – resulting in improved vehicle performance and energy efficiency across a variety of operating conditions.
For centralized drive systems in electric heavy-duty trucks, the transmission is typically mounted in the center of the chassis. This offers sufficient space in both lateral and longitudinal directions to support multi-speed gearbox designs. For instance, a European OEM’s diesel-to-electric conversion model directly retains the 12-speed gearbox from the original ICE platform. However, given that electric motors have a much wider and flatter torque curve than diesel engines, a 12-speed transmission often provides more complexity than necessary. In most EV use cases, a 6-speed gearbox is sufficient to handle demanding road and load conditions.
For e-axles with an integrated axle housing structure, space is limited – gearboxes are typically limited to 2-speed designs. In contrast, for three-piece axle housings, where the transmission is positioned in the center section, it becomes feasible to design 3-, 4-, or even 6-speed gearboxes.
Take, for example, our recently launched electric drive axle. Its 4-speed gearbox features gear ratios of 71.0, 36.3, 20.0, and 10.2, enabling a maximum output torque of 45000 N.m at the wheel end.

Recommended configurations based on terrain:
- For flat regions, a 2-speed transmission is cost-effective and offers high reliability.
- For hilly regions, a 3-speed transmission provides better adaptability and balance.
- For mountainous regions, a 4-speed transmission is recommended to ensure sufficient torque under demanding gradients.
4. PTO Design

Many early-generation electric drive axles did not include a PTO interface due to space constraints. These models are typically suitable for applications such as parcel delivery, LTL freight, and urban logistics. However, in China’s current market, electric heavy-duty trucks are primarily used in resource-based transportation – such as coal, aggregates, and ores – where the trailers are often side-tipping or rear-tipping dump types that require hydraulic power driven by a PTO.
In some cases, where the e-axle lacks a PTO, OEMs are forced to install an auxiliary electric motor behind the cab to power the hydraulic pump. This setup is clearly suboptimal – the auxiliary motor is inactive during normal driving, acting as dead weight, increasing both the vehicle’s overall weight and cost.

Recommendation: When specifying an electric drive axle, it is strongly advised to choose a model with a built-in PTO, even if the initial use case (e.g., parcel delivery or express freight) does not require one. This future-proofs the vehicle’s second-life value, as most used electric trucks are eventually resold into resource-based operations—where a PTO is almost always required.
Brogen Electric Truck Axle Solutions for Heavy Commercial Vehicles
At Brogen, we provide a wide selection of electric truck axles engineered for heavy-duty commercial vehicles such as tractors, semi-trucks, trailers, tippers, mining trucks, water tankers, garbage trucks, and more. These eAxle solutions are built on different technical architectures – such as integrated or distributed designs – to match the specific demands of various vehicle platforms and operating conditions. Whether it’s high torque for off-road mining or energy efficiency for urban logistics, we tailor the technology to deliver optimal performance for every application.
1. Single Motor Electric Truck Axle With Integrated Axle Housing
Model | OEEA60 | OEEA85 | OEEA95 | OEEA100 | OESTEA40000Z-1.5 | OESTEA40000Z-1.6 |
Rated axle load capacity | 6000 kg | 8500 kg | 9500 kg | 10000 kg | 13000 kg | 13000 kg |
Speed ratio | 16.473 | 20.475 | 19.22 | 55.2/17.24 | 13.2/4.4 | 13.2/4.4 |
Motor rated/peak power | 100/200 kW | 80/160 kW | 200/320 kW | 200/320 kW | 121/250 kW | 135/290 kW |
Motor rated/peak torque | 220/426 N.m | 200/450 N.m | 350/750 N.m | 350/750 N.m | 320/850 N.m | 326/860 N.m |
Motor peak speed | 12000 rpm | 12000 rpm | 12000 rpm | 12000 rpm | 10000 rpm | 10000 rpm |
Weight | 382 kg | 525 kg | 710 kg | 876 kg | 1030 kg | 1030 kg |
Brake type | Pneumatic disc type | Pneumatic disc type | Pneumatic disc type | Pneumatic drum type | Drum brake | Drum brake |
2. Dual Motor Electric Truck Axle With Integrated Axle Housing
Model | OEEA5000N-1 | OEEA5000N-2 |
Cooling Method | Liquid-Cooled | Oil-Cooled |
Rated axle load capacity | 11500/13000/16000 kg | |
Maximum output torque | 2×27262 N.m | 2×22397~25740 N.m |
Motor rated/peak power | 2×80/180 kW | 2×200/300 kW |
Maximum wheel speed | 615 rpm | |
Brake type | Air disc/drum brakes | |
Gear ratio | 61.955/19.18 | |
Weight | 856~950 kg (depending on the configuration) | |
Rated voltage | 600 VDC | 600/800 VDC |
Suspension type | Air suspension / Leaf spring | |
PTO | Optional integrated PTO |
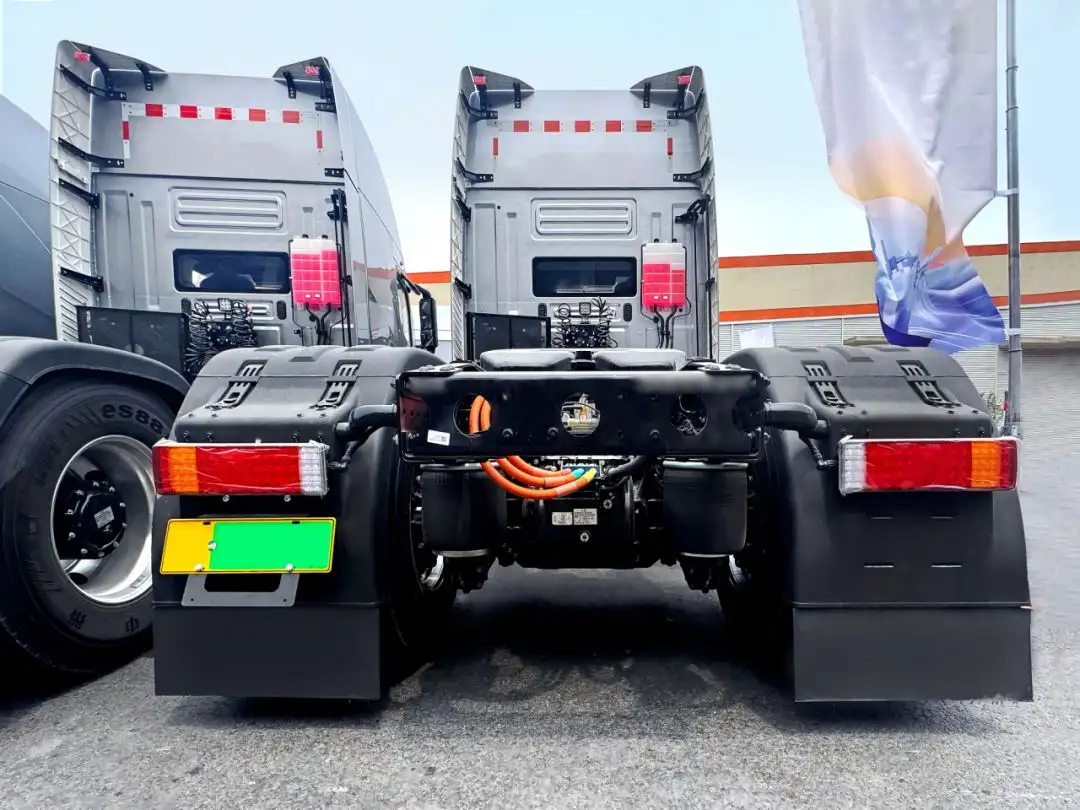
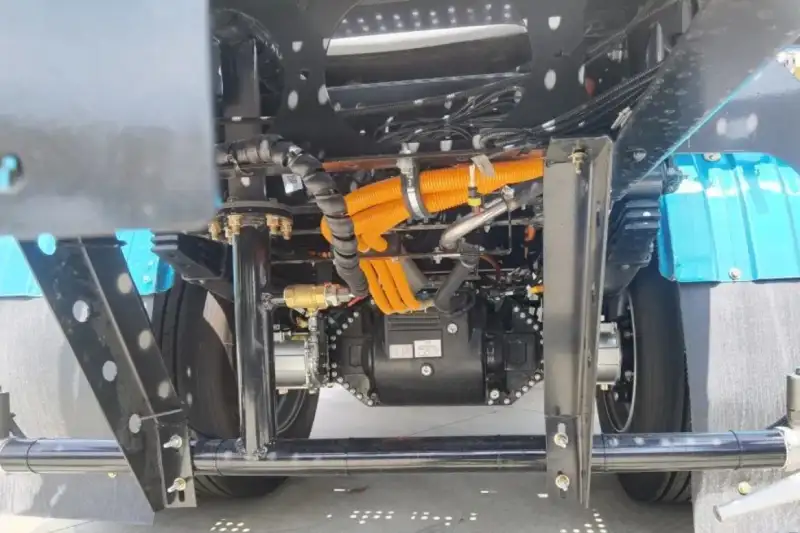
It’s worth noting that our electric truck axles are already in mass production and have been widely deployed by leading OEMs across the globe, including in China, the United Arab Emirates, the United States, Canada, Australia, Brazil, and other key markets.
- Discover our Electric Truck Axle Solutions here: https://brogenevsolution.com/electric-axle-for-truck/
About Brogen
At Brogen, we provide advanced EV solutions for global commercial vehicle manufacturers, enabling them to streamline research and development while capitalizing on cutting-edge technology. Our offerings ensure superior efficiency, extended range, and seamless system integration with proven reliability—empowering our partners to lead in the rapidly evolving green mobility landscape.
Currently, our EV solutions for battery electric heavy trucks have been adopted by vehicle manufacturers in countries and regions such as Canada, Türkiye, Brazil, the Philippines, Indonesia, the Middle East, and more.
- Discover our HCV electrification solution here: https://brogenevsolution.com/heavy-duty-vehicle-electrification-solutions/
- Discover our Public Transport Electrification solution here: https://brogenevsolution.com/public-transport-electrification-solutions/
- Looking for an EV solution for your project? Reach out to us at contact@brogenevsolution.com
Contact Us
Get in touch with us by sending us an email, using the Whatsapp number below, or filling in the form below. We usually reply within 2 business days.
Email: contact@brogenevsolution.com
Respond within 1 business day
Whatsapp: +8619352173376
Business hours: 9 am to 6 pm, GMT+8, Mon. to Fri.
LinkedIn channel
Follow us for regular updates >
YouTube channel
Ev systems introduction & industry insights >