How an e-Axle with Independent Suspension is Shaping the Future of Electric Bus Design?
As the world shifts toward sustainable transportation, the demand for energy-efficient, high-performance solutions in electric buses and other Zero Emission Buses (ZEBs) is steadily increasing. One of the key innovations at the forefront of this transformation is the wheel-side e-axle with independent suspension system for public transportation electrification. This solution is reshaping the way we think about electric bus powertrains, improving overall passenger experience, and enhancing operational efficiency.
The Next Level of Efficiency: Wheel-Side Distributed Drive E-Axle With Independent Suspension
The wheel-side distributed drive e-axle with independent suspension system is designed to offer a lighter, more efficient, and more compact solution for EV buses. This technology effectively reduces vehicle weight and energy consumption. The result? More spacious interior, greater energy savings, and increased passenger capacity flexibility.
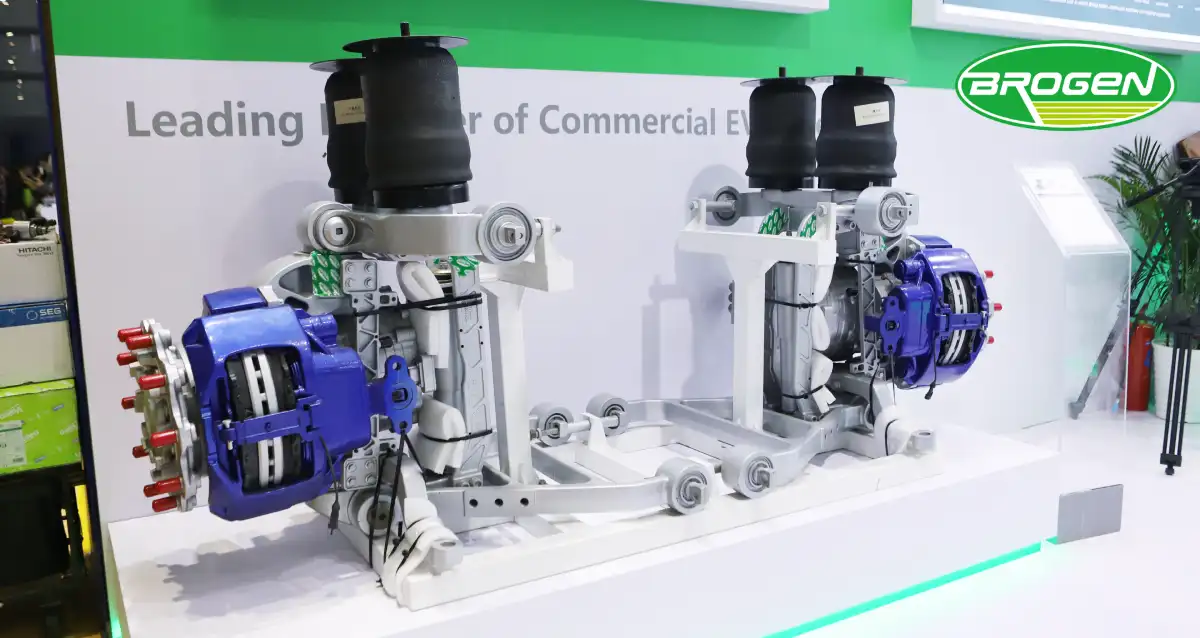
What sets this system apart is its unique design: the left and right wheel-side motors replace the traditional differential and gearbox, applying torque directly to the wheels. This not only simplifies the drivetrain but also minimizes energy loss, making the electric bus more efficient. The integration of high-speed motors and reducers ensures that the system delivers large torque in a small form factor, enhancing the vehicle’s power output.
The wheel-side drive e-axle and its controller operate based on the same principles as the motor and controller systems used in other pure electric or hybrid buses. However, the key challenge in wheel-side distributed drive control for buses lies in achieving the differential speed function between the drive e-axles. As a result, the control strategy and functionality of wheel-side drive e-axles differ from those in other battery electric or hybrid buses.
1.1 Three Configurations of the ePowertrain System for Electric Buses
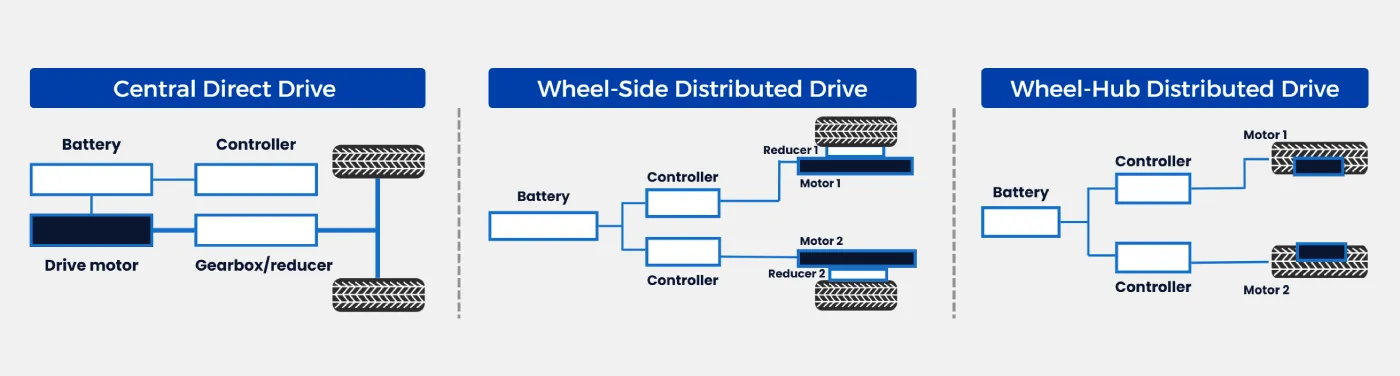
The distributed wheel-side e-Axle solution eliminates the need for a differential, half-shaft, and shortens the transmission chain. This results in higher transmission efficiency, a lighter vehicle, and reduced energy consumption. The compact motor size and wide central aisle make it suitable for low-floor layouts. Before in-hub motor technology become fully mature, wheel-side distributed drive e-axles remain the best matching solution for electric buses.
1.2 Basic Structure of the Wheel-Side Distributed Drive e-Axle with Independent Suspension
- Independent Suspension System: Featuring a four-airbag double wishbone design, this system offers reduced unsprung mass, resulting in a smoother ride with improved comfort and stability.
- Dual Wheel-Side Motors: With high torque and power density, the dual motors provide a strong and reliable output.
- Reducer: Reduces the motor output power to increase torque.
- Motor Controller: Controls the motor to operate at the desired speed, angle, direction, and response time.
- Electronic Components: Includes accelerator pedal sensors, brake pedal sensors, Hall-effect wheel speed sensors, Hall-effect steering angle sensors, roll angle sensors, yaw rate sensors, and controller hardware.
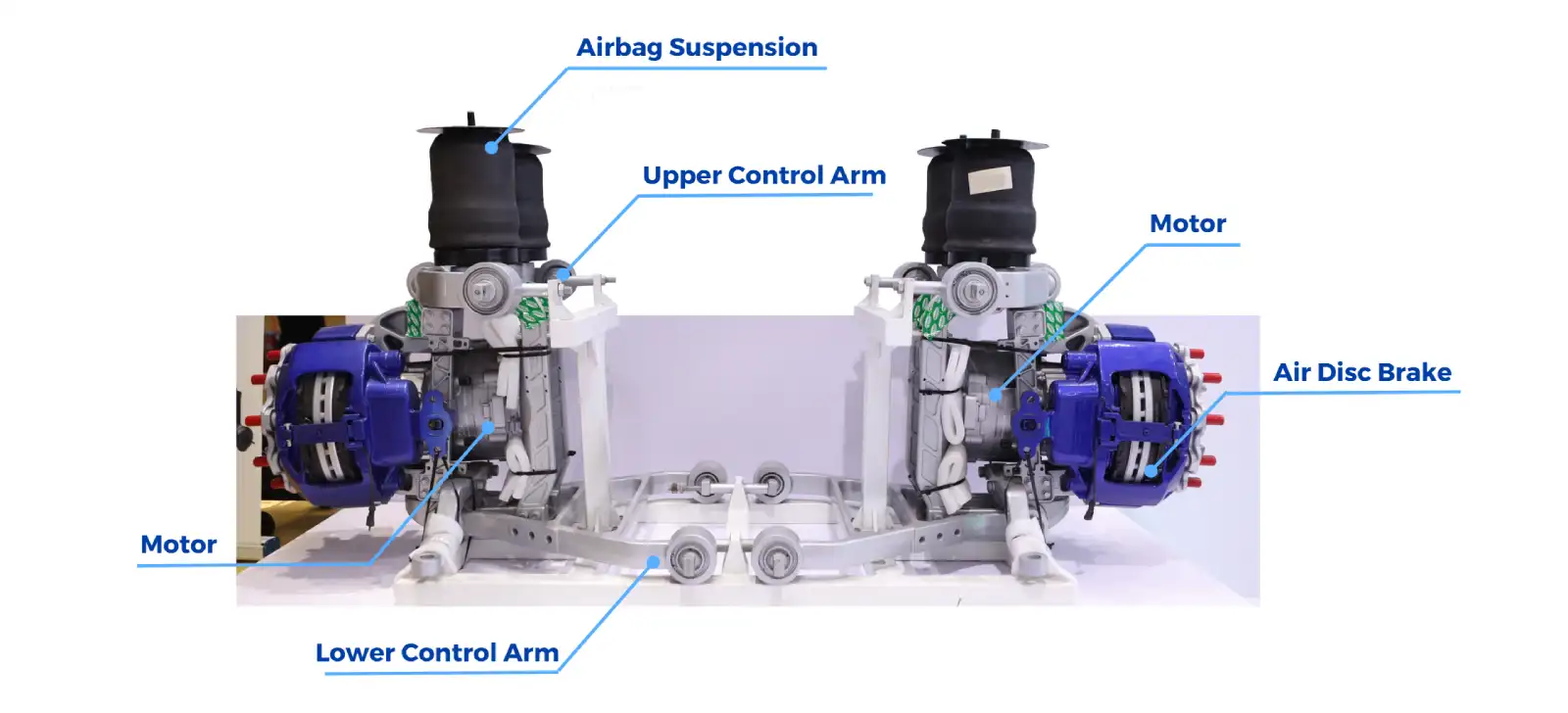
1.3 Working Principles of the Wheel-Side Distributed Drive e-Axle with Independent Suspension
At the heart of the wheel-side distributed drive e-axle system is the Vehicle Control Unit (VCU), which calculates the total torque demand based on the driver’s acceleration or deceleration intent. The electronic differential system allocates the total torque between the left and right drive motors based on the steering angle. vehicle posture sensors, and road surface traction coefficients. The left and right motor controllers, upon receiving the instructions, convert the energy from the battery to the necessary power for the drive emotors, ensuring the vehicle’s stability and handling.
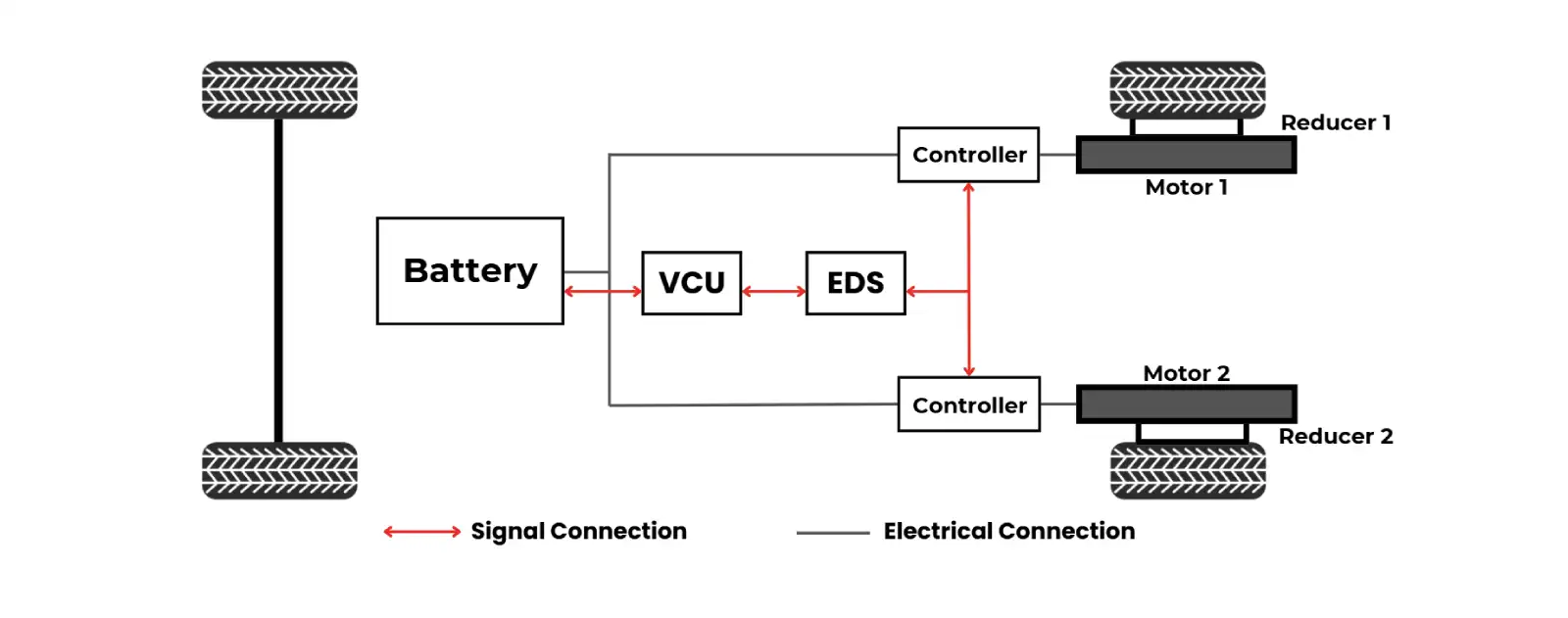
1.4 Operating Modes of the Wheel-Side Distributed Drive e-Axle with Independent Suspension
- Driving Mode: The battery supplies energy to the drive motor through the motor controller, which then directly drives the wheels.
- Regenerative Braking Mode: The rolling wheels drive the motor (regenerative generation) to charge the battery (energy recovery).
Applications of the Distributed Drive e-Axle With Independent Suspension on Electric Buses
The wheel-side e-axle with 4-airbag independent suspension system is not just about technological innovation; it’s about transforming the way we experience and operate electric buses in urban environments. The system offers several key advantages:
- Increased Safety: With a low-floor layout, passengers, including the elderly, children, and people with disabilities, can easily board and disembark. The design also reduces the risk of accidents caused by falls on traditional steps, offering a safer and more inclusive experience for all.
- Enhanced Comfort: The independent suspension system significantly improves ride quality, with reduced vibration and a smoother overall journey.
- Improved Operational Efficiency: For an 8.8-meter electric bus, the weight of the e-powertrain system can be reduced by more than 700 kg; for a 10-meter electric bus, the weight of the e-powertrain system can be reduced by more than 800 kg, offering significant energy savings, improved range, and lower maintenance costs.
Real-World Impact: Proven Performance
The independent suspension e-axle has already been deployed successfully on electric buses in several countries. Statistics show that after one year of use of a city’s 200 units of electric buses, the passenger injury accident rate has dropped by about 70%, largely due to the elimination of high-step entryways and the vehicle’s stable ride quality. These buses are proving to be a safer, more efficient, and comfortable choice for city transportation.
Advantages of our Electric Bus Powertrain Solution
The wheel-side distributed drive electric axle system is a leading-edge solution for electric buses, offering a future-proof EV technology that enables operators to meet sustainability goals while improving passenger experience and operational performance. As the global market for electric buses expands, this innovation is paving the way for more sustainable, energy-efficient public transit systems in cities across the globe.
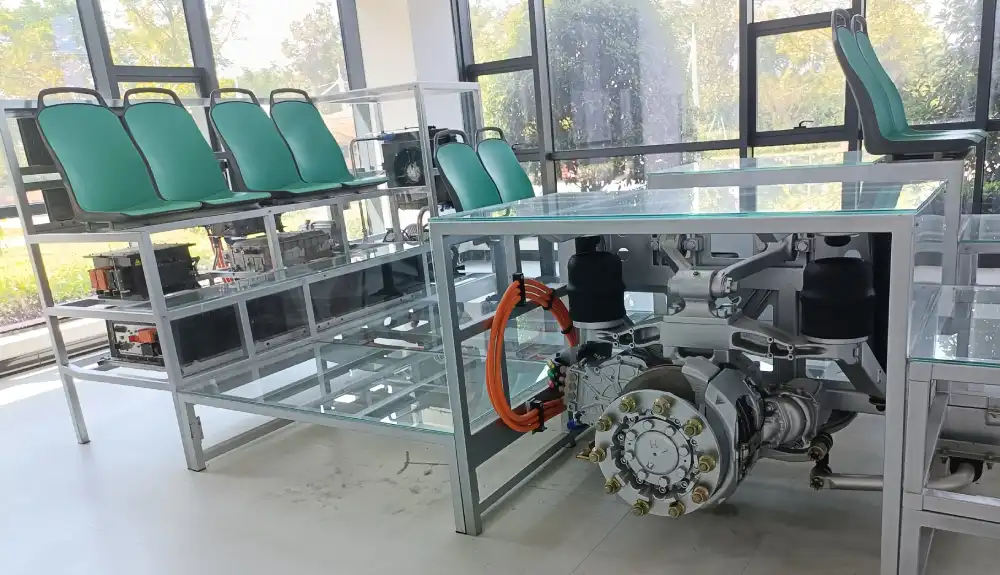
Optimized Interior Space – Enables an 800 mm wide aisle and a fully flat low-floor design for enhanced accessibility and passenger comfort.
Enhanced Maneuverability & Safety – Integrated steering function allows the rear wheels to track the front wheels, significantly reducing right-turn accidents caused by wheel differences.
Proven Reliability – Features a mature and dependable electronic differential system, with tire replacement mileage exceeding 100,000 km.
Technical Parameters
Item | Parameters |
Motor type | PMSM |
Motor power | 2×55 kW / 2×90 kW |
Maximum motor speed | 9500 rpm |
Motor torque | 2×140 N.m / 2×350 N.m |
Rated voltage | 600 VDC |
IP | IP68 |
Axle weight | 850 kg |
Rated axle load | 9000 kg |
Maximum wheel speed | 540 rpm |
Gear ratio | 17.55 |
Brake | Air disc brake |
Maximum steering angle | ±18° |
Discover our distributed drive e-axle solutions for buses here: https://brogenevsolution.com/distributed-electric-drive-axle-for-bus/
Business inquiry: contact@brogenevsolution.com or contact us through the table below.
Contact Us
Get in touch with us by sending us an email, using the Whatsapp number below, or filling in the form below. We usually reply within 2 business days.
Email: contact@brogenevsolution.com
Respond within 1 business day
Whatsapp: +8619352173376
Business hours: 9 am to 6 pm, GMT+8, Mon. to Fri.
LinkedIn channel
Follow us for regular updates >
YouTube channel
Ev systems introduction & industry insights >