Public Transport Electrification Solutions

As cities pursue cleaner and more efficient mobility, public transport electrification is rapidly gaining momentum worldwide. Electric vehicles significantly reduce emissions, noise, and operating costs, establishing themselves as the premier choice for sustainable urban transit. Their lower energy consumption and minimal maintenance requirements deliver long-term savings while enhancing passenger comfort.
At Brogen, we provide advanced EV solutions for global bus manufacturers, enabling them to streamline research and development while capitalizing on cutting-edge technology. Our offerings ensure superior efficiency, extended range, and seamless system integration with proven reliability—empowering our partners to lead in the rapidly evolving public transport landscape.
Email: contact@brogenevsolution.com
Why Choose Brogen
Our Public Transport Electrification Solution Advantages
Bus/Coach
Van
Train
Tram
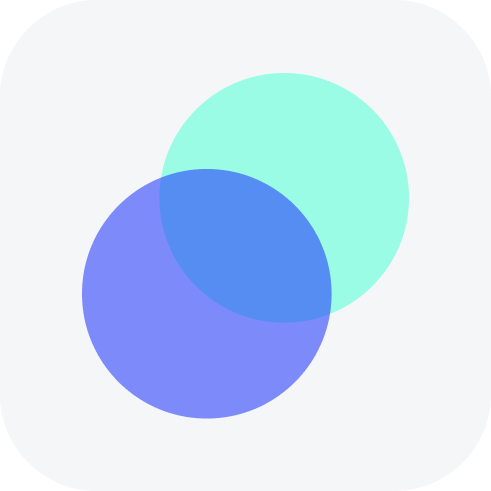
Lightweight Design
Our EV solutions for public transport are engineered with a lightweight approach, reducing energy consumption while improving vehicle dynamics, safety, and passenger capacity, enabling end clients to enhance operational efficiency.
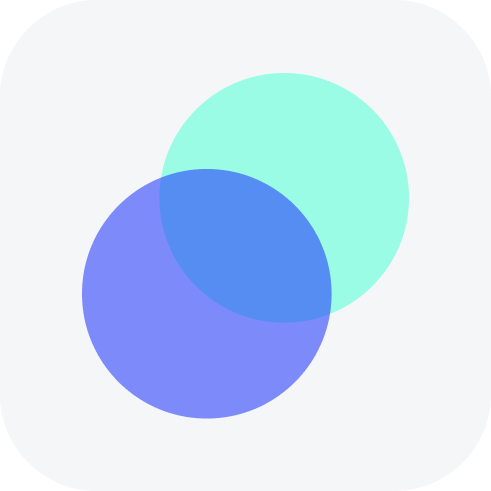
Proven Safety & Reliability
Our EV systems undergo rigorous testing and have been deployed in mass-production buses from leading OEMs. With real-world validation, they deliver exceptional safety, reliability, and compliance with industry standards.
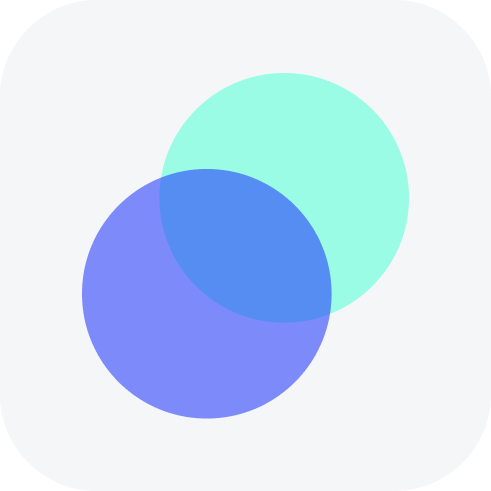
Advanced Technology
We integrate advanced EV technologies. By combining state-of-the-art hardware and intelligent software, we empower OEMs to develop high-performance, future-ready electric buses that stand out in the market.
What We Offer
Our Public Transport Electrification Solutions
Electric Powertrain
We offer a wide range of electric powertrain solutions for public transport vehicles, tailored to meet diverse technical requirements. Our offerings include central direct drive solutions, centralized electric drive axle solutions, and distributed drive solutions. Leveraging high-performance PMSM motors with superior power density, compact dimensions, and low operating noise, our EV systems enhance vehicle integration efficiency. Additionally, based on customer and project needs, we provide either standalone MCUs or integrated multifunction controllers.
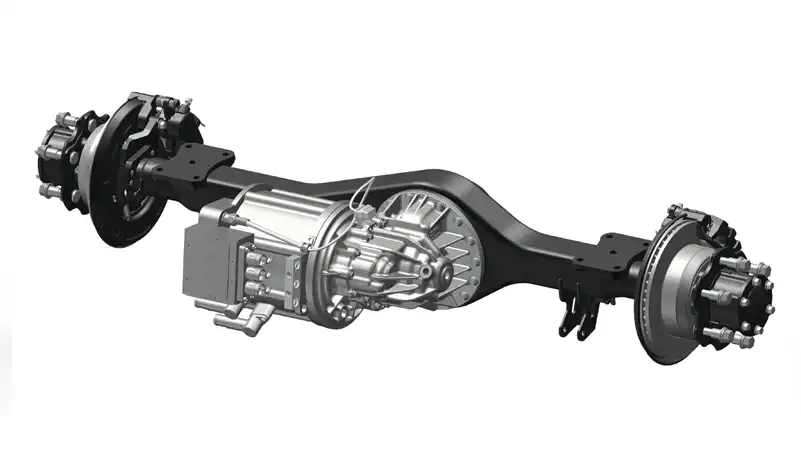
The electric drive axle is a highly integrated e-powertrain system that embeds electric motors directly into the axle. By eliminating traditional transmission components like the drive shaft, this solution significantly boosts energy efficiency and reduces mechanical complexity. For public transport vehicles, its compact design enables a fully flat, low-floor configuration, which maximizes interior passenger space and enhances ride comfort.
Parallel-Axis eAxle Configuration
Parallel-Axis eAxle Configuration
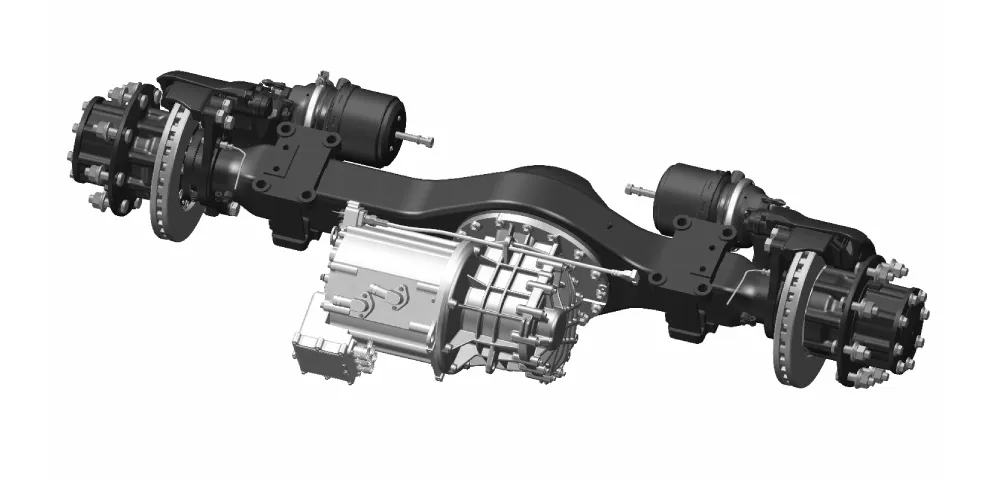
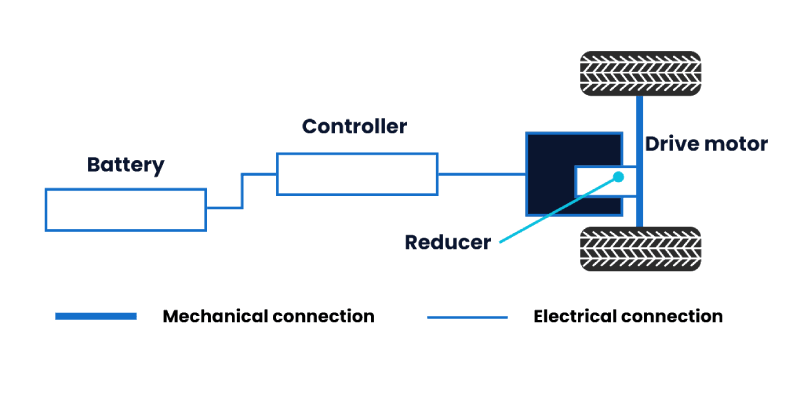
Solution Features
Compact Design
The motor, gearbox, and axle utilize a highly integrated parallel-axis design, resulting in a lightweight system with high transmission efficiency.
Improved NVH Performance
The gearbox is engineered for all operating conditions, featuring in-house manufactured DIN 4-grade high-precision gears, ensuring low noise levels.
Flexible Vehicle Layout
By eliminating the driveshaft, the chassis provides additional space for battery placement, allowing for a more flexible vehicle layout.
Advanced Technology
- High load-bearing capacity with reduced weight, minimizing the risk of oil leakage.
- Integrated gear housing design reduces oil leakage risks, while the smooth curved internal surface minimizes oil churn losses.
- High-precision two-stage helical cylindrical gear transmission with double-sided precision grinding for superior efficiency, lower noise, and extended lifespan.
- Reduced motor offset relative to the axle housing decreases the risk of oil leakage at the reducer joint.
Co-Axial eAxle Configuration
Co-Axial eAxle Configuration
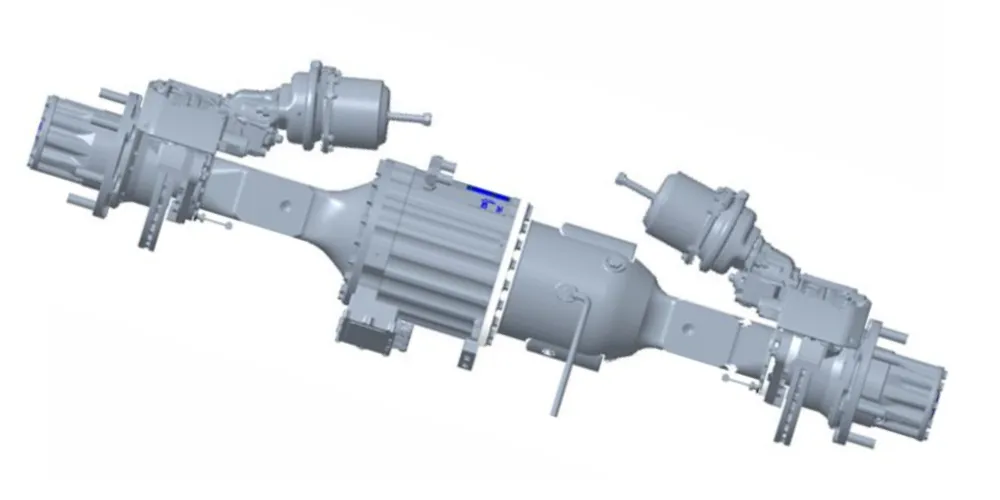
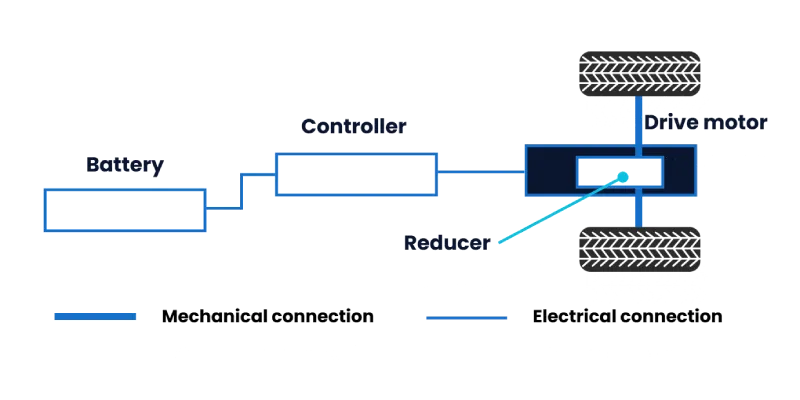
Solution Features
Compact Design
Both the electric motor and output shaft are aligned along the same axis, allowing for a more compact, stable, and efficient design, helping improve overall layout.
Improved NVH Performance
Superior NVH performance, with reduced center-of-gravity offset and less vibration thanks to the improved rotational stability.
Enhanced System Efficiency
Increased system efficiency due to the elimination of high-speed bearings and a more direct power transfer.
Advanced Technology
- Industry-leading integration technology with the most compact chassis footprint and the lightest weight in its class.
- Symmetrical motor layout ensures balanced unsprung mass distribution, minimizing impact on suspension load conditions.
- High-precision helical gear transmission for reduced weight, high efficiency, low noise, and extended lifespan.
- High-strength cast axle housing with a smooth curved inner cavity to reduce oil churning losses.
Distributed Drive eAxle Configuration
Distributed Drive eAxle Configuration
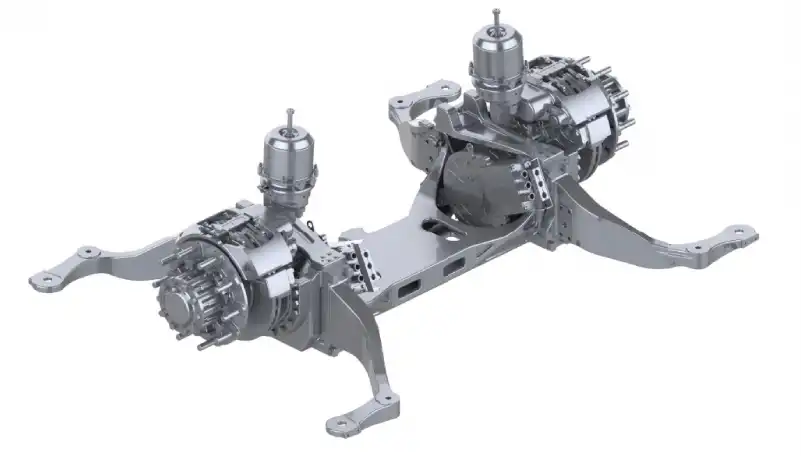
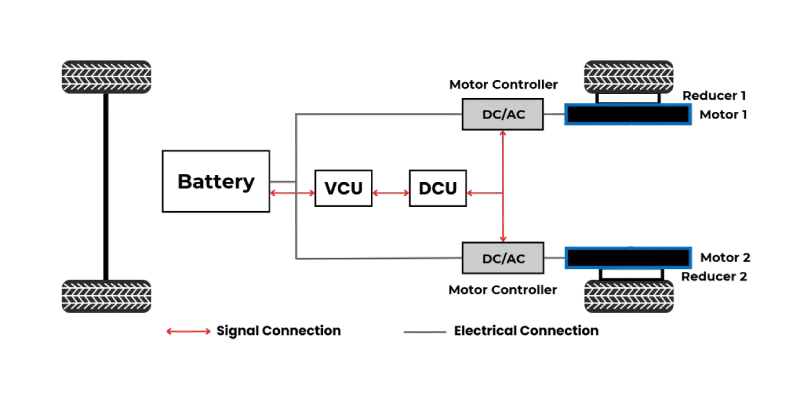
Solution Features
Short Transmission Chain
The distributed drive eAxle solution ensures each motor drives one wheel, significnatly shortening the transmission chain, minimizing transmission loss and maximizing efficiency..
Compact Structure
The distributed drive axle systems save space and contribute to a more compact vehicle structure. It's about 200 kg lighter than the central direct drive system.
Improved Tire Grip Distribution
The distributed eAxle enables individual adjustment of motor torque, optimizing the grip distribution, enhancing vehicle handling and driving stability, providing a safter and more controlled driving experience.
Enhanced Drive Efficiency
Aligning the motor's optimal efficiency range with the vehicle's operate at peak performance.
Advanced Technology
- Integrating two electric motors with the axle for strong power and additional safety redundancy.
- Equipped with EDS, EASR, IESS, and other safety configurations to increase vehicle safety and stability in harsh environments.
- The integrated design of the electric bus axle lowers the gravity center of the battery system, increasing the stability of the whole vehicle.
- Distributed drive approach adds additional safety redundancy to the vehicle, offering a flexible power distribution strategy for different working conditions.

We provide central direct drive solutions for public transport vehicles, offering multiple configurations, including standalone electric motors and 2-in-1 e-powertrain systems integrating the motor with the controller. Designed for simplicity and reliability, these solutions are well-established and widely adopted across the industry. Achieving dual 90% efficiency benchmarks, our technology enhances green transportation and sustainability development, reinforcing our commitment to environmental stewardship.
Direct Drive Motor
Central Direct Drive Motor
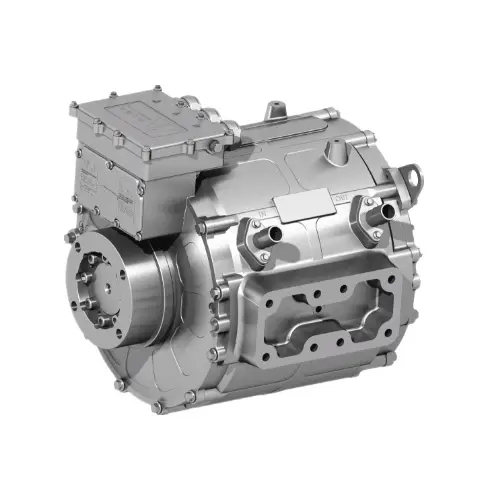
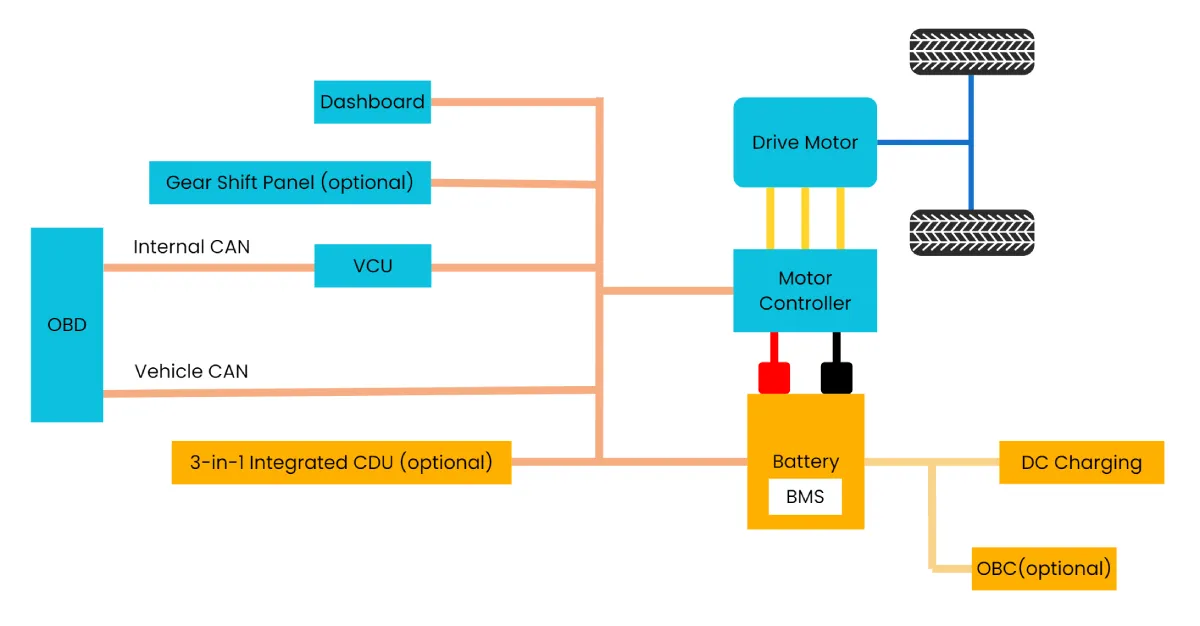
Solution Features
High Efficiency
Achieve peak efficiency exceeding 97%. More than 90% of the system operates within an efficiency range of ≥85%, significantly enhancing energy utilization.
Noise Reduction
The no-load noise level across the full speed range ramains below 72 dB, providing a distinct competitive advantage in the industry.
Mature Applications
Our direct drive solutions have been widely deployed in electric buses worldwide, demonstrating proven reliability in real-world operations.
Advanced Technology
- Utilizes advanced designs such as thin silicon steel laminations, high magnetic permeability materials, and sinusoidal air-gap flux density optimization.
- Features rotor segmented skewing and optimized auxiliary slot parameters at the rotor's outer edge, effectively reducing motor noise.
- Incorporates a dual-helical water channel design to enhance heat dissipation and stability while maintaining optimal water resistance and pressure differential.
- Equipped with a flange dustproof structure to prevent mud, sand, and wastewater from entering the motor, improving long-term reliability.
Integrated Motor + Controller
Integrated Motor + Controller
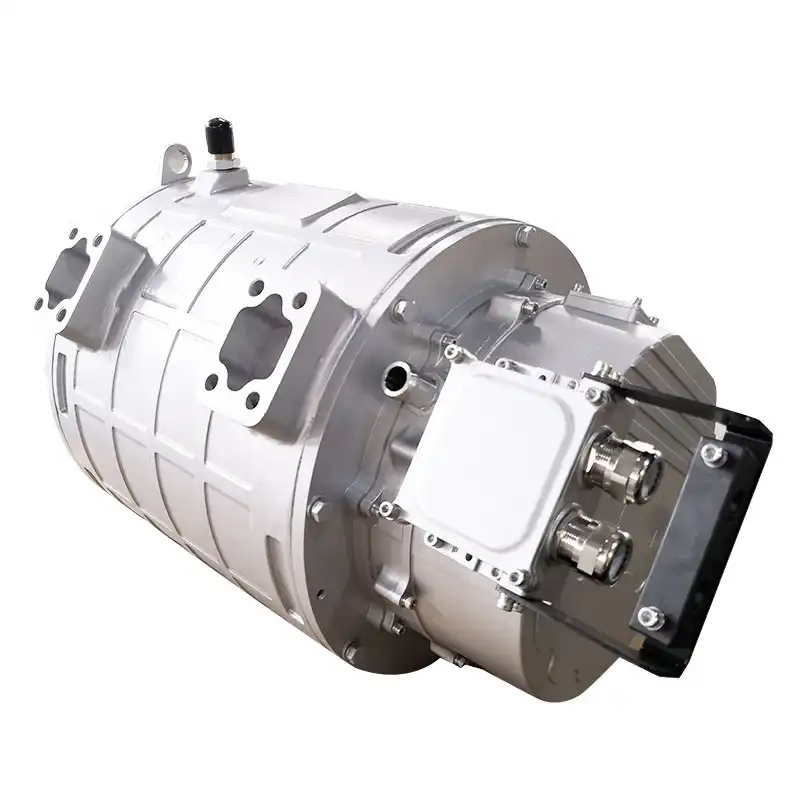
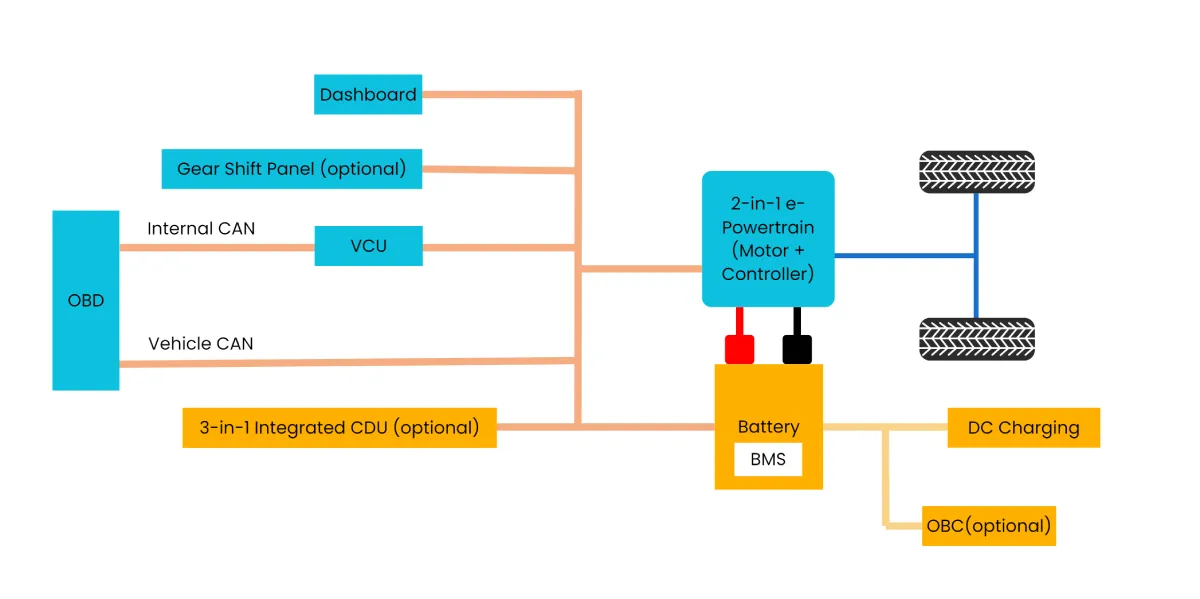
Solution Features
Compact Integrated Design
Optimized for minimal space usage, making vehicle integration more efficient.
Enhanced EMC Performance
Eliminates three-phase wiring harness radiation, reducing electromagnetic interference while improving overall system stability.
Lower Energy and Procurement Costs
Reduces power loss in wiring, improving efficiency and lowering component costs.
Proven Track Record
With over 30,000 units delivered, our e-powertrain for electric buses is trusted by industry leaders, providing its reliability and scalability in the market.
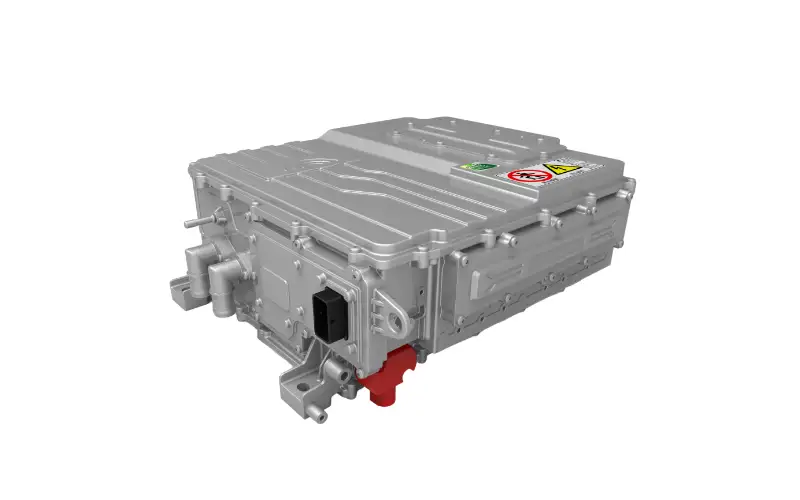
We can offer standalone Motor Control Units (MCU) or high-voltage integrated controllers customized to client requirements, integrating MCU, PDU, DC-DC, and steering and braking DC/AC.
Advanced Technology
- Dual integration design: combines functional and physical integration to reduce size and weight while lowering manufacturing costs.
- High-efficiency dual inverter control: reduces energy losses and achieves a peak controller efficiency of 98.5%.
- Advanced filtering & shielding: features multi-stage filtering, optimized wiring layout, enhanced structural processing, and reinforced enclosure shielding for improved electromagnetic compatibility.
- Modular & scalable architecture: designed with a modular and platform-based approach, allowing greater flexibility and expandability.
- Digital simulation & optimization: utilizes digital modeling for simulation analysis, enabling more versatile and cost-effective component selection.
EV Battery
For public transport vehicles, we provide tailored EV battery solutions based on specific customer requirements. Our comprehensive solutions encompass battery packs, battery management systems (BMS), battery thermal management systems (BTMS), and cloud-based services for full lifecycle management.
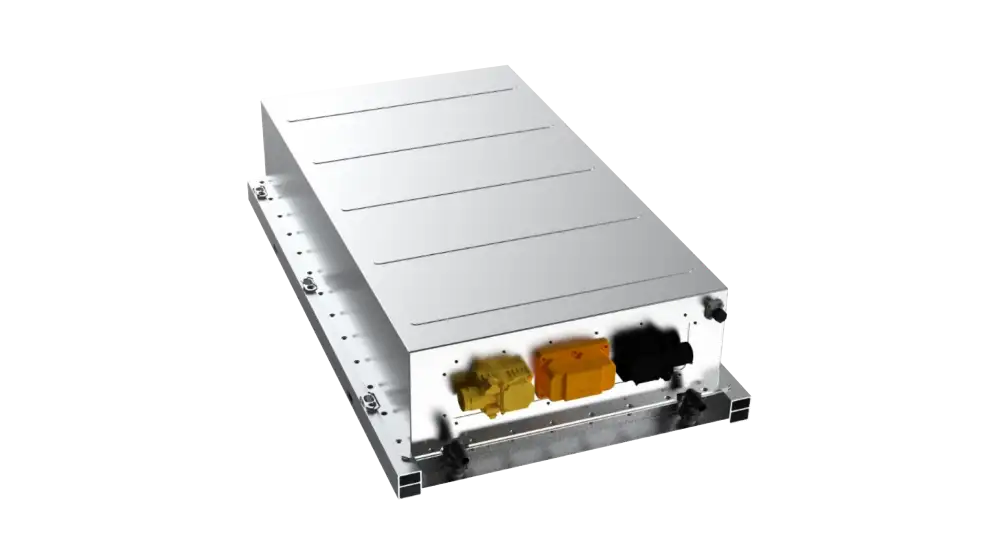
Our standardized EV battery packs are widely deployed across various applications. These packs are built using high-quality, industry-standard materials and proven manufacturing processes. With a standardized and modular design, we optimize the battery system structure layer by layer, achieving energy density levels that surpass the industry average for both battery modules and complete packs.
Solution Features
High Safety & Reliability
Built on a high-safety LFP system, with battery cells sourced from top-tier manufacturers such as CATL, EVE, and Gotion. The robust pack design meets relevant safety standards.
Wide Capacity Options
Offer multiple battery capacity configurations to meet diverse market demands, including extended range and high-load applications.
Lightweight & High Energy Density
Optimized design achieves an energy density of ≥140 Wh/kg, enhancing vehicle efficiency.
Superior Temperature Adaptability
Can be equipped with liquid cooling or heating systems based on customer requirements, ensuring reliable performance in extreme heat or cold conditions.
Strong Mechanical Protection
Features IP67-rated protection, making it highly resistant to harsh environmental conditions.
Advanced Technology
- Independently designed pack integration structure, adaptable to various battery cells and capacity requirements.
- Custom-designed electrical circuits and component selection, with in-house electrical testing capabilities to ensure compliance with industry standards.
- Highly integrated safety system, including harnesses, aluminum busbars, temperature sensors, internal pack pressure monitoring, explosion-proof valves, electrolyte leakage detection, and BMS collection boards, providing comprehensive and reliable active safety protection.
- Thermal runaway protection: equipped with insulation barriers between battery cells. If a cell reaches 900°C due to thermal runaway, the safety valve automatically releases pressure to prevent further hazards.
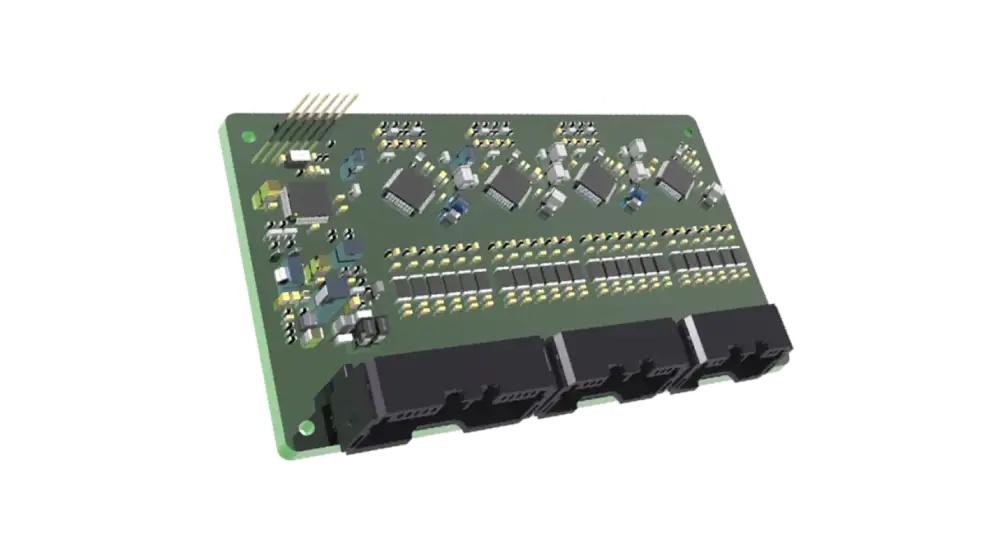
The Battery Management System (BMS) is a critical component designed to monitor and manage battery performance. Working alongside battery cells, the BMS acts as the system’s intelligent monitoring unit to ensure safety and efficient operation. Key functions of BMS include continuously tracking essential battery parameters, preventing overcharging and over-discharging, safeguarding the battery from potential damage; and optimizing performance and longevity by maintaining optimal operating conditions.
Our R&D Capabilities
- Independently develop BMS software for battery management control.
- Custom-designed control strategies and diagnostic analysis algorithms.
- Proprietary design of controller mainboards, control circuits, monitoring circuits, and communication circuits.
Advanced Technology
- High-Precision Calculations: SOC accuracy ≤3%; SOH health assessment accuracy ≤5%.
- Three-Tier Architecture: Ensures precise battery cell management, reduces error margins, and enables full lifecycle battery management.
- High-Speed Daisy-Chain Communication: Faster data transmission, lower power consumption, enhanced stability, strong anti-interference capability, and high voltage resistance.
- High Integration: BMS and PDU integration increases battery energy density, saving approximately 30% of space and reducing weight by 10%.
- Comprehensive Smart BMS Platform: Covers the entire system, from BMS controller software to an integrated edge-side BMS+EMS system and an EMS/battery management cloud platform, ensuring full-process security and control.
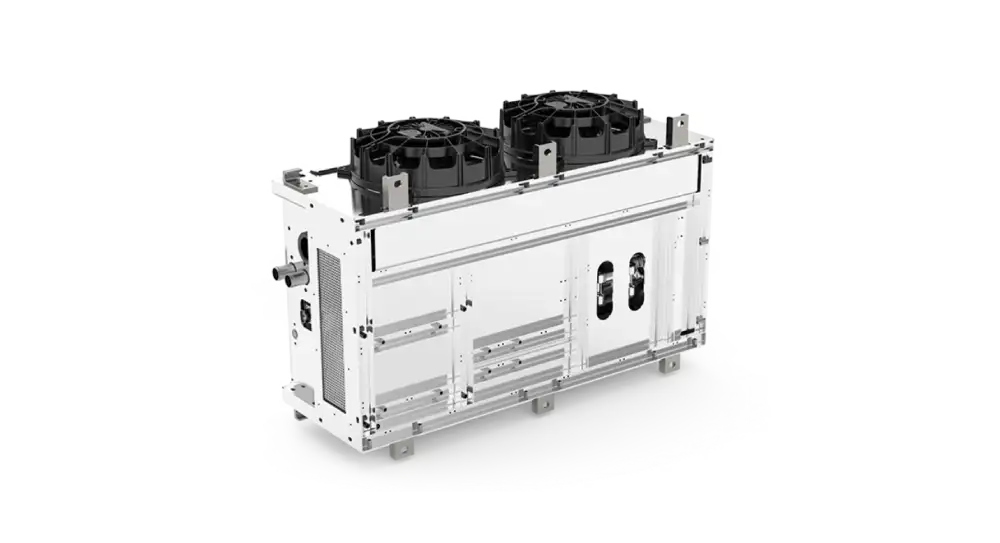
The Battery Thermal Management System (BTMS) is an integrated cooling and heating system designed to regulate the temperature of onboard batteries. The primary goal of BTMS is to keep the battery pack within an optimal temperature range, ensuring peak performance and longevity. By managing thermal energy across the vehicle, the system effectively reduces waste heat emissions, enhances energy efficiency, and minimizes environmental impact.
Solution Features
- Accurately measures and tracks battery temperature in real time.
- Effectively dissipates heat when battery temperature is high, preventing thermal runaway.
- Warms the battery in low temperatures to ensure safe and efficient charging and discharging.
- Reduces temperature differences within the battery pack, preventing localized overheating and extending overall battery lifespan.
Advanced Technology
- Aluminum alloy frame reduces weight and improves efficiency.
- Optional PTC liquid heater with standby, cooling, heating, and self-circulating modes.
- CAN bus communication for real-time fault self-diagnosis and status updates.
- Optional add-ons: tube-fin condenser, DC-DC, expansion tank.
EV Charging Solutions
Designed for city buses, coaches, shuttle buses, and commuter vehicles operating on fixed routes. These charging solutions are ideal for locations requiring centralized, high-power charging. Typically, vehicles are charged in bulk overnight, with fast charging available during the day to meet operational demands.
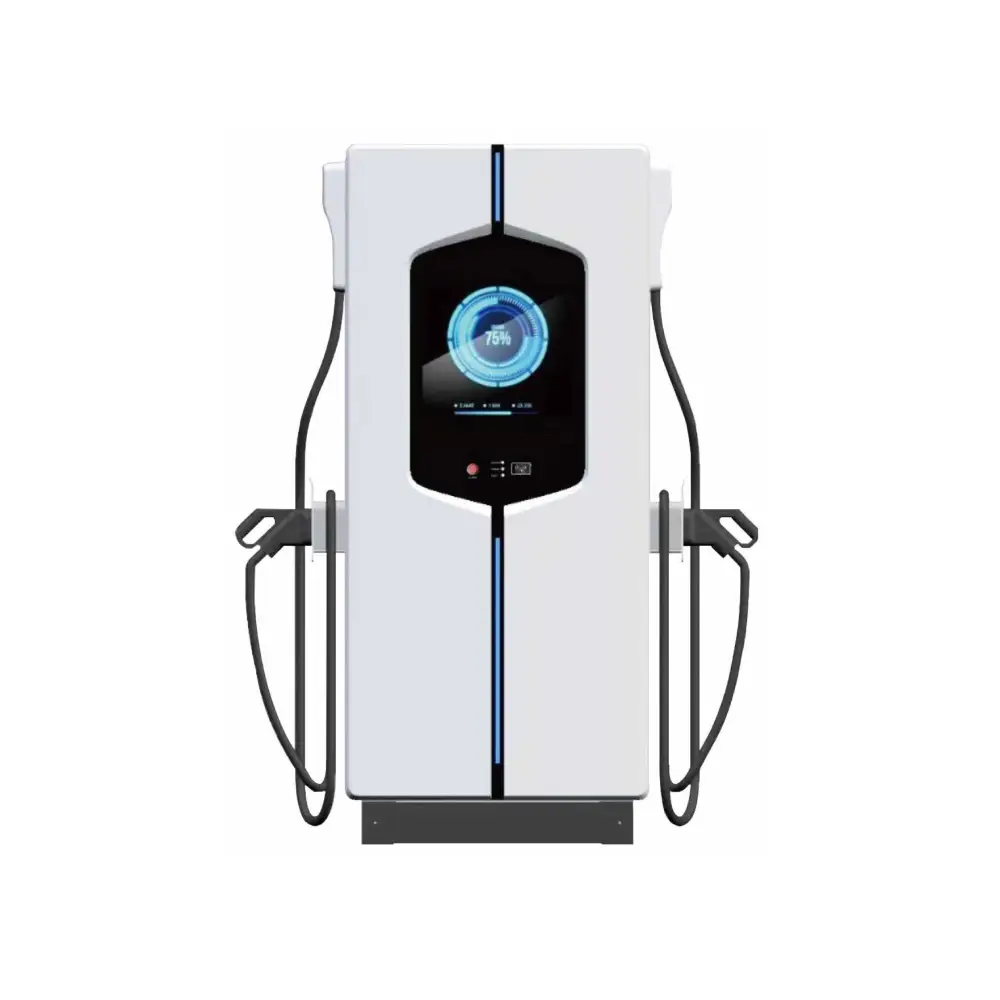
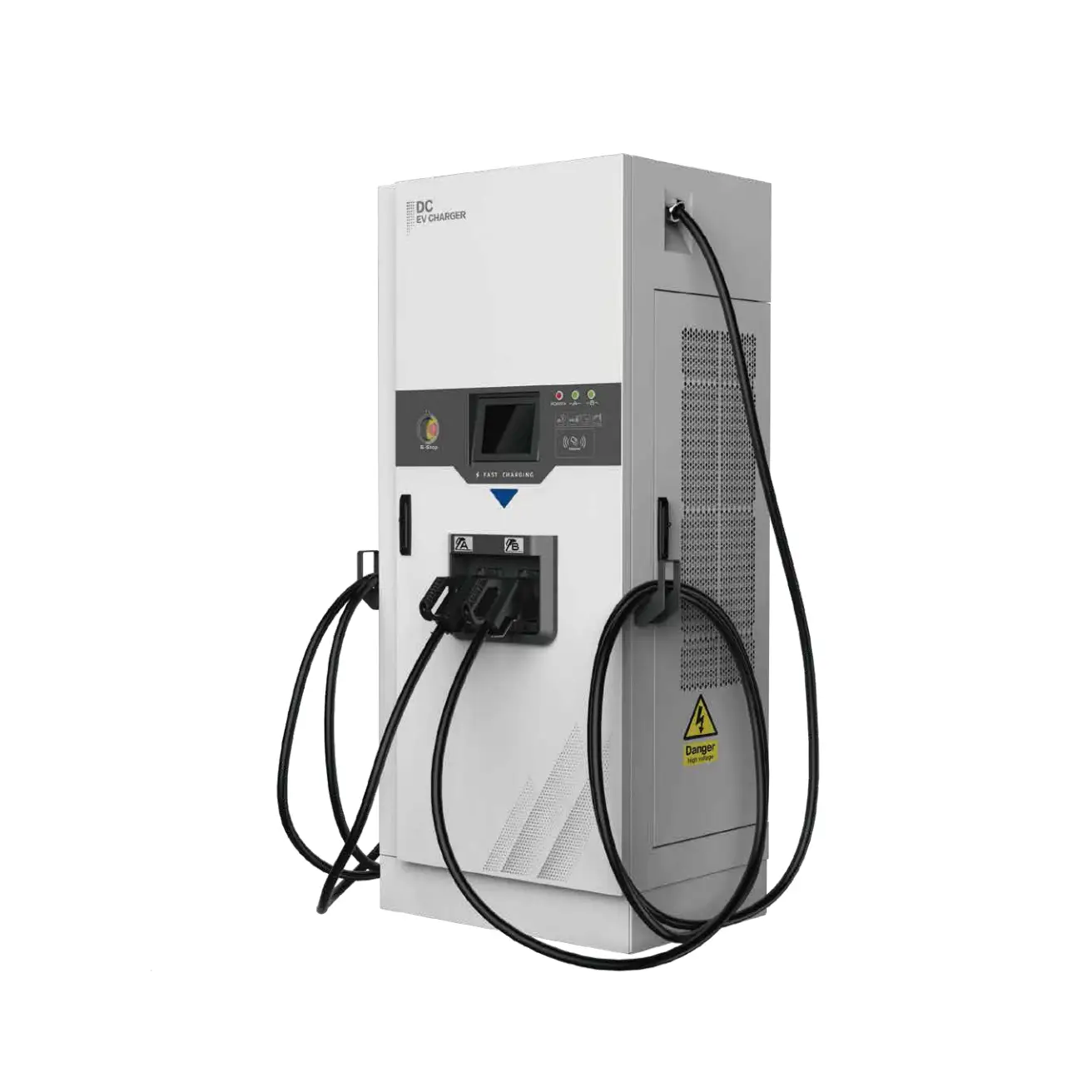
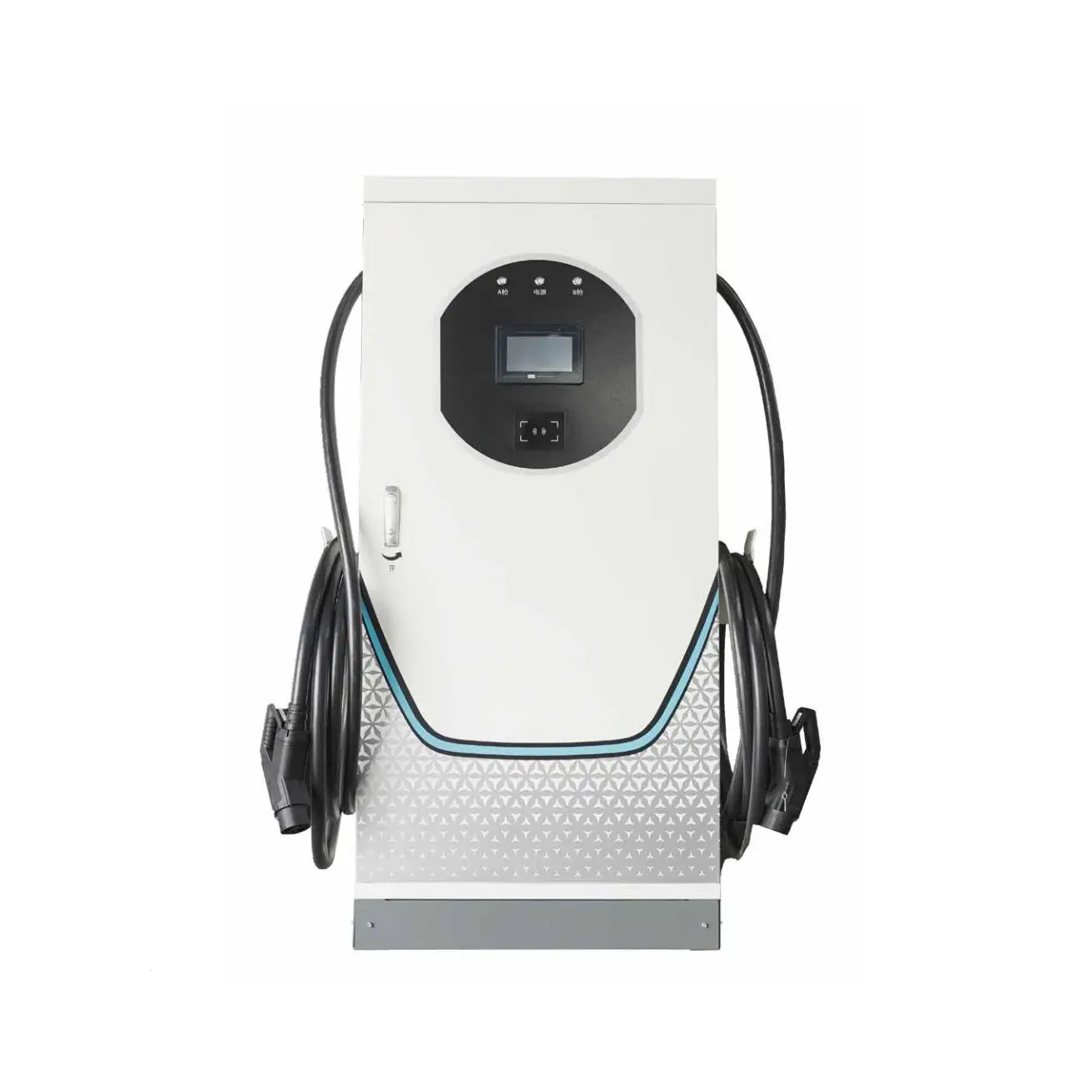
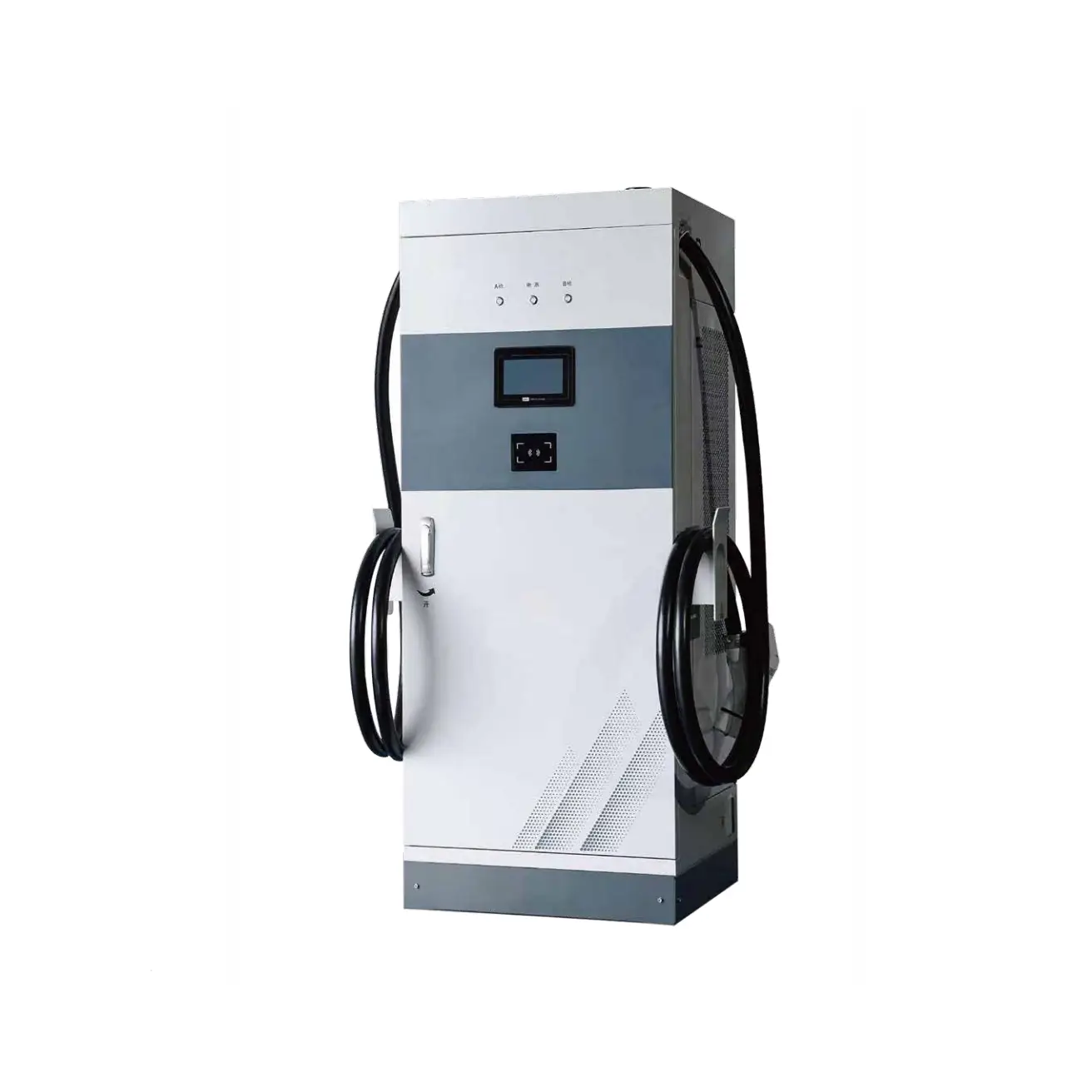
Other EV Systems for Light Commercial Vehicles
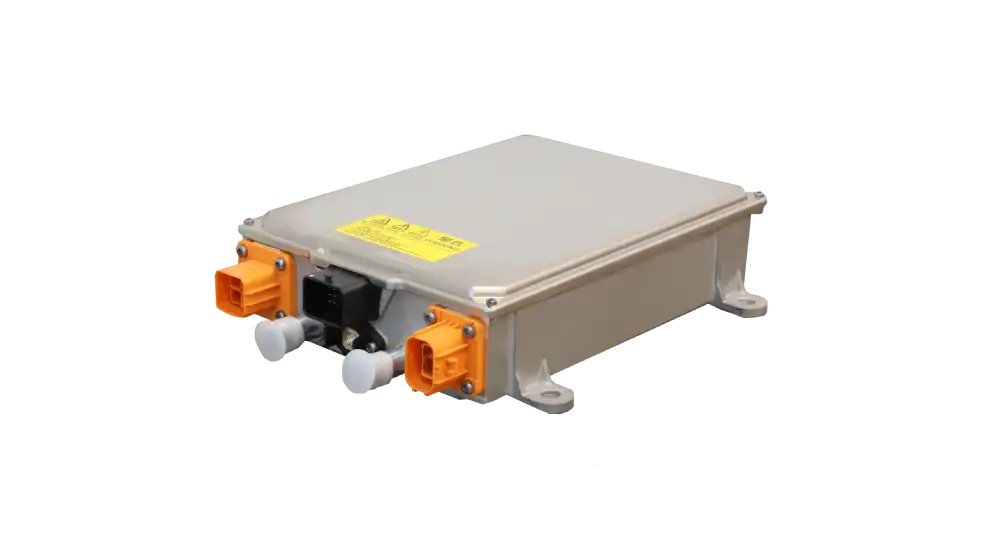
Onboard Charger, DC-DC Converter, PDU
Experience peak performance and reliability with our integrated EV on board charger (OBC), DC/DC converter, and PDU combo tailored for electric vehicles. Engineered for top-tier power conversion efficiency and remarkable power density, our chargers cover a broad power spectrum, ranging from 3.3 kW to 40 kW.
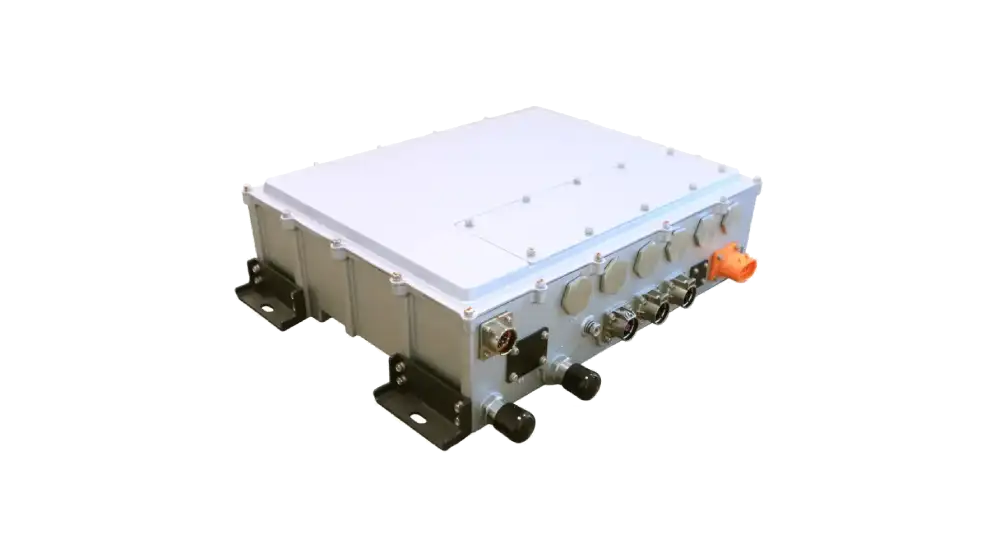
Auxiliary Inverter
We provide modular and scalable X-in-1 auxiliary inverters for public transport vehicle applications. Our auxiliary inverters cater to various types of new energy vehicles, including hybrid electric vehicles (HEV), battery electric vehicles (BEVs), and hydrogen fuel cell electric vehicles (FCEVs).
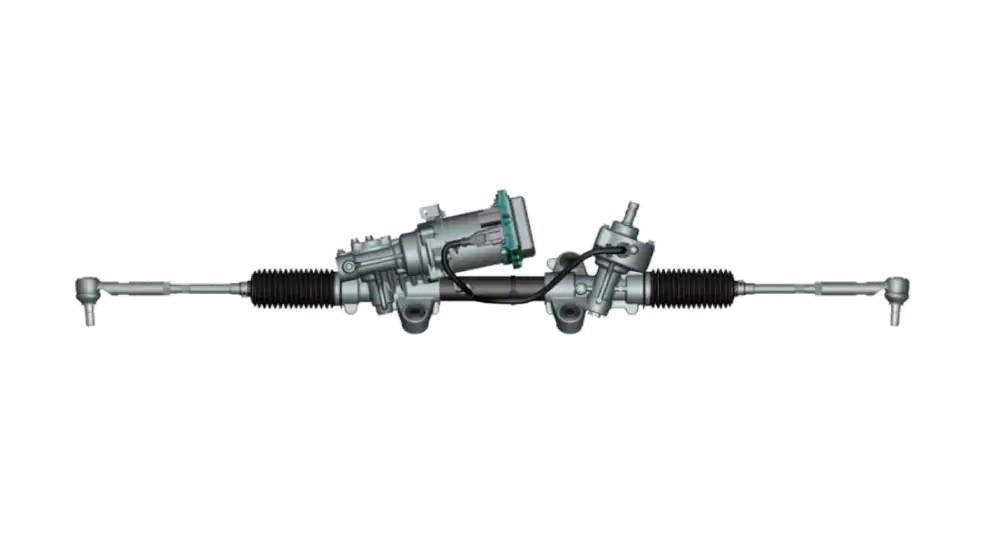
Electric Power Steering (EPS)
The Electric Power Steering System (EPS) is a type of power steering solution that uses an electric motor to assist the driver in steering. We offer various EPS systems based on the positioning of the assist motor, including C-EPS, P-EPS, DP-EPS, and R-EPS, each designed to meet the specific needs of different vehicle types.
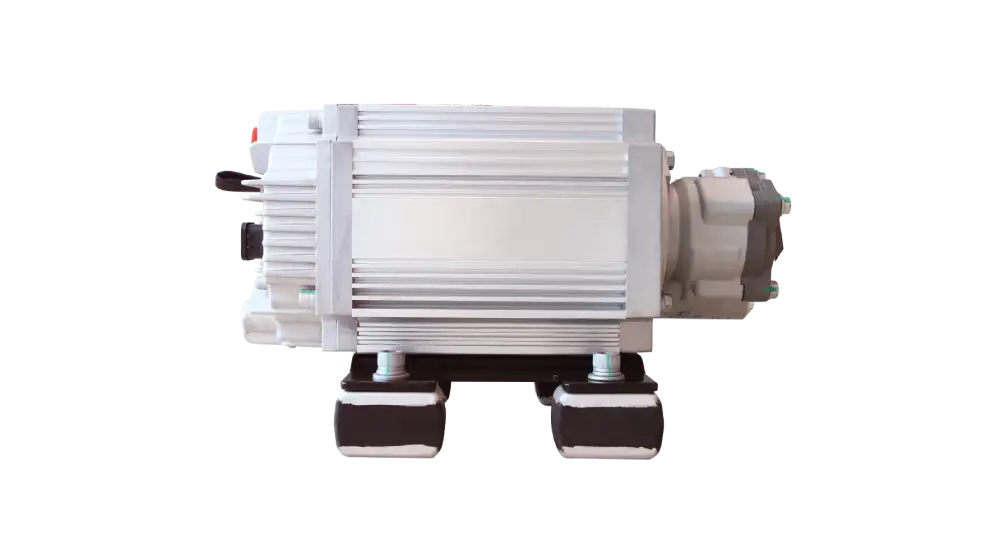
Electro-Hydraulic Power Steering (EHPS)
The Electro-Hydraulic Power Steering (EHPS) system is an upgraded version of the traditional hydraulic power steering (HPS) system. In this system, the steering pump is no longer driven directly by the engine but by an electric motor, coupled with an electronic control unit. This allows the steering assist to be adjusted not only based on the steering angle but also in response to the vehicle’s speed, providing a more efficient and responsive steering experience.
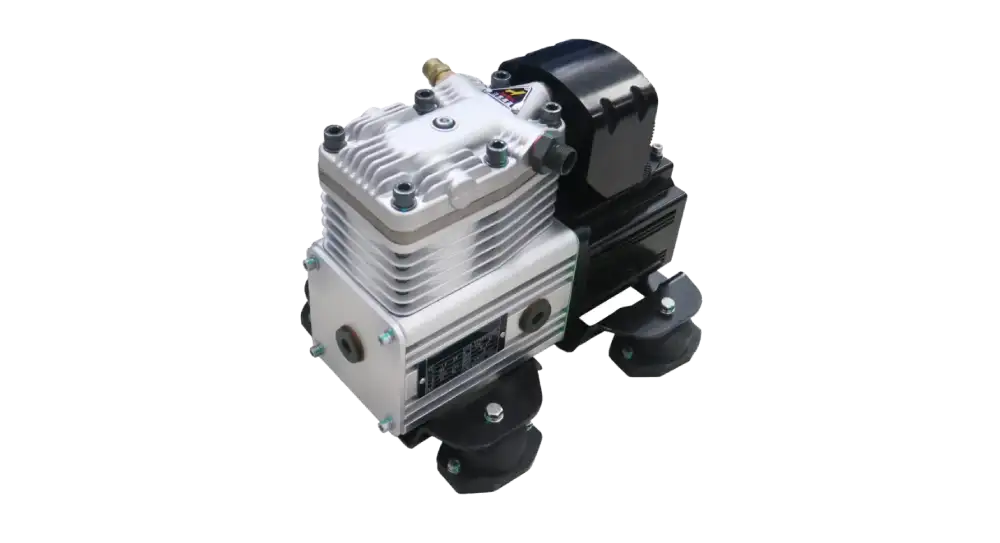
Air Brake Compressor
Our two-stage oil-free electric air brake compressors ensure the delivery of oil and water-free air, eliminating concerns associated with oil emulsification, leaks, and fire hazards. Its innovative structural design minimizes energy wastage during the compression process, thereby optimizing overall efficiency.
How We Work
Navigating Our Process
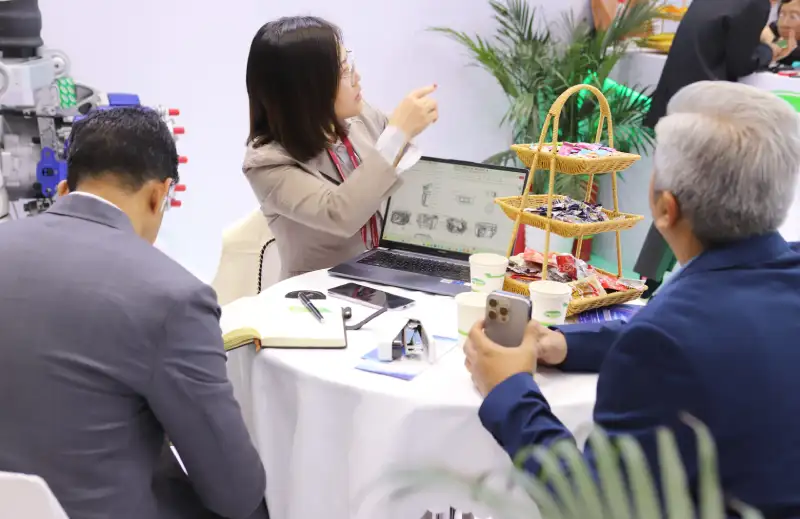
Demand Analysis & Project Evaluation
Once we receive your inquiry, our experts will connect with you within two business days to understand your specific requirements for the EV solution and conduct an initial feasibility evaluation of your project.
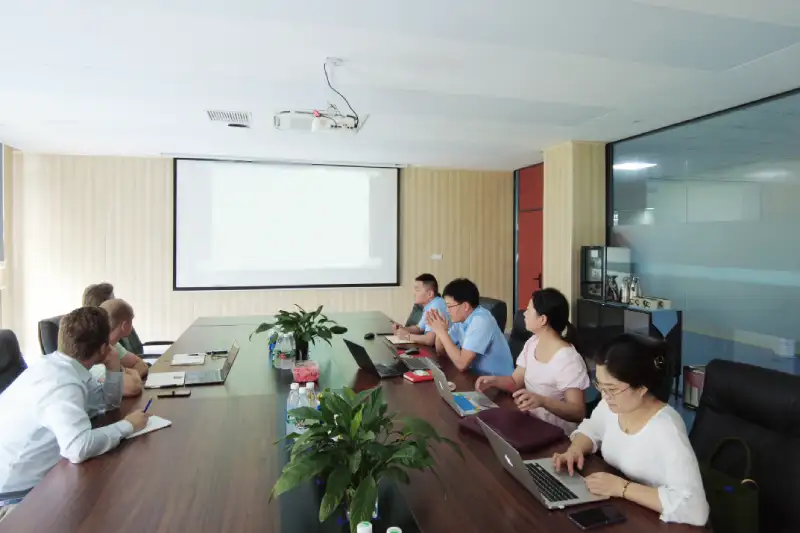
Project & Technical Coordination
If the project is deemed feasible, our engineering team will collaborate closely with your team on both hardware and software aspects to develop a viable solution. We will also provide a detailed quotation based on the technical requirements.
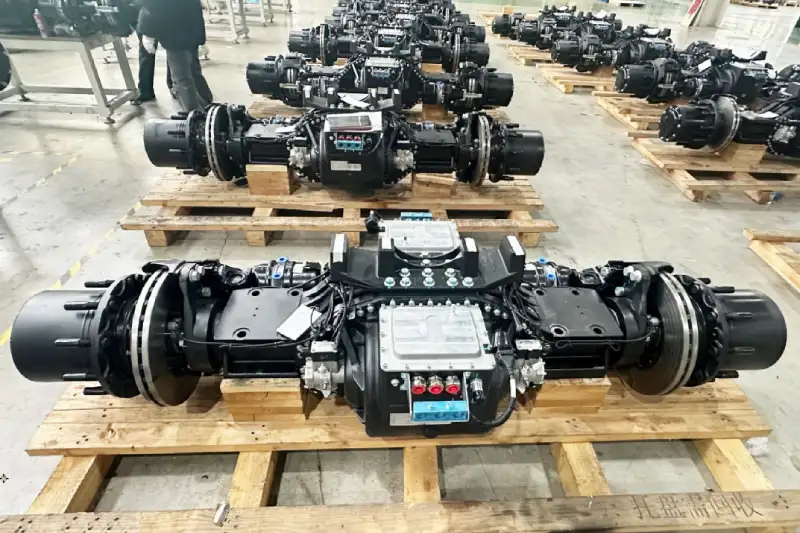
Development, Manufacturing & Testing
For customized or modified systems, we proceed with product development, including hardware and software adaptations. Our EV systems undergo rigorous testing to ensure quality, reliability, and full functionality before deployment.
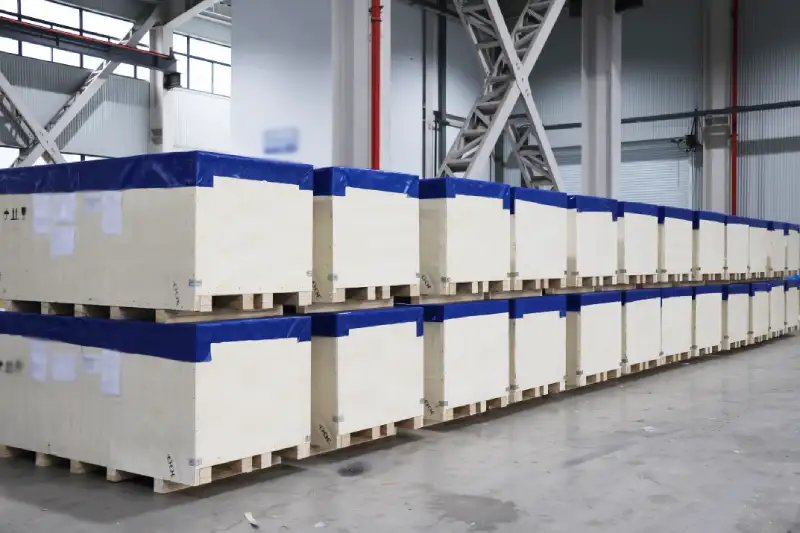
In-Time Global Shipping & Delivery
We have established strong partnerships with international shipping providers, ensuring safe and timely delivery of products to your specified location. This guarantees a smooth and efficient deployment of your EV project.
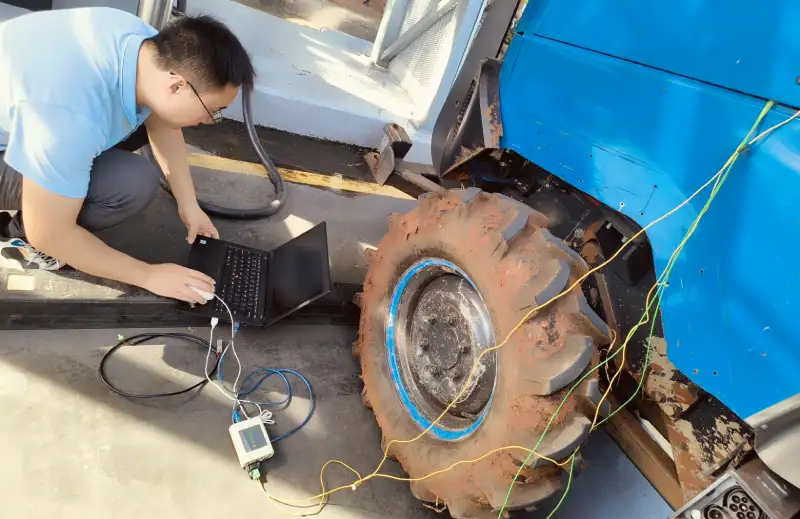
Full-Stage Remote/Onsite Technical Support
We provide technical support throughout the entire project lifecycle, including consultancy, hardware and software development, calibration, and both onsite and remote debugging, ensuring optimal performance and long-term success.
What we offer
Product Highlights
Explore our most popular and widely used systems for public transport vehicles. Additional options are available upon request to meet your specific needs.
320 kW Distributed Drive Electric Portal Axle
- Distributed drive approach adding additional safety redundancy to the vehicle
- Compact and lightweight design lowers the center of gravity and icnreases the stability
- Advanced core technologies such as EDS, EASR, IESS, etc.
- Adapts to the fully flat, low-floor design and wide interior aisle layout

360 kW Distributed Drive Electric Axle
- Dual-motor structure and advanced gear-shifting control strategy to ensure uninterrupted power delivery
- Distributed drive approach adding additional safety redundancy to the vehicle
- Compact and lightweight design lowers the center of gravity and icnreases the stability
- Advanced core technologies such as EDS, EASR, IESS, etc.
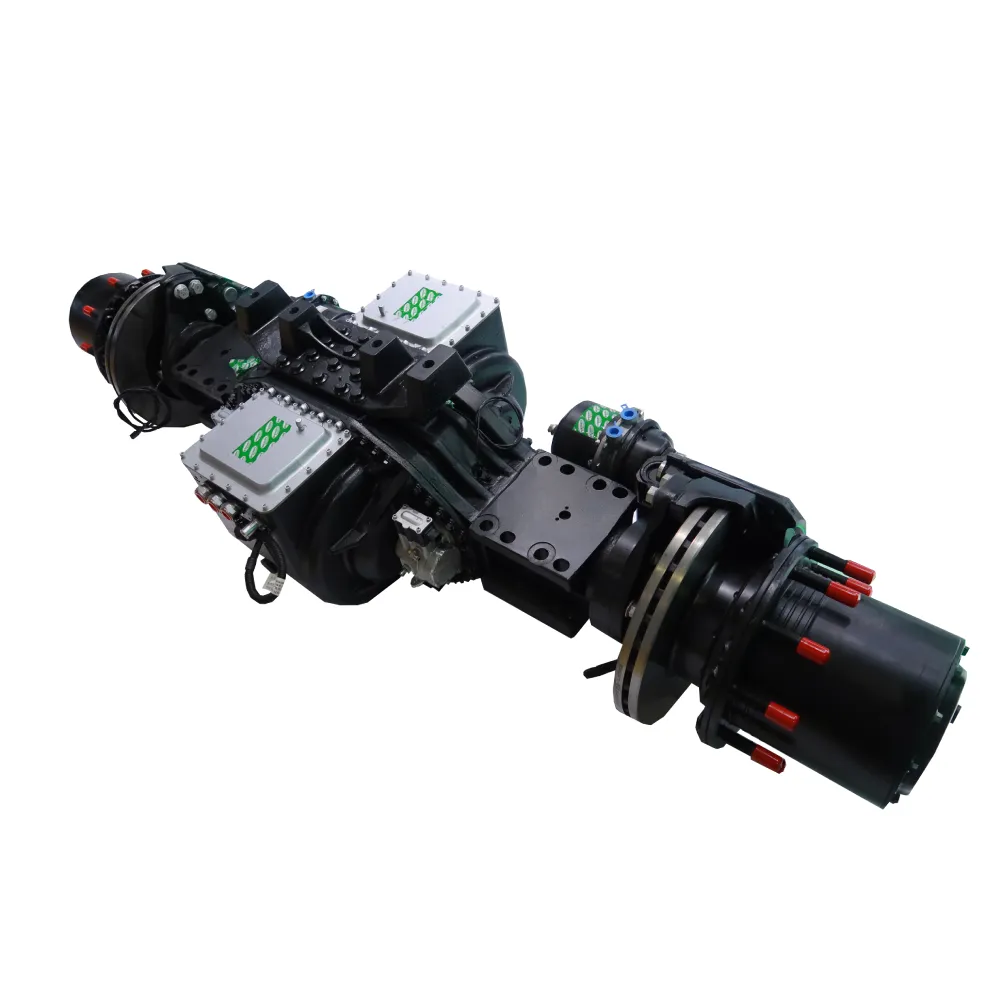
180 kW Distributed Drive Electric Portal Axle
- 4-airbag independent suspension system for enhanced comfort during driving and steering
- Distributed drive approach adding additional safety redundancy to the vehicle
- Compact and lightweight design lowers the center of gravity and icnreases the stability
- Advanced core technologies such as EDS, EASR, IESS, etc.

80 kW / 160 kW Integrated Electric Axle
- 10% increase in energy recovery efficiency
- Successfully passed the 1-million-kilometer durability test
- Adopting the two-stage helical gear transmission to shorten the drivetrain
- Highly compact system integrating the motor, gearbox, and rear axle
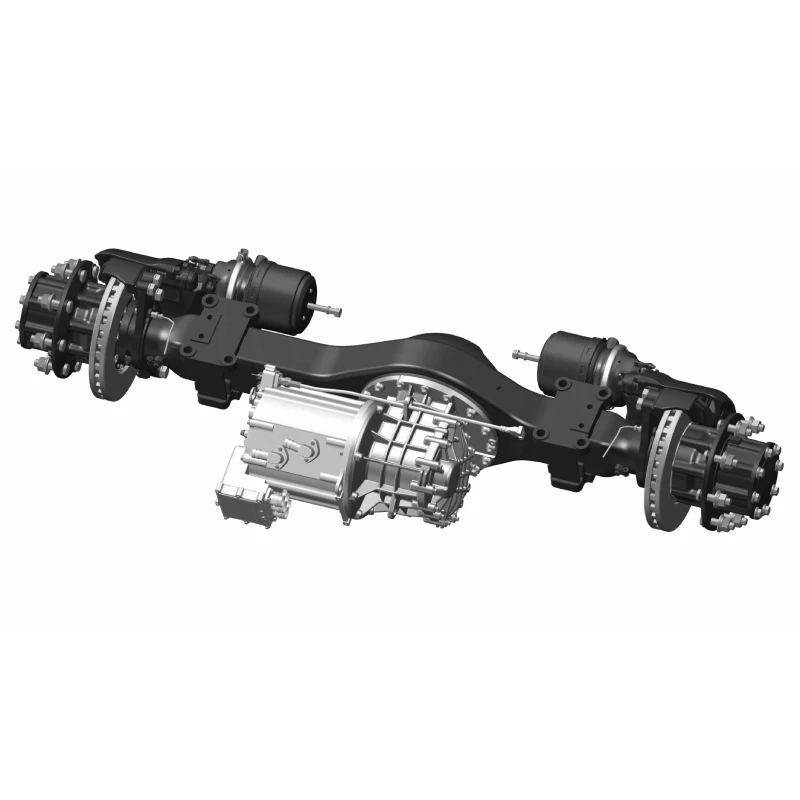
60 kW / 115 kW Integrated Electric Axle
- 100 kg reduce in weight compared to direct drive systems
- 5% reduce in power consumption compared to direct drive systems
- 350 N.m maximum torque for robust power during climbing
- 100% counter torque for increased cruising range
- Lower than 70 dB noise for a more pleasant driving experience
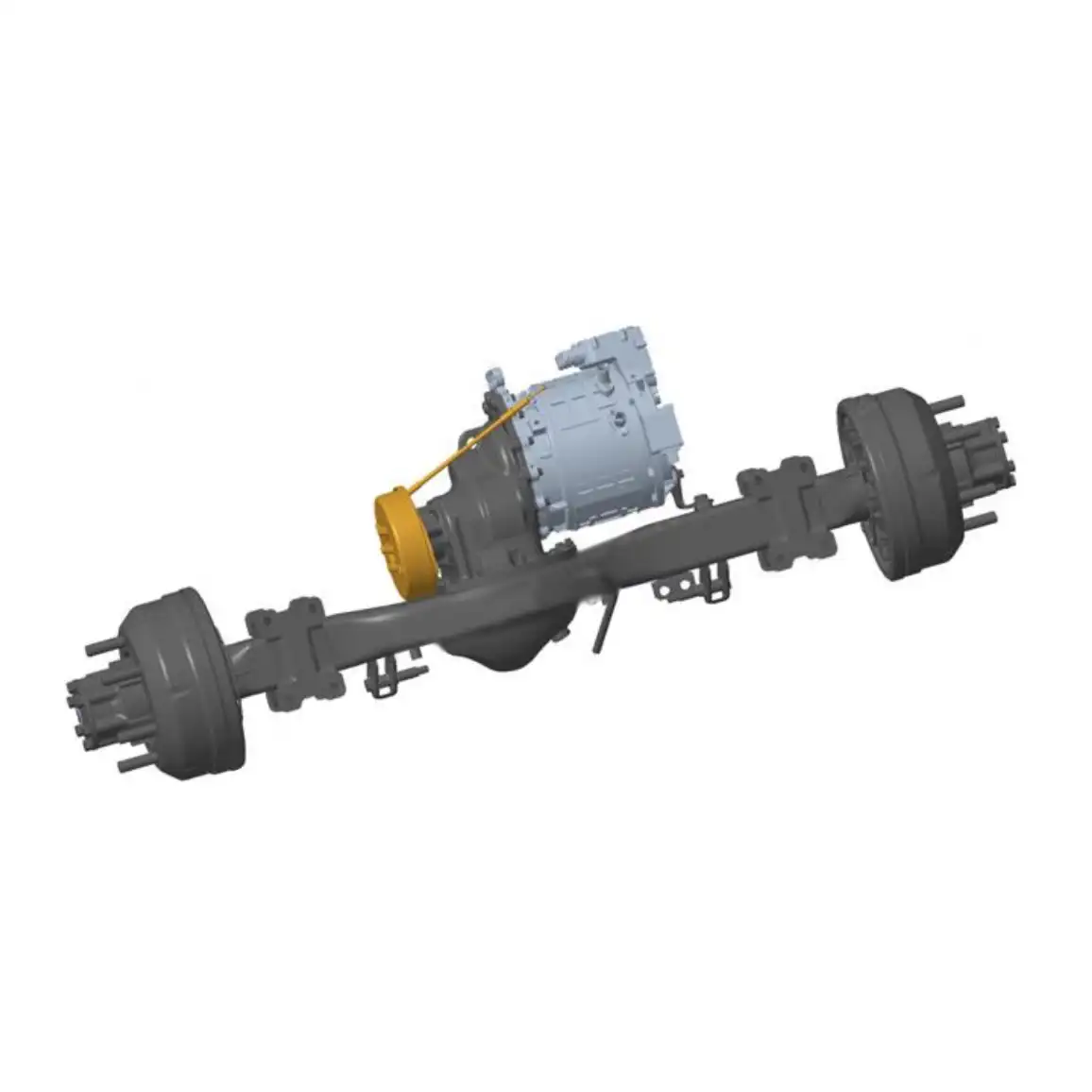
60 kW / 130 kW Coaxial Electric Axle
- 100 kg weight reduction compared to direct drive systems
- 15% reduce in power consumption compared to direct drive systems
- 30% increase in passenger capacity
- Lower than 70 dB noise for a more pleasant driving experience
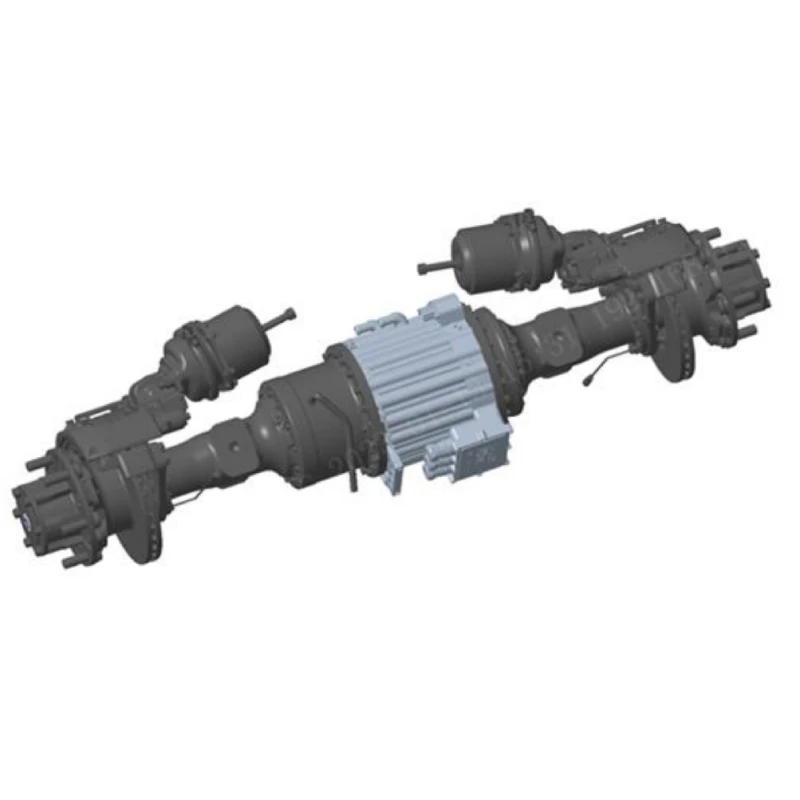
120 kW / 240 kW Direct Electric Drive Motor
- For city buses from 10 meters to 12 meters and coaches from 8 meters to 10 meters
- Motor peak efficiency ≥ 97% thanks to advanced design technologies
- IP68 protection with a flange-based mud and water protection structure
- Spiral cooling channel design for excellent heat dissipation
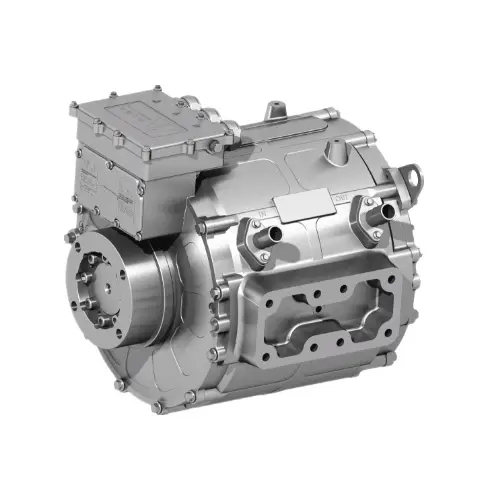
150 kW / 180 kW / 200 kW 2-in-1 E-Powertrain
- Integrates the motor and controller for a compact and lightweight design
- Mass production since 2018 with over 30,000 units successfully deployed
- Achieves over 90% motor efficiency, optimizing energy use
- Suitable for electric buses or coaches from 8 meters to 12 meters
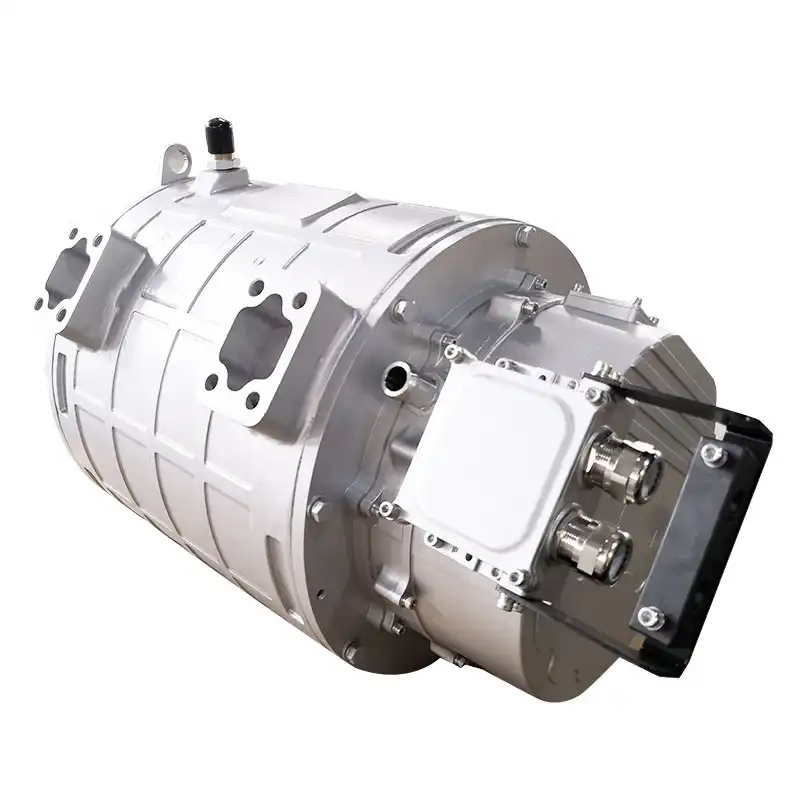
60 kW / 100 kW 3-in-1 E-Powertrain
- Compact design integrating motor, motor controller, and gearbox
- Reduced weight by utilizing shared housing and wiring harnesses
- Provide more flexibility in vehicle layout to create scalable platforms
- Wide applications for pickup trucks, vans, and light trucks

30 kW / 60 kW Direct Drive Motor
- Have been deployed in over 10,000 EVs globally and in mass production now
- With built-in ASR for overall vehicle safety by preventing wheel slippage
- Achieves up to 95% peak efficiency
- High EMC design meets Class 4 standards

Standardized LFP Battery Pack
- Independent slave control: simplifies installation and maintenance
- Integrated liquid cooling: strong adaptability in high-temperature environments
- All-aluminum casing: lightweight design with high energy density
- Protection level: IP67
- Standard equipped with heating film
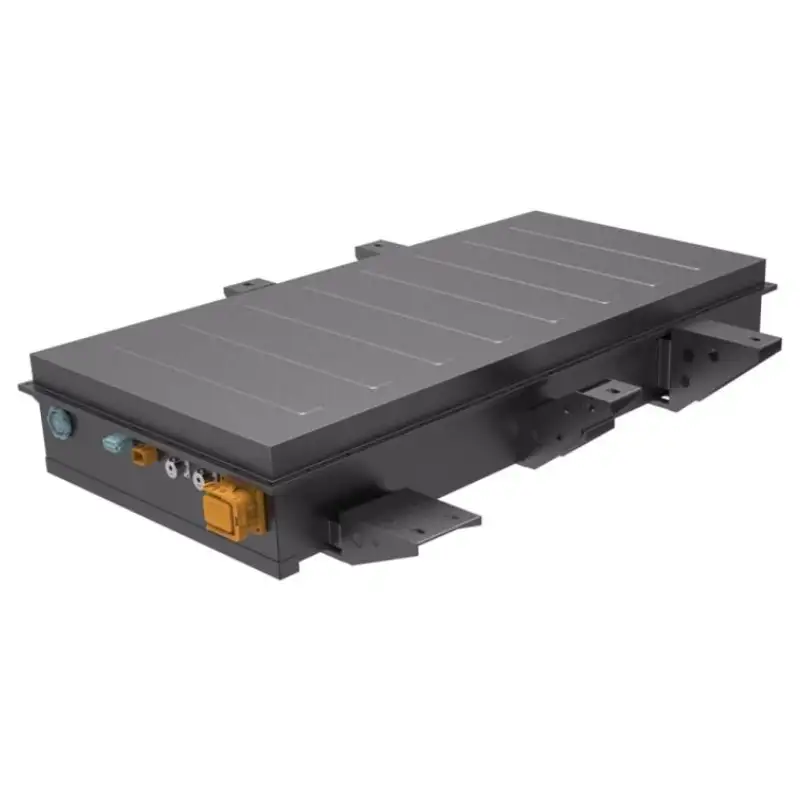
Dimension (mm) | 1060*630*240 | ||||
Cell Capacity (Ah) | 105 | 173 | 230 | 280 | 304 |
Battery Packing Scheme | 2P48S | 1P63S | 1P48S | 1P36S | 1P36S |
System Capacity (Ah) | 210 | 173 | 230 | 280 | 304 |
Nominal Voltage (V) | 153.6 | 202.86 | 153.6 | 115.2 | 115.2 |
Energy (kWh) | 32.256 | 35.095 | 35.328 | 32.256 | 35.02 |
Blade Battery Pack
- CTP (Cell-to-Pack) design, bypassing the need for battery modules
- Reduced pack size, more flexible space for easier layout
- Higher energy density for longer cruising range
- Stacked design provides more uniform current density and superior internal heat dissipation
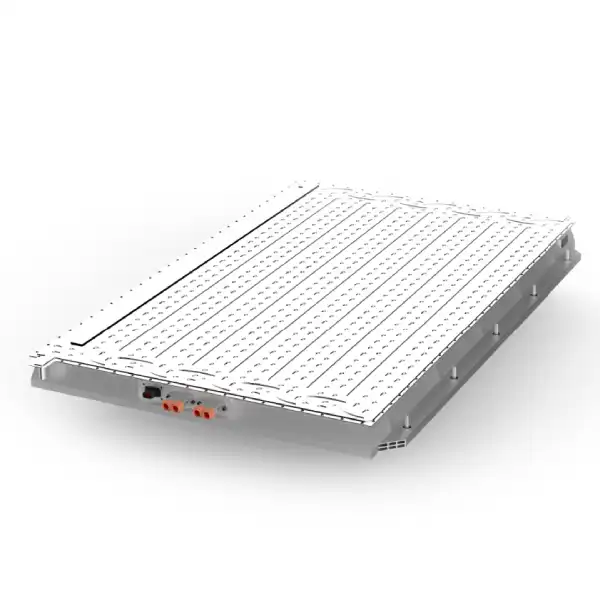
Pack | B30 | B31 | B32 | B33 |
Energy | 37.5 kWh | 31.2 kWh | 38 kWh | 31.7 kWh |
Voltage | 153.6 V | 128 V | 115.2 V | 96 V |
Cell capacity | 244 Ah | 244 Ah | 330 Ah | 330 Ah |
Size | 1050*627*240 mm | 905*627*240 mm | 1050*627*240 mm | 905*627*240 mm |
3-in-1 / 4-in-1 Auxiliary Inverter
- Integrated design with a DC/DC converter, two DC/AC inverters, and a PDU
- Compact and lightweight to improve vehicle layout
- Quiet operation with minimal disruption at less than 42 dB
- Versatile applications across diverse work conditions, including challenging environments
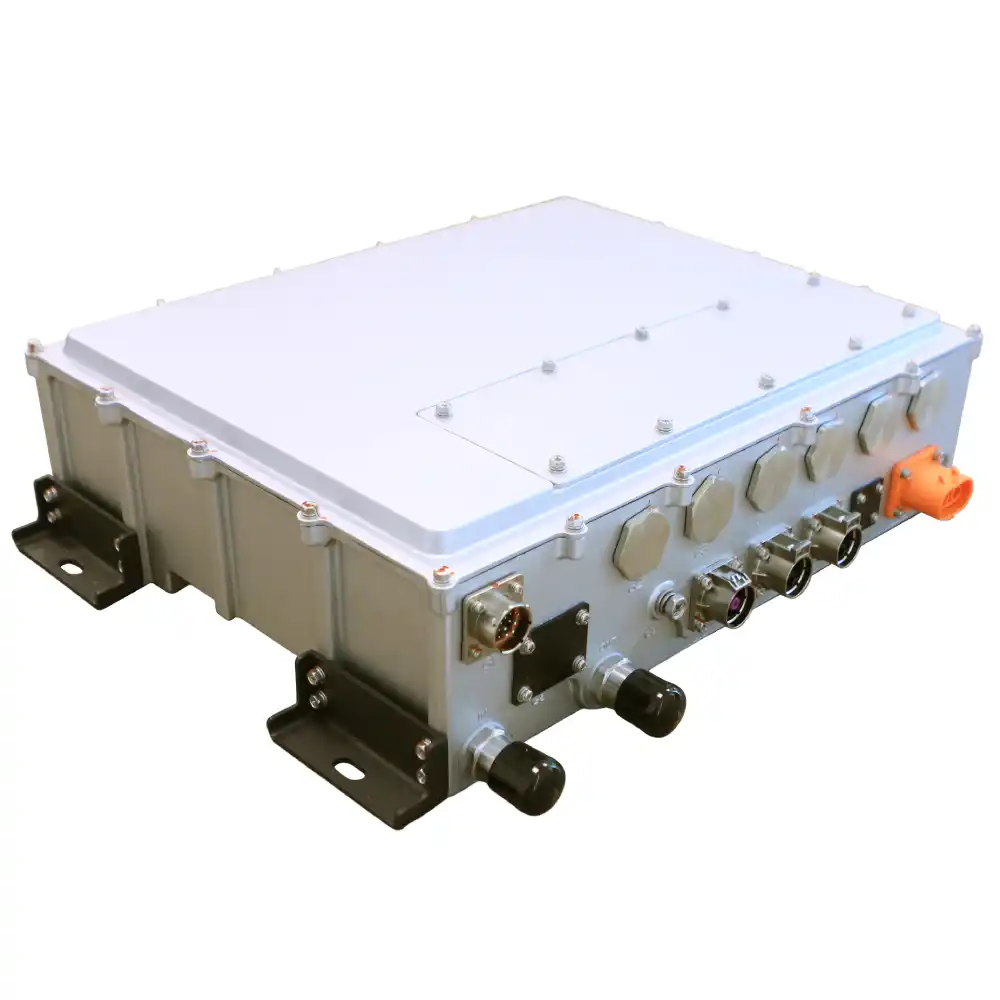
20 kW Liquid-Cooled Onboard Charger
- Liquid-cooling
- Compact and lightweight design for easy installation into various vehicle platforms
- Constant power and constant current charging capabilities
- Vibration-resistant with an IP67 rating
- DC high voltage interlock loop (HVIL) protection
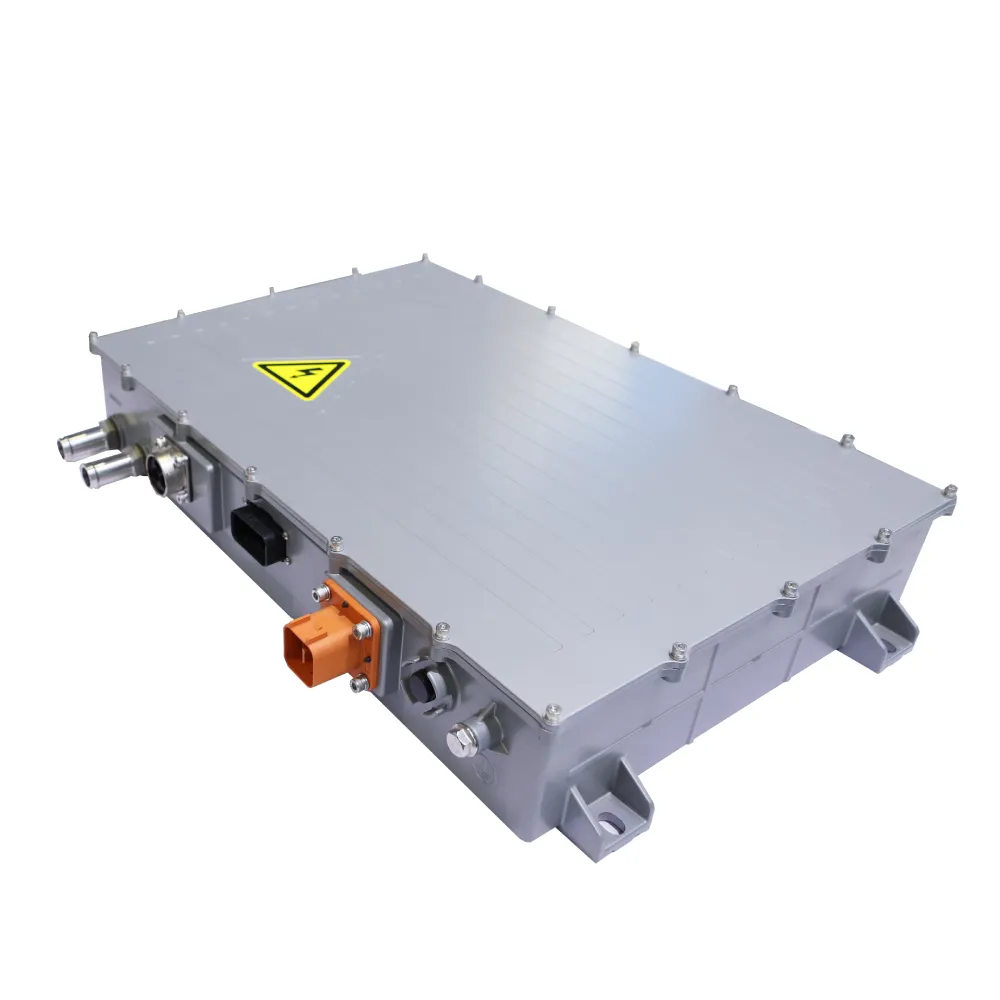
20 kW Air-Cooled Onboard Charger
- Air-cooling
- Comprehensive protection mechanisms
- CAN interface communication
- Improved system robustness

Rack-assist Type Electric Power Steering (R-EPS)
- Easy installation: adopts to existing layouts for a smooth transition
- Simplified design: fewer parts for efficient assembly
- Utilizes non-contact sensors for accurate angle measurement
- Maintains some steering assistance even under certain failure modes
- Adapts to the needs of ADAS and autonomous driving, particularly for large steer-by-wire chassis
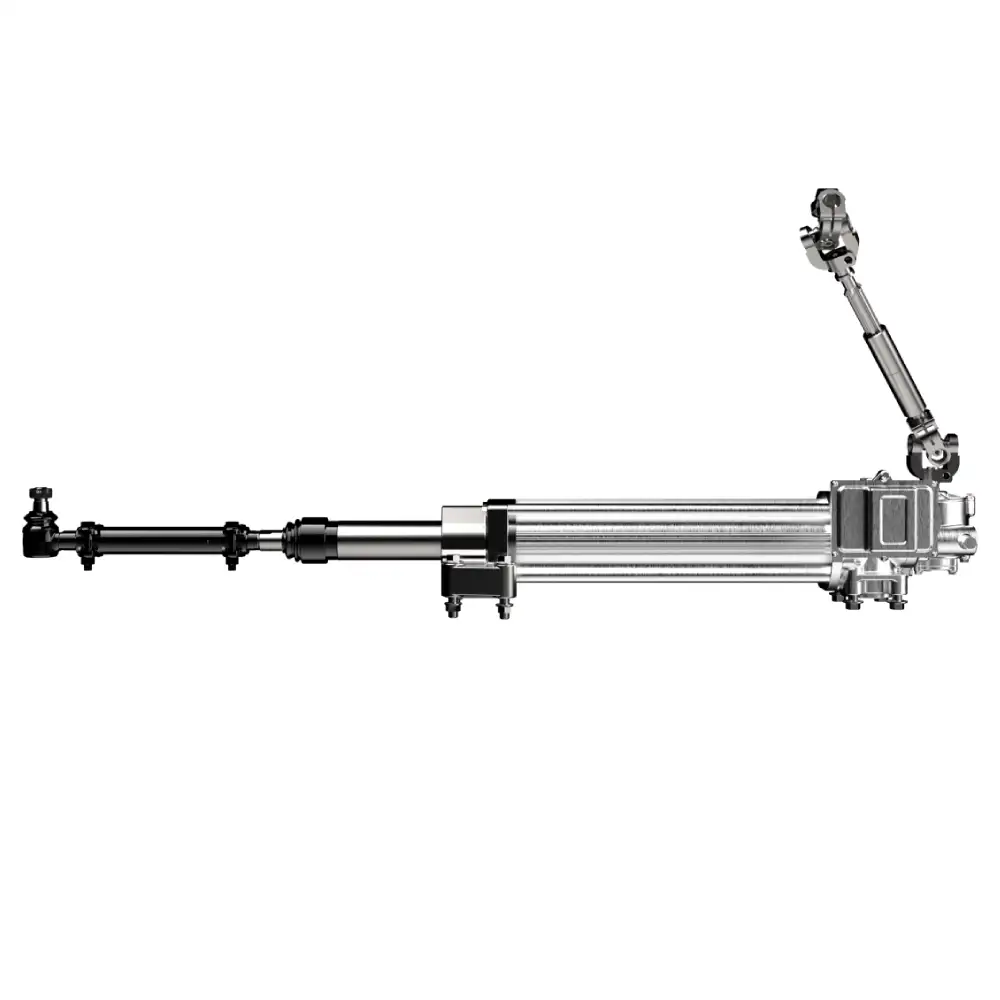
Dual-Power Source Electro-Hydraulic Power Steering System
- Additional safety redundancy due to the dual-power functionality
- The high-voltage and low-voltage circuits are completely independent
- Lightweight and designed for easy installation within the vehicle chassis
- Communication terminal provide feedback on operational parameters for real-time monitoring
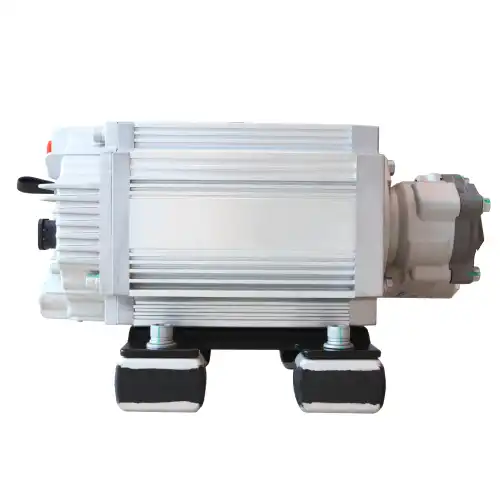
Oil-Free Piston Air Brake Compressor
- Self-lubricating materials for oil-free compression and no pollution
- Two-stage compression system for high efficiency, low energy consumption, and exceptional reliability
- Advanced noise reduction technology for minimal operational noise
- Compact design for easy installation and convenient chassis layout
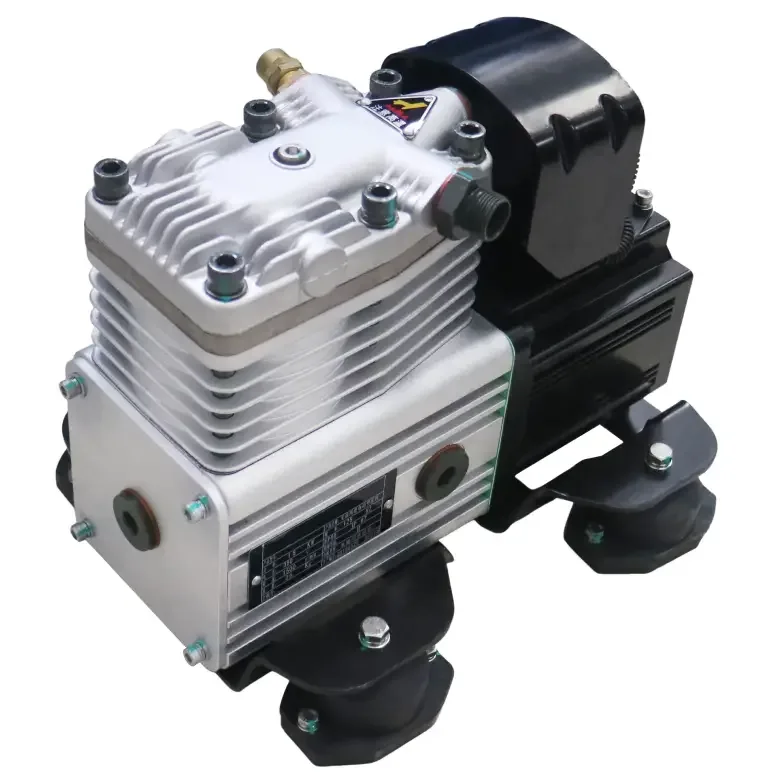
Case Study

Electric Bus Project
In response to Turkey’s growing environmental initiatives, a well-established Turkish commercial vehicle manufacturer embarked on an electric bus project, focusing on 8-meter and 12-meter models. Leveraging our expertise in electric bus battery systems, we delivered a tailored solution that included a 280 kWh battery system, a custom BMS with PDU, a cooling unit, and other essential components. This case study outlines our approach to overcoming technical challenges and providing comprehensive support throughout the project
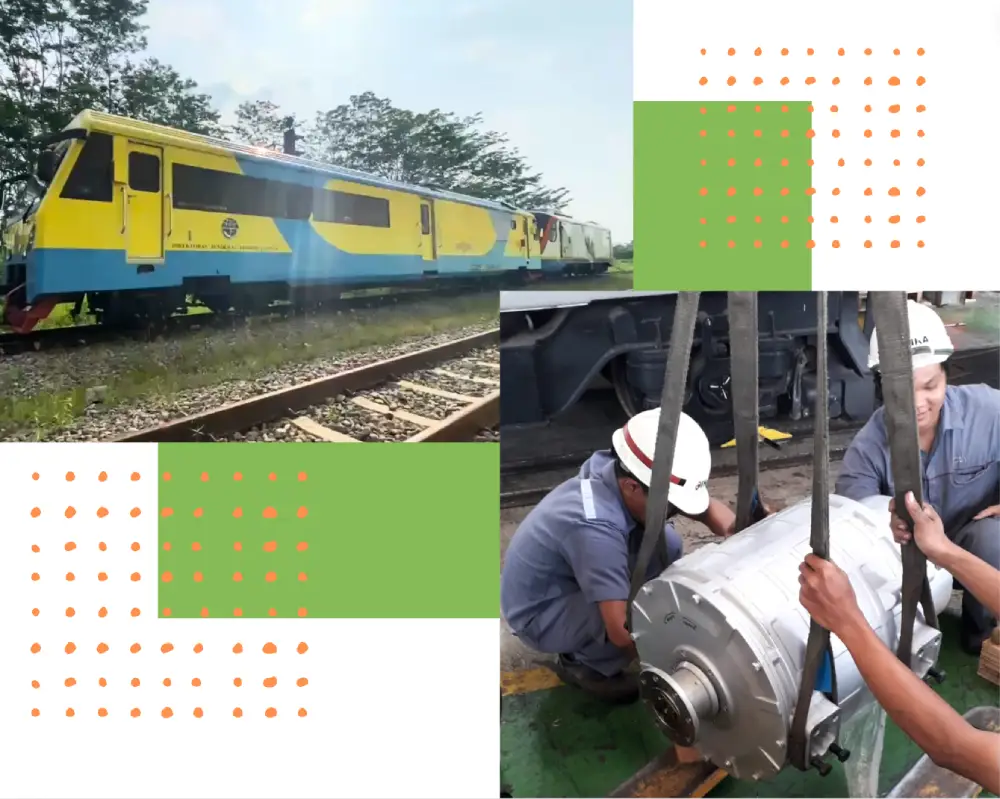
Electric Train Project
This project is about the electric train. In this project, we have supplied the PMSM electric motors. In the photo, technicians are seen installing these motors, which are designated for traction in the first carriage and propulsion in the last carriage. A successful test drive has been completed, confirming that the system operates smoothly on the train. The electric motor has a rated power of 120 kW and a peak power of 200 kW. It adopts the integrated design, saving space and improve the vehicle layout.
Contact Us
Get in touch with us by sending us an email, using the Whatsapp number below, or filling in the form below. We usually reply within 2 business days.
Email: contact@brogenevsolution.com
Respond within 1 business day
Whatsapp: +8619352173376
Business hours: 9 am to 6 pm, GMT+8, Mon. to Fri.
LinkedIn channel
Follow us for regular updates >
YouTube channel
Ev systems introduction & industry insights >