Heavy Duty Vehicle Electrification Solutions
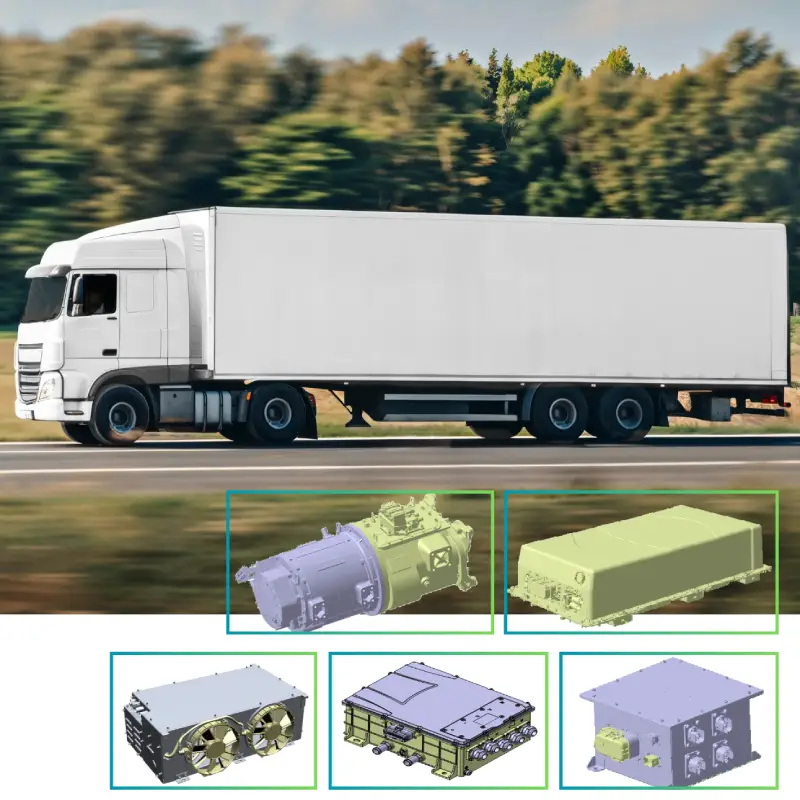
Heavy-duty vehicle electrification is a key solution for reducing carbon emissions in road transport. Heavy trucks consume large amounts of fuel per mile, have long annual mileage, and generate substantial emissions, making them one of the most significant contributors to transportation-related pollution.
Electric heavy trucks enable truly zero-carbon transportation. Their electric powertrains significantly cut energy costs compared to diesel, reducing per-mile expenses by up to one-third.
At Brogen, we deliver tailored EV solutions for heavy-duty vehicles, offering multiple technological configurations to meet manufacturers’ diverse needs.
Email: contact@brogenevsolution.com
Why Choose Brogen
Our Heavy Duty Vehicle Electrification Solution Advantages
Medium Truck
Heavy Truck
E-trailer
Tractor
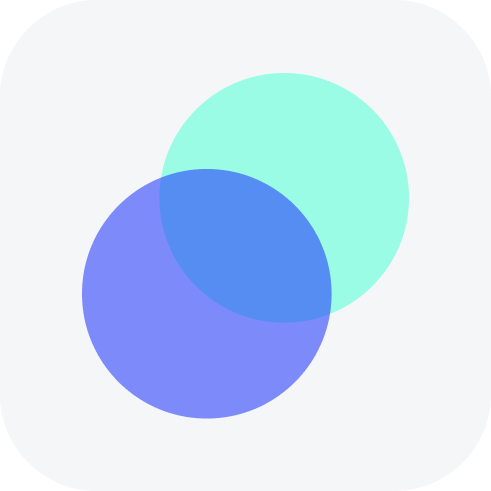
Lightweight Design
Our EV solutions for heavy duty vehicles are engineered with a lightweight approach, reducing energy consumption while improving vehicle dynamics, safety, and cargo capacity, enabling end clients to enhance operational efficiency.
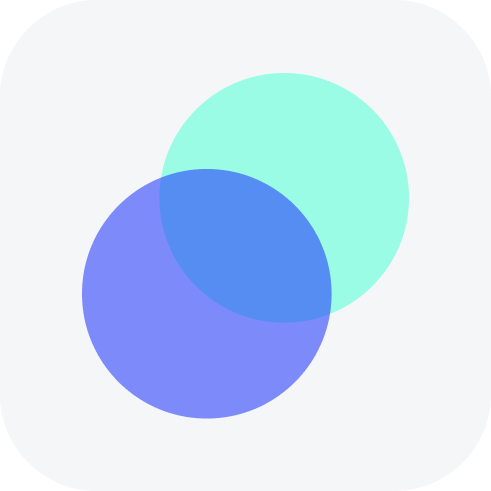
Proven Safety & Reliability
Our EV systems undergo rigorous testing and have been deployed in mass-production trucks from leading OEMs. With real-world validation, they deliver exceptional safety, reliability, and compliance with industry standards.
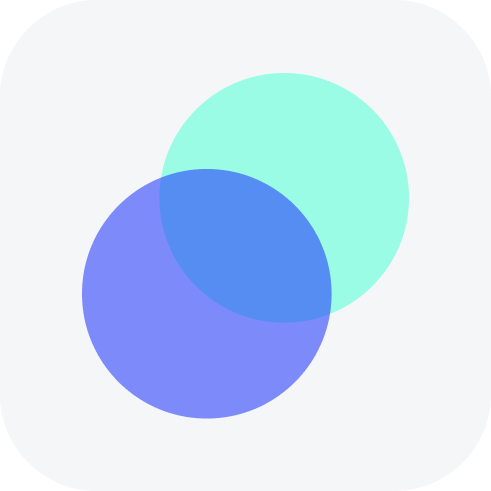
Advanced Technology
We integrate advanced EV technologies. By combining state-of-the-art hardware and intelligent software, we empower OEMs to develop high-performance, future-ready electric trucks that stand out in the market.
What We Offer
Our Heavy Duty Vehicle Electrification Solutions
Electric Powertrain
We offer a wide range of electric powertrain solutions for heavy-duty vehicles, tailored to meet diverse technical requirements. Our offerings include central direct drive solutions, centralized electric drive axle solutions, and distributed drive solutions. Leveraging high-performance PMSM motors with superior power density, compact dimensions, and low operating noise, our EV systems enhance vehicle integration efficiency. Additionally, based on customer and project needs, we provide either standalone MCUs or integrated multifunction controllers.
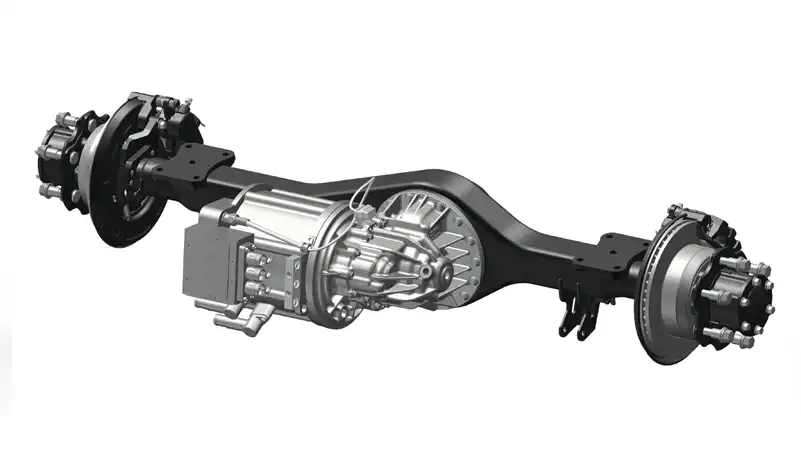
The electric drive axle is a highly integrated e-powertrain system that incorporates electric motors directly into the axle, eliminating traditional components like the driveshaft. This streamlined design enhances energy efficiency and reduces mechanical complexity.
For heavy-duty vehicles, the electric axle optimizes vehicle layout, allowing for better battery placement and extended driving range, while also lowering maintenance costs for end customers.
Centralized eAxle Configuration
Centralized eAxle Configuration
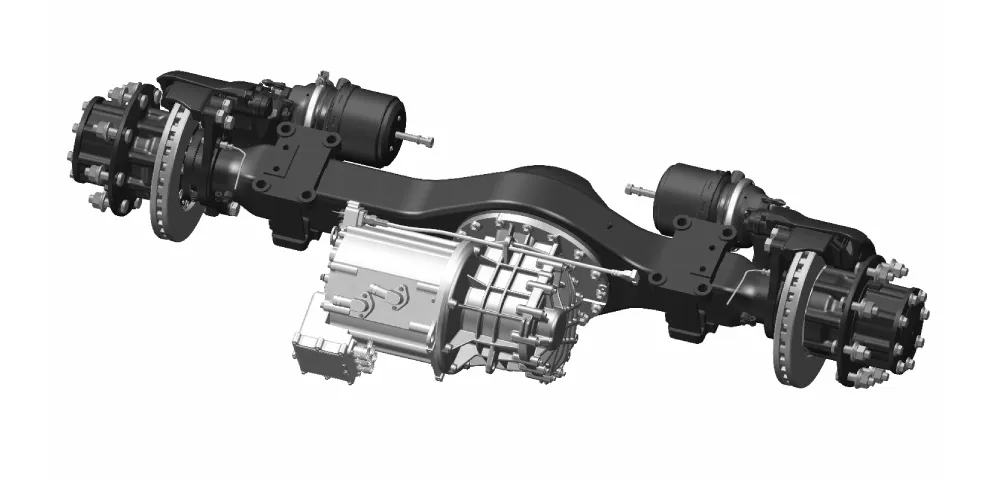
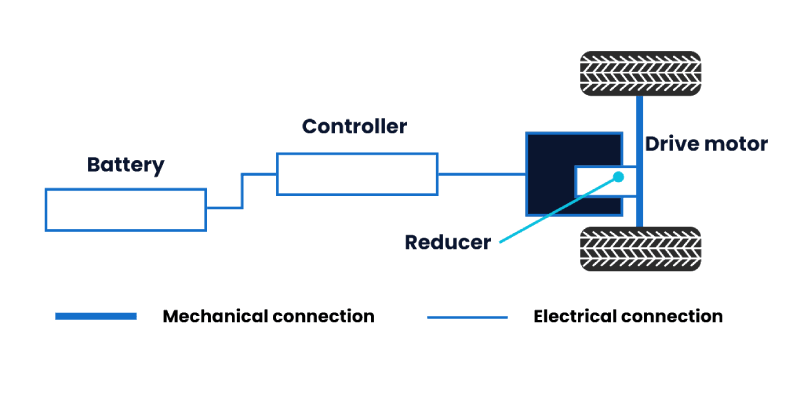
Solution Features
Compact Design
The motor, gearbox, and axle utilize a highly integrated parallel-axis design, resulting in a lightweight system with high transmission efficiency.
Improved NVH Performance
The gearbox is engineered for all operating conditions, featuring in-house manufactured DIN 4-grade high-precision gears, ensuring low noise levels.
Flexible Vehicle Layout
By eliminating the driveshaft, the chassis provides additional space for battery placement, allowing for a more flexible vehicle layout.
Advanced Technology
- High load-bearing capacity with reduced weight, minimizing the risk of oil leakage.
- Integrated gear housing design reduces oil leakage risks, while the smooth curved internal surface minimizes oil churn losses.
- High-precision two-stage helical cylindrical gear transmission with double-sided precision grinding for superior efficiency, lower noise, and extended lifespan.
- Reduced motor offset relative to the axle housing decreases the risk of oil leakage at the reducer joint.
Distributed Drive eAxle Configuration
Distributed Drive eAxle Configuration
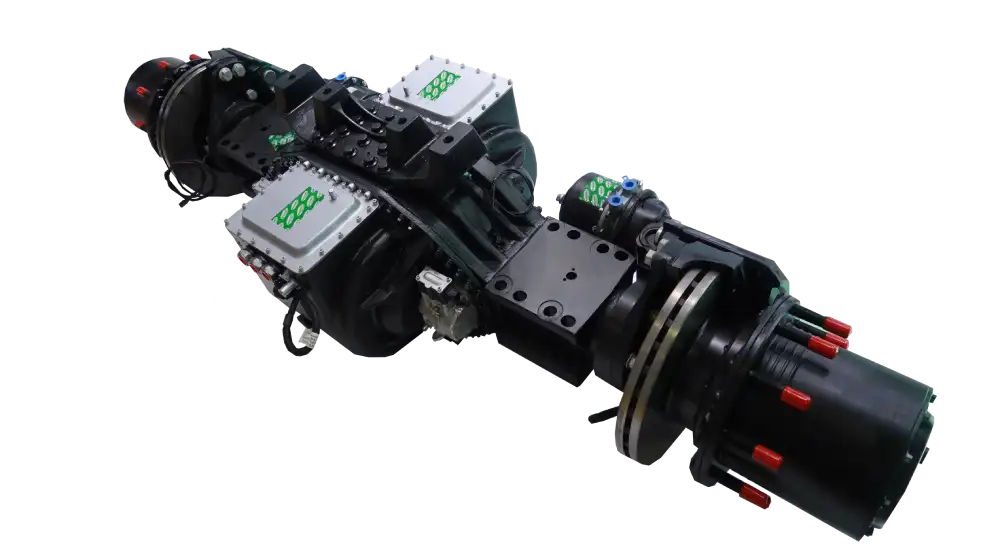

Solution Features
Short Transmission Chain
The distributed drive eAxle solution ensures each motor drives one wheel, significnatly shortening the transmission chain, minimizing transmission loss and maximizing efficiency..
Compact Structure
The distributed drive axle systems save space and contribute to a more compact vehicle structure.
Improved Tire Grip Distribution
The distributed eAxle enables individual adjustment of motor torque, optimizing the grip distribution, enhancing vehicle handling and driving stability, providing a safter and more controlled driving experience.
Enhanced Drive Efficiency
Aligning the motor's optimal efficiency range with the vehicle's operate at peak performance.
Advanced Technology
- Integrating two electric motors with the axle for strong power and additional safety redundancy.
- Equipped with EDS, EASR, IESS, and other safety configurations to increase vehicle safety and stability in harsh environments.
- The integrated design of the electric truck axle lowers the gravity center of the battery system, increasing the stability of the whole vehicle.
- Distributed drive approach adds additional safety redundancy to the vehicle, offering a flexible power distribution strategy for different working conditions.
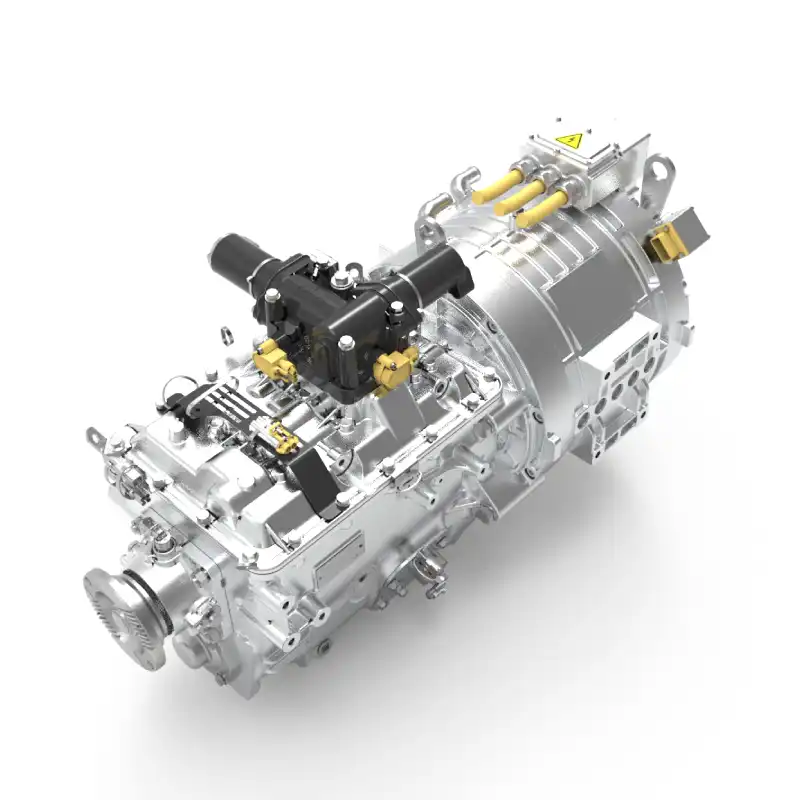
Direct Drive Motor
Central Direct Drive Motor
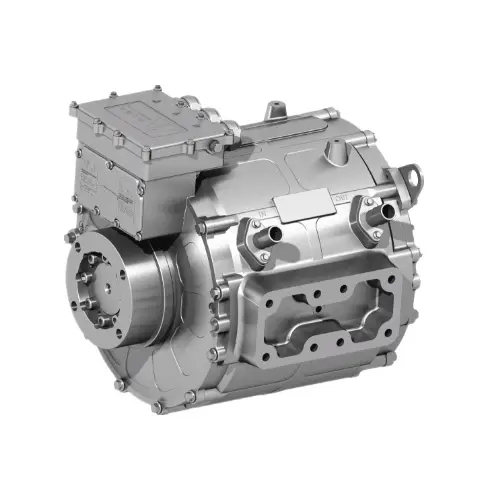
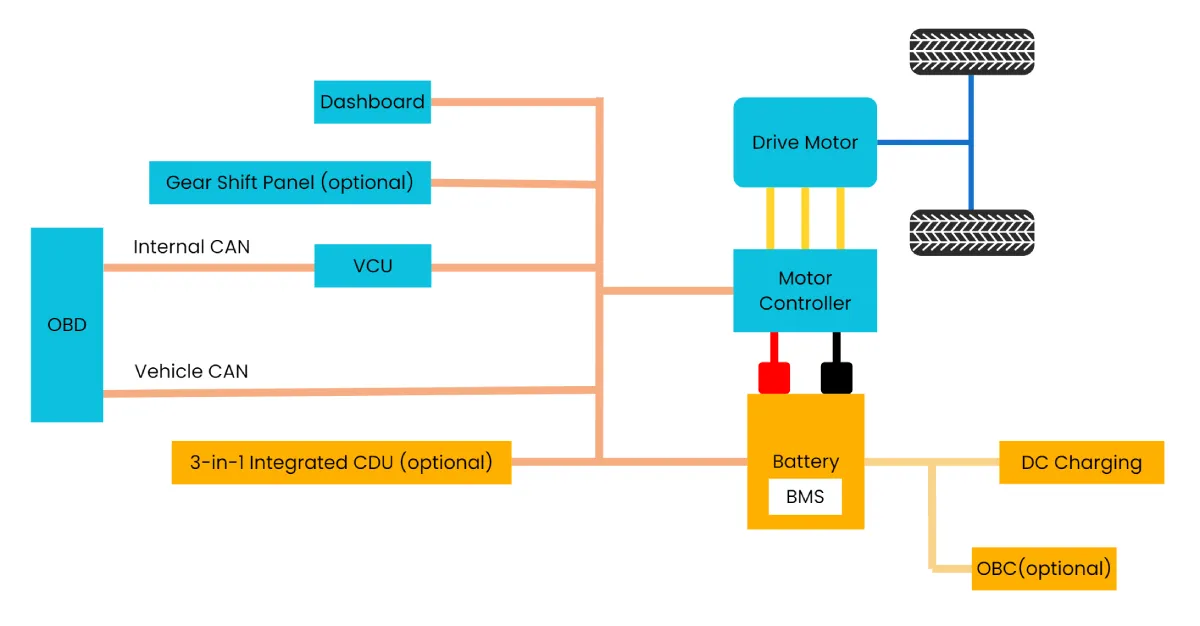
Solution Features
Easy Conversion
Ideal for retrofitting traditional fuel vehicles with minimal modifications and low risk.
Cost-Effective & Fast Development
Short development cycle with manufacturing costs similar to conventional vehicles.
High Efficiency
Over 95% peak efficiency with a broad high-efficiency range for optimal performance.
Wide Applicability
Suitable for heavy-duty trucks, tractors, mining trucks, garbage trucks, and more.
Advanced Technology
- Utilizes advanced designs such as thin silicon steel laminations, high magnetic permeability materials, and sinusoidal air-gap flux density optimization.
- Features rotor segmented skewing and optimized auxiliary slot parameters at the rotor's outer edge, effectively reducing motor noise.
- Incorporates a dual-helical water channel design to enhance heat dissipation and stability while maintaining optimal water resistance and pressure differential.
- Equipped with a flange dustproof structure to prevent mud, sand, and wastewater from entering the motor, improving long-term reliability.
Integrated E-Powertrain
Integrated E-Powertrain (Motor+Gearbox/Transmission)
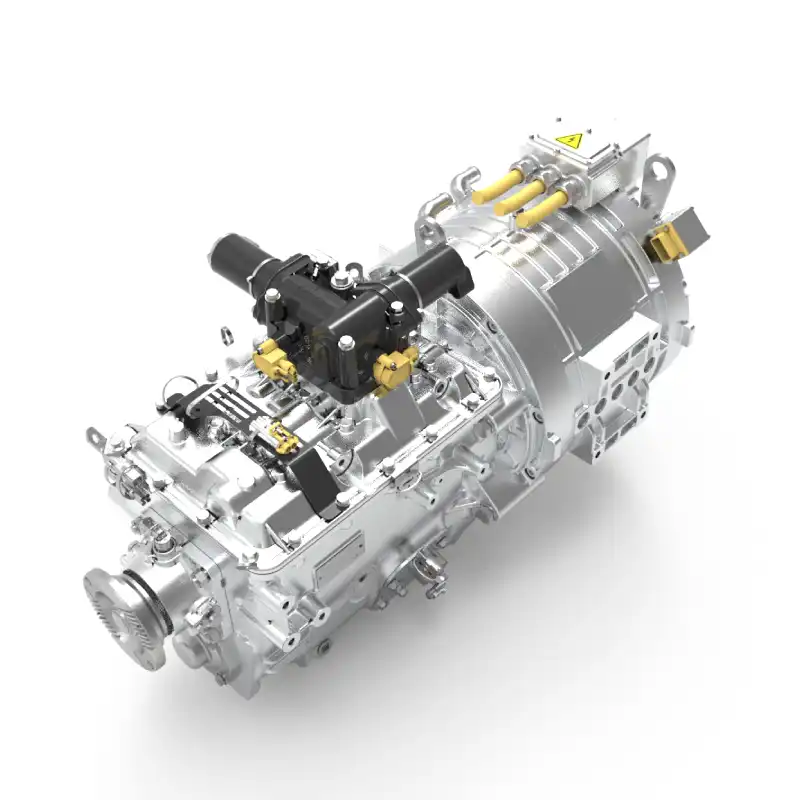
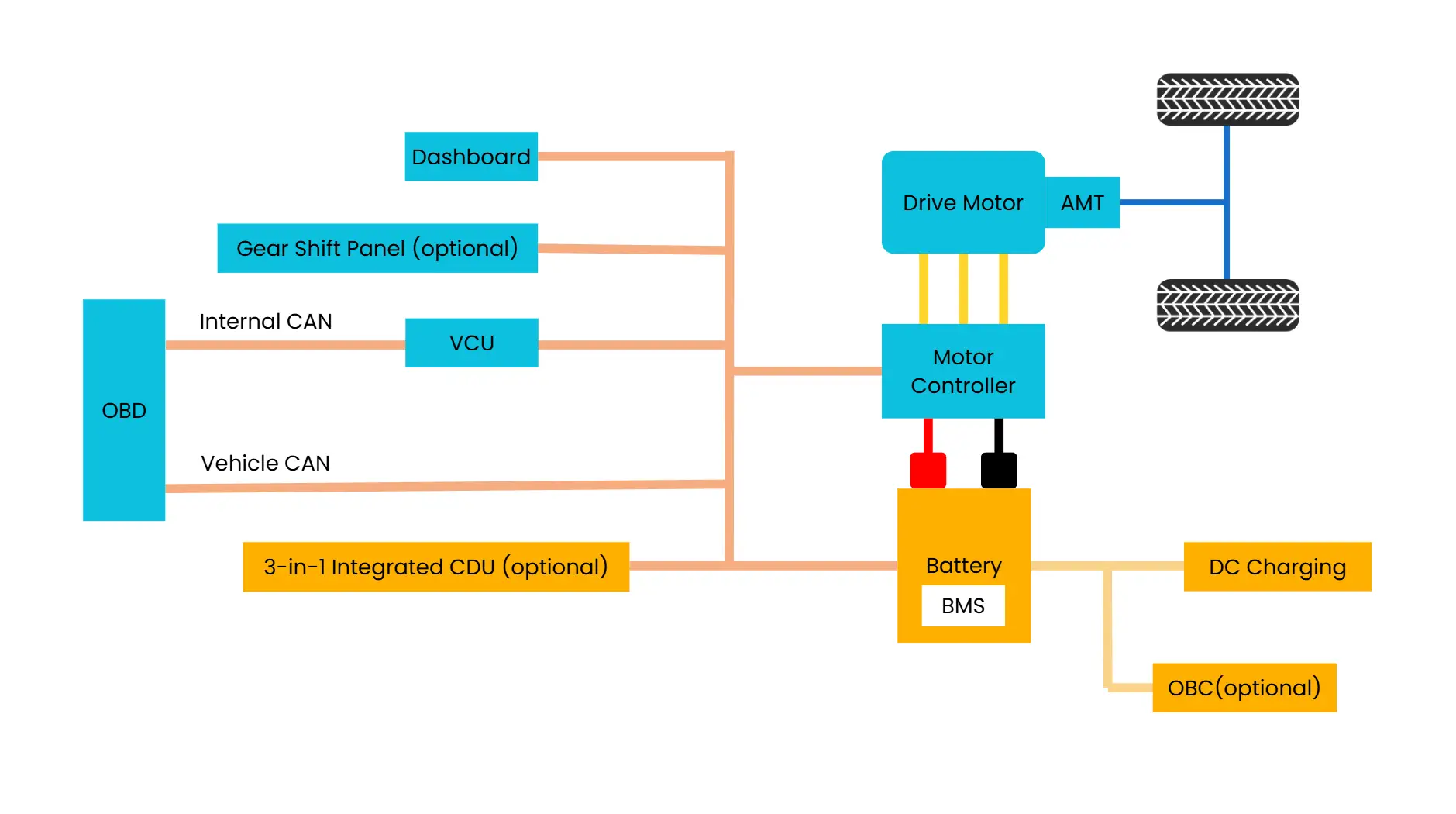
Solution Features
Powerful & Smooth Performance
The multi-speed transmission enables fast and seamless shifting, eliminating jolts during gear changes. High output torque improves climbing capability, while the powerful motor ensures strong acceleration.
Automated AMT Transmission
The AMT transmission shifts gears automatically based on vehicel speed and motor RPM, eliminating the complexity of manual shifting and enhancing driving comfort.
Flexible PTO System
The power take-off (PTO) system is optional and can be tailored tto specific vehicle needs. Integrating PTO into the drivetrain reduces additional installation costs.
Proven Track Record
Developed with globally recognized transmission manufacturers, the system has undergone road trials, ensuring durability and real-world validation.
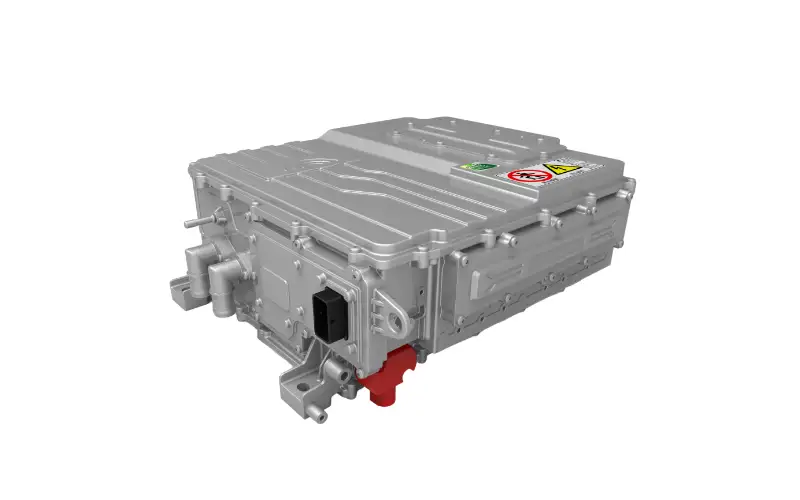
We can offer standalone Motor Control Units (MCU) or high-voltage integrated controllers customized to client requirements, integrating MCU, PDU, DC-DC, and steering and braking DC/AC.
Advanced Technology
- Dual integration design: combines functional and physical integration to reduce size and weight while lowering manufacturing costs.
- High-efficiency dual inverter control: reduces energy losses and achieves a peak controller efficiency of 98.5%.
- Advanced filtering & shielding: features multi-stage filtering, optimized wiring layout, enhanced structural processing, and reinforced enclosure shielding for improved electromagnetic compatibility.
- Modular & scalable architecture: designed with a modular and platform-based approach, allowing greater flexibility and expandability.
- Digital simulation & optimization: utilizes digital modeling for simulation analysis, enabling more versatile and cost-effective component selection.
EV Battery
For heavy duty vehicles, we provide tailored EV battery solutions based on specific customer requirements. Our comprehensive solutions encompass battery packs, battery management systems (BMS), battery thermal management systems (BTMS), and cloud-based services for full lifecycle management.
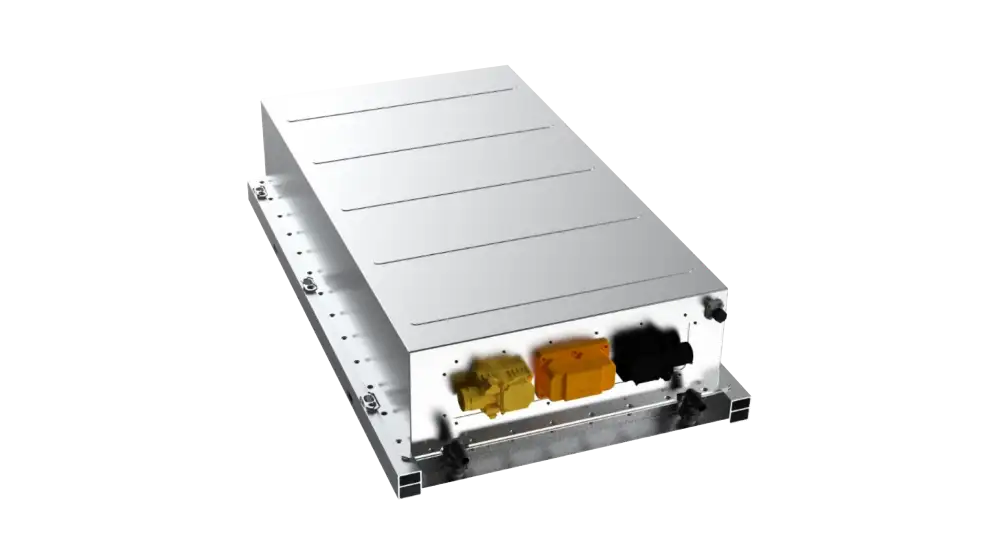
Our standardized EV battery packs are widely deployed across various applications. These packs are built using high-quality, industry-standard materials and proven manufacturing processes. With a standardized and modular design, we optimize the battery system structure layer by layer, achieving energy density levels that surpass the industry average for both battery modules and complete packs.
Solution Features
High Safety & Reliability
Built on a high-safety LFP system, with battery cells sourced from top-tier manufacturers such as CATL, EVE, and Gotion. The robust pack design meets relevant safety standards.
Wide Capacity Options
Offer multiple battery capacity configurations to meet diverse market demands, including extended range and high-load applications.
Lightweight & High Energy Density
Optimized design achieves an energy density of ≥140 Wh/kg, enhancing vehicle efficiency.
Superior Temperature Adaptability
Can be equipped with liquid cooling or heating systems based on customer requirements, ensuring reliable performance in extreme heat or cold conditions.
Strong Mechanical Protection
Features IP67-rated protection, making it highly resistant to harsh environmental conditions.
Advanced Technology
- Independently designed pack integration structure, adaptable to various battery cells and capacity requirements.
- Custom-designed electrical circuits and component selection, with in-house electrical testing capabilities to ensure compliance with industry standards.
- Highly integrated safety system, including harnesses, aluminum busbars, temperature sensors, internal pack pressure monitoring, explosion-proof valves, electrolyte leakage detection, and BMS collection boards, providing comprehensive and reliable active safety protection.
- Thermal runaway protection: equipped with insulation barriers between battery cells. If a cell reaches 900°C due to thermal runaway, the safety valve automatically releases pressure to prevent further hazards.
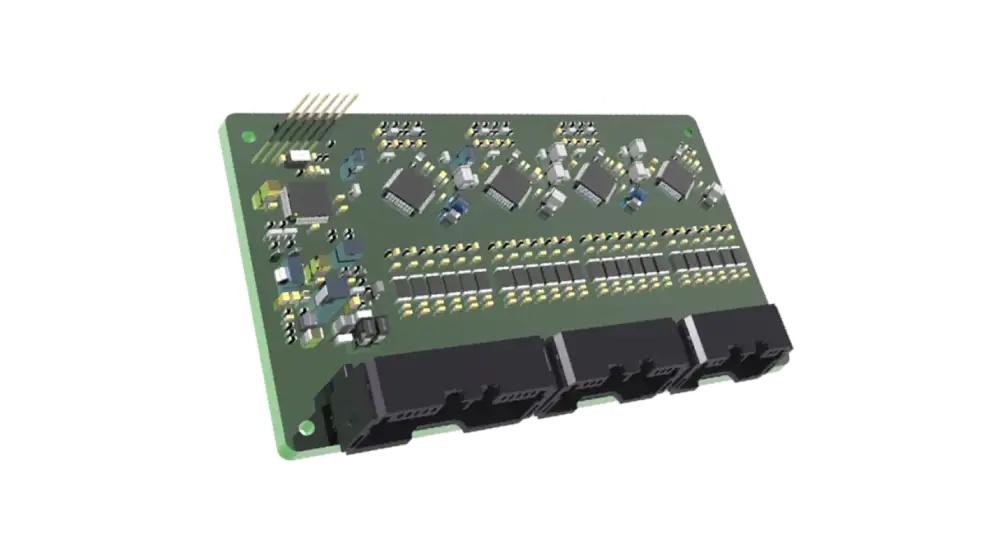
The Battery Management System (BMS) is a critical component designed to monitor and manage battery performance. Working alongside battery cells, the BMS acts as the system’s intelligent monitoring unit to ensure safety and efficient operation. Key functions of BMS include continuously tracking essential battery parameters, preventing overcharging and over-discharging, safeguarding the battery from potential damage; and optimizing performance and longevity by maintaining optimal operating conditions.
Our R&D Capabilities
- Independently develop BMS software for battery management control.
- Custom-designed control strategies and diagnostic analysis algorithms.
- Proprietary design of controller mainboards, control circuits, monitoring circuits, and communication circuits.
Advanced Technology
- High-Precision Calculations: SOC accuracy ≤3%; SOH health assessment accuracy ≤5%.
- Three-Tier Architecture: Ensures precise battery cell management, reduces error margins, and enables full lifecycle battery management.
- High-Speed Daisy-Chain Communication: Faster data transmission, lower power consumption, enhanced stability, strong anti-interference capability, and high voltage resistance.
- High Integration: BMS and PDU integration increases battery energy density, saving approximately 30% of space and reducing weight by 10%.
- Comprehensive Smart BMS Platform: Covers the entire system, from BMS controller software to an integrated edge-side BMS+EMS system and an EMS/battery management cloud platform, ensuring full-process security and control.
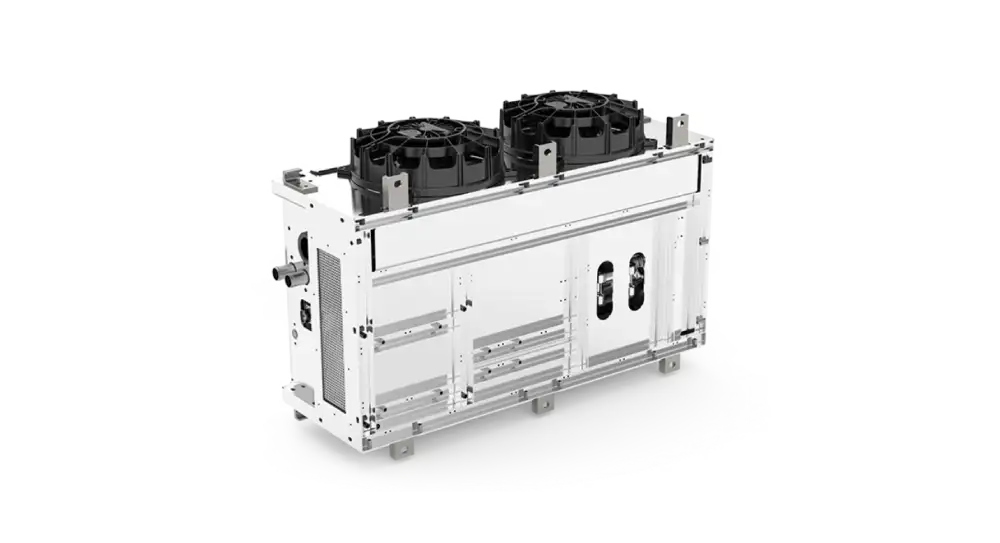
The Battery Thermal Management System (BTMS) is an integrated cooling and heating system designed to regulate the temperature of onboard batteries. The primary goal of BTMS is to keep the battery pack within an optimal temperature range, ensuring peak performance and longevity. By managing thermal energy across the vehicle, the system effectively reduces waste heat emissions, enhances energy efficiency, and minimizes environmental impact.
Solution Features
- Accurately measures and tracks battery temperature in real time.
- Effectively dissipates heat when battery temperature is high, preventing thermal runaway.
- Warms the battery in low temperatures to ensure safe and efficient charging and discharging.
- Reduces temperature differences within the battery pack, preventing localized overheating and extending overall battery lifespan.
Advanced Technology
- Aluminum alloy frame reduces weight and improves efficiency.
- Optional PTC liquid heater with standby, cooling, heating, and self-circulating modes.
- CAN bus communication for real-time fault self-diagnosis and status updates.
- Optional add-ons: tube-fin condenser, DC-DC, expansion tank.
EV Charging Solutions
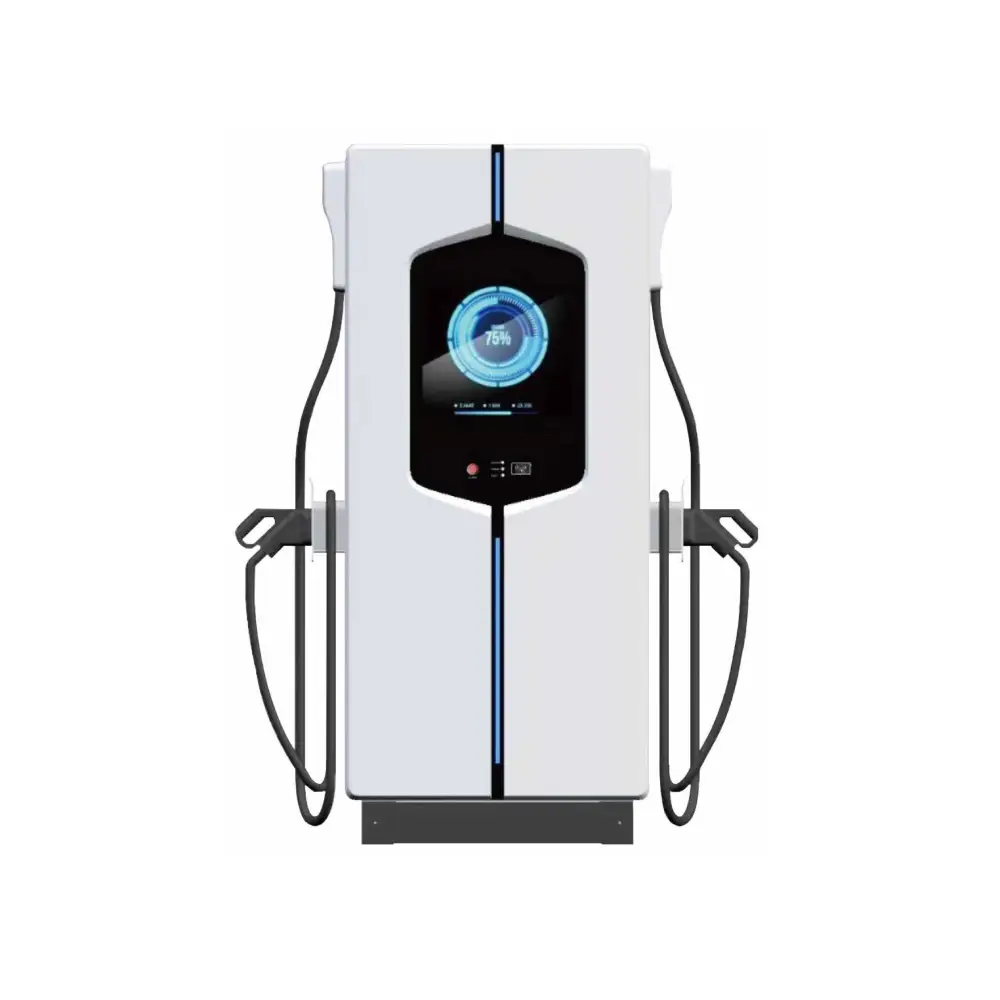
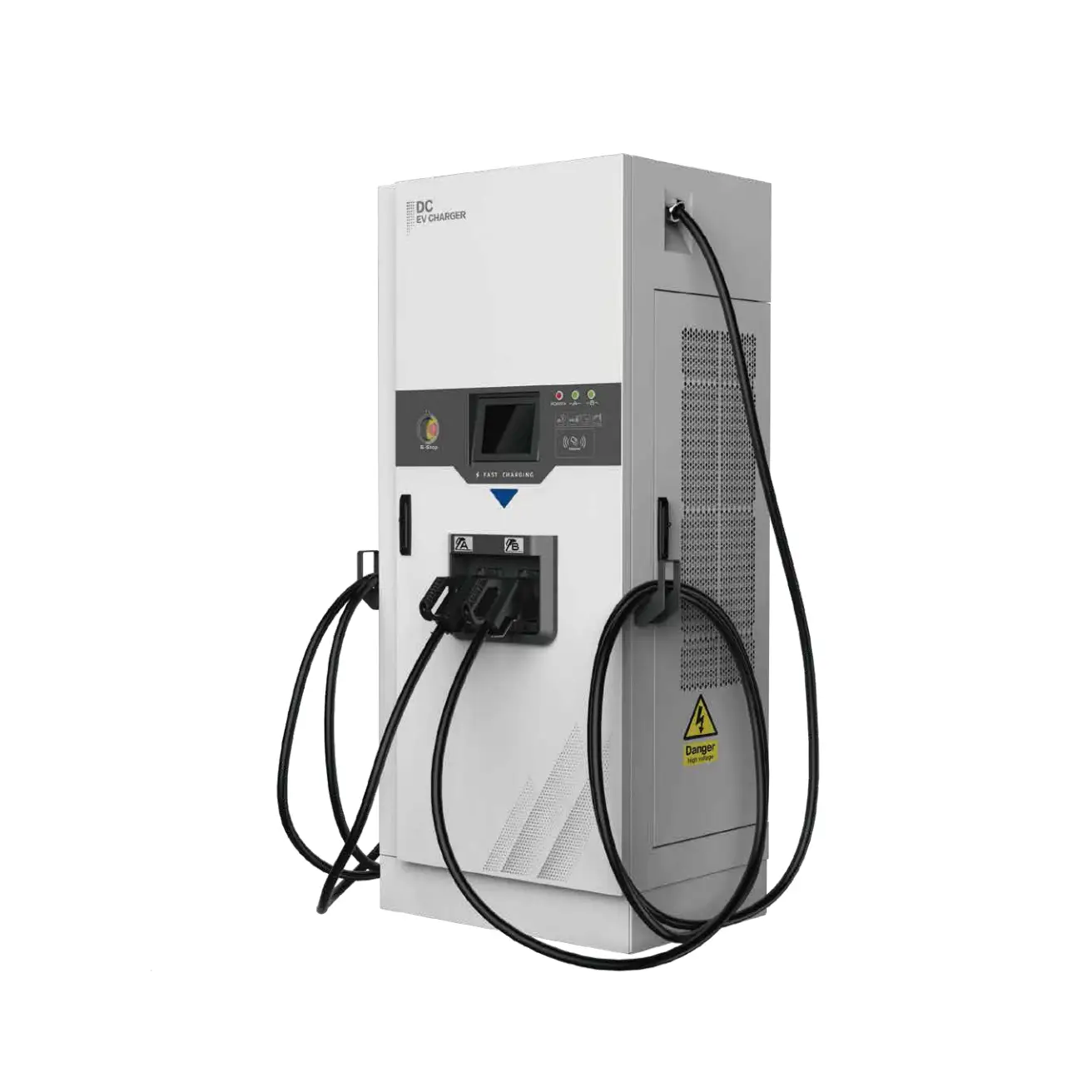
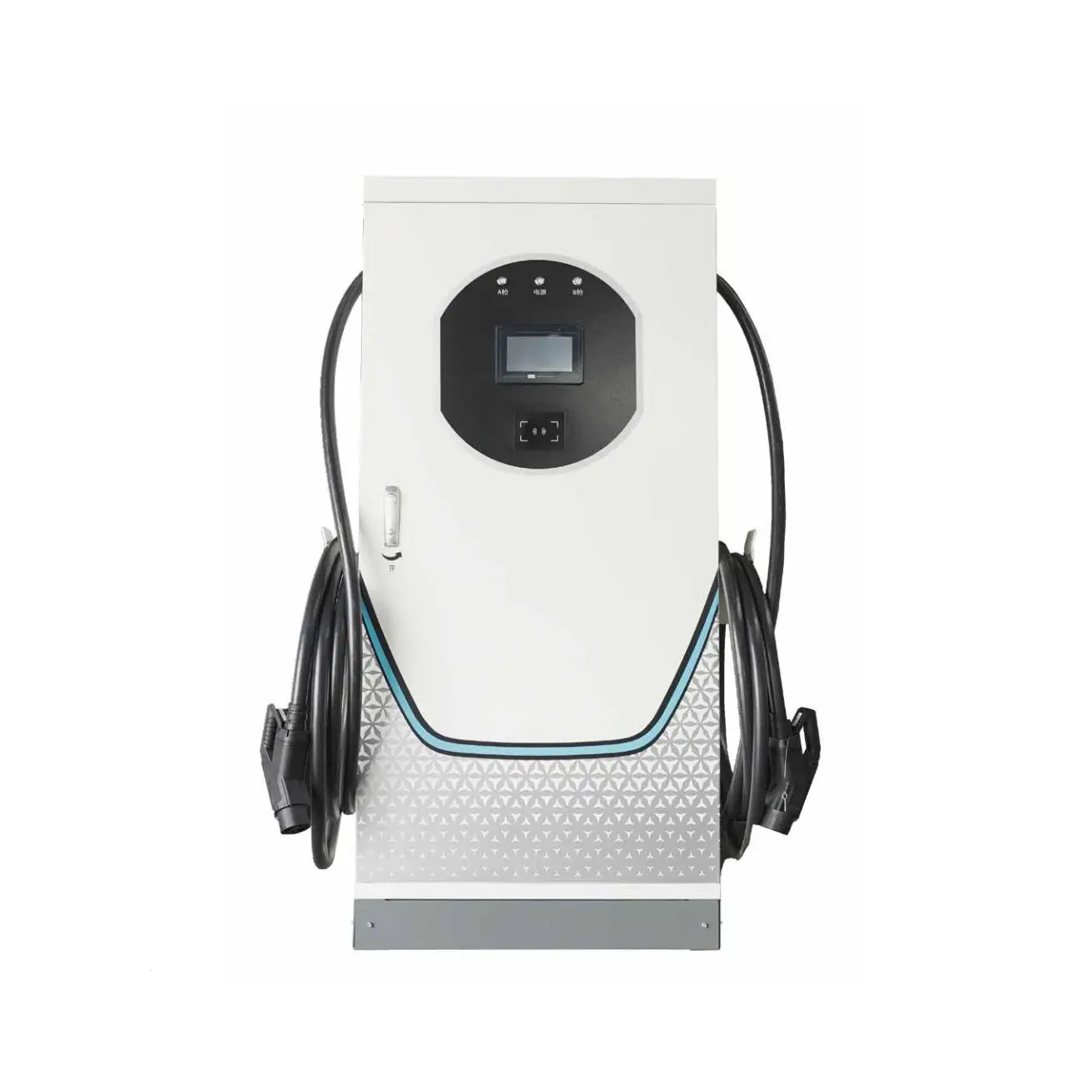
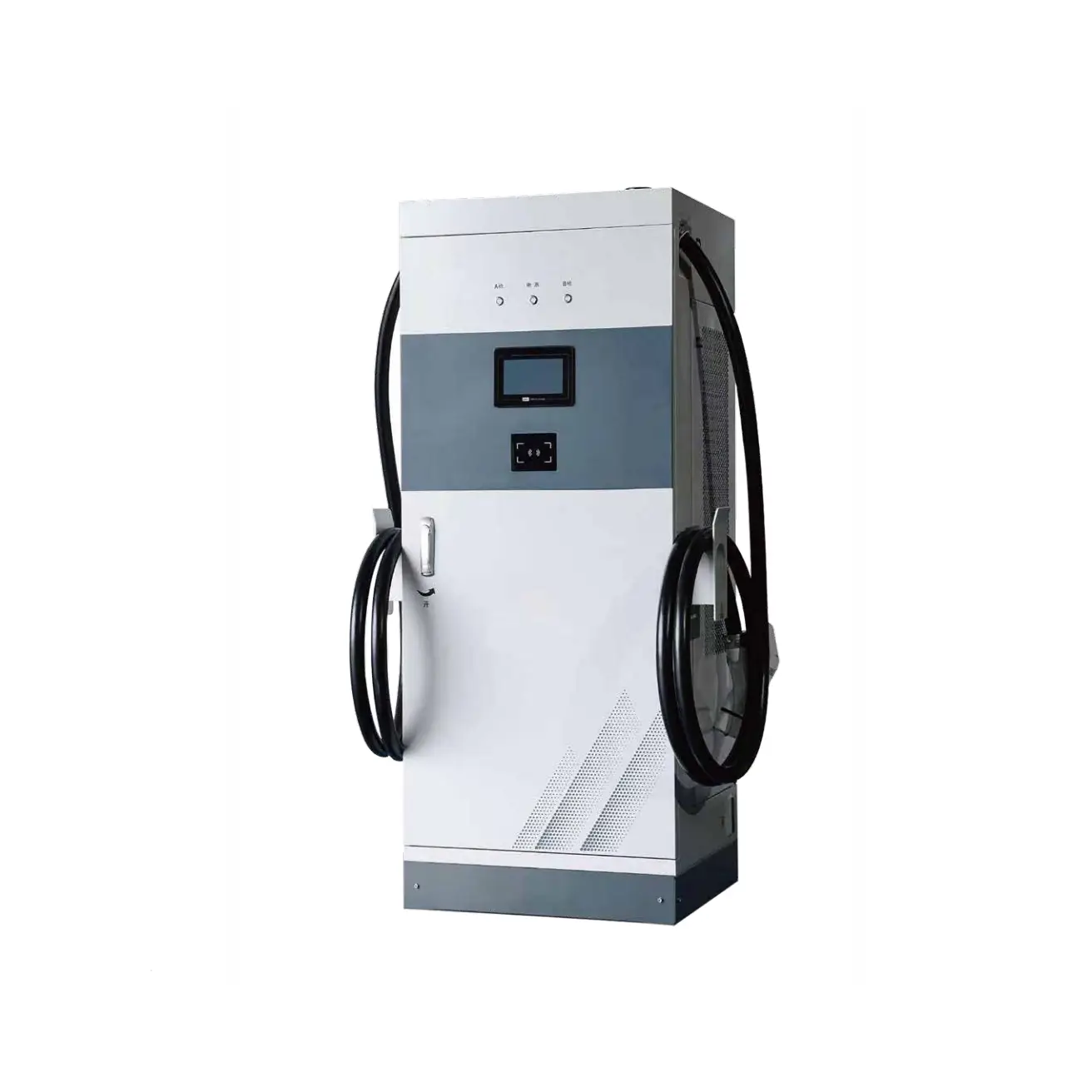
Other EV Systems for Heavy Duty Vehicles
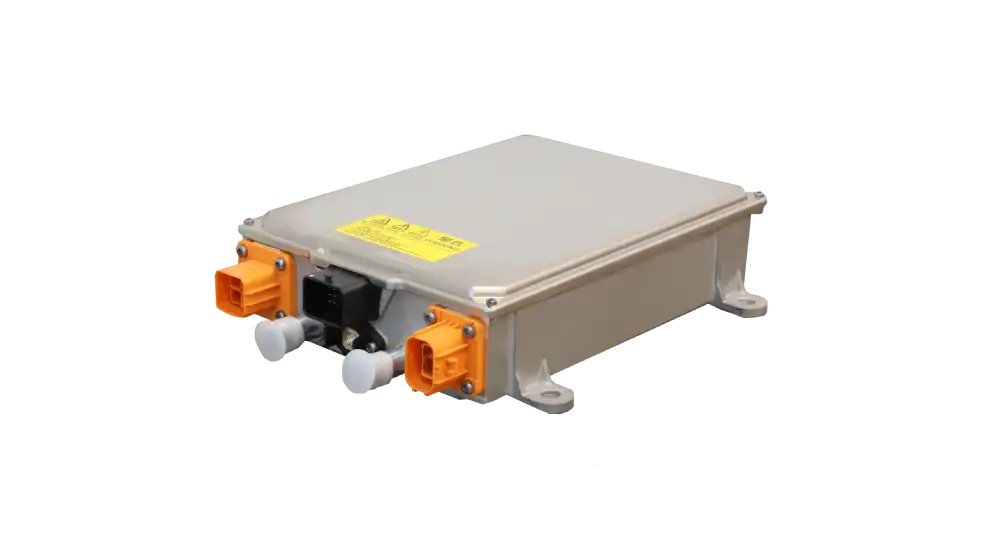
Onboard Charger, DC-DC Converter, PDU
Experience peak performance and reliability with our integrated EV on board charger (OBC), DC/DC converter, and PDU combo tailored for electric vehicles. Engineered for top-tier power conversion efficiency and remarkable power density, our chargers cover a broad power spectrum, ranging from 3.3 kW to 40 kW.
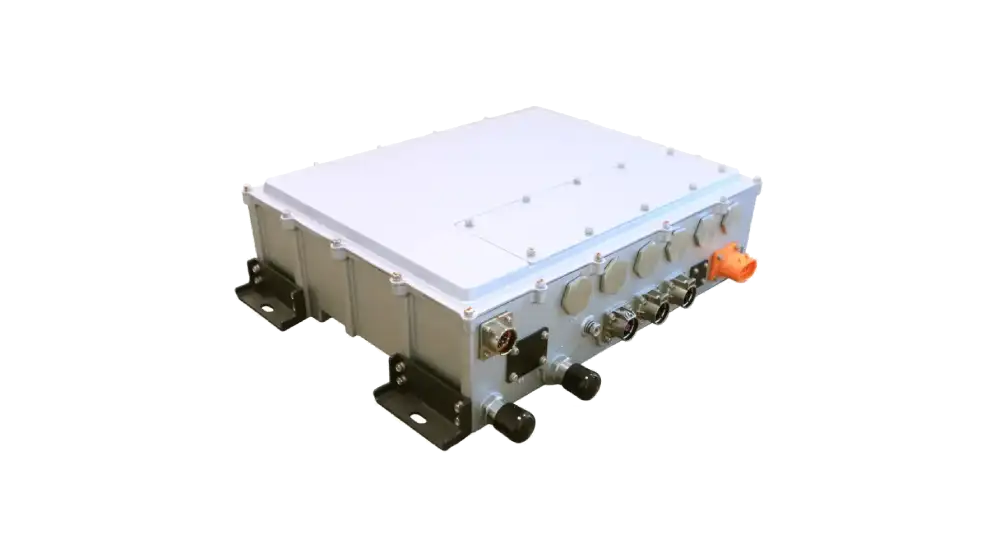
Auxiliary Inverter
We provide modular and scalable X-in-1 auxiliary inverters for public transport vehicle applications. Our auxiliary inverters cater to various types of new energy vehicles, including hybrid electric vehicles (HEV), battery electric vehicles (BEVs), and hydrogen fuel cell electric vehicles (FCEVs).
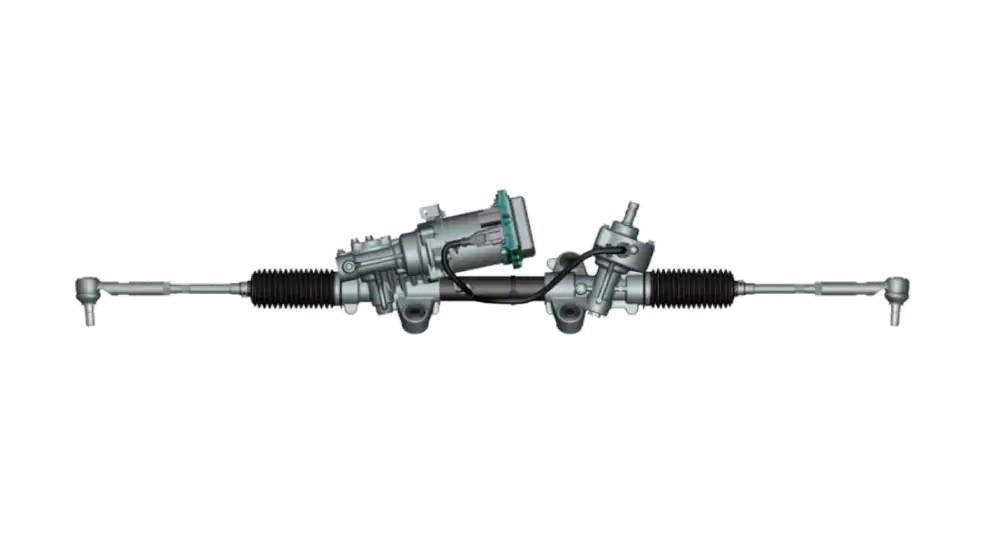
Electric Power Steering (EPS)
The Electric Power Steering System (EPS) is a type of power steering solution that uses an electric motor to assist the driver in steering. We offer various EPS systems based on the positioning of the assist motor, including C-EPS, P-EPS, DP-EPS, and R-EPS, each designed to meet the specific needs of different vehicle types.
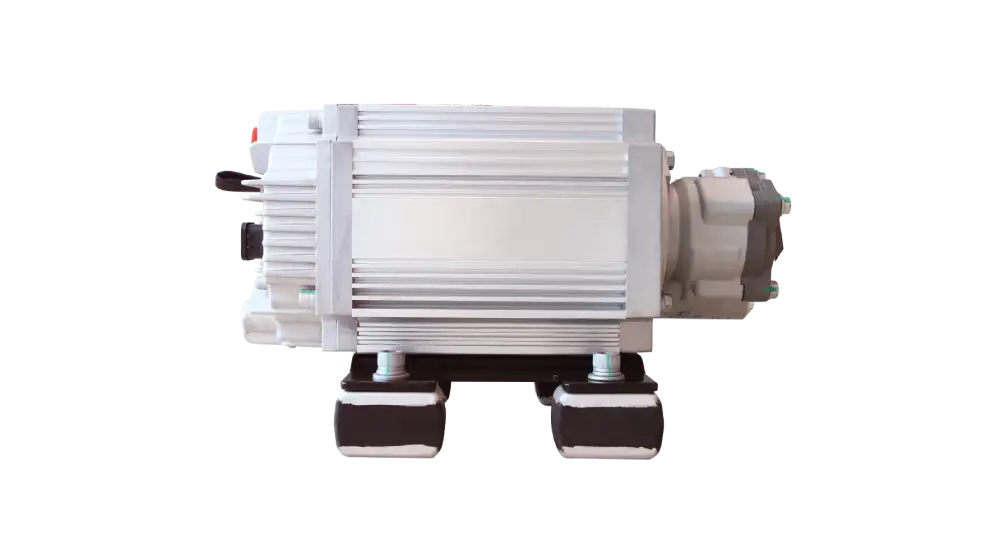
Electro-Hydraulic Power Steering (EHPS)
The Electro-Hydraulic Power Steering (EHPS) system is an upgraded version of the traditional hydraulic power steering (HPS) system. In this system, the steering pump is no longer driven directly by the engine but by an electric motor, coupled with an electronic control unit. This allows the steering assist to be adjusted not only based on the steering angle but also in response to the vehicle’s speed, providing a more efficient and responsive steering experience.
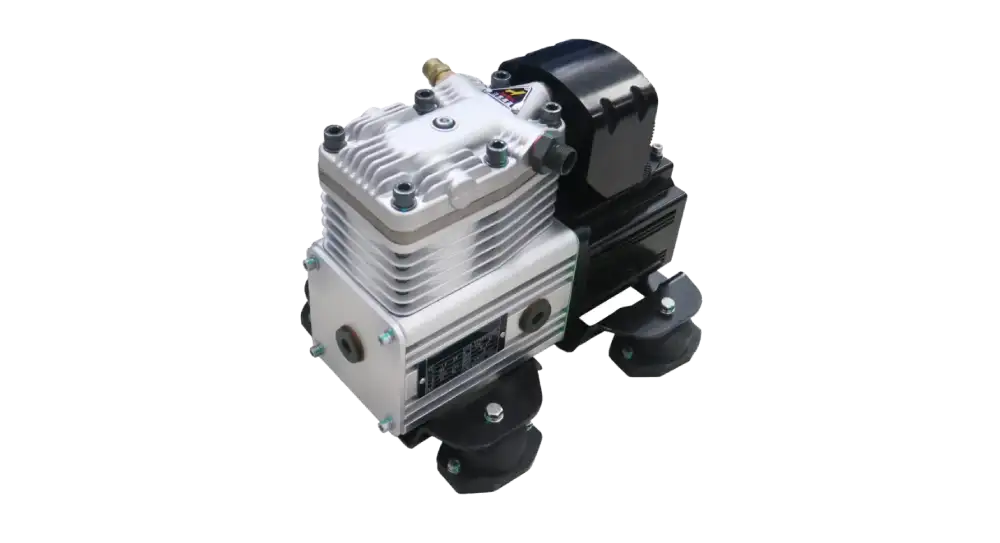
Air Brake Compressor
Our two-stage oil-free electric air brake compressors ensure the delivery of oil and water-free air, eliminating concerns associated with oil emulsification, leaks, and fire hazards. Its innovative structural design minimizes energy wastage during the compression process, thereby optimizing overall efficiency.
How We Work
Navigating Our Process
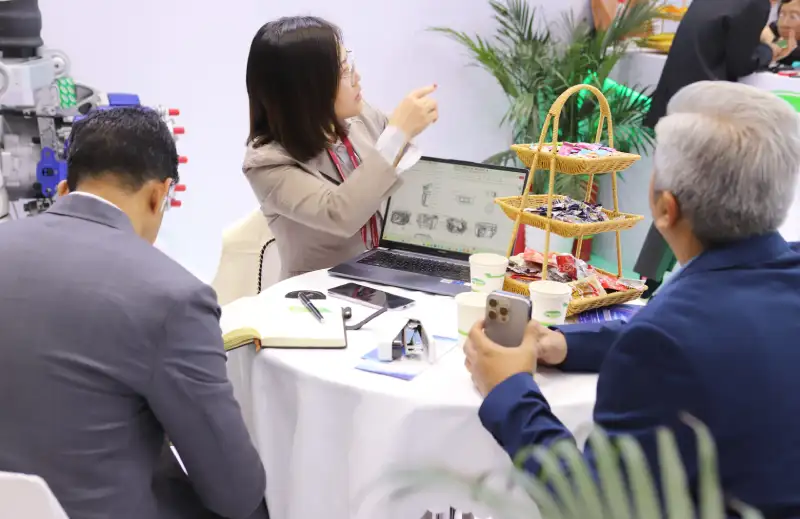
Demand Analysis & Project Evaluation
Once we receive your inquiry, our experts will connect with you within two business days to understand your specific requirements for the EV solution and conduct an initial feasibility evaluation of your project.
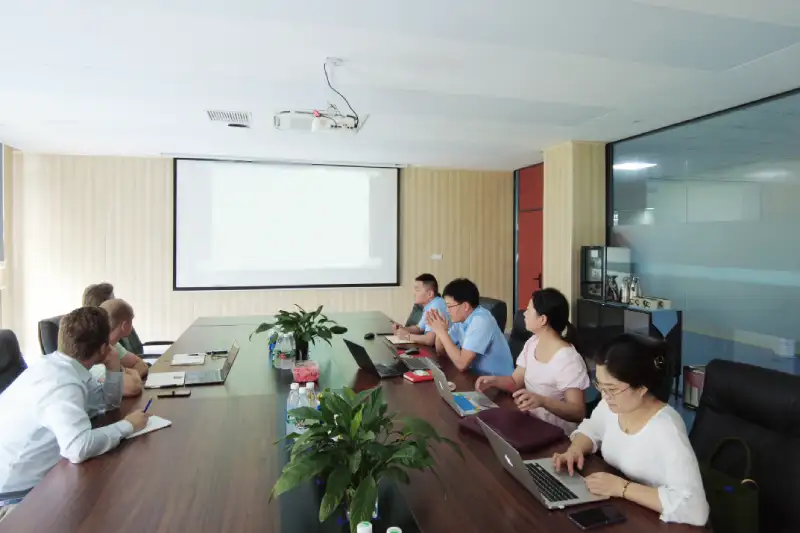
Project & Technical Coordination
If the project is deemed feasible, our engineering team will collaborate closely with your team on both hardware and software aspects to develop a viable solution. We will also provide a detailed quotation based on the technical requirements.
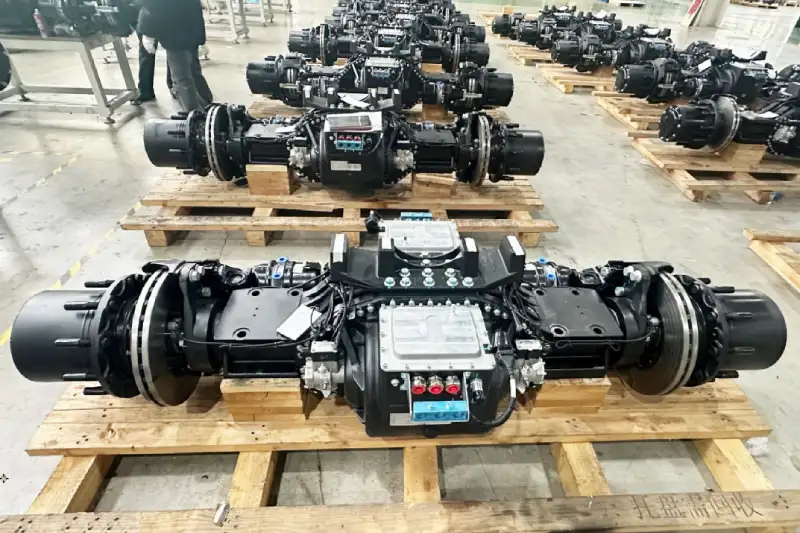
Development, Manufacturing & Testing
For customized or modified systems, we proceed with product development, including hardware and software adaptations. Our EV systems undergo rigorous testing to ensure quality, reliability, and full functionality before deployment.
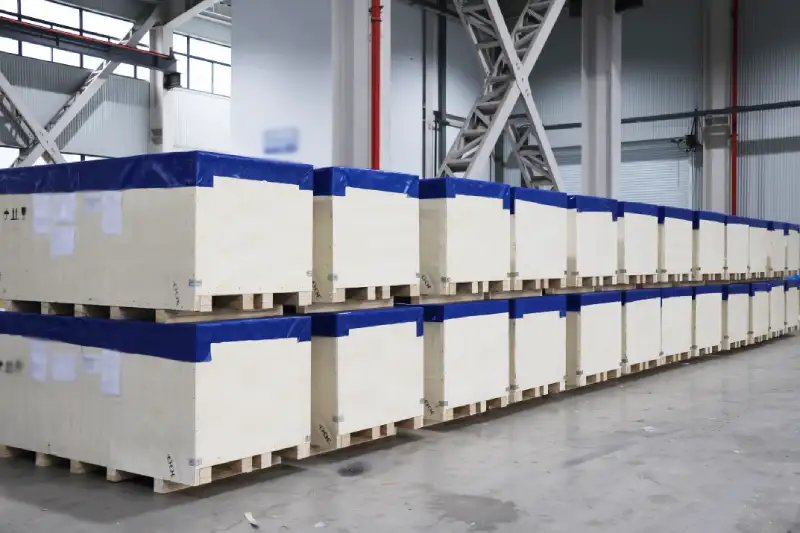
In-Time Global Shipping & Delivery
We have established strong partnerships with international shipping providers, ensuring safe and timely delivery of products to your specified location. This guarantees a smooth and efficient deployment of your EV project.
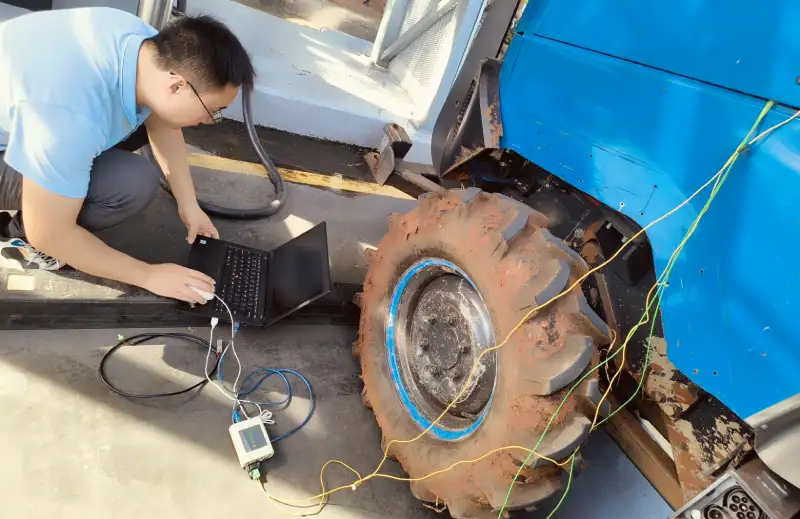
Full-Stage Remote/Onsite Technical Support
We provide technical support throughout the entire project lifecycle, including consultancy, hardware and software development, calibration, and both onsite and remote debugging, ensuring optimal performance and long-term success.
What we offer
Product Highlights
Explore our most popular and widely used systems for heavy commercial vehicles. Additional options are available upon request to meet your specific needs.
360 kW Distributed Drive Electric Axle
- Dual-motor structure and advanced gear-shifting control strategy to ensure uninterrupted power delivery
- Distributed drive approach adding additional safety redundancy to the vehicle
- Compact and lightweight design lowers the center of gravity and icnreases the stability
- Advanced core technologies such as EDS, EASR, IESS, etc.
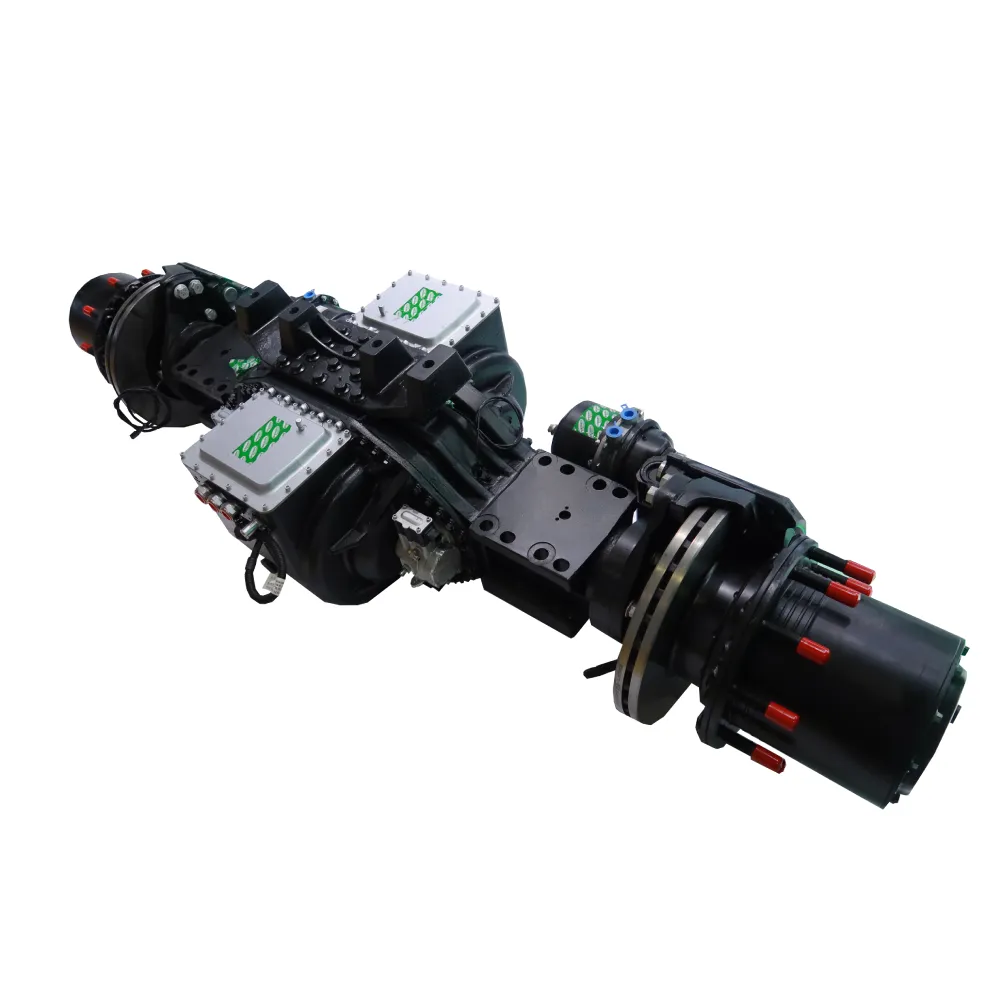
250 kW Integrated Electric Axle
- Features a maximum output torque of 40,000 N.m for demanding tasks
- Integrated design of a PMSM motor, transmission, and rear axle
- Lightweight and compact structure for improved vehicle layout
- Higher transmission efficiency due to the elimination of driveshaft
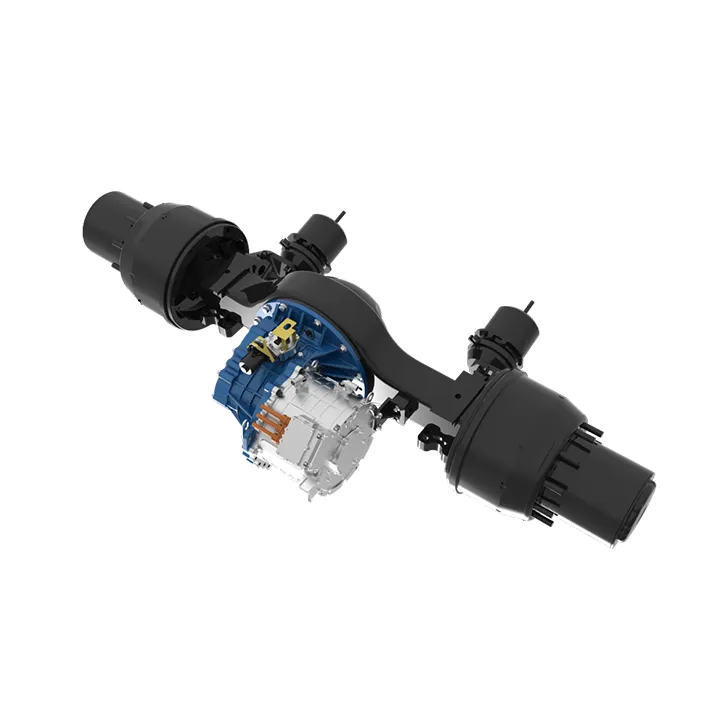
360 kW Integrated Electric Powertrain
- Integrated electric powertrain design with motor, controller, and gearbox
- Wide applications for heavy tractor, dump truck, muck truck, mining truck, etc.
- Gradient recognition gear shift strategy with digital electronic control for smooth shifting
- 6 levels / 170 safety alerts, with a dual-protection design for the controller
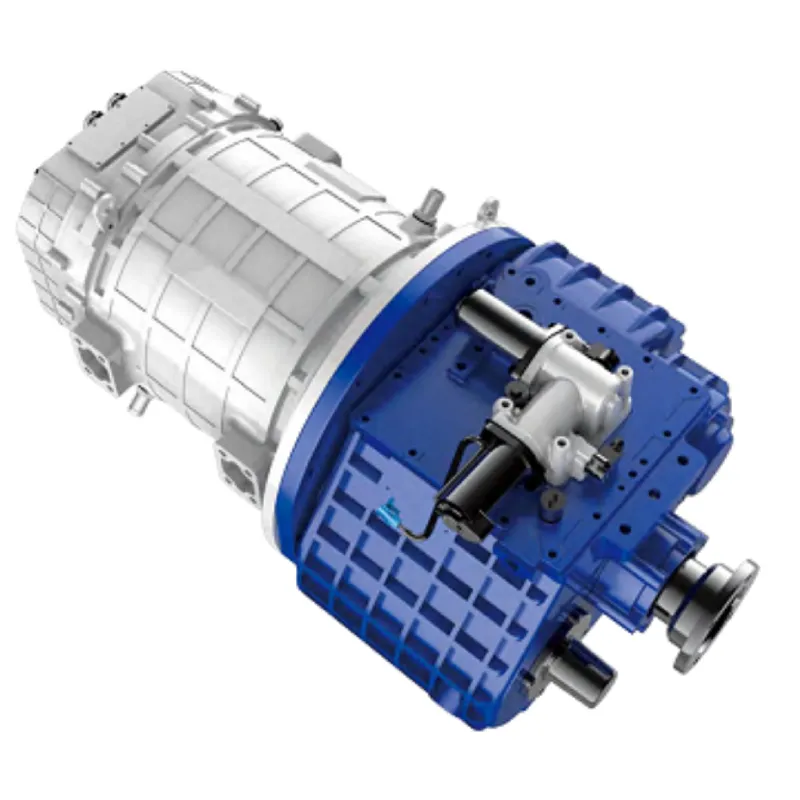
200 kW Integrated Electric Powertrain
- Integrated electric powertrain design with motor, gearbox, and controller (optional)
- Wide applications for 14 to 18-ton heavy truck, water truck, dump truck, street sweeper, etc.
- Mature applications on more than 100 electric truck modesl and sales of 4,500 sets
- Compact design for improved vehicle layout and higher energy efficiency
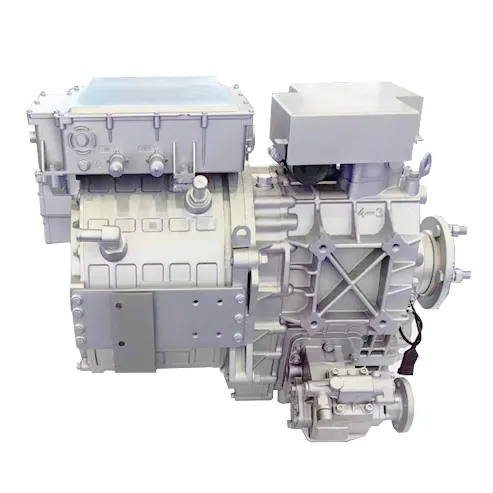
500 kW Direct Drive Motor
- The maximum motor efficiency exceeds 97%
- The motor's no-load noise level is kept below 75 dB
- Dual-spiral water channel design for improved cooling capability and stability
- Wide applications for heavy trucks and municipal vehicles
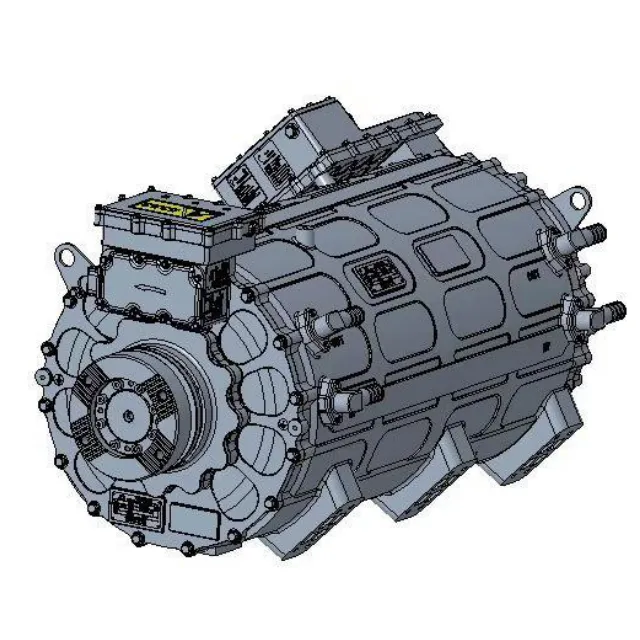
Standardized LFP Battery Pack
- Independent slave control: simplifies installation and maintenance
- Integrated liquid cooling: strong adaptability in high-temperature environments
- All-aluminum casing: lightweight design with high energy density
- Protection level: IP67
- Standard equipped with heating film
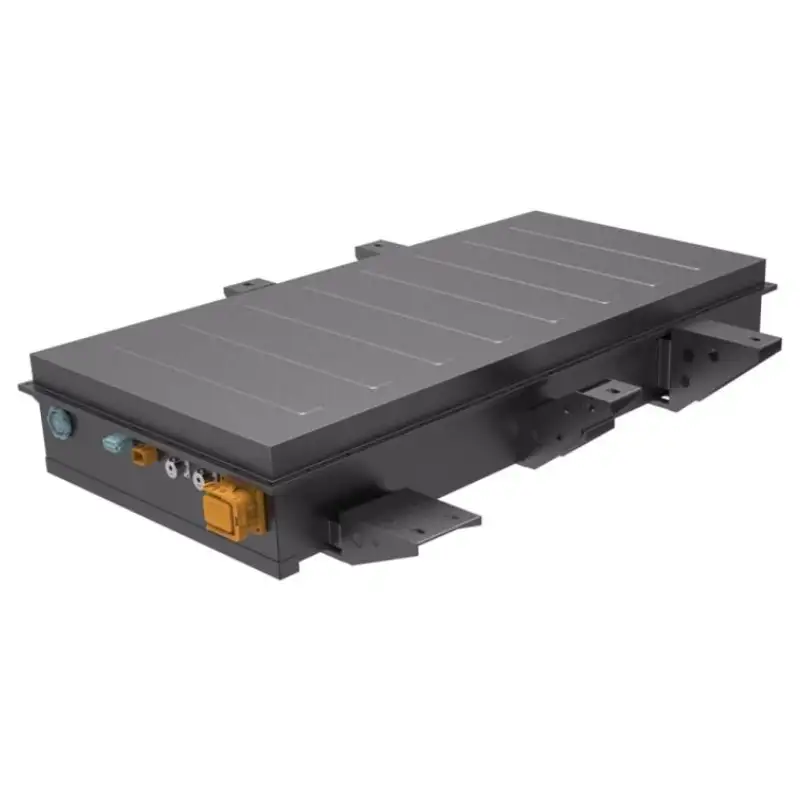
Dimension (mm) | 1060*630*240 | ||||
Cell Capacity (Ah) | 105 | 173 | 230 | 280 | 304 |
Battery Packing Scheme | 2P48S | 1P63S | 1P48S | 1P36S | 1P36S |
System Capacity (Ah) | 210 | 173 | 230 | 280 | 304 |
Nominal Voltage (V) | 153.6 | 202.86 | 153.6 | 115.2 | 115.2 |
Energy (kWh) | 32.256 | 35.095 | 35.328 | 32.256 | 35.02 |
Blade Battery Pack
- CTP (Cell-to-Pack) design, bypassing the need for battery modules
- Reduced pack size, more flexible space for easier layout
- Higher energy density for longer cruising range
- Stacked design provides more uniform current density and superior internal heat dissipation
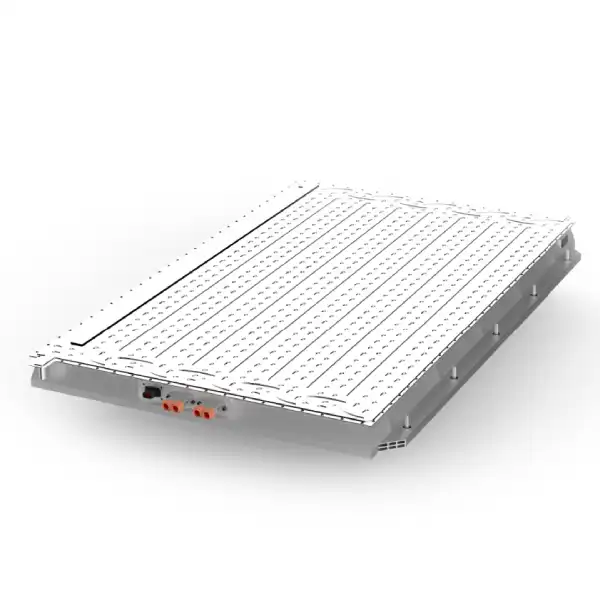
Pack | Energy | Voltage | Cell capacity | Size |
B01 | 10 kWh | 102.4 V | 100 Ah | 660*840*130 mm |
PC5 | 24 kWh | 243.2 V | 100 Ah | 1238*840*235 mm |
B04 | 35 kWh | 352 V | 100 Ah | 1000*840*210 mm |
B05 | 42.3 kWh | 313.6 V | 135 Ah | 1120*880*210 mm |
B06 | 44.9 kWh | 332.8 V | 135 Ah | 1120*880*210 mm |
B07 | 50 kWh | 332.8 V | 150 Ah | 1120*880*210 mm |
B10 | 41.6 kWh | 268.8 V | 155 Ah | 1560*470*240 mm |
B11 | 22.6 kWh | 128 V | 177 Ah | 920*470*240 mm |
B12 | 27.1 kWh | 156.3 V | 177 Ah | 1060*470*240 mm |
B13 | 18.3 kWh | 381.6 V | 48 Ah | 1246*578*226 mm |
B20 | 76 kWh | 230.4 V | 330 Ah | 1900*627*240 mm |
B21 | 75 kWh | 307.2 V | 244 Ah | 1900*627*240 mm |
B22 | 66.5 kWh | 201.6 V | 330 Ah | 1700*627*240 mm |
B23 | 65.6 kWh | 268.8 V | 244 Ah | 1700*627*240 mm |
B24 | 96 kWh | 601.6 V | 160 Ah | 2000*690*270 mm |
3-in-1 / 4-in-1 Auxiliary Inverter
- Integrated design with a DC/DC converter, two DC/AC inverters, and a PDU
- Compact and lightweight to improve vehicle layout
- Quiet operation with minimal disruption at less than 42 dB
- Versatile applications across diverse work conditions, including challenging environments
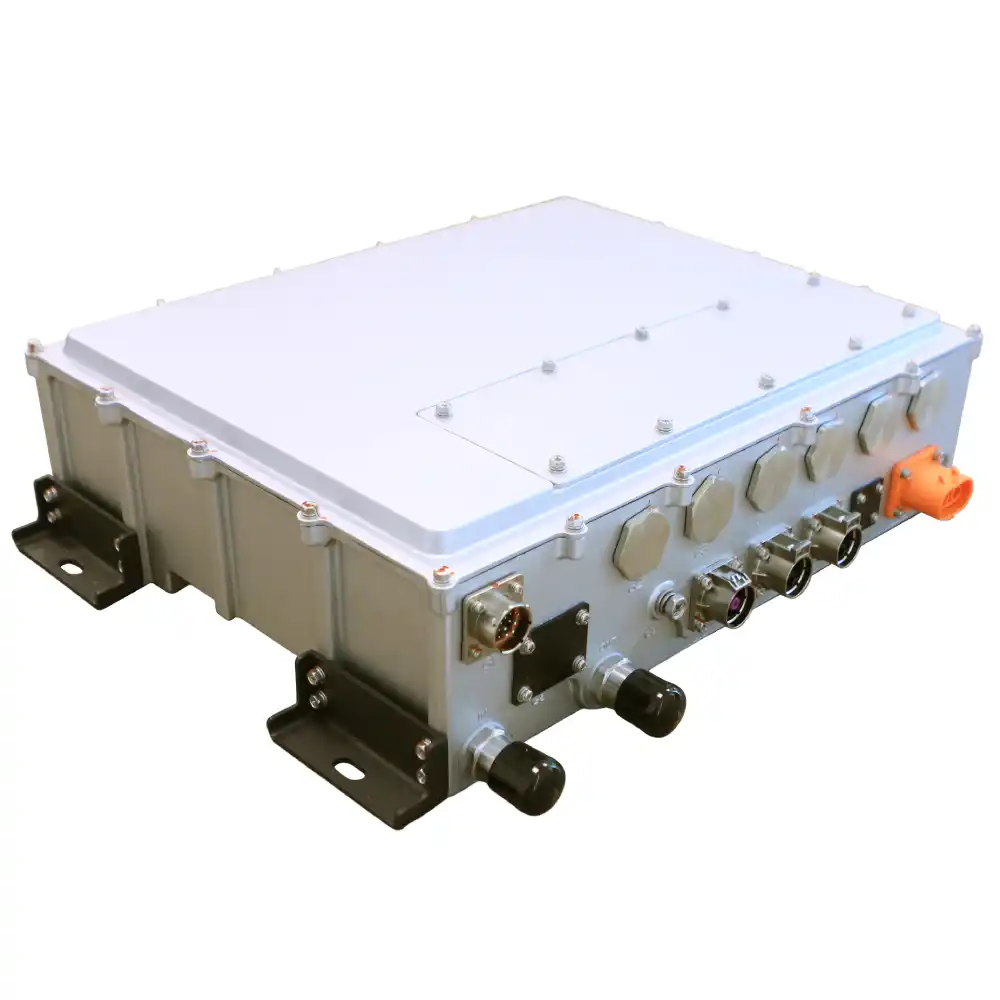
20 kW Liquid-Cooled Onboard Charger
- Liquid-cooling
- Compact and lightweight design for easy installation into various vehicle platforms
- Constant power and constant current charging capabilities
- Vibration-resistant with an IP67 rating
- DC high voltage interlock loop (HVIL) protection
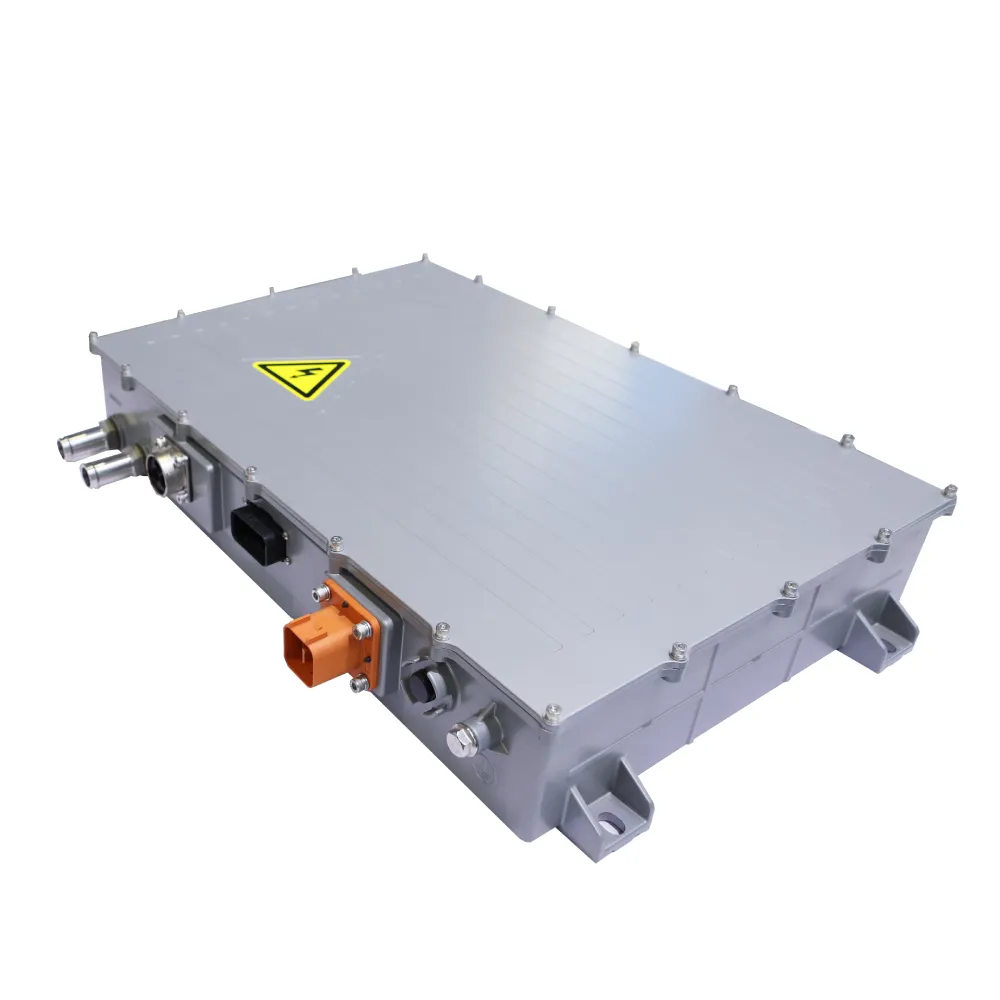
Dual-Power Source Electro-Hydraulic Power Steering System
- Additional safety redundancy due to the dual-power functionality
- The high-voltage and low-voltage circuits are completely independent
- Lightweight and designed for easy installation within the vehicle chassis
- Communication terminal provide feedback on operational parameters for real-time monitoring
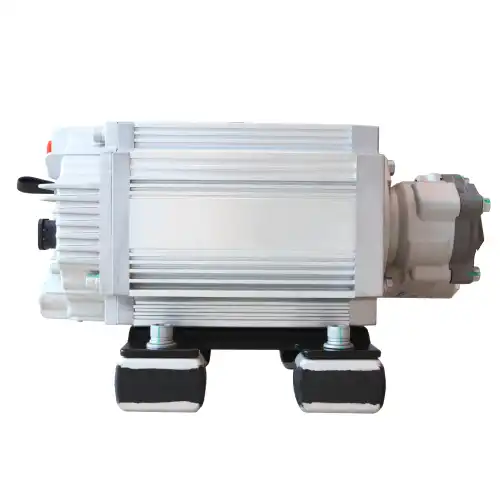
Oil-Free Piston Air Brake Compressor
- Self-lubricating materials for oil-free compression and no pollution
- Two-stage compression system for high efficiency, low energy consumption, and exceptional reliability
- Advanced noise reduction technology for minimal operational noise
- Compact design for easy installation and convenient chassis layout
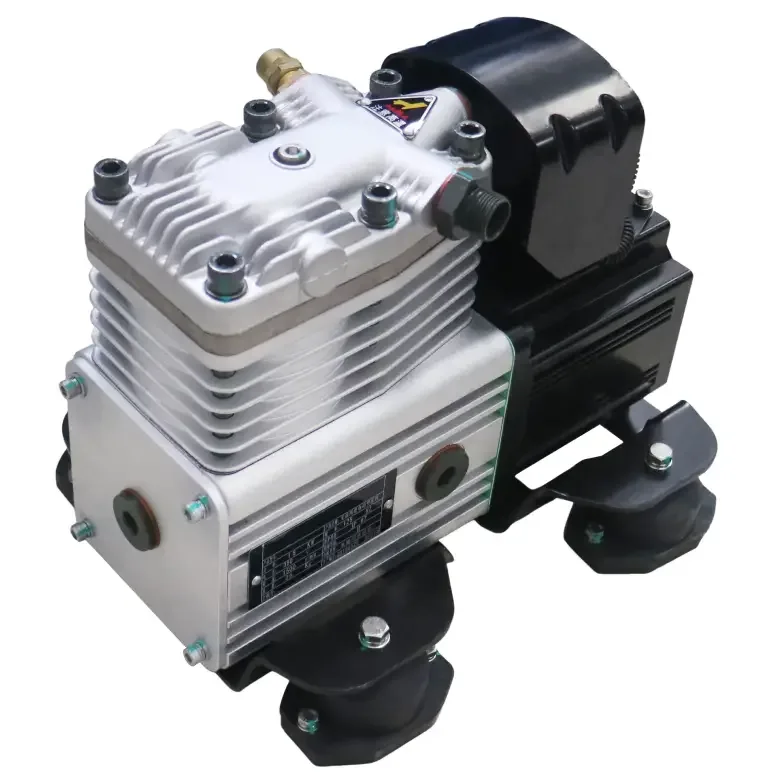
Case Studies
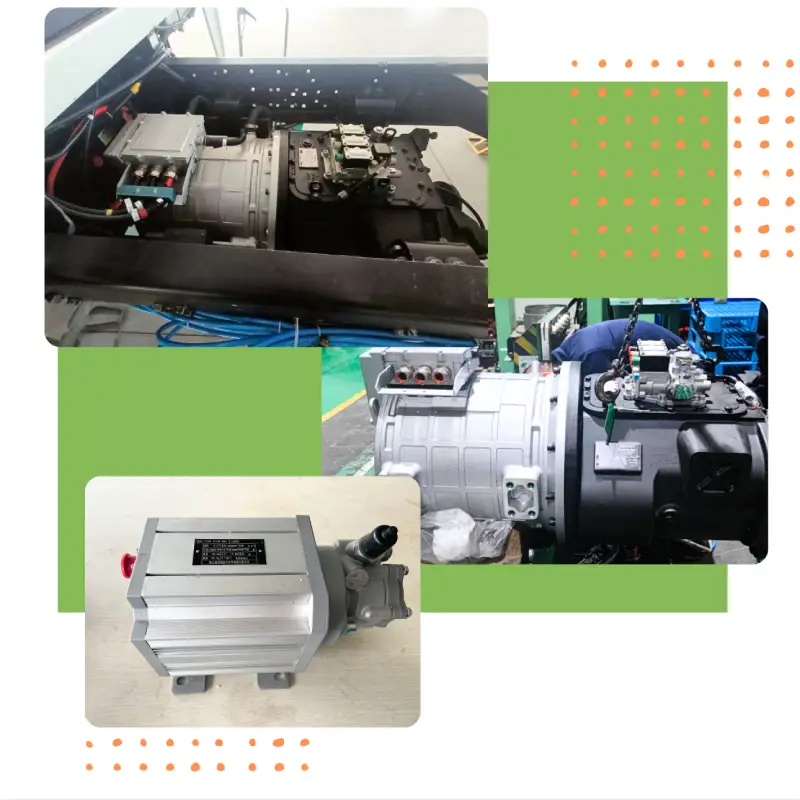
40-ton Electric Truck Project in Portugal
In 2021, a Portuguese company approached us for their first electric heavy truck project. From the initial discussions to project completion, we maintained close communication to fully understand their requirements and provide a tailored EV solution that met their exact specifications.
Throughout the process, we helped them navigate technical challenges, offering expert guidance and ensuring seamless integration of our EV systems. Our solution included a 350 kW e-powertrain, 4 kW EHPS, 4 kW air brake compressor, and an integrated 3-in-1 auxiliary inverter.
Beyond delivery, we continue to provide remote technical support and collaborate with their team to address ongoing technical concerns, ensuring long-term performance and reliability.
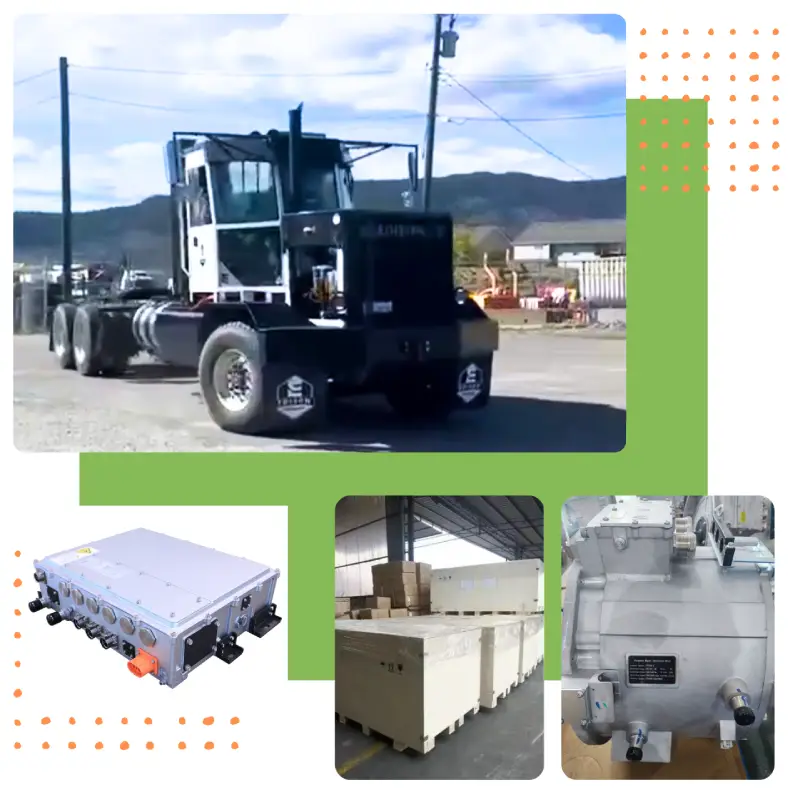
Electric Semi-Truck Project in Canada
Edison Motors is a Canadian clean technology company that specializes in manufacturing electric semi-trucks. For their heavy commercial vehicle (HCV) projects, we supplied tailored electric drive solutions, including electric axles, PMSM drive motors, and the compact auxiliary inverter systems.
Designed for versatility, our solution supports HEVs, BEVs, and FCEVs, making it suitable for a wide range of applications, including logistics vehicles, trucks, municipal vehicles, trailers, and semi-trucks. By enhancing efficiency and performance, our system helps meet the evolving demands of modern electric transportation.
Contact Us
Get in touch with us by sending us an email, using the Whatsapp number below, or filling in the form below. We usually reply within 2 business days.
Email: contact@brogenevsolution.com
Respond within 1 business day
Whatsapp: +8619352173376
Business hours: 9 am to 6 pm, GMT+8, Mon. to Fri.
LinkedIn channel
Follow us for regular updates >
YouTube channel
Ev systems introduction & industry insights >